What is Front-End Data Optimization?
Front-end data optimization refers to the process of enhancing and fine-tuning the data used in the initial stages of PCB design and manufacturing. This data includes, but is not limited to:
- Bill of Materials (BOM)
- Gerber files
- Pick and Place files
- Assembly drawings
By optimizing this data, manufacturers can ensure that the PCB Assembly process runs smoothly, minimizing errors, delays, and unnecessary costs.
The Benefits of Front-End Data Optimization
Implementing front-end data optimization offers several key benefits for PCB manufacturers:
-
Improved Accuracy: Optimized data reduces the likelihood of errors during the assembly process, resulting in higher quality PCBs and fewer defects.
-
Increased Efficiency: Streamlined data allows for smoother assembly processes, reducing the time required for setup, production, and quality control.
-
Cost Savings: By minimizing errors and increasing efficiency, front-end data optimization helps manufacturers save on material costs, labor, and rework expenses.
-
Faster Time-to-Market: Optimized data enables quicker assembly and fewer delays, allowing manufacturers to deliver PCBs to their clients more rapidly.
Key Elements of Front-End Data Optimization
To effectively optimize front-end data, PCB manufacturers should focus on several critical elements:
1. Bill of Materials (BOM) Accuracy
The Bill of Materials is a comprehensive list of all components required for a PCB assembly. Ensuring BOM accuracy is crucial for several reasons:
- Accurate component procurement
- Proper component placement during assembly
- Fewer assembly errors and delays
To optimize the BOM, manufacturers should:
- Verify component part numbers and descriptions
- Ensure consistent formatting and structure
- Cross-reference the BOM with design files
BOM Optimization Tip | Benefit |
---|---|
Verify part numbers | Ensures correct component procurement |
Consistent formatting | Improves readability and reduces errors |
Cross-reference design files | Catches discrepancies early in the process |
2. Gerber File Accuracy
Gerber files contain the essential data needed to fabricate PCBs, including copper layers, solder mask, and silkscreen information. Optimizing Gerber files involves:
- Checking for proper layer alignment
- Verifying aperture definitions
- Ensuring correct file formatting
Gerber File Optimization Tip | Benefit |
---|---|
Check layer alignment | Prevents manufacturing errors |
Verify aperture definitions | Ensures correct feature sizes |
Correct file formatting | Smooth data transfer and processing |
3. Pick and Place File Optimization
Pick and Place files provide instructions for automated assembly machines, dictating where each component should be placed on the PCB. Optimizing these files requires:
- Accurate component coordinates
- Correct orientation information
- Proper file formatting
Pick and Place File Optimization Tip | Benefit |
---|---|
Accurate component coordinates | Precise component placement |
Correct orientation information | Prevents component rotation errors |
Proper file formatting | Seamless machine integration |
4. Assembly Drawing Clarity
Assembly drawings provide visual guidance for the PCB assembly process, including component placement, orientation, and special instructions. To optimize assembly drawings, manufacturers should focus on:
- Clear and concise labeling
- Consistent symbology and terminology
- Accurate dimensioning
Assembly Drawing Optimization Tip | Benefit |
---|---|
Clear and concise labeling | Reduces interpretation errors |
Consistent symbology | Improves readability and understanding |
Accurate dimensioning | Ensures proper component placement |
Implementing Front-End Data Optimization
To successfully implement front-end data optimization, PCB manufacturers should follow these steps:
1. Establish Standard Operating Procedures (SOPs)
Develop and document SOPs for each aspect of front-end data optimization, including BOM creation, Gerber File Generation, Pick and Place file preparation, and assembly drawing creation. These SOPs should outline best practices, formatting guidelines, and quality control measures.
2. Invest in Automation Tools
Utilize automation tools to streamline the front-end data optimization process. These tools can help with tasks such as:
- BOM validation and formatting
- Gerber file analysis and verification
- Pick and Place file generation and optimization
- Assembly drawing creation and annotation
Automation Tool | Benefit |
---|---|
BOM validation software | Catches errors and inconsistencies |
Gerber file analysis tools | Identifies potential manufacturing issues |
Pick and Place file optimization software | Improves assembly efficiency |
Assembly drawing automation tools | Ensures consistency and clarity |
3. Foster Collaboration and Communication
Encourage open communication and collaboration between design teams, manufacturing engineers, and quality control personnel. Regular meetings, design reviews, and feedback sessions can help identify areas for improvement and ensure that everyone is working towards the same goal of optimized front-end data.
4. Continuously Monitor and Improve
Regularly assess the effectiveness of your front-end data optimization efforts. Track key performance indicators (KPIs) such as:
- Assembly error rates
- Time-to-market
- Manufacturing costs
Use this data to identify areas for improvement and make necessary adjustments to your SOPs and automation tools.
