Introduction to PCB De-Paneling Methods
Printed Circuit Boards (PCBs) are essential components in modern electronics manufacturing. They provide a platform for mounting and connecting electronic components, enabling the creation of complex circuits and devices. In most cases, multiple PCBs are manufactured together on a single panel to optimize production efficiency and reduce costs. However, once the manufacturing process is complete, these individual PCBs need to be separated from the panel for further assembly or use. This process is known as de-paneling or depaneling.
De-paneling is a critical step in PCB manufacturing, as it directly affects the quality, functionality, and reliability of the final product. Improper de-paneling can lead to damaged boards, broken components, or compromised circuit integrity. Therefore, choosing the right de-paneling method is crucial for ensuring the success of the entire manufacturing process.
In this article, we will explore two popular methods for de-paneling PCBs: half holes and V-cut. We will discuss their advantages, disadvantages, and applications, helping you make an informed decision when selecting the most suitable de-paneling method for your specific needs.
What are PCB Half Holes?
PCB half holes, also known as perforations or mouse bites, are a common de-paneling method that involves drilling small, circular holes along the edges of individual PCBs on the panel. These holes are typically arranged in a straight line, creating a perforation that allows for easy separation of the boards.
The size and spacing of the half holes depend on various factors, such as the thickness of the PCB, the required break-away force, and the desired edge quality. Generally, the diameter of the half holes ranges from 0.5mm to 1.5mm, with a spacing of 0.8mm to 2.0mm between the centers of adjacent holes.
Advantages of PCB Half Holes
-
Cost-effective: Half holes are relatively inexpensive to implement, as they can be drilled using standard PCB manufacturing equipment without requiring additional tools or processes.
-
Versatility: This method is suitable for a wide range of PCB Thicknesses and materials, making it a versatile choice for various applications.
-
Ease of separation: PCBs with half holes can be easily separated by hand or using simple tools, such as pliers or a manual depaneling machine.
-
Minimal waste: Half holes generate less waste compared to other de-paneling methods, as the removed material is limited to the small circular holes.
Disadvantages of PCB Half Holes
-
Rough edges: The edges of the separated PCBs may be rough or jagged, requiring additional finishing or sanding to achieve a smooth surface.
-
Potential for damage: If not carefully designed or executed, half holes can lead to stress concentration points, which may cause the PCB to crack or break during the separation process.
-
Limited design flexibility: The presence of half holes along the edges of the PCB may restrict the placement of components or traces near the perimeter of the board.
What is V-Cut PCB De-Paneling?
V-cut de-paneling is another popular method for separating individual PCBs from a panel. This technique involves using a specialized cutting tool with a V-shaped blade to create a groove along the edges of the PCBs. The depth of the V-cut is typically around one-third of the PCB thickness, leaving a thin layer of material connecting the individual boards to the panel.
The angle of the V-cut can vary depending on the specific requirements of the PCB and the de-paneling process. Common angles range from 30° to 60°, with 45° being the most frequently used.
Advantages of V-Cut PCB De-Paneling
-
Clean edges: V-cut de-paneling produces clean and smooth edges on the separated PCBs, reducing the need for additional finishing or sanding.
-
Reduced stress: The V-shaped groove distributes the stress more evenly along the edge of the PCB, minimizing the risk of damage during the separation process.
-
Design flexibility: V-cuts allow for greater design flexibility, as they do not require the presence of holes along the edges of the PCB, enabling components and traces to be placed closer to the perimeter.
-
Automation compatibility: V-cut de-paneling is well-suited for automated assembly processes, as the PCBs can be easily separated using specialized equipment.
Disadvantages of V-Cut PCB De-Paneling
-
Higher cost: Implementing V-cut de-paneling requires specialized cutting tools and equipment, which can increase the overall manufacturing cost compared to half holes.
-
Limited thickness range: V-cuts are most effective for PCBs with thicknesses ranging from 0.8mm to 3.2mm. Thinner or thicker boards may require alternative de-paneling methods.
-
Potential for breakage: If the V-cut is too deep or the remaining material is too thin, the PCBs may break or snap prematurely during handling or assembly.
