What is AutoDesk Eagle?
AutoDesk Eagle is a powerful electronic design automation (EDA) software that enables users to create schematic diagrams and design PCBs. It offers a user-friendly interface and a wide range of features, making it a popular choice among hobbyists, students, and professionals alike.
Prerequisites
Before we dive into the tutorial, ensure that you have the following:
- A computer running Windows, macOS, or Linux
- AutoDesk Eagle Software installed (free educational licenses are available)
- Basic understanding of electronic components and circuits
Setting Up Your Workspace
Step 1: Create a New Project
- Open AutoDesk Eagle and click on “File” in the menu bar.
- Select “New” and then choose “Project.”
- Give your project a name and select a location to save it.
Step 2: Create a Schematic
- In the project tree, right-click on your project name and select “New” followed by “Schematic.”
- A new schematic editor window will open.
Step 3: Customize the Grid Settings
- Click on “View” in the menu bar and select “Grid.”
- Adjust the grid settings according to your preferences. A common setting is 0.1 inches for the grid size.
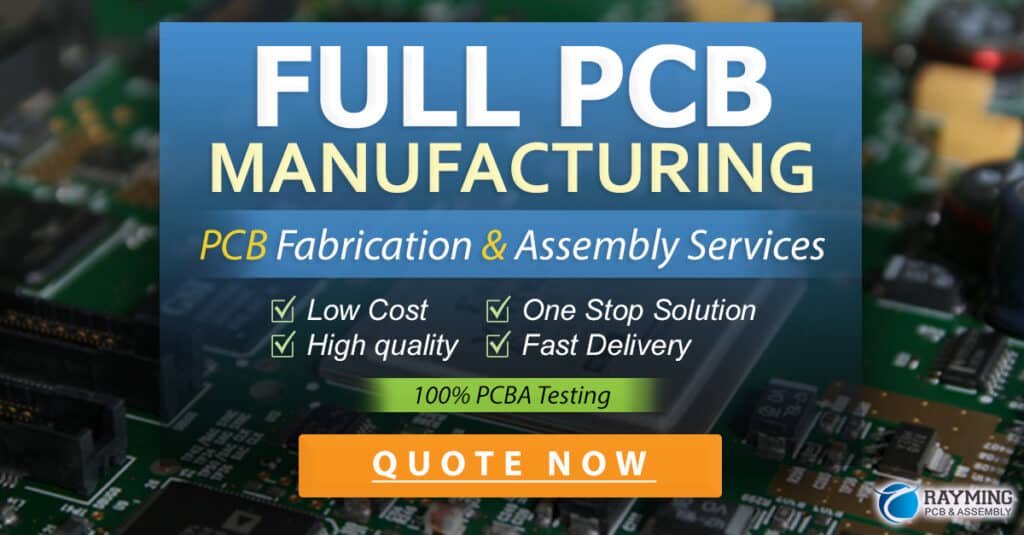
Designing the Schematic
Step 1: Place Components
- Click on the “Add” tool in the left toolbar or press the “Add” button on your keyboard.
- In the “Libraries” dialog, browse through the available libraries and select the components you need.
- Click on the schematic editor to place the components.
Step 2: Wire the Components
- Select the “Net” tool from the left toolbar or press the “N” key on your keyboard.
- Click on the connection points of the components to create wires between them.
- Use the “Name” tool to assign names to the nets if necessary.
Step 3: Add Power and Ground Symbols
- Use the “Add” tool to place power and ground symbols from the “supply1” library.
- Connect the power and ground symbols to the appropriate nets.
Step 4: Check the Schematic
- Click on the “ERC” (Electrical Rule Check) button in the top toolbar to run a check for errors.
- Resolve any issues identified by the ERC.
Creating the PCB Layout
Step 1: Generate a Board from the Schematic
- Click on the “Board” button in the top toolbar or select “File” > “Switch to Board.”
- If prompted, choose “Yes” to create a new board from the schematic.
Step 2: Define the Board Outline
- Select the “Wire” tool from the left toolbar.
- Draw a rectangle to define the outline of your PCB.
Step 3: Place Components
- Use the “Move” tool to arrange the components on the board.
- Ensure that the components are placed within the board outline and with sufficient spacing between them.
Step 4: Route the Traces
- Select the “Route” tool from the left toolbar.
- Click on the connection points of the components to create traces between them.
- Adjust the trace width as needed using the “Change” tool.
Step 5: Add Vias
- Use the “Via” tool to create vias (connections between layers) when necessary.
- Ensure that the via size is appropriate for your PCB manufacturer’s specifications.
Step 6: Define the Ground Plane
- Select the “Polygon” tool from the left toolbar.
- Draw a polygon that covers the entire board area, excluding the component footprints and traces.
- Name the polygon “GND” and set the appropriate settings, such as the isolation distance.
Step 7: Run Design Rule Check (DRC)
- Click on the “DRC” button in the top toolbar to run a design rule check.
- Resolve any violations identified by the DRC.
Generating Gerber Files
Step 1: Open the CAM Processor
- Click on the “CAM” button in the top toolbar or select “File” > “CAM Processor.”
Step 2: Select the Gerber Format
- In the CAM Processor window, click on “File” > “Open” and select the “gerb274x.cam” file.
- Adjust the output directory if necessary.
Step 3: Generate Gerber Files
- Click on the “Process Job” button to generate the Gerber files.
- The generated files will be saved in the specified output directory.
Frequently Asked Questions (FAQ)
1. Can I use AutoDesk Eagle for commercial projects?
Yes, AutoDesk Eagle offers both free and paid licenses. The free educational license is suitable for personal and educational use, while the paid licenses are required for commercial projects.
2. How do I add custom components to my library?
To add custom components, you can create your own library or download existing libraries from online resources. In Eagle, select “Library” > “New Library” to create a new library, and then use the library editor to create or modify components.
3. What are the different layers in a PCB layout?
A PCB layout typically consists of multiple layers, including:
Layer | Description |
---|---|
Top | The top copper layer where components are placed and routed |
Bottom | The bottom copper layer, often used for routing and ground plane |
Silkscreen | The layer containing text and graphics for component identification |
Solder Mask | The protective layer that covers the copper, exposing only the pads |
4. How do I choose the appropriate trace width?
The trace width depends on factors such as the current carrying capacity, voltage drop, and PCB manufacturing capabilities. You can refer to online calculators or consult with your PCB manufacturer for recommended trace widths based on your specific requirements.
5. What are the common file formats for PCB manufacturing?
The most common file formats for PCB manufacturing are:
- Gerber files (RS-274X): These files contain information about the copper layers, solder mask, silkscreen, and drill holes.
- Drill files (Excellon): These files specify the locations and sizes of the drill holes on the PCB.
- Pick and Place files: These files provide information about the component placement on the PCB for automated assembly.
Conclusion
Creating a PCB using AutoDesk Eagle involves several steps, from designing the schematic to generating the Gerber files for manufacturing. By following this tutorial, you should now have a good understanding of the process and be able to create your own PCBs using Eagle.
Remember to double-check your designs, run ERC and DRC checks, and communicate with your PCB manufacturer to ensure that your PCB meets their specifications. With practice and experience, you’ll be able to design more complex PCBs and bring your electronic projects to life.
Happy PCB designing!
No responses yet