Introduction to Lead Free Soldering
Lead free soldering is the process of joining two or more electronic parts using a lead-free solder alloy. The electronics industry has moved away from using lead-based solder alloys due to environmental and health concerns. Lead is a toxic substance that can cause serious health problems if ingested or inhaled. Therefore, the use of lead-free solder alloys has become mandatory in many countries.
Lead-free solder alloys typically contain tin, silver, and copper. The most common lead-free solder alloy is SAC305, which contains 96.5% tin, 3% silver, and 0.5% copper. Other lead-free solder alloys include SN100C, which contains tin, copper, and a small amount of nickel and germanium, and SN96.5AG3.5, which contains 96.5% tin and 3.5% silver.
Benefits of Lead Free Soldering
Lead free soldering offers several benefits over lead-based soldering, including:
-
Environmental friendliness: Lead-free solder alloys are more environmentally friendly than lead-based alloys because they do not contain toxic substances that can harm the environment.
-
Health and safety: Lead-free solder alloys are safer for workers because they do not contain lead, which can cause serious health problems if inhaled or ingested.
-
Reliability: Lead-free solder joints are more reliable than lead-based solder joints because they have a higher melting point and are less prone to fatigue and creep.
-
Compliance with regulations: Using lead-free solder alloys ensures compliance with environmental and health regulations in many countries.
Challenges of Lead Free Soldering
While lead free soldering offers several benefits, it also presents some challenges, including:
-
Higher melting point: Lead-free solder alloys have a higher melting point than lead-based alloys, which means that higher temperatures are required for soldering.
-
Wetting issues: Lead-free solder alloys have lower wetting ability than lead-based alloys, which means that they may not flow as easily and may require additional flux.
-
Tin whiskers: Lead-free solder alloys are more prone to tin whisker growth, which can cause short circuits and other reliability issues.
-
Compatibility with existing equipment: Switching to lead-free solder alloys may require upgrading or replacing existing soldering equipment.
Reflow Soldering Process
Reflow soldering is a process used to attach surface mount components to a printed circuit board (PCB) using a solder paste. The solder paste is a mixture of solder powder and flux that is applied to the PCB pads using a stencil. The components are then placed on the PCB and the entire assembly is heated in a reflow oven to melt the solder and form a permanent connection between the components and the PCB.
Reflow Soldering Steps
The reflow soldering process involves the following steps:
-
Solder paste printing: A stencil is used to apply solder paste to the PCB pads. The stencil is aligned with the PCB and the solder paste is squeezed through the openings in the stencil onto the pads.
-
Component placement: The surface mount components are placed on the PCB using a pick-and-place machine or by hand. The components are aligned with the solder paste on the pads.
-
Reflow: The PCB Assembly is placed in a reflow oven and heated to a specific temperature profile. The solder paste melts and flows around the component leads, forming a permanent connection between the components and the PCB.
-
Cooling: After reflow, the PCB assembly is cooled to room temperature. The solder solidifies, forming a strong mechanical and electrical connection between the components and the PCB.
Reflow Temperature Profile
The reflow temperature profile is a critical aspect of the reflow soldering process. It determines the temperature and duration of each stage of the reflow process. The reflow temperature profile must be carefully controlled to ensure that the solder melts and flows properly without damaging the components or the PCB.
A typical reflow temperature profile consists of four stages:
-
Preheat: The PCB assembly is gradually heated to a temperature below the melting point of the solder. This stage activates the flux and removes any moisture from the PCB and components.
-
Soak: The PCB assembly is held at a constant temperature to allow the flux to clean the surfaces of the PCB and components and to prepare the solder for melting.
-
Reflow: The temperature is increased above the melting point of the solder, causing the solder to melt and flow around the component leads. This stage is critical for forming a strong and reliable solder joint.
-
Cooling: The PCB assembly is cooled to room temperature, allowing the solder to solidify and form a permanent connection between the components and the PCB.
The following table shows a typical reflow temperature profile for a lead-free solder alloy:
Stage | Temperature Range (°C) | Time (seconds) |
---|---|---|
Preheat | 150-180 | 60-120 |
Soak | 180-200 | 60-120 |
Reflow | 235-245 | 30-60 |
Cooling | 25-30 | 60-120 |
It is important to note that the reflow temperature profile may vary depending on the specific solder alloy being used and the size and complexity of the PCB assembly. The reflow oven must be calibrated and the temperature profile must be optimized for each specific application.
Solder Paste
Solder paste is a critical component of the reflow soldering process. It consists of a mixture of solder powder and flux that is used to attach surface mount components to a PCB. The solder paste is applied to the PCB pads using a stencil and the components are placed on top of the solder paste.
Solder Paste Composition
Solder paste typically consists of the following components:
-
Solder powder: The solder powder is made up of small spheres of solder alloy. The size and shape of the solder powder particles can affect the printing and reflow properties of the solder paste.
-
Flux: The flux is a chemical compound that is used to remove oxides and other contaminants from the surfaces of the PCB and components. It also helps to improve the wetting and flow properties of the solder.
-
Solvents: Solvents are used to control the viscosity and printing properties of the solder paste.