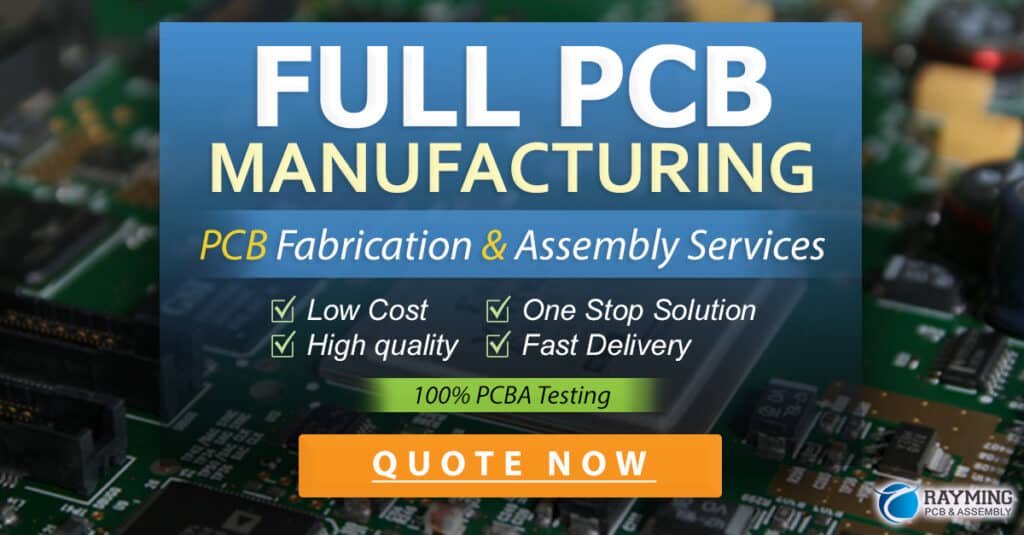
Comparison of PCB Half Holes and V-Cut De-Paneling Methods
Feature | Half Holes | V-Cut |
---|---|---|
Edge Quality | Rough, may require finishing | Clean and smooth |
Stress Distribution | Potential for stress concentration | More even stress distribution |
Design Flexibility | Limited component placement near edges | Greater flexibility for component placement |
Cost | Lower cost, standard equipment | Higher cost, specialized equipment |
PCB Thickness Range | Suitable for a wide range of thicknesses | Most effective for 0.8mm to 3.2mm |
Automation Compatibility | Manual separation or simple tools | Well-suited for automated assembly |
Waste Generation | Minimal waste | Minimal waste |
Choosing the Right De-Paneling Method
When selecting the most suitable de-paneling method for your PCB manufacturing process, consider the following factors:
-
PCB thickness and material: Evaluate the thickness and material of your PCBs to ensure compatibility with the chosen de-paneling method.
-
Edge quality requirements: Determine the desired edge quality for your PCBs and choose a method that meets those standards.
-
Design constraints: Consider the placement of components and traces near the edges of the PCB and select a method that accommodates your design requirements.
-
Production volume and automation: Assess your production volume and automation needs to choose a de-paneling method that aligns with your manufacturing process and equipment.
-
Cost considerations: Evaluate the cost implications of each de-paneling method, taking into account equipment, tooling, and labor costs.
Best Practices for PCB De-Paneling
Regardless of the de-paneling method you choose, follow these best practices to ensure optimal results and minimize the risk of damage:
-
Design for manufacturability: Incorporate de-paneling considerations into your PCB design, ensuring adequate spacing and clearance for the chosen method.
-
Use appropriate tooling: Select the right tools and equipment for your de-paneling method, ensuring proper maintenance and calibration.
-
Test and validate: Conduct thorough testing and validation of your de-paneling process to identify and address any potential issues before full-scale production.
-
Train personnel: Provide adequate training to your manufacturing personnel to ensure consistent and accurate de-paneling practices.
-
Monitor and optimize: Continuously monitor the de-paneling process and make necessary adjustments to optimize quality, efficiency, and cost-effectiveness.
Frequently Asked Questions (FAQ)
-
Q: Can PCB half holes and V-cut de-paneling methods be used together on the same panel?
A: Yes, it is possible to combine both methods on a single panel, depending on the specific requirements of the PCBs and the manufacturing process. However, this may increase the complexity and cost of the de-paneling process. -
Q: Are there any alternative de-paneling methods besides half holes and V-cut?
A: Yes, there are other de-paneling methods, such as scoring, routing, and punching. Each method has its own advantages and disadvantages, and the choice depends on factors such as PCB thickness, material, and design requirements. -
Q: How do I determine the appropriate size and spacing for PCB half holes?
A: The size and spacing of half holes depend on the PCB thickness, material, and desired break-away force. Consult with your PCB manufacturer or refer to industry standards and guidelines to determine the optimal dimensions for your specific application. -
Q: Can V-cut de-paneling be used for Flexible PCBs?
A: Yes, V-cut de-paneling can be used for flexible PCBs, but the depth and angle of the cut may need to be adjusted to accommodate the material properties and thickness of the flexible substrate. -
Q: What is the typical cost difference between PCB half holes and V-cut de-paneling methods?
A: The cost difference between half holes and V-cut de-paneling methods can vary depending on factors such as PCB complexity, production volume, and equipment requirements. In general, V-cut de-paneling tends to be more expensive due to the need for specialized cutting tools and equipment. However, the overall cost impact should be evaluated on a case-by-case basis, considering the specific requirements and constraints of the project.
Conclusion
PCB de-paneling is a critical step in the electronics manufacturing process, directly impacting the quality, reliability, and functionality of the final product. Half holes and V-cut are two popular methods for separating individual PCBs from a panel, each with its own advantages and disadvantages.
When choosing between PCB half holes and V-cut de-paneling methods, consider factors such as PCB thickness, edge quality requirements, design constraints, production volume, automation needs, and cost implications. By carefully evaluating these factors and following best practices for de-paneling, you can ensure a smooth and efficient manufacturing process that delivers high-quality PCBs for your specific applications.
As technology advances and new materials and manufacturing techniques emerge, it is essential to stay informed about the latest developments in PCB de-paneling methods. By understanding the strengths and limitations of each method and adapting to evolving industry standards and best practices, you can optimize your PCB manufacturing process and maintain a competitive edge in the fast-paced world of electronics production.
No responses yet