What is Solder?
Solder is a fusible metal alloy used to create a permanent bond between electronic components and the circuit board. It typically consists of a combination of tin, lead, and other metals, depending on the specific type of solder. When heated, solder melts and flows into the joint, creating an electrical and mechanical connection upon cooling.
Types of Solder
There are two main types of solder used in electronic applications:
1. Lead-based Solder
Lead-based solder, also known as tin-lead solder, has been widely used in the electronics industry for decades. It typically consists of a 60/40 ratio of tin to lead. The advantages of lead-based solder include:
- Lower melting point (around 183°C)
- Excellent wetting properties
- Good electrical conductivity
- Easy to work with
However, due to environmental and health concerns, the use of lead-based solder has been restricted by various regulations, such as the Restriction of Hazardous Substances (RoHS) directive.
2. Lead-free Solder
Lead-free solder has gained popularity as a more environmentally friendly alternative to lead-based solder. Common lead-free solder alloys include:
- Tin-Silver-Copper (SAC): Typically contains 95.5% tin, 3.8% silver, and 0.7% copper.
- Tin-Copper (SnCu): Contains 99.3% tin and 0.7% copper.
- Tin-Silver (SnAg): Contains 96.5% tin and 3.5% silver.
Lead-free solder has a higher melting point compared to lead-based solder, usually around 217°C to 227°C. While it may require slightly higher soldering temperatures, lead-free solder offers several benefits:
- Compliance with environmental regulations
- Reduced health risks
- Improved mechanical strength
- Better resistance to thermal cycling
Factors to Consider When Choosing Solder
When selecting solder for your circuit board, consider the following factors:
1. Melting Point
The melting point of the solder is a critical factor to consider. It determines the temperature at which the solder melts and flows into the joint. Choose a solder with a melting point suitable for your soldering equipment and the components being soldered. Lead-free solder generally has a higher melting point compared to lead-based solder.
2. Wetting Properties
Wetting refers to the ability of the molten solder to flow and adhere to the surfaces being joined. Good wetting properties ensure a strong and reliable connection. Lead-based solder typically has better wetting properties compared to lead-free solder. However, advancements in lead-free solder formulations have significantly improved their wetting characteristics.
3. Mechanical Strength
The mechanical strength of the solder joint is crucial for the long-term reliability of the circuit board. Lead-free solder alloys, such as SAC and SnAg, offer improved mechanical strength compared to lead-based solder. They provide better resistance to fatigue and thermal cycling, which is especially important for applications subjected to vibration or temperature fluctuations.
4. Electrical Conductivity
Solder acts as an electrical conductor, allowing current to flow through the joint. Both lead-based and lead-free solders have good electrical conductivity. However, the specific alloy composition can affect the conductivity to some extent. Ensure that the solder you choose meets the electrical requirements of your application.
5. Compatibility with Components and PCB
Consider the compatibility of the solder with the components and the printed circuit board (PCB) materials. Some components may have specific soldering requirements, such as temperature sensitivity or lead-free compatibility. Additionally, ensure that the solder is compatible with the surface finish of the PCB, such as HASL (Hot Air Solder Leveling) or ENIG (Electroless Nickel Immersion Gold).
6. Flux Type
Flux is a chemical compound that helps remove oxides and improve the wetting properties of the solder. There are different types of flux, including rosin-based, water-soluble, and no-clean flux. Choose a flux that is compatible with your soldering process and the specific requirements of your application. Consider factors such as the need for post-soldering cleaning, environmental considerations, and the level of activity required.
7. Regulatory Compliance
If your electronic products are subject to specific regulations, such as RoHS or REACH, ensure that the solder you choose complies with these requirements. Lead-free solder is often necessary to meet environmental regulations. Check the compliance status of the solder and obtain the necessary certifications from the supplier.