-
Additives: Additives such as thickeners and stabilizers may be used to improve the printing and storage properties of the solder paste.
Solder Paste Selection
Selecting the right solder paste is critical for achieving a successful reflow soldering process. The following factors should be considered when selecting a solder paste:
-
Alloy composition: The solder alloy should be compatible with the PCB and component materials and should meet the required electrical and mechanical properties.
-
Particle size: The particle size of the solder powder should be selected based on the size and pitch of the PCB pads and component leads.
-
Flux type: The flux type should be selected based on the PCB and component materials and the required cleaning and reliability properties.
-
Viscosity: The viscosity of the solder paste should be selected based on the printing process and the size and shape of the PCB pads and component leads.
-
Storage and handling: The solder paste should be stored and handled according to the manufacturer’s recommendations to ensure optimal performance and shelf life.
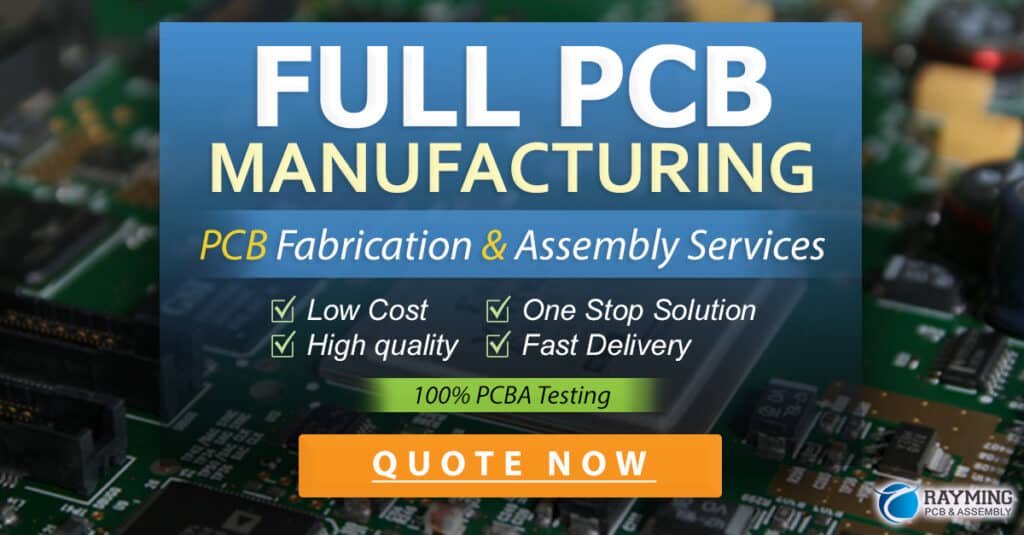
Stencil Printing
Stencil printing is the process of applying solder paste to the PCB pads using a stencil. The stencil is a thin sheet of metal or plastic with openings that correspond to the size and shape of the PCB pads. The solder paste is squeezed through the openings in the stencil onto the PCB pads using a squeegee.
Stencil Design
The design of the stencil is critical for achieving a successful stencil printing process. The following factors should be considered when designing a stencil:
-
Aperture size and shape: The size and shape of the stencil apertures should match the size and shape of the PCB pads. The aperture size should be slightly larger than the pad size to allow for some solder paste overflow.
-
Stencil thickness: The thickness of the stencil should be selected based on the size and pitch of the PCB pads and component leads. A thicker stencil will result in more solder paste being deposited on the pads.
-
Stencil material: The stencil material should be selected based on the required durability and printing properties. Stainless steel and nickel-plated stencils are commonly used for high-volume production.
-
Aperture wall angle: The angle of the aperture walls can affect the release of the solder paste from the stencil. A wall angle of 5-10 degrees is typically recommended.
Stencil Printing Process
The stencil printing process involves the following steps:
-
Stencil alignment: The stencil is aligned with the PCB using fiducial marks or other alignment features.
-
Solder paste application: The solder paste is applied to the stencil and squeezed through the apertures onto the PCB pads using a squeegee.
-
Stencil removal: The stencil is carefully removed from the PCB, leaving the solder paste on the pads.
-
Inspection: The PCB is inspected for solder paste print quality and any defects are corrected before component placement.
Stencil Printing Defects
Stencil printing defects can occur due to a variety of factors, including:
-
Poor stencil alignment: If the stencil is not properly aligned with the PCB, the solder paste may be deposited in the wrong locations or may not be deposited at all.
-
Inadequate solder paste volume: If the solder paste volume is too low, there may not be enough solder to form a reliable joint. If the volume is too high, the solder may bridge between adjacent pads or components.
-
Solder paste slumping: If the solder paste is too thick or has poor rheology, it may slump or spread out on the PCB, causing bridging or other defects.
-
Stencil damage: If the stencil is damaged or worn, it may not print the solder paste accurately or consistently.
Component Placement
Component placement is the process of placing surface mount components onto the solder paste on the PCB pads. This can be done using a pick-and-place machine or by hand, depending on the volume and complexity of the PCB assembly.
