Introduction to Rogers and Teflon PCB Materials
Printed Circuit Boards (PCBs) are essential components in modern electronics, providing a platform for mounting and interconnecting electronic components. The choice of PCB material plays a crucial role in determining the performance, reliability, and cost of the final product. Two popular high-performance PCB materials are Rogers and Teflon. While both offer excellent electrical and mechanical properties, there are distinct differences between them that make each suitable for specific applications.
What is Rogers PCB Material?
Rogers Corporation is a leading manufacturer of high-performance PCB materials, offering a range of products designed for demanding applications. Rogers PCB materials are known for their excellent electrical properties, including low dielectric loss, high thermal conductivity, and stable performance over a wide frequency range. Some popular Rogers PCB materials include:
- RT/duroid®: A ceramic-filled PTFE composite offering low dielectric loss and high thermal conductivity.
- RO4000®: A hydrocarbon ceramic laminate with low loss and good thermal stability.
- RO3000®: A ceramic-filled PTFE composite with low dielectric constant and loss tangent.
What is Teflon PCB Material?
Teflon, or Polytetrafluoroethylene (PTFE), is a synthetic fluoropolymer known for its excellent chemical resistance, low friction, and high temperature stability. Teflon PCB materials offer superior electrical properties, making them suitable for high-frequency and microwave applications. Some common Teflon PCB materials include:
- Teflon-based laminates: PTFE-based laminates with low dielectric constant and loss tangent.
- Teflon-ceramic composites: PTFE mixed with ceramic fillers for improved thermal and mechanical properties.
Comparing Rogers and Teflon PCB Materials
Electrical Properties
Both Rogers and Teflon PCB materials offer excellent electrical properties, making them suitable for high-frequency and microwave applications. However, there are some differences in their specific characteristics:
Property | Rogers PCB Materials | Teflon PCB Materials |
---|---|---|
Dielectric Constant | Typically 2.2 to 10.2 | Typically 2.0 to 2.6 |
Loss Tangent | Low, typically 0.0009 to 0.003 | Very low, typically 0.0002 to 0.001 |
Thermal Conductivity | High, up to 1.6 W/m·K | Low, typically 0.2 to 0.3 W/m·K |
Thermal Expansion | Low to moderate, depends on the specific material | Very low, typically 50 to 100 ppm/°C |
Mechanical Properties
Rogers and Teflon PCB materials have different mechanical properties, which can influence their suitability for certain applications:
Property | Rogers PCB Materials | Teflon PCB Materials |
---|---|---|
Tensile Strength | High, typically 20 to 50 MPa | Moderate, typically 10 to 30 MPa |
Flexural Strength | High, typically 30 to 70 MPa | Moderate, typically 10 to 30 MPa |
Compressive Strength | High, typically 100 to 200 MPa | Moderate, typically 10 to 30 MPa |
Density | Moderate to high, typically 1.7 to 3.0 g/cm³ | Low, typically 2.1 to 2.3 g/cm³ |
Thermal Properties
Thermal management is a critical factor in PCB design, and the choice of material can significantly influence the thermal performance of the board:
Property | Rogers PCB Materials | Teflon PCB Materials |
---|---|---|
Thermal Conductivity | High, up to 1.6 W/m·K | Low, typically 0.2 to 0.3 W/m·K |
Thermal Expansion | Low to moderate, depends on the specific material | Very low, typically 50 to 100 ppm/°C |
Glass Transition Temperature (Tg) | High, typically 280 to 320°C | High, typically 327°C |
Decomposition Temperature | High, typically 500 to 600°C | Very high, typically 400 to 500°C |
Chemical Resistance
Both Rogers and Teflon PCB materials offer excellent chemical resistance, making them suitable for harsh environments:
Property | Rogers PCB Materials | Teflon PCB Materials |
---|---|---|
Resistance to Acids | Excellent | Excellent |
Resistance to Bases | Excellent | Excellent |
Resistance to Solvents | Excellent | Excellent |
Moisture Absorption | Low, typically 0.02 to 0.1% | Very low, typically 0.01% |
Cost and Availability
The cost and availability of Rogers and Teflon PCB materials can vary depending on the specific product and supplier:
Factor | Rogers PCB Materials | Teflon PCB Materials |
---|---|---|
Cost | Relatively high, depends on the specific material | High, due to the cost of PTFE |