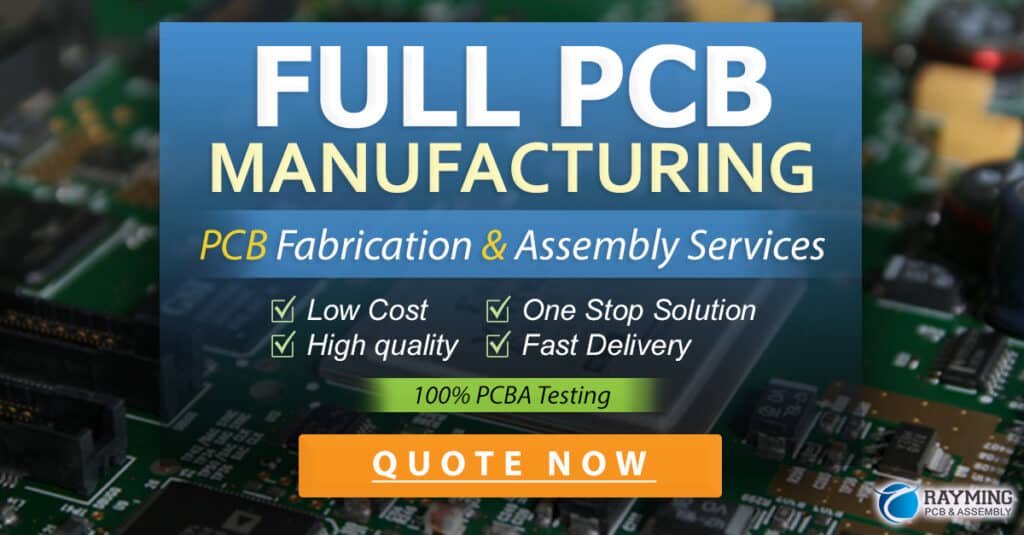
Solder Selection Table
To help you compare and select the best solder for your circuit board, here’s a table summarizing the key characteristics of common Solder Types:
Solder Type | Melting Point | Wetting Properties | Mechanical Strength | Electrical Conductivity | RoHS Compliant |
---|---|---|---|---|---|
Sn60Pb40 | 183°C | Excellent | Good | Good | No |
Sn63Pb37 | 183°C | Excellent | Good | Good | No |
SAC305 | 217-220°C | Good | Excellent | Good | Yes |
SnCu0.7 | 227°C | Fair | Good | Good | Yes |
SnAg3.5 | 221°C | Good | Excellent | Good | Yes |
Frequently Asked Questions (FAQ)
-
Q: Can I use lead-free solder for all my electronic projects?
A: Yes, lead-free solder can be used for most electronic projects. It is a versatile choice that complies with environmental regulations and offers good mechanical strength and electrical conductivity. -
Q: Is it necessary to use a specific type of flux with lead-free solder?
A: Lead-free solder can work with various types of flux, including rosin-based, water-soluble, and no-clean flux. Choose a flux that is compatible with your soldering process and the specific requirements of your application. -
Q: Can I mix lead-based and lead-free solder?
A: It is not recommended to mix lead-based and lead-free solder. They have different melting points and mixing them can lead to inconsistent and unreliable solder joints. Stick to using either lead-based or lead-free solder for your projects. -
Q: How do I select the right solder wire diameter?
A: The choice of solder wire diameter depends on the size of the components and the soldering iron tip you are using. For most through-hole soldering, a diameter of 0.8mm to 1.0mm is suitable. For surface-mount soldering, a smaller diameter of 0.5mm to 0.7mm is typically used. -
Q: What is the shelf life of solder?
A: The shelf life of solder depends on the storage conditions and the specific alloy composition. Generally, solder has a shelf life of several years when stored in a cool, dry place away from direct sunlight and moisture. Consult the manufacturer’s guidelines for specific storage recommendations and shelf life information.
Conclusion
Selecting the best solder for your circuit board is essential for creating reliable and long-lasting electronic connections. Consider factors such as melting point, wetting properties, mechanical strength, electrical conductivity, compatibility, flux type, and regulatory compliance when making your choice.
Lead-free solder, such as SAC305 or SnAg3.5, is a popular choice for its environmental friendliness, good mechanical strength, and compliance with regulations. However, the specific requirements of your application and the components being soldered should guide your decision.
By understanding the characteristics of different solder types and considering the factors discussed in this article, you can make an informed decision and choose the best solder for your circuit board projects. Always follow proper soldering techniques, use appropriate soldering equipment, and adhere to safety guidelines to ensure the best results.
No responses yet