Introduction to PCB Grounding
Proper grounding is essential in the design of printed circuit boards (PCBs) to ensure reliable operation, reduce noise and electromagnetic interference (EMI), and protect sensitive components from damage. PCB grounding involves creating low-impedance paths for currents to return to their source, minimizing voltage differences between components, and shielding sensitive circuits from external noise sources.
In this article, we will explore five common PCB grounding methods and six types of grounding used in electronic circuits. We will also discuss best practices for implementing effective grounding strategies and answer frequently asked questions about PCB grounding.
Why is Proper PCB Grounding Important?
Effective PCB grounding is crucial for several reasons:
- Signal integrity: Proper grounding minimizes noise and ensures clean, undistorted signals throughout the circuit.
- EMI reduction: Well-designed grounding reduces electromagnetic interference, preventing unwanted interactions between components and improving overall system performance.
- Safety: Appropriate grounding protects users and equipment from electrical hazards, such as electric shock and fire.
- Reliability: Robust grounding enhances the long-term reliability of electronic devices by minimizing the risk of component damage due to voltage spikes or transients.
5 PCB Grounding Methods
There are several methods for implementing effective grounding in PCB designs. Each method has its advantages and limitations, and the choice depends on factors such as the circuit’s complexity, frequency of operation, and EMI requirements. Let’s explore five common PCB grounding methods:
1. Single-Point Grounding
Single-point grounding, also known as star grounding, involves connecting all ground points to a single common point, usually near the power supply. This method is suitable for low-frequency circuits and helps minimize ground loops and voltage differences between components.
Advantages:
- Simple to implement
- Minimizes ground loops
- Suitable for low-frequency circuits
Limitations:
- May not be effective for high-frequency circuits
- Requires careful layout to avoid long ground traces
2. Multi-Point Grounding
Multi-point grounding connects ground points to multiple locations on a common ground plane. This method is more suitable for high-frequency circuits and helps reduce ground impedance and EMI.
Advantages:
- Lower ground impedance
- Better EMI reduction
- Suitable for high-frequency circuits
Limitations:
- More complex to implement
- Requires careful layout to avoid ground loops
3. Hybrid Grounding
Hybrid grounding combines single-point and multi-point grounding techniques. It involves using single-point grounding for low-frequency components and multi-point grounding for high-frequency components. This method offers a balance between the benefits of both techniques.
Advantages:
- Combines benefits of single-point and multi-point grounding
- Suitable for circuits with both low and high-frequency components
Limitations:
- More complex to implement
- Requires careful segregation of low and high-frequency components
4. Partitioned Ground Planes
Partitioned ground planes involve dividing the ground plane into separate sections for different circuit functions, such as analog, digital, and power. This method helps isolate noise-sensitive circuits from noisy components and reduces EMI.
Advantages:
- Isolates noise-sensitive circuits
- Reduces EMI between different circuit sections
Limitations:
- Requires careful layout and separation of ground planes
- May increase PCB complexity and manufacturing cost
5. Gridded Ground Planes
Gridded ground planes use a mesh-like structure of ground traces to create a low-impedance path for return currents. This method helps maintain a consistent ground reference across the PCB and reduces EMI.
