Understanding PCBA Contamination
Before diving into the cleaning methods, it is essential to understand the types of contamination that can affect PCBAs. Common contaminants include:
- Flux residues
- Dust and debris
- Oils and greases
- Corrosion
- Fungal growth
Each type of contamination requires a specific cleaning approach to ensure the best results without causing damage to the PCBA.
Factors to Consider Before Cleaning PCBA
When planning to clean your PCBA, consider the following factors:
- The type of contamination present
- The materials used in the PCBA (e.g., solder mask, conformal coating)
- The sensitivity of components to cleaning agents and methods
- The accessibility of the contaminated areas
- The available cleaning equipment and resources
Taking these factors into account will help you choose the most appropriate cleaning method and avoid potential issues during the cleaning process.
Cleaning Methods for PCBA
There are several cleaning methods suitable for PCBAs, each with its own advantages and disadvantages. The most common methods include:
1. Manual Cleaning
Manual cleaning involves using brushes, swabs, or wipes to remove contamination from the PCBA surface. This method is suitable for localized cleaning or when dealing with sensitive components that may be damaged by more aggressive cleaning techniques.
Advantages:
– Precise and targeted cleaning
– Minimal risk of damage to sensitive components
– Low cost and minimal equipment required
Disadvantages:
– Time-consuming and labor-intensive
– Inconsistent results, depending on the operator’s skill
– Limited effectiveness for heavy contamination or hard-to-reach areas
2. Ultrasonic Cleaning
Ultrasonic cleaning uses high-frequency sound waves to agitate a cleaning solution, creating tiny bubbles that implode and release energy, effectively removing contamination from the PCBA surface.
Advantages:
– Thorough cleaning, even in hard-to-reach areas
– Efficient removal of stubborn contamination
– Automated process, reducing labor costs
Disadvantages:
– Risk of damage to sensitive components due to high-frequency vibrations
– Requires specialized equipment and cleaning solutions
– May not be suitable for all types of PCBAs
3. Spray Cleaning
Spray cleaning involves using pressurized air or liquid to dispense cleaning agents onto the PCBA surface. This method is effective for removing loose contamination and drying the PCBA after cleaning.
Advantages:
– Fast and efficient cleaning process
– Suitable for large-scale cleaning operations
– Effective removal of loose contamination
Disadvantages:
– Risk of damage to sensitive components due to high-pressure spray
– Potential for incomplete cleaning in hard-to-reach areas
– Requires specialized equipment and cleaning solutions
4. Vapor Degreasing
Vapor degreasing uses a boiling solvent to create a vapor that condenses on the PCBA surface, dissolving and removing contamination. The condensed solvent then drips back into the boiling reservoir, carrying the contaminants with it.
Advantages:
– Thorough and efficient cleaning
– Minimal risk of damage to sensitive components
– Automated process, reducing labor costs
Disadvantages:
– Requires specialized equipment and solvents
– Potential for solvent residues on the PCBA surface
– Environmental and health concerns associated with solvent use
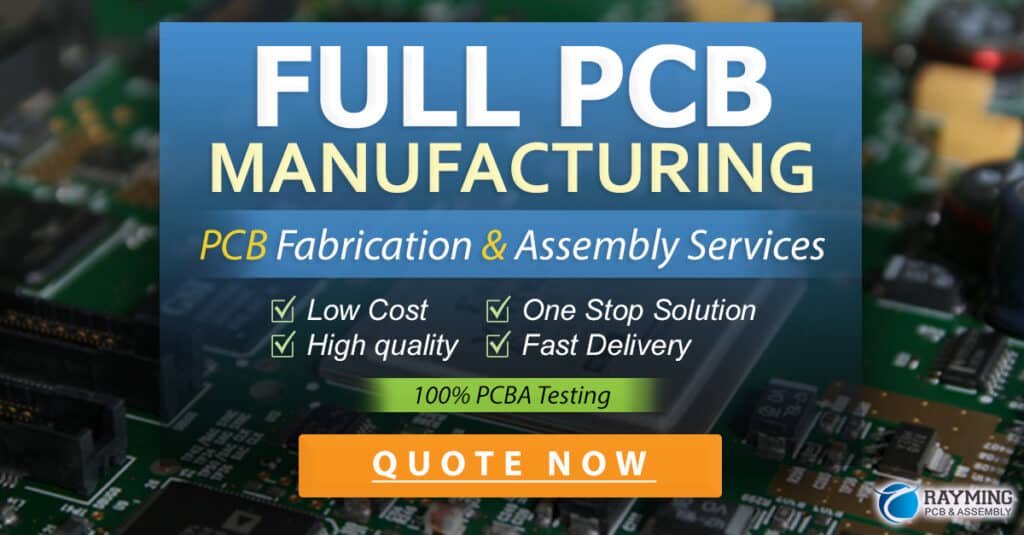
Selecting the Right Cleaning Agents
Choosing the appropriate cleaning agents is crucial for effective PCBA Cleaning without causing damage. Common cleaning agents include:
- Isopropyl alcohol (IPA)
- Deionized water
- Specialized solvents (e.g., terpenes, hydrocarbons)
- Aqueous cleaning solutions
When selecting a cleaning agent, consider the following factors:
- Compatibility with PCBA materials and components
- Effectiveness in removing the specific type of contamination
- Environmental and health concerns
- Cost and availability
Always refer to the manufacturer’s recommendations and safety data sheets when choosing cleaning agents for your PCBA.
