Introduction to PCB Heaters
PCB (Printed Circuit Board) heaters are an essential component in many electronic devices, providing localized heating for various applications. These heaters are designed to be compact, efficient, and easily integrated into PCBs. In this article, we will explore the fundamentals of PCB heaters, their types, applications, advantages, and factors to consider when selecting and designing them.
How Do PCB Heaters Work?
PCB heaters work on the principle of Joule heating, where an electric current passing through a resistive element generates heat. The resistive element is typically a thin layer of conductive material, such as copper or nickel, that is etched onto the PCB. When an electric current is applied, the resistive element heats up, and the heat is transferred to the surrounding area.
The amount of heat generated by a PCB heater depends on several factors, including:
- The resistance of the heating element
- The amount of current flowing through the element
- The surface area of the heating element
- The thermal conductivity of the PCB material
By controlling these factors, engineers can design PCB heaters to provide the desired amount of heat for a specific application.
Types of PCB Heaters
There are several types of PCB heaters, each with its own unique characteristics and applications. Some of the most common types include:
Etched Foil Heaters
Etched foil heaters are the most common type of PCB heater. They consist of a thin layer of resistive foil, typically made of copper or nickel, that is etched onto the PCB. The foil is patterned to create a specific resistance and heating profile, allowing for precise control over the heat output.
Polyimide Heaters
Polyimide heaters are made from a thin, flexible polyimide film that is coated with a resistive material. These heaters are lightweight, durable, and can conform to various shapes and sizes, making them ideal for applications where flexibility is required, such as in wearable devices.
Ceramic Heaters
Ceramic heaters are constructed using a ceramic substrate with a resistive heating element bonded to its surface. These heaters are known for their high thermal conductivity, excellent electrical insulation, and ability to withstand high temperatures, making them suitable for high-temperature applications.
Silicone Rubber Heaters
Silicone rubber heaters consist of a wire-wound resistive element embedded in a silicone rubber matrix. These heaters are flexible, moisture-resistant, and can be molded into various shapes, making them ideal for applications that require a conformable heating solution.
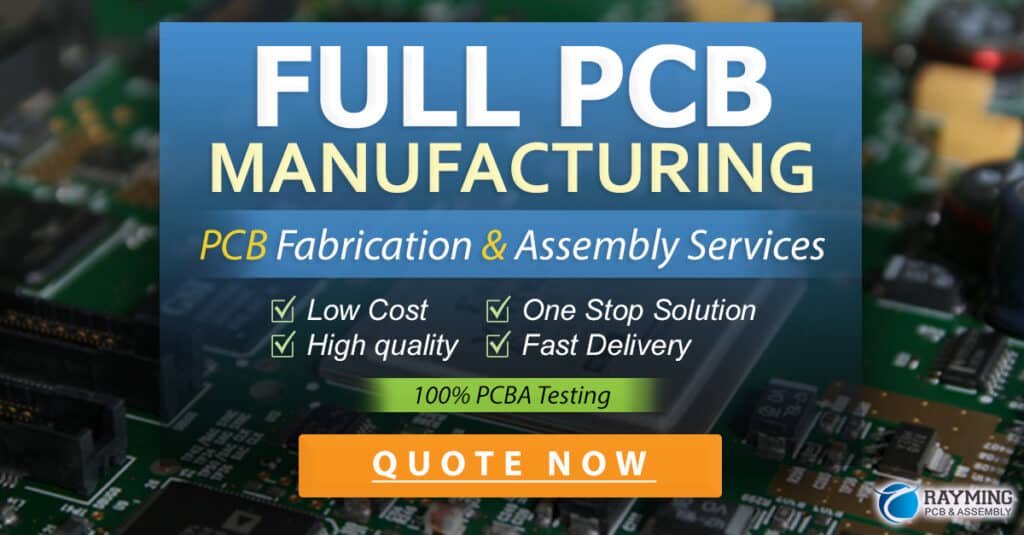
Applications of PCB Heaters
PCB heaters find applications in a wide range of industries and devices. Some common applications include:
-
Electronics: PCB heaters are used to maintain stable temperatures for sensitive electronic components, such as sensors, batteries, and displays.
-
Medical devices: In medical equipment, PCB heaters are used to maintain the temperature of fluids, prevent condensation on sensors, and provide localized heating for patient comfort.
-
Automotive: PCB heaters are used in automotive applications to prevent condensation on sensors, cameras, and displays, as well as to maintain the temperature of battery packs in electric vehicles.
-
Aerospace: In aerospace applications, PCB heaters are used to prevent ice formation on sensors and maintain the temperature of critical components in harsh environments.
