Introduction to PCB Buildup
The buildup of a printed circuit board (PCB) refers to the layering structure and materials used in the fabrication process. The PCB buildup determines key characteristics of the final board, such as its thickness, flexibility, thermal properties, signal integrity, and manufacturability.
Understanding PCB buildup is essential for designers and engineers to create boards that meet their specific requirements while optimizing cost and reliability. This article will delve into the details of PCB buildup, exploring the various types, materials, and design considerations involved.
Types of PCB Buildup
There are several types of PCB buildup, each with its own advantages and applications. The most common types include:
1. Through-Hole Technology (THT)
THT is the traditional PCB buildup method, where components are mounted on one side of the board, and their leads are inserted through drilled holes to the other side, where they are soldered. THT buildup is known for its robustness and reliability, making it suitable for high-power and high-reliability applications.
2. Surface Mount Technology (SMT)
SMT involves mounting components directly onto the surface of the PCB without the need for through-holes. SMT allows for smaller components and higher component density, enabling more compact and lightweight designs. It is the dominant technology in modern electronics manufacturing.
3. Mixed Technology
Mixed technology PCB buildup combines both THT and SMT Components on the same board. This approach leverages the strengths of both technologies, allowing designers to use THT for larger, high-power components and SMT for smaller, more densely packed components.
4. High Density Interconnect (HDI)
HDI PCB buildup involves the use of microvias and fine-pitch traces to achieve higher interconnect density. HDI boards typically have multiple layers and use advanced materials to enable smaller feature sizes and improved signal integrity. This technology is essential for high-speed, high-frequency applications, such as 5G communication and advanced computing.
PCB Buildup Materials
The choice of materials used in PCB buildup significantly impacts the board’s performance, reliability, and cost. The primary materials used in PCB Fabrication include:
1. Substrate
The substrate is the base material that provides mechanical support and electrical insulation for the PCB. The most common substrate materials are:
a. FR-4: A glass-reinforced epoxy laminate, FR-4 is the most widely used substrate material due to its good mechanical and electrical properties, as well as its cost-effectiveness.
b. High-Tg FR-4: A variant of FR-4 with a higher glass transition temperature (Tg), offering better thermal stability and performance in high-temperature applications.
c. Polyimide: A high-performance substrate material with excellent thermal and chemical resistance, suitable for demanding applications such as aerospace and military electronics.
2. Copper
Copper is used to create the conductive traces, pads, and planes on the PCB. The thickness of the copper layer is typically measured in ounces per square foot (oz/ft²), with common thicknesses ranging from 0.5 oz/ft² to 2 oz/ft². Thicker copper layers offer lower resistance and better current-carrying capacity but may increase the board’s cost and weight.
3. Solder Mask
The solder mask is a thin, protective layer applied over the copper traces to prevent accidental short circuits and improve the board’s aesthetic appearance. Solder masks are typically made of polymer materials and are available in various colors, with green being the most common.
4. Silkscreen
Silkscreen is a layer of text and symbols printed on the PCB surface to provide information such as component designators, logos, and assembly instructions. The silkscreen is typically white but can be any color that contrasts well with the solder mask.
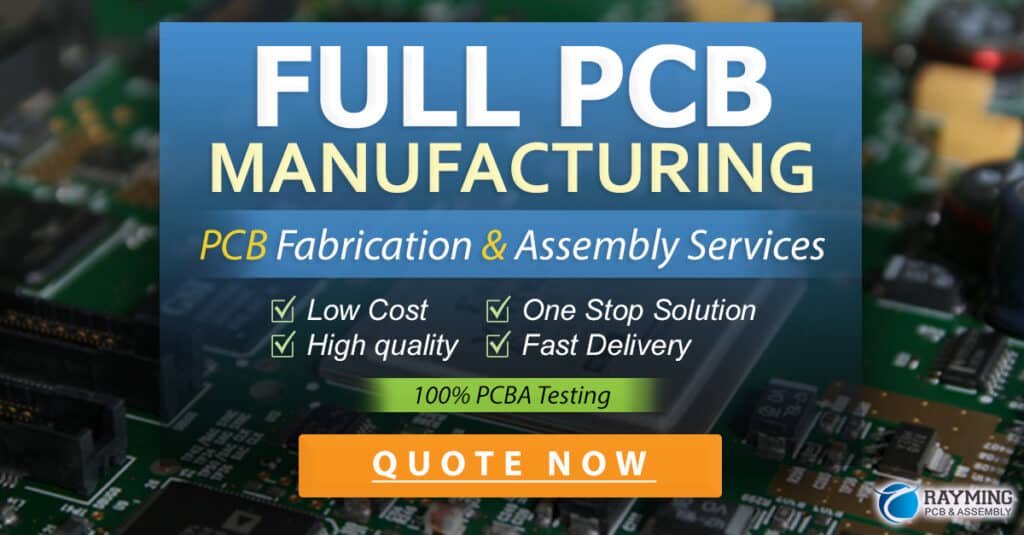
PCB Buildup Design Considerations
When designing a PCB, several factors related to the buildup must be considered to ensure optimal performance, reliability, and manufacturability. These include:
1. Layer Stack-up
The layer stack-up refers to the arrangement of conductive and insulating layers in the PCB. A well-designed stack-up ensures proper signal integrity, power distribution, and EMI/EMC performance. Factors to consider include the number of layers, layer sequence, dielectric thickness, and impedance control.