Advantages:
- Maintains consistent ground reference
- Reduces EMI
- Suitable for high-frequency circuits
Limitations:
- Requires more PCB real estate
- May increase PCB complexity and manufacturing cost
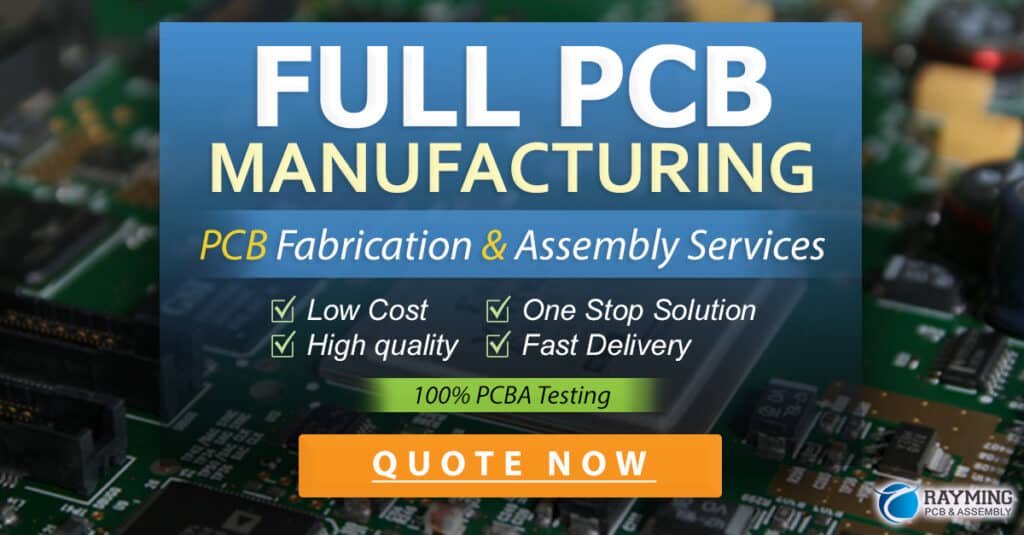
6 Types of Grounding in Circuits
In addition to the PCB grounding methods discussed above, there are several types of grounding used in electronic circuits. These grounding types serve different purposes and are chosen based on the specific requirements of the circuit. Let’s examine six common types of grounding:
1. Earth Ground
Earth ground, also known as protective earth (PE) or safety ground, is a connection to the earth or a conductive body that serves as a reference point for zero potential. It is primarily used for safety purposes to protect users and equipment from electrical hazards.
2. Chassis Ground
Chassis ground refers to the connection of the circuit’s metal enclosure or chassis to the ground. This type of grounding helps shield sensitive components from external EMI and provides a low-impedance path for noise currents.
3. Digital Ground
Digital ground is a dedicated ground plane or trace used for digital circuits. It is separated from analog and power grounds to minimize noise coupling between digital and sensitive analog circuits.
4. Analog Ground
Analog ground is a dedicated ground plane or trace used for analog circuits. It is isolated from digital and power grounds to minimize noise coupling and maintain signal integrity.
5. Power Ground
Power ground is the ground connection for the power supply. It is typically connected to the circuit’s ground at a single point, usually near the power supply, to avoid ground loops and minimize noise.
6. Shield Ground
Shield ground is used to connect cable shields or conductive enclosures to the ground. This type of grounding helps reduce EMI and provides a low-impedance path for noise currents induced on the shield.
Best Practices for PCB Grounding
To ensure effective grounding in PCB designs, consider the following best practices:
-
Plan grounding early: Incorporate grounding considerations early in the PCB design process to optimize layout and minimize potential issues.
-
Use appropriate grounding method: Choose the grounding method that best suits your circuit’s requirements, considering factors such as frequency, noise sensitivity, and EMI.
-
Minimize ground impedance: Use wide, short, and direct ground traces to minimize ground impedance and ensure a low-resistance path for return currents.
-
Separate ground planes: Use separate ground planes for analog, digital, and power circuits to minimize noise coupling and maintain signal integrity.
-
Avoid ground loops: Carefully route ground connections to avoid creating ground loops, which can introduce noise and degrade performance.
-
Use ground vias: Place ground vias near components to provide a low-impedance path for return currents and minimize the length of ground traces.
-
Consider EMI shielding: Use shielding techniques, such as ground planes and conductive enclosures, to reduce EMI and protect sensitive circuits.
-
Test and validate: Perform thorough testing and validation of the PCB design to ensure proper grounding and identify any potential issues.
Frequently Asked Questions (FAQ)
1. What is the difference between single-point and multi-point grounding?
Single-point grounding connects all ground points to a single common point, while multi-point grounding connects ground points to multiple locations on a common ground plane. Single-point grounding is suitable for low-frequency circuits and helps minimize ground loops, while multi-point grounding is more effective for high-frequency circuits and reduces ground impedance.
