What is Ceramic PCB Manufacturing?
Ceramic printed circuit board (PCB) manufacturing is a process that involves creating circuit boards using ceramic materials as the base substrate. Ceramic PCBs offer several advantages over traditional FR-4 PCBs, such as higher thermal conductivity, better electrical insulation, and improved durability in harsh environments. These properties make ceramic PCBs ideal for applications in the aerospace, automotive, and military industries, as well as in high-power electronics and LED lighting.
Advantages of Ceramic PCBs
- High thermal conductivity
- Excellent electrical insulation
- Improved durability in harsh environments
- Low dielectric constant and loss tangent
- Resistance to high temperatures and thermal shock
- High mechanical strength and rigidity
The 7 Ceramic PCB Manufacturing Processes
The ceramic PCB manufacturing process involves several steps, each of which plays a crucial role in determining the quality and performance of the final product. The following are the seven main processes involved in ceramic PCB manufacturing:
1. Material Preparation
The first step in ceramic PCB manufacturing is to prepare the ceramic substrate material. The most commonly used ceramic materials for PCBs are alumina (Al2O3) and aluminum nitride (AlN). These materials are chosen for their excellent thermal and electrical properties.
The ceramic substrate is typically provided in the form of a green tape, which is a flexible, unfired ceramic material. The green tape is cut to the desired size and shape using a laser or mechanical punching process.
2. Via Hole Formation
Once the ceramic substrate is prepared, the next step is to create via holes. Via holes are small holes drilled through the ceramic substrate to allow electrical connections between different layers of the PCB.
There are several methods for creating via holes in ceramic PCBs, including:
- Mechanical drilling
- Laser drilling
- Punching
The choice of method depends on the size and density of the via holes required, as well as the thickness of the ceramic substrate.
3. Conductive Paste Printing
After the via holes are formed, a conductive paste is printed onto the ceramic substrate to create the desired circuit pattern. The conductive paste is typically made of a mixture of metal particles (such as silver, gold, or copper) and a glass frit, which helps the metal adhere to the ceramic substrate.
The conductive paste is applied using a screen printing process, where a stencil with the desired circuit pattern is placed over the ceramic substrate, and the paste is forced through the openings in the stencil using a squeegee.
4. Stacking and Lamination
If the ceramic PCB design requires multiple layers, the next step is to stack and laminate the printed ceramic substrates together. The substrates are aligned and stacked in the desired order, with conductive paste applied between each layer to create electrical connections.
The stacked substrates are then laminated together under high pressure and temperature to form a solid, multilayer structure. The lamination process typically involves the use of a hydraulic press and a controlled heating and cooling cycle.
5. Firing
After lamination, the ceramic PCB is subjected to a high-temperature firing process. During firing, the ceramic substrate and conductive paste are sintered together to form a dense, solid material with excellent mechanical and electrical properties.
The firing process typically involves heating the ceramic PCB to temperatures between 850°C and 1,600°C, depending on the specific ceramic material and conductive paste used. The firing cycle is carefully controlled to ensure uniform heating and cooling, which helps to minimize thermal stress and prevent warping or cracking of the ceramic substrate.
6. Post-Firing Processing
After firing, the ceramic PCB may undergo additional post-processing steps, depending on the specific application requirements. These steps can include:
- Surface grinding and polishing to achieve a smooth, flat surface
- Cutting and shaping to the final desired dimensions
- Drilling additional holes for component mounting or attachment
- Applying surface finishes, such as nickel/gold plating, to improve solderability and corrosion resistance
7. Quality Control and Testing
The final step in the ceramic PCB manufacturing process is quality control and testing. Each ceramic PCB is thoroughly inspected for defects, such as cracks, voids, or misaligned layers, using a combination of visual inspection and automated optical inspection (AOI) techniques.
Electrical testing is also performed to ensure that the ceramic PCB meets the specified performance requirements, such as impedance, capacitance, and insulation resistance. This may involve the use of specialized test equipment, such as network analyzers and high-voltage test systems.