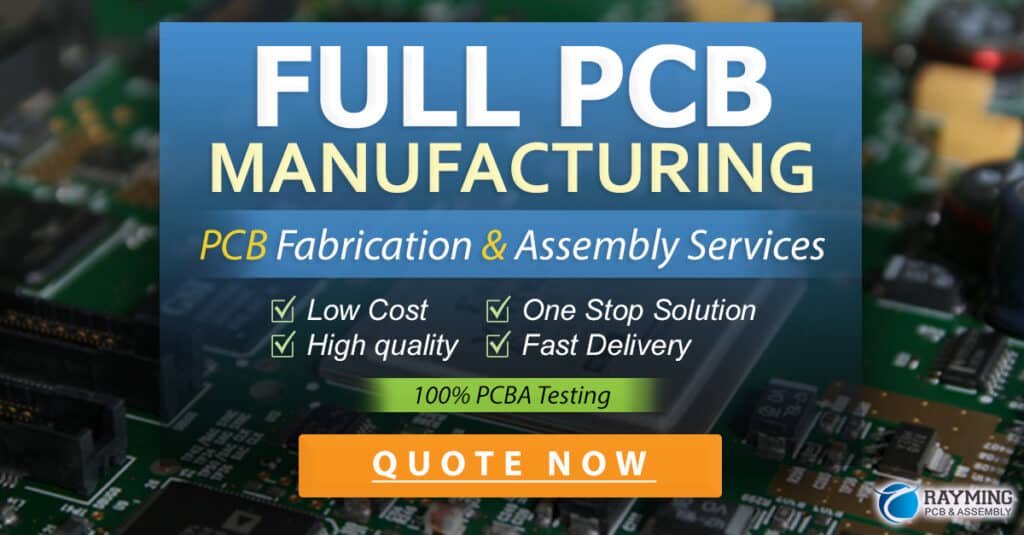
The Future of Front-End Data Optimization
As PCB technology continues to advance, the importance of front-end data optimization will only grow. Emerging trends and technologies that will shape the future of this field include:
1. Artificial Intelligence and Machine Learning
AI and machine learning algorithms can analyze vast amounts of front-end data, identifying patterns and potential issues that human operators might miss. These technologies can help automate and optimize various aspects of the front-end data optimization process, from BOM validation to assembly drawing creation.
2. Cloud-Based Collaboration Platforms
Cloud-based collaboration platforms allow design teams, manufacturers, and clients to share and access front-end data seamlessly. These platforms can help streamline communication, reduce errors, and accelerate the overall PCB assembly process.
3. Digital Twin Technology
Digital twin technology involves creating virtual replicas of physical PCBs, allowing manufacturers to simulate and optimize the assembly process before committing to physical production. This technology can help identify potential issues early in the design phase, reducing the need for costly rework and delays.
Frequently Asked Questions (FAQ)
-
What is the difference between front-end and back-end data optimization?
Front-end data optimization focuses on the data used in the early stages of PCB design and manufacturing, such as BOMs, Gerber files, and assembly drawings. Back-end data optimization deals with data generated during the actual assembly process, such as machine logs and quality control data. -
How often should I review and update my front-end data optimization SOPs?
It is recommended to review and update your front-end data optimization SOPs at least once a year, or whenever significant changes occur in your manufacturing processes or technology. -
Can front-end data optimization be outsourced?
Yes, some PCB manufacturers choose to outsource their front-end data optimization to specialized service providers. However, it is essential to maintain close communication and collaboration with these providers to ensure that the optimized data meets your specific requirements and standards. -
What are some common mistakes in front-end data optimization?
Common mistakes include: - Inconsistent formatting and terminology
- Incomplete or inaccurate BOMs
- Incorrect Gerber file aperture definitions
- Misaligned Pick and Place files
-
Unclear or ambiguous assembly drawings
-
How can I measure the ROI of front-end data optimization efforts?
To measure the ROI of front-end data optimization, track key metrics such as: - Reduction in assembly errors and defects
- Improved time-to-market
- Decreased manufacturing costs
- Increased customer satisfaction
Compare these metrics before and after implementing front-end data optimization to quantify the benefits and justify ongoing investment in this area.
Conclusion
Front-end data optimization is a critical aspect of successful PCB assembly. By focusing on key elements such as BOM accuracy, Gerber file optimization, Pick and Place file refinement, and assembly drawing clarity, manufacturers can improve efficiency, reduce costs, and accelerate time-to-market.
Implementing effective front-end data optimization requires a combination of well-defined SOPs, automation tools, collaboration, and continuous improvement. As PCB technology advances, emerging trends such as AI, cloud-based platforms, and digital twin technology will play an increasingly important role in front-end data optimization.
By embracing these best practices and technologies, PCB manufacturers can stay competitive, deliver high-quality products, and meet the ever-evolving needs of their customers in the dynamic world of electronics manufacturing.
No responses yet