How does a Pre-heater work?
Pre-heaters work by utilizing the heat from exhaust gases or other heat sources to raise the temperature of the incoming raw materials. The pre-heating process typically involves a series of cyclones or stages, where the hot gases and raw materials are brought into contact with each other. As the materials pass through each stage, they are gradually heated, with the temperature increasing at each successive stage.
The pre-heater is usually designed as a vertical tower, with the raw materials being fed in at the top and the hot gases entering from the bottom. The materials and gases flow in opposite directions, known as counter-current flow, which maximizes heat transfer efficiency.
Types of Pre-heaters
There are several types of pre-heaters used in various industrial applications:
-
Suspension Pre-heaters: These are the most common type of pre-heaters used in the cement industry. They consist of a series of cyclones arranged vertically, where the raw materials are suspended in the hot exhaust gases from the kiln.
-
Grate Pre-heaters: These pre-heaters are used in the steel industry and consist of a moving grate that carries the raw materials through a chamber heated by exhaust gases.
-
Shaft Pre-heaters: These are vertical shaft-type pre-heaters used in the production of lime and other materials. The raw materials are fed into the top of the shaft, while hot gases are introduced from the bottom.
-
Flash Pre-heaters: These pre-heaters are used in the chemical industry and involve the rapid heating of fine, solid particles by bringing them into contact with hot gases.
Type of Pre-heater | Industry | Description |
---|---|---|
Suspension Pre-heater | Cement | Series of cyclones; raw materials suspended in hot exhaust gases |
Grate Pre-heater | Steel | Moving grate carries raw materials through heated chamber |
Shaft Pre-heater | Lime | Vertical shaft; raw materials fed from top, hot gases from bottom |
Flash Pre-heater | Chemical | Rapid heating of fine, solid particles by contact with hot gases |
Benefits of using a Pre-heater
The use of pre-heaters offers several significant benefits in industrial processes:
Energy Efficiency
Pre-heating raw materials before they enter the main processing unit reduces the amount of energy required to bring them up to the desired temperature. By utilizing waste heat from exhaust gases, pre-heaters can significantly improve the overall energy efficiency of the process. This translates to lower fuel consumption and reduced operating costs.
Increased Production Capacity
With pre-heaters, the main processing unit can operate more efficiently, as it does not need to expend as much energy heating the raw materials. This allows for higher production rates and increased capacity, as the processing unit can focus on its primary function of converting the raw materials into the desired end product.
Improved Product Quality
Pre-heating raw materials can also enhance the quality of the final product. By ensuring that the materials enter the main processing unit at a uniform and optimal temperature, pre-heaters help to reduce thermal stresses and minimize variations in the end product. This results in more consistent quality and fewer defects.
Reduced Emissions
By improving energy efficiency and reducing fuel consumption, pre-heaters also contribute to lower emissions of greenhouse gases and other pollutants. This is particularly important in industries such as cement production, which is known for its high carbon footprint. The use of pre-heaters can help mitigate the environmental impact of these processes.
Applications of Pre-heaters
Pre-heaters find extensive use in various industries, with some of the most notable applications being:
Cement Industry
In the cement industry, suspension pre-heaters are used to heat the raw meal (a mixture of limestone and other materials) before it enters the rotary kiln. The raw meal is fed into the top of the pre-heater tower, while hot exhaust gases from the kiln enter from the bottom. As the meal passes through the series of cyclones, it is progressively heated by the counter-current flow of hot gases. By the time the raw meal reaches the kiln, it is already partially calcined, which reduces the energy required in the kiln and improves the overall efficiency of the cement production process.
Steel Industry
In the steel industry, grate pre-heaters are used to heat the iron ore, coke, and other raw materials before they are fed into the blast furnace. The raw materials are carried on a moving grate through a chamber heated by the hot exhaust gases from the blast furnace. This pre-heating process reduces the amount of coke required in the blast furnace, thereby lowering costs and improving efficiency.
Lime Production
Shaft pre-heaters are commonly used in the production of lime. The limestone is fed into the top of the vertical shaft, while hot gases from the lime kiln are introduced from the bottom. As the limestone descends through the shaft, it is gradually heated by the rising hot gases. This pre-heating process helps to reduce the energy required in the lime kiln and improves the quality of the final product.