Ceramic PCB Manufacturing Process Flow
The following table summarizes the main steps involved in the ceramic PCB manufacturing process:
Step | Process | Description |
---|---|---|
1 | Material Preparation | Cut ceramic green tape to desired size and shape |
2 | Via Hole Formation | Create via holes using mechanical drilling, laser drilling, or punching |
3 | Conductive Paste Printing | Print conductive paste onto ceramic substrate using screen printing |
4 | Stacking and Lamination | Stack and laminate printed ceramic substrates together under high pressure and temperature |
5 | Firing | Sinter ceramic substrate and conductive paste together at high temperatures |
6 | Post-Firing Processing | Perform additional processing steps, such as surface grinding, cutting, drilling, and plating |
7 | Quality Control and Testing | Inspect and test ceramic PCBs for defects and performance requirements |
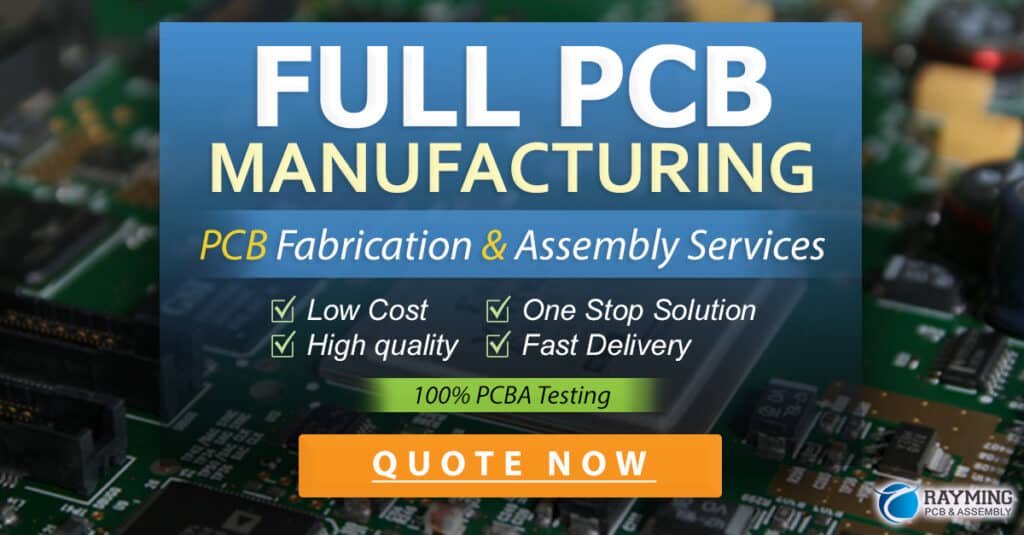
Frequently Asked Questions (FAQ)
-
What are the main advantages of ceramic PCBs compared to traditional FR-4 PCBs?
Ceramic PCBs offer several advantages over FR-4 PCBs, including higher thermal conductivity, better electrical insulation, improved durability in harsh environments, low dielectric constant and loss tangent, resistance to high temperatures and thermal shock, and high mechanical strength and rigidity. -
What are the most common ceramic materials used for PCB manufacturing?
The most commonly used ceramic materials for PCB manufacturing are alumina (Al2O3) and aluminum nitride (AlN). These materials are chosen for their excellent thermal and electrical properties. -
What methods are used to create via holes in ceramic PCBs?
Via holes in ceramic PCBs can be created using mechanical drilling, laser drilling, or punching. The choice of method depends on the size and density of the via holes required, as well as the thickness of the ceramic substrate. -
How are the different layers of a multilayer ceramic PCB connected?
In a multilayer ceramic PCB, the different layers are connected using conductive paste applied between each layer. The stacked layers are then laminated together under high pressure and temperature to form a solid, multilayer structure with electrical connections between the layers. -
What quality control and testing methods are used in ceramic PCB manufacturing?
Quality control and testing in ceramic PCB manufacturing involve a combination of visual inspection, automated optical inspection (AOI), and electrical testing. Each ceramic PCB is thoroughly inspected for defects, such as cracks, voids, or misaligned layers, and tested for electrical performance requirements, such as impedance, capacitance, and insulation resistance.
Conclusion
Ceramic PCB manufacturing is a complex process that involves several critical steps, from material preparation and via hole formation to conductive paste printing, stacking and lamination, firing, post-processing, and quality control. Each step plays a crucial role in determining the quality and performance of the final product.
By understanding the various processes involved in ceramic PCB manufacturing, designers and engineers can make informed decisions when selecting ceramic PCBs for their specific applications. With their excellent thermal, electrical, and mechanical properties, ceramic PCBs offer a reliable and high-performance alternative to traditional FR-4 PCBs in demanding environments and applications.
As technology continues to advance and the demand for high-performance electronics grows, the importance of ceramic PCB manufacturing will only continue to increase. By staying up-to-date with the latest developments and best practices in ceramic PCB manufacturing, manufacturers can ensure that they are producing the highest quality products to meet the evolving needs of their customers.
No responses yet