Availability | Good, with a range of products available | Limited, fewer suppliers compared to Rogers |
Lead Time | Moderate, typically 2 to 6 weeks | Longer, typically 4 to 8 weeks |
Applications of Rogers and Teflon PCB Materials
Rogers PCB Material Applications
Rogers PCB materials are widely used in various industries and applications, including:
- Wireless communication systems
- Radar and satellite systems
- Automotive radar sensors
- Medical imaging equipment
- High-speed digital circuits
- Aerospace and defense electronics
Teflon PCB Material Applications
Teflon PCB materials are preferred for specific applications that require their unique properties:
- Microwave and millimeter-wave circuits
- High-frequency antenna systems
- Radar and satellite communication equipment
- Aerospace and defense electronics
- High-temperature applications
- Chemical processing equipment
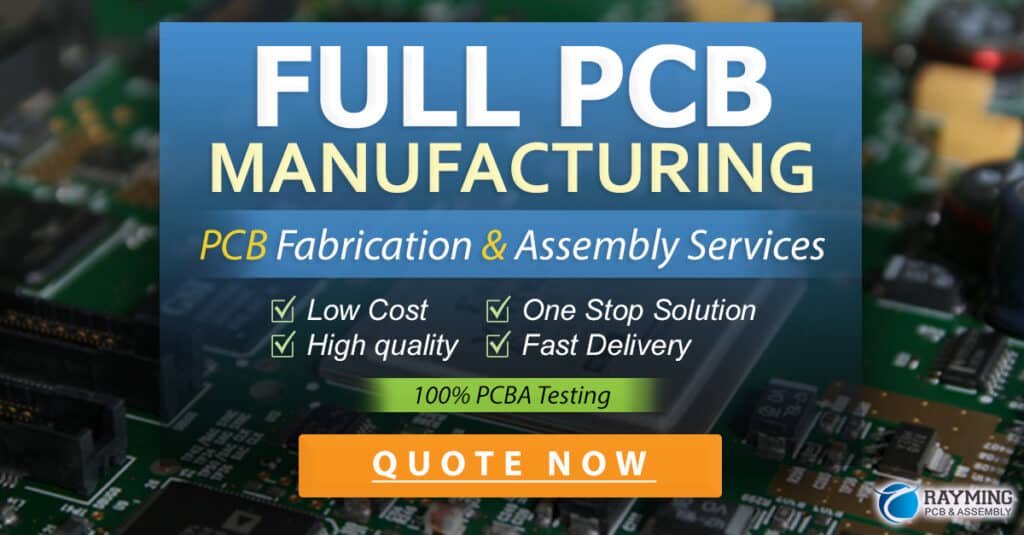
Choosing Between Rogers and Teflon PCB Materials
When selecting between Rogers and Teflon PCB materials, consider the following factors:
- Electrical requirements: Consider the dielectric constant, loss tangent, and thermal conductivity needed for your application.
- Mechanical requirements: Evaluate the required tensile, flexural, and compressive strength, as well as the density of the material.
- Thermal requirements: Assess the thermal conductivity, thermal expansion, glass transition temperature, and decomposition temperature of the material.
- Chemical resistance: Both materials offer excellent chemical resistance, but consider any specific chemical exposure in your application.
- Cost and availability: Compare the cost and lead times of the specific materials you are considering.
FAQ
1. Can Rogers and Teflon PCB materials be used for multilayer boards?
Yes, both Rogers and Teflon PCB materials can be used for multilayer boards. However, the specific material and manufacturing process may need to be optimized for the desired layer count and board thickness.
2. Are Rogers and Teflon PCB materials suitable for flexible circuits?
While Rogers and Teflon PCB materials are primarily used for rigid boards, some specialized products are available for flexible circuits. These materials offer excellent electrical properties and mechanical stability, making them suitable for high-performance flexible applications.
3. How do Rogers and Teflon PCB materials compare in terms of environmental impact?
Both Rogers and Teflon PCB materials have different environmental considerations. Rogers materials are generally more recyclable and have a lower carbon footprint compared to Teflon. However, Teflon materials offer longer product life and higher temperature stability, which can reduce the need for replacements and repairs.
4. Can Rogers and Teflon PCB materials be combined in the same board?
Yes, it is possible to combine Rogers and Teflon PCB materials in the same board, especially in multilayer designs. This approach allows designers to optimize the performance and cost of the board by using the most suitable material for each layer or section.
5. Are there any limitations in processing Rogers and Teflon PCB materials?
Yes, both Rogers and Teflon PCB materials require specialized processing techniques due to their unique properties. For example, Teflon materials require higher processing temperatures and pressures compared to conventional PCB materials. Rogers materials may require specific drilling and routing parameters to avoid delamination or other defects.
Conclusion
Rogers and Teflon PCB materials are both high-performance options for demanding electronic applications. While they share some similarities, such as excellent electrical properties and chemical resistance, they also have distinct differences in their mechanical, thermal, and cost characteristics.
When choosing between Rogers and Teflon PCB materials, it is essential to consider the specific requirements of your application, including electrical, mechanical, thermal, and environmental factors. By carefully evaluating these needs and consulting with experienced PCB manufacturers, you can select the most suitable material for your project, ensuring optimal performance, reliability, and cost-effectiveness.
As technology continues to advance, both Rogers and Teflon PCB materials will likely play an increasingly important role in enabling the next generation of high-performance electronic devices and systems.
No responses yet