Pick-and-Place Machine
A pick-and-place machine is an automated system that uses a vacuum nozzle to pick up components from a feeder and place them onto the PCB. The machine is programmed with the component locations and orientations and can place components at high speed and accuracy.
The following factors should be considered when using a pick-and-place machine:
-
Nozzle selection: The nozzle size and shape should be selected based on the size and shape of the components being placed.
-
Placement pressure: The placement pressure should be adjusted to ensure that the components are securely placed on the solder paste without damaging the components or the PCB.
-
Placement accuracy: The placement accuracy should be verified using a vision system or other inspection method to ensure that the components are placed in the correct locations and orientations.
Hand Placement
For low-volume or prototype PCB assemblies, components can be placed by hand using tweezers or other tools. Hand placement requires a steady hand and good eyesight to ensure that the components are placed accurately and securely on the solder paste.
The following factors should be considered when placing components by hand:
-
Component orientation: The components should be oriented correctly according to the PCB layout and the component markings.
-
Placement pressure: The components should be pressed gently onto the solder paste to ensure good contact without damaging the components or the PCB.
-
Inspection: The PCB should be inspected after component placement to ensure that all components are placed correctly and securely.
Reflow Oven
A reflow oven is used to heat the PCB assembly and melt the solder paste, forming a permanent connection between the components and the PCB. The reflow oven controls the temperature and duration of each stage of the reflow process to ensure that the solder melts and flows properly without damaging the components or the PCB.
Reflow Oven Types
There are two main types of reflow ovens:
-
Convection reflow oven: A convection reflow oven uses forced air convection to heat the PCB assembly. The heated air is circulated around the PCB using fans and baffles to ensure even heating.
-
Infrared reflow oven: An infrared reflow oven uses infrared lamps or heaters to heat the PCB assembly. The infrared energy is absorbed by the PCB and components, heating them directly.
Reflow Oven Control
The reflow oven must be carefully controlled to ensure that the temperature profile is followed accurately and consistently. The following factors should be considered when controlling a reflow oven:
-
Temperature sensors: The reflow oven should be equipped with temperature sensors to monitor the temperature of the PCB assembly throughout the reflow process.
-
Heating zones: The reflow oven should have multiple heating zones that can be independently controlled to achieve the desired temperature profile.
-
Cooling rate: The cooling rate of the PCB assembly should be controlled to minimize thermal stress and ensure that the solder joints solidify properly.
-
Atmosphere control: The reflow oven atmosphere should be controlled to minimize oxidation and other defects. Nitrogen or other inert gases may be used to provide a controlled atmosphere.
Inspection and Testing
After the reflow soldering process is complete, the PCB assembly should be inspected and tested to ensure that it meets the required quality and reliability standards. The following inspection and testing methods may be used:
-
Visual inspection: The PCB assembly should be visually inspected for defects such as solder bridges, insufficient solder, or component misalignment.
-
X-ray inspection: X-ray inspection can be used to detect internal defects such as voids or cracks in the solder joints.
-
Electrical testing: Electrical testing should be performed to verify that the PCB assembly functions as intended and meets the required performance specifications.
-
Environmental testing: Environmental testing may be performed to verify that the PCB assembly can withstand the expected operating conditions, such as temperature, humidity, and vibration.
Frequently Asked Questions (FAQ)
-
What is the difference between lead-based and lead-free solder?
Lead-based solder contains lead, while lead-free solder does not. Lead-free solder has a higher melting point and requires different processing parameters than lead-based solder. -
What are the benefits of using lead-free solder?
Lead-free solder is more environmentally friendly and safer for workers than lead-based solder. It also provides better reliability and longer service life for electronic products. -
What is a reflow profile?
A reflow profile is a graph that shows the temperature of the PCB assembly over time during the reflow soldering process. It is used to control the heating and cooling rates and ensure that the solder paste melts and flows properly. -
What are some common defects that can occur during reflow soldering?
Common defects include solder bridges, insufficient solder, component misalignment, and voids or cracks in the solder joints. These defects can be caused by improper stencil printing, component placement, or reflow profile. -
How can I optimize my reflow soldering process?
To optimize your reflow soldering process, you should select the appropriate solder paste and stencil design for your PCB assembly, use a pick-and-place machine for accurate component placement, and carefully control the reflow oven temperature profile. You should also perform regular inspection and testing to identify and correct any defects or issues.
Conclusion
Lead-free soldering and reflow profiling are critical processes in the manufacturing of electronic products. By using lead-free solder and carefully controlling the reflow soldering process, manufacturers can produce high-quality, reliable PCB assemblies that meet the required performance and environmental standards.
Proper selection of solder paste, stencil design, and component placement techniques are essential for achieving a successful reflow soldering process. The reflow oven temperature profile must be carefully controlled to ensure that the solder paste melts and flows properly without damaging the components or the PCB.
Regular inspection and testing of the PCB assembly are also important for identifying and correcting any defects or issues that may arise during the manufacturing process.
By following best practices and continuously improving their processes, manufacturers can ensure the quality and reliability of their electronic products while minimizing environmental impact and complying with relevant regulations and standards.
No responses yet