What is SMT?
Surface-mount technology (SMT) is a method for producing electronic circuits in which the components are mounted directly onto the surface of printed circuit boards (PCBs). An electronic device so made is called a surface-mount device (SMD). In industry, this approach has largely replaced the through-hole technology construction method of fitting components, in large part because SMT allows for increased manufacturing automation which reduces cost and improves quality. It also allows for more components to fit on a given area of substrate. Both technologies can be used on the same board, with the through-hole technology often used for components not suitable for surface mounting such as large transformers and heat-sinked power semiconductors.
Key Benefits of SMT
- Smaller components
- Increased circuit density
- Lower initial cost and time of setting up for production
- Simpler and faster automated assembly
- Fewer holes need to be drilled through the PCB
- Lower resistance and inductance at the connection
- Better mechanical performance under shake and vibration conditions
- Faster assembly due to less space between components
- Traces can be routed between pads on all PCB Layers
SMT Manufacturing Process Overview
The SMT manufacturing process consists of several key steps:
-
Solder Paste Printing: Solder paste is applied to the PCB pads using a stencil printing process. The stencil has cutouts that match the pads on the PCB.
-
Component Placement: The components are automatically placed onto their pads by pick-and-place machines. These use vacuum nozzles or grippers to pick up and accurately position the components.
-
Reflow Soldering: The entire board is heated in a reflow oven. This melts the solder paste, permanently connecting the components to the pads.
-
Inspection: The assembled PCBs are inspected, often using automated optical inspection (AOI) systems that check for missing components, misalignments, solder defects, etc.
-
Testing: The boards are electrically tested to ensure they function correctly. Any faulty boards are repaired or discarded.
SMT Process Flow
Step | Description |
---|---|
1. PCB Design & Fabrication | The PCB is designed and fabricated with pads for SMT components |
2. Solder Paste Printing | Solder paste is applied to the pads using a stencil |
3. Component Placement | SMT components are placed onto the pads by pick-and-place machines |
4. Reflow Soldering | The PCB is heated to melt the solder paste, bonding the components |
5. Inspection | The assembled PCB is inspected for defects |
6. Testing | The PCB is electrically tested to ensure proper function |
Solder Paste Printing
Solder paste printing is the process of applying solder paste to a PCB. Solder paste is a mixture of tiny solder particles suspended in flux. It’s applied using a stencil, which is a thin sheet of stainless steel or nickel with laser-cut openings that match the pads on the PCB.
Stencil Design Considerations
- Aperture Size: The openings in the stencil must be slightly larger than the pads to allow for a slight paste overprint. This helps ensure sufficient solder volume.
- Stencil Thickness: Thicker stencils deposit more paste. The thickness is chosen based on the size of the components and the desired solder volume.
- Aperture Shape: The shape of the openings can affect paste release. Rounded corners and tapered walls can improve release.
Solder Paste Properties
- Particle Size: Smaller particles allow for finer pitch components but can be more prone to oxidation.
- Metal Content: Higher metal content means more solder volume but can affect printability.
- Viscosity: The paste must be viscous enough to stay in place after printing but not so viscous that it doesn’t release from the stencil cleanly.
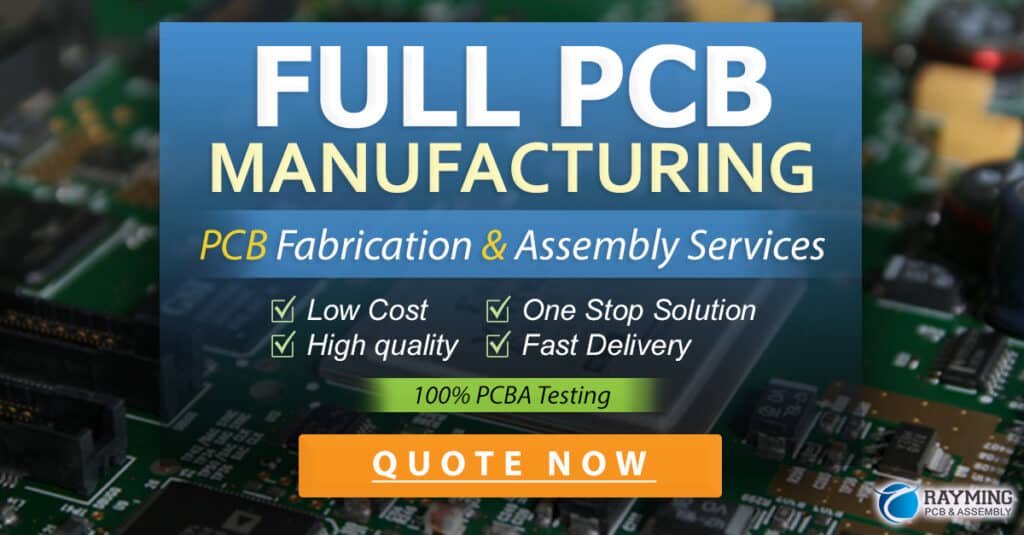
Component Placement
After solder paste printing, the components are placed onto the pads. This is done by pick-and-place machines, which use vacuum nozzles or mechanical grippers to pick up the components from feeders and place them accurately on the PCB.