2. When should I use partitioned ground planes?
Partitioned ground planes are useful when you have noise-sensitive circuits that need to be isolated from noisy components. By dividing the ground plane into separate sections for analog, digital, and power circuits, you can reduce EMI and maintain signal integrity.
3. What is the purpose of chassis ground?
Chassis ground is used to connect the metal enclosure or chassis of a circuit to the ground. This helps shield sensitive components from external EMI and provides a low-impedance path for noise currents, improving the overall performance and reliability of the circuit.
4. How can I minimize ground impedance in my PCB design?
To minimize ground impedance, use wide, short, and direct ground traces. This ensures a low-resistance path for return currents and helps maintain a consistent ground reference across the PCB. Additionally, place ground vias near components to provide a low-impedance path for return currents and minimize the length of ground traces.
5. What are the consequences of poor PCB grounding?
Poor PCB grounding can lead to several issues, including:
- Increased noise and EMI
- Degraded signal integrity
- Reduced reliability and performance
- Potential safety hazards, such as electric shock
To avoid these consequences, it is essential to implement effective grounding strategies and follow best practices throughout the PCB design process.
Conclusion
Proper PCB grounding is crucial for ensuring reliable operation, reducing noise and EMI, and protecting sensitive components from damage. By understanding the different PCB grounding methods and types of grounding used in electronic circuits, designers can make informed decisions and implement effective grounding strategies in their PCB designs.
Remember to consider factors such as circuit complexity, frequency of operation, and EMI requirements when choosing the appropriate grounding method. Additionally, follow best practices, such as minimizing ground impedance, separating ground planes, and avoiding ground loops, to optimize the performance and reliability of your PCB.
By prioritizing proper PCB grounding and staying informed about the latest techniques and best practices, you can create robust and reliable electronic devices that meet the demands of today’s increasingly complex applications.
PCB Grounding Method | Description | Advantages | Limitations |
---|---|---|---|
Single-Point Grounding | Connects all ground points to a single common point | – Simple to implement – Minimizes ground loops – Suitable for low-frequency circuits |
– May not be effective for high-frequency circuits – Requires careful layout to avoid long ground traces |
Multi-Point Grounding | Connects ground points to multiple locations on a common ground plane | – Lower ground impedance – Better EMI reduction – Suitable for high-frequency circuits |
– More complex to implement – Requires careful layout to avoid ground loops |
Hybrid Grounding | Combines single-point and multi-point grounding techniques | – Combines benefits of single-point and multi-point grounding – Suitable for circuits with both low and high-frequency components |
– More complex to implement – Requires careful segregation of low and high-frequency components |
Partitioned Ground Planes | Divides the ground plane into separate sections for different circuit functions | – Isolates noise-sensitive circuits – Reduces EMI between different circuit sections |
– Requires careful layout and separation of ground planes – May increase PCB complexity and manufacturing cost |
Gridded Ground Planes | Uses a mesh-like structure of ground traces to create a low-impedance path for return currents | – Maintains consistent ground reference – Reduces EMI – Suitable for high-frequency circuits |
– Requires more PCB real estate – May increase PCB complexity and manufacturing cost |
Grounding Type | Description |
---|---|
Earth Ground | A connection to the earth or a conductive body that serves as a reference point for zero potential, primarily used for safety purposes |
Chassis Ground | The connection of the circuit’s metal enclosure or chassis to the ground, helps shield sensitive components from external EMI |
Digital Ground | A dedicated ground plane or trace used for digital circuits, separated from analog and power grounds to minimize noise coupling |
Analog Ground | A dedicated ground plane or trace used for analog circuits, isolated from digital and power grounds to maintain signal integrity |
Power Ground | The ground connection for the power supply, typically connected to the circuit’s ground at a single point near the power supply |
Shield Ground | Used to connect cable shields or conductive enclosures to the ground, helps reduce EMI and provides a low-impedance path for noise currents |
No responses yet