2. Via Technology
Vias are conductive pathways that connect different layers of the PCB. The choice of via technology depends on the board’s design requirements and manufacturing constraints. Common via types include:
a. Through-hole vias: Drilled holes that span the entire thickness of the board.
b. Blind vias: Vias that start from an outer layer and terminate at an inner layer.
c. Buried vias: Vias that connect inner layers without reaching the outer layers.
d. Microvias: Small-diameter vias (typically less than 150 µm) used in HDI designs.
3. Trace Width and Spacing
The width and spacing of copper traces on the PCB directly impact signal integrity, crosstalk, and EMI. Designers must carefully select trace geometries based on the signal speed, current requirements, and available board space. High-speed designs may require impedance-controlled traces and advanced layout techniques to maintain signal integrity.
4. Thermal Management
PCB buildup plays a crucial role in the thermal management of the board. Factors such as the substrate material, copper thickness, and the presence of thermal vias can affect the board’s ability to dissipate heat. Proper thermal management is essential to ensure the long-term reliability of the components and prevent premature failure due to overheating.
PCB Buildup Manufacturing Process
The manufacturing process for PCB buildup involves several steps, each contributing to the final quality and reliability of the board. The main steps include:
1. Lamination
The substrate material is laminated with copper foil using heat and pressure. The copper foil is bonded to the substrate, creating a solid foundation for the subsequent processing steps.
2. Drilling
Holes are drilled through the laminated board to accommodate through-hole components and vias. The drilling process can be done mechanically or using lasers, depending on the required hole size and accuracy.
3. Plating
The drilled holes are plated with copper to create conductive pathways between layers. This process involves electroless copper deposition followed by electrolytic copper plating to achieve the desired thickness.
4. Patterning
The copper layers are patterned to create the desired circuit layout. This is typically done using photolithography, where a photoresist is applied, exposed, and developed to create a mask. The exposed copper is then etched away, leaving only the desired traces and pads.
5. Solder Mask Application
The solder mask is applied to the board, covering the copper traces while leaving the pads exposed. The solder mask is typically applied using screen printing or photoimaging techniques.
6. Surface Finish
A surface finish is applied to the exposed copper pads to protect them from oxidation and enhance solderability. Common surface finishes include:
a. Hot Air Solder Leveling (HASL): A tin-lead alloy is applied to the pads and leveled using hot air.
b. Electroless Nickel Immersion Gold (ENIG): A layer of nickel is deposited on the pads, followed by a thin layer of gold.
c. Immersion Silver: A thin layer of silver is deposited on the pads.
d. Immersion Tin: A thin layer of tin is deposited on the pads.
7. Silkscreen Printing
The silkscreen is printed on the PCB surface using a screen printing process. The silkscreen ink is typically a durable, epoxy-based material that adheres well to the solder mask.
8. Electrical Testing
The manufactured PCB undergoes electrical testing to ensure that all connections are correct and there are no short circuits or open connections. This is typically done using automated test equipment (ATE) that probes the board and verifies its functionality.
FAQ
1. What is the difference between THT and SMT PCB buildup?
THT (Through-Hole Technology) involves mounting components with leads that are inserted through drilled holes in the PCB and soldered on the opposite side. SMT (Surface Mount Technology) involves mounting components directly onto the surface of the PCB without the need for through-holes. SMT allows for smaller components and higher component density, while THT is known for its robustness and reliability.
2. What is the purpose of the solder mask in PCB buildup?
The solder mask is a thin, protective layer applied over the copper traces on a PCB. Its primary purposes are to prevent accidental short circuits between adjacent traces, protect the copper from oxidation, and improve the board’s aesthetic appearance. The solder mask also provides a surface for the silkscreen to be printed on.
3. How does the choice of substrate material affect PCB performance?
The substrate material used in PCB buildup significantly impacts the board’s performance, particularly in terms of its thermal, mechanical, and electrical properties. For example, FR-4 is a commonly used substrate material that offers good all-round performance and cost-effectiveness. However, for high-temperature or high-reliability applications, materials like High-Tg FR-4 or polyimide may be preferred due to their superior thermal stability and mechanical strength.
4. What are microvias, and when are they used in PCB buildup?
Microvias are small-diameter vias (typically less than 150 µm) used in High Density Interconnect (HDI) PCB designs. They enable higher interconnect density by allowing more connections to be made in a smaller area. Microvias are typically used to connect the outer layers of the PCB to the inner layers, facilitating the routing of high-speed signals and reducing signal path length.
5. What is the role of copper thickness in PCB buildup?
The thickness of the copper layers in a PCB, typically measured in ounces per square foot (oz/ft²), plays a crucial role in the board’s electrical and thermal performance. Thicker copper layers offer lower resistance and better current-carrying capacity, which is important for power distribution and high-current applications. However, thicker copper also increases the board’s weight and cost. The choice of copper thickness must balance the electrical and thermal requirements with the design constraints and budget.
Conclusion
PCB buildup is a critical aspect of printed circuit board design and manufacturing, encompassing the layering structure, materials, and processes used to create the final board. Understanding the types of PCB buildup, the materials involved, and the design considerations is essential for creating boards that meet specific performance, reliability, and cost requirements.
From the traditional through-hole technology to the advanced high-density interconnect designs, PCB buildup continues to evolve to keep pace with the ever-increasing demands of modern electronics. By carefully selecting the appropriate buildup type, materials, