Introduction to Glass PCBs
Glass Printed Circuit Boards (Glass PCBs) are an emerging technology in the world of PCB design and manufacturing. Unlike traditional PCBs that use FR4 or other polymer-based substrates, Glass PCBs utilize thin sheets of glass as the base material. This unique substrate offers several advantages over conventional PCB materials, making Glass PCBs an attractive option for certain applications.
What are Glass PCBs?
Glass PCBs are printed circuit boards that use glass as the primary substrate material instead of the more common FR4 or other polymer-based materials. The glass used in these PCBs is typically a thin, tempered glass that provides excellent electrical insulation and mechanical stability. The conductive traces and components are then mounted on the glass substrate using standard PCB manufacturing processes, such as photolithography, etching, and soldering.
Advantages of Glass PCBs
-
Transparency: Glass is a transparent material, allowing for unique design possibilities and visual inspection of the PCB’s internal structure.
-
High Thermal Stability: Glass has a low coefficient of thermal expansion (CTE), which makes it more stable under varying temperature conditions compared to FR4.
-
Excellent Electrical Insulation: Glass provides superior electrical insulation properties, making it suitable for high-frequency and high-voltage applications.
-
Dimensional Stability: Glass PCBs maintain their shape and size even under stress, reducing the risk of warping or deformation.
-
Environmentally Friendly: Glass is an inert and recyclable material, making Glass PCBs a more environmentally friendly option compared to traditional PCBs.
Applications of Glass PCBs
High-Frequency and RF Applications
Glass PCBs are particularly well-suited for high-frequency and radio frequency (RF) applications due to their excellent electrical insulation properties and low dielectric constant. The low dielectric constant of glass reduces signal loss and allows for faster signal propagation, making it ideal for applications such as:
- 5G wireless communication systems
- Radar and satellite communication
- High-speed digital circuits
- Microwave devices
Automotive and Aerospace Industries
The automotive and aerospace industries require PCBs that can withstand harsh environmental conditions, such as extreme temperatures and vibrations. Glass PCBs offer a high degree of thermal and mechanical stability, making them suitable for these demanding applications. Examples include:
- Engine control units (ECUs)
- Satellite and spacecraft electronics
- Avionics and flight control systems
- Vehicle infotainment systems
Medical Devices and Instruments
Glass PCBs are also finding applications in the medical device and instrument industry due to their transparency and compatibility with sterilization processes. The transparency of glass allows for easy visual inspection of the PCB’s internal structure, which is crucial for medical devices that require high reliability and safety standards. Some examples of medical applications include:
- Implantable medical devices
- Diagnostic imaging equipment
- Surgical instruments
- Biosensors and lab-on-a-chip devices
Manufacturing Process of Glass PCBs
Substrate Preparation
The first step in manufacturing Glass PCBs is preparing the glass substrate. The glass is typically a thin, tempered sheet that is cut to the desired size and shape. The glass surface is then cleaned and treated to improve adhesion of the conductive traces and components.
Metallization and Patterning
Next, a thin layer of conductive material, such as copper or aluminum, is deposited onto the glass substrate using techniques like sputtering or evaporation. The conductive layer is then patterned using photolithography and etching processes to create the desired circuit traces and pads.
Component Assembly
Once the circuit pattern is formed on the glass substrate, electronic components are mounted onto the PCB using standard assembly techniques, such as surface mount technology (SMT) or through-hole mounting. The components are then soldered to the PCB using reflow or Wave Soldering processes.
Finishing and Coating
Finally, the assembled Glass PCB undergoes a finishing process to protect the circuitry and improve its durability. This may include applying a conformal coating or encapsulating the PCB in a protective housing, depending on the application requirements.
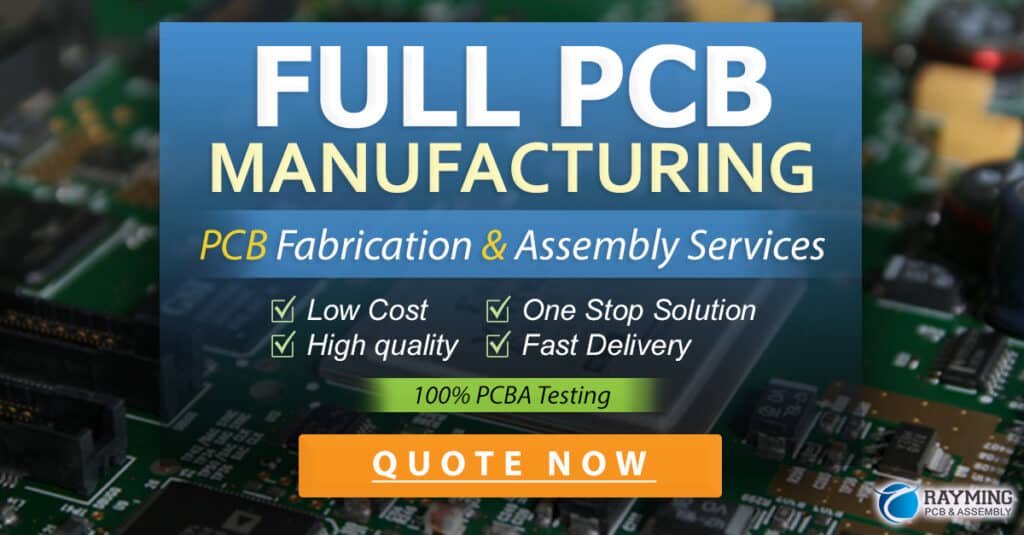
Challenges and Considerations
Cost Considerations
One of the main challenges associated with Glass PCBs is their higher cost compared to traditional FR4-based PCBs. The specialized materials and manufacturing processes required for Glass PCBs contribute to their increased cost. However, as the technology matures and demand grows, it is expected that the cost of Glass PCBs will decrease over time.