-
Consumer products: PCB heaters are found in various consumer products, such as 3D printers, coffee makers, and hair styling tools, where they provide localized heating for specific functions.
Advantages of PCB Heaters
PCB heaters offer several advantages over traditional heating methods, making them an attractive choice for many applications:
-
Compact size: PCB heaters are thin and can be easily integrated into PCBs, allowing for space-saving designs.
-
Efficient heating: The direct contact between the PCB heater and the component being heated ensures efficient heat transfer and minimizes power consumption.
-
Precise temperature control: By adjusting the power input and using temperature sensors, PCB heaters can provide accurate and stable temperature control.
-
Rapid heating: PCB heaters have a low thermal mass, enabling them to heat up quickly and respond to temperature changes rapidly.
-
Customizable: PCB heaters can be designed to fit specific applications, with customizable sizes, shapes, and heating profiles.
Factors to Consider When Selecting PCB Heaters
When choosing a PCB heater for a specific application, several factors should be considered to ensure optimal performance and reliability:
-
Temperature range: Ensure that the PCB heater can operate within the required temperature range for the application.
-
Power density: Consider the power density of the heater, which determines the amount of heat generated per unit area. Higher power densities may be required for applications with limited space or high heat requirements.
-
Size and shape: Select a PCB heater that fits within the available space and conforms to the required shape of the application.
-
Thermal conductivity: Choose a PCB material with appropriate thermal conductivity to ensure efficient heat transfer from the heater to the target component.
-
Reliability: Consider the heater’s reliability, including its resistance to thermal cycling, vibration, and environmental factors such as humidity and corrosion.
Designing PCB Heaters
Designing PCB heaters requires careful consideration of several factors to ensure optimal performance and reliability. Some key aspects to consider include:
-
Heater layout: The layout of the heating element should be designed to provide uniform heating across the target area, avoiding hot spots or cold zones.
-
Power distribution: Ensure that the power distribution is balanced across the heating element to prevent localized overheating or undervoltage.
-
Temperature sensing: Incorporate temperature sensors, such as thermistors or RTDs, to monitor and control the heater’s temperature accurately.
-
Thermal management: Consider the thermal management of the PCB, including the use of heat sinks, thermal vias, or other cooling methods to dissipate excess heat and prevent damage to components.
-
Safety features: Include safety features, such as fuses, thermostats, or thermal cutoffs, to protect the heater and surrounding components from overheating or fault conditions.
FAQ
-
Q: How long do PCB heaters typically last?
A: The lifespan of a PCB heater depends on various factors, such as the application, operating temperature, and environmental conditions. With proper design and use, PCB heaters can last for several years or even decades. -
Q: Can PCB heaters be used in high-humidity environments?
A: Yes, PCB heaters can be designed to withstand high-humidity environments. Proper encapsulation, conformal coatings, and moisture-resistant materials can be used to protect the heater from humidity and corrosion. -
Q: Are PCB heaters energy-efficient?
A: PCB heaters are generally energy-efficient due to their direct contact with the target component, minimizing heat loss. However, the overall efficiency depends on factors such as the heater design, power density, and thermal management of the PCB. -
Q: Can PCB heaters be customized for specific applications?
A: Yes, PCB heaters can be customized to fit specific applications. Factors such as size, shape, power density, and heating profile can be tailored to meet the requirements of a particular application. -
Q: How do I select the right PCB heater for my application?
A: When selecting a PCB heater, consider factors such as the required temperature range, power density, size and shape, thermal conductivity, and reliability. Consult with a PCB heater manufacturer or a thermal management expert to determine the best solution for your specific application.
Conclusion
PCB heaters are a versatile and efficient solution for providing localized heating in various electronic devices and applications. By understanding the fundamentals of PCB heaters, their types, applications, advantages, and design considerations, engineers can select and design the optimal heating solution for their specific needs.
As technology advances and new applications emerge, the demand for compact, efficient, and reliable heating solutions will continue to grow. PCB heaters are well-positioned to meet these challenges, offering customizable and high-performance heating for a wide range of industries and devices.
PCB Heater Type | Characteristics | Typical Applications |
---|---|---|
Etched Foil | – Thin resistive foil etched onto PCB – Precise heating control |
– Electronics – Automotive – Consumer products |
Polyimide | – Thin, flexible polyimide film – Lightweight and conformable |
– Wearable devices – Medical equipment |
Ceramic | – Ceramic substrate with resistive element – High-temperature |
– High-temperature applications – Aerospace |
Silicone Rubber | – Wire-wound element in silicone rubber – Flexible and moldable |
– Medical devices – Consumer products |
By selecting the appropriate PCB heater type and carefully considering the design factors, engineers can create efficient, reliable, and high-performance heating solutions for a wide range of applications.
No responses yet