Best Practices for PCBA Cleaning
To ensure the best results and minimize the risk of damage during PCBA cleaning, follow these best practices:
- Always wear appropriate personal protective equipment (PPE) when handling cleaning agents and equipment.
- Follow the manufacturer’s guidelines for cleaning agents and equipment usage.
- Test the cleaning method and agents on a small, non-critical area of the PCBA before proceeding with the entire assembly.
- Use the minimum amount of cleaning agent necessary to avoid excessive residue or damage to the PCBA.
- Ensure proper ventilation and temperature control during the cleaning process.
- Allow sufficient drying time after cleaning to prevent moisture-related issues.
- Inspect the PCBA thoroughly after cleaning to verify the removal of contamination and the absence of damage.
By adhering to these best practices, you can minimize the risk of damage and ensure the effectiveness of your PCBA cleaning process.
Common PCBA Cleaning Challenges and Solutions
Despite following best practices and selecting appropriate cleaning methods, challenges may arise during the PCBA cleaning process. Some common challenges and their solutions include:
Challenge 1: Incomplete removal of contamination
Solution: Adjust the cleaning method, increase the cleaning time, or use a more effective cleaning agent. Re-evaluate the type of contamination and ensure the chosen method is suitable.
Challenge 2: Damage to sensitive components
Solution: Use a gentler cleaning method, such as manual cleaning or a less aggressive cleaning agent. Consider protecting sensitive components with conformal coatings or temporary masking.
Challenge 3: Residues left behind after cleaning
Solution: Ensure proper rinsing and drying of the PCBA after cleaning. Use a more volatile cleaning agent that evaporates quickly without leaving residues.
Challenge 4: Difficulty accessing contaminated areas
Solution: Use specialized cleaning tools, such as brushes or swabs with varying shapes and sizes, to reach hard-to-access areas. Consider using a cleaning method with better penetration, such as ultrasonic cleaning.
By addressing these challenges and adapting your cleaning approach accordingly, you can overcome obstacles and achieve optimal results in your PCBA cleaning process.
PCBA Cleaning Equipment and Tools
To perform effective PCBA cleaning, you may need the following equipment and tools:
- Brushes and swabs
- Lint-free wipes or cloths
- Compressed air or air blower
- Ultrasonic cleaning tank
- Spray cleaning system
- Vapor degreasing machine
- Personal protective equipment (gloves, safety glasses, respirator)
Invest in high-quality equipment and tools to ensure consistent and reliable cleaning results while minimizing the risk of damage to your PCBAs.
Frequently Asked Questions (FAQ)
1. How often should I clean my PCBA?
The frequency of PCBA cleaning depends on factors such as the operating environment, the type of contamination, and the criticality of the device. As a general rule, clean your PCBA when you notice visible contamination, experience performance issues, or as part of a regular maintenance schedule recommended by the manufacturer.
2. Can I use household cleaning agents to clean my PCBA?
No, it is not recommended to use household cleaning agents for PCBA cleaning. These products may contain chemicals that can damage the PCBA or leave harmful residues. Always use cleaning agents specifically designed for electronic components and PCBAs.
3. Is it necessary to wear personal protective equipment (PPE) when cleaning PCBAs?
Yes, wearing appropriate PPE is essential when cleaning PCBAs. Cleaning agents can be harmful if inhaled or come into contact with skin or eyes. Always wear gloves, safety glasses, and a respirator (if required) to protect yourself during the cleaning process.
4. Can I clean a PCBA without removing it from the device?
In some cases, it may be possible to clean a PCBA without removing it from the device. However, this depends on the accessibility of the PCBA and the cleaning method used. If the PCBA is easily accessible and the cleaning method is suitable for in-situ cleaning, you may be able to clean it without removal. Always consult the device manufacturer’s guidelines before attempting in-situ cleaning.
5. How do I know if my PCBA is clean enough?
Visually inspect the PCBA after cleaning to ensure that all visible contamination has been removed. You can also use a magnifying glass or microscope to check for any remaining contaminants. Some advanced methods, such as ionic contamination testing or surface insulation resistance (SIR) testing, can provide quantitative measurements of cleanliness. However, these methods require specialized equipment and are generally used in professional manufacturing and testing environments.
By following the guidelines, best practices, and solutions presented in this article, you can effectively clean your PCBA while minimizing the risk of damage. Regular and proper cleaning will help maintain the performance and longevity of your electronic devices, ensuring their reliable operation for years to come.
No responses yet