Mechanical Strength
Although glass is a strong material, it is also brittle and can be prone to cracking or shattering under certain conditions. Designers must take into account the mechanical stresses that the Glass PCB will be subjected to and design accordingly. Proper handling and mounting techniques are crucial to ensure the long-term reliability of Glass PCBs.
Thermal Management
While glass has a low CTE, it also has a relatively low thermal conductivity compared to other PCB materials. This can present challenges in applications that generate significant heat, as the glass substrate may not dissipate heat as efficiently as other materials. Designers must carefully consider the thermal management requirements of their application and incorporate appropriate cooling solutions, such as heat sinks or thermal vias.
Compatibility with Existing Manufacturing Processes
Glass PCBs may require some modifications to existing PCB manufacturing processes and equipment. For example, the handling and processing of thin glass substrates may require specialized tooling and fixturing. Manufacturers must adapt their processes and equipment to accommodate the unique properties of glass substrates.
Future Outlook and Potential
Emerging Applications
As the technology behind Glass PCBs continues to advance, new applications are emerging that leverage the unique properties of glass substrates. Some potential future applications include:
- Flexible and wearable electronics: The use of thin, flexible glass substrates could enable the development of novel wearable devices and flexible electronics.
- Optoelectronic integration: The transparency of glass opens up possibilities for integrating optical components, such as waveguides and photonic circuits, directly onto the PCB.
- Advanced packaging solutions: Glass PCBs could be used as interposers or substrates for advanced packaging technologies, such as 2.5D and 3D integrated circuits.
Research and Development Efforts
Significant research and development efforts are underway to further improve the performance and manufacturability of Glass PCBs. Some areas of focus include:
- Developing new glass materials with enhanced properties, such as higher thermal conductivity or improved mechanical strength.
- Optimizing manufacturing processes to reduce cost and increase yield.
- Exploring hybrid PCB designs that combine glass with other materials, such as FR4 or ceramics, to leverage the strengths of each material.
Industry Adoption and Standardization
As Glass PCBs gain traction in various industries, there is a growing need for standardization and industry-wide adoption. Collaborative efforts between material suppliers, PCB manufacturers, and end-users are crucial to establish common guidelines and best practices for designing and manufacturing Glass PCBs. Industry organizations, such as IPC (Association Connecting Electronics Industries), are actively working on developing standards and specifications for Glass PCBs to facilitate their widespread adoption.
Frequently Asked Questions (FAQ)
-
Q: How do the costs of Glass PCBs compare to traditional FR4 PCBs?
A: Glass PCBs are currently more expensive than FR4 PCBs due to the specialized materials and manufacturing processes involved. However, as the technology matures and demand increases, it is expected that the cost of Glass PCBs will decrease over time. -
Q: Can Glass PCBs be used for flexible electronics applications?
A: Yes, thin and flexible glass substrates are being developed that could enable the use of Glass PCBs in flexible and wearable electronics applications. However, this technology is still in the research and development stage and is not yet widely available. -
Q: Are Glass PCBs compatible with standard PCB Assembly processes?
A: Glass PCBs are generally compatible with standard PCB assembly processes, such as SMT and through-hole mounting. However, some modifications to the manufacturing process and equipment may be necessary to accommodate the unique properties of glass substrates. -
Q: What are the main advantages of using Glass PCBs over traditional PCBs?
A: Glass PCBs offer several advantages over traditional PCBs, including transparency, high thermal stability, excellent electrical insulation, dimensional stability, and environmental friendliness. These properties make Glass PCBs well-suited for applications such as high-frequency and RF circuits, automotive and aerospace electronics, and medical devices. -
Q: Are there any specific design considerations for Glass PCBs?
A: Yes, designers must take into account the mechanical strength and thermal management properties of glass when designing Glass PCBs. Proper handling and mounting techniques are crucial to ensure the long-term reliability of the PCBs. Additionally, designers may need to incorporate appropriate cooling solutions to manage heat dissipation in applications that generate significant heat.
Conclusion
Glass Printed Circuit Boards represent an exciting new technology in the world of PCB design and manufacturing. With their unique properties, such as transparency, high thermal stability, and excellent electrical insulation, Glass PCBs offer a compelling alternative to traditional PCB materials for certain applications.
While there are challenges associated with Glass PCBs, such as higher costs and specific design considerations, ongoing research and development efforts are addressing these issues and paving the way for wider adoption. As the technology matures and industry standards emerge, it is expected that Glass PCBs will find increasing use in various industries, from high-frequency electronics to automotive and medical applications.
PCB designers and manufacturers should keep a close eye on the development of Glass PCBs and consider them as a potential option for their future projects. By leveraging the unique properties of glass substrates, designers can push the boundaries of PCB Performance and enable new and innovative applications.
Property | Glass PCBs | FR4 PCBs |
---|---|---|
Substrate Material | Thin Glass | FR4 |
Transparency | Yes | No |
Thermal Stability (CTE) | Low | Moderate |
Electrical Insulation | Excellent | Good |
Dimensional Stability | High | Moderate |
Environmental Friendliness | High | Moderate |
Cost | Higher | Lower |
Mechanical Strength | Brittle | Robust |
Thermal Conductivity | Low | Moderate |
Table: Comparison of key properties between Glass PCBs and FR4 PCBs
In conclusion, Glass PCBs represent a promising new technology that offers unique advantages over traditional PCB materials. As the technology continues to evolve and mature, it is poised to open up new possibilities in PCB design and enable the development of innovative electronic products across various industries.
No responses yet