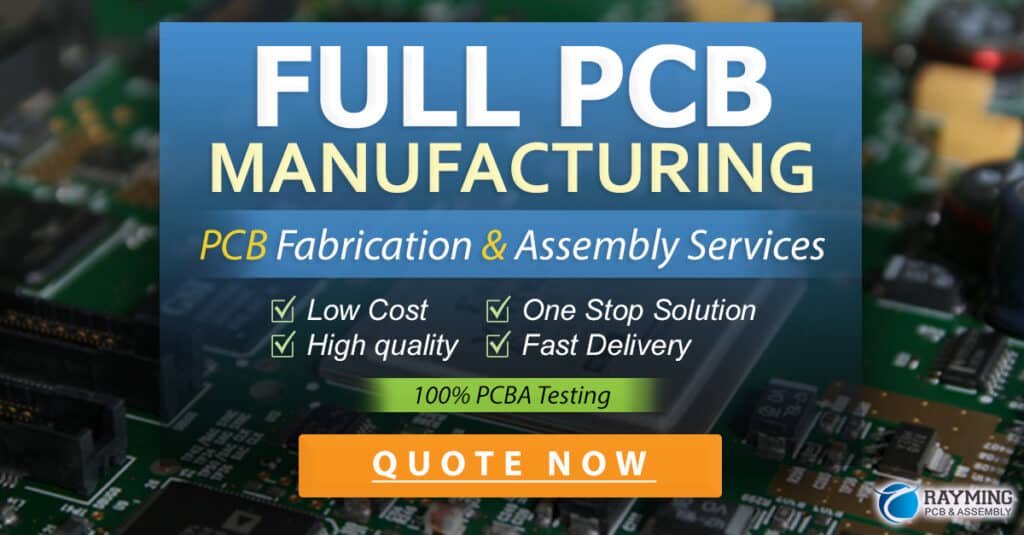
Future Developments in Pre-heater Technology
As industries continue to focus on improving efficiency, reducing costs, and minimizing environmental impact, pre-heater technology is expected to evolve and advance. Some potential future developments include:
Integration with Renewable Energy Sources
Pre-heaters could be designed to utilize heat from renewable energy sources, such as solar thermal or geothermal energy. This would further reduce the reliance on fossil fuels and lower the carbon footprint of industrial processes.
Advanced Materials and Coatings
The development of advanced materials and coatings that can withstand higher temperatures and resist corrosion could extend the life of pre-heaters and improve their performance. This could lead to longer maintenance intervals and reduced downtime.
Smart Control Systems
The integration of smart control systems and sensors could enable real-time monitoring and optimization of pre-heater performance. By continuously adjusting operating parameters based on data from sensors, the efficiency of the pre-heating process could be maximized, and potential issues could be detected and addressed proactively.
Frequently Asked Questions (FAQ)
-
What is the main purpose of a pre-heater?
The main purpose of a pre-heater is to heat raw materials before they enter the main processing unit, such as a kiln or furnace, in order to improve efficiency, reduce energy consumption, and enhance product quality. -
How does a pre-heater improve energy efficiency?
A pre-heater improves energy efficiency by utilizing waste heat from exhaust gases to raise the temperature of incoming raw materials. This reduces the amount of energy required by the main processing unit to bring the materials up to the desired temperature. -
What are the different types of pre-heaters?
The different types of pre-heaters include suspension pre-heaters (used in the cement industry), grate pre-heaters (used in the steel industry), shaft pre-heaters (used in lime production), and flash pre-heaters (used in the chemical industry). -
How do pre-heaters contribute to reducing emissions?
By improving energy efficiency and reducing fuel consumption, pre-heaters help to lower emissions of greenhouse gases and other pollutants associated with industrial processes. -
What are some potential future developments in pre-heater technology?
Potential future developments in pre-heater technology include integration with renewable energy sources, the use of advanced materials and coatings, and the incorporation of smart control systems for real-time optimization of pre-heater performance.
In conclusion, pre-heaters play a crucial role in various industrial processes, offering significant benefits in terms of energy efficiency, production capacity, product quality, and environmental impact. As industries continue to prioritize sustainability and cost-effectiveness, the importance of pre-heater technology is likely to grow, driving further advancements and innovations in this field.
No responses yet