Pick-and-Place Machine Types
- Chip Shooters: These are high-speed machines that place simple, regular-shaped components like resistors and capacitors. They can place thousands of components per hour.
- Flexible Placement Machines: These handle a wider variety of components, including irregular shapes. They are slower than chip shooters but more versatile.
- Multi-Head Machines: These have multiple placement heads working in parallel, allowing for high throughput.
Placement Accuracy
Placement accuracy is critical, especially for fine-pitch components. Factors affecting accuracy include:
– Machine calibration
– Nozzle or gripper design
– Component feeding precision
– PCB alignment and fixturing
Reflow Soldering
After component placement, the PCB is heated in a reflow oven to melt the solder paste. The heat activates the flux, which cleans the component leads and pad surfaces. As the solder melts, surface tension causes it to wick onto the component leads and pads, forming a reliable electrical and mechanical bond as it cools.
Reflow Profile
The reflow profile is a graph of temperature over time. It typically includes several stages:
1. Preheat: The PCB is gradually heated to activate the flux and dry out the solder paste.
2. Soak: The temperature is held steady to allow all parts of the PCB to reach an even temperature.
3. Reflow: The temperature is rapidly increased above the melting point of the solder. This is where the actual soldering occurs.
4. Cooling: The PCB is cooled, allowing the solder to solidify.
The exact temperatures and times depend on the solder paste being used and the thermal mass of the components and PCB.
Reflow Defects
Several types of defects can occur during reflow:
– Bridging: Solder bridges form between adjacent pads.
– Tombstoning: Components stand up on one end due to uneven heating or pad design.
– Insufficient Wetting: Solder doesn’t fully wet the pads or component leads.
– Voids: Bubbles form in the solder joint.
Many of these can be mitigated by proper paste printing, component placement, and reflow profile design.
Inspection and Testing
After reflow, the assembled PCBs are inspected and tested to ensure quality.
Automated Optical Inspection (AOI)
AOI systems use cameras and image processing to check for assembly defects such as:
– Missing components
– Misaligned components
– Solder bridges or insufficient solder
– Reversed polarity components
AOI can quickly scan the entire PCB and flag potential issues for manual review.
Electrical Testing
Electrical testing verifies that the PCB functions as intended. This can include:
– In-circuit testing (ICT): Probes are used to test individual components and circuits.
– Functional testing: The PCB is powered up and its overall functionality is tested.
– Boundary scan: Special test features built into some ICs allow their connections to be tested.
Boards that fail testing may be repaired or reworked if possible, or scrapped if the defects are too severe.
FAQ
What are the advantages of SMT over through-hole technology?
SMT allows for smaller components, increased circuit density, automated assembly, fewer drilled holes, and better performance under vibration. It generally results in lower costs and higher reliability compared to through-hole.
What is solder paste made of?
Solder paste is a mixture of tiny solder particles (typically tin, silver, and copper) suspended in a thick flux paste. The flux helps clean the surfaces to be soldered and prevents oxidation during reflow.
How does a pick-and-place machine work?
Pick-and-place machines use vacuum nozzles or mechanical grippers to pick up SMT components from tape feeders, trays, or reels. They then position the components accurately on the PCB and place them onto the solder paste deposits. High-end machines can place thousands of components per hour with great precision.
What happens during reflow soldering?
During reflow, the PCB is heated according to a carefully controlled temperature profile. The heat activates the flux in the solder paste, which cleans the surfaces to be soldered. As the temperature rises further, the solder particles melt and wet the surfaces of the pads and component leads. Surface tension causes the molten solder to wick onto the surfaces and form a strong bond as it cools and solidifies.
Why is inspection important in SMT assembly?
Inspection is crucial for ensuring the quality and reliability of the assembled PCBs. Automated optical inspection (AOI) can quickly detect common defects like missing or misaligned components, solder bridges, or insufficient solder. Electrical testing verifies that the PCB functions as intended. Catching defects early prevents faulty products from reaching customers and allows for timely rework or process improvements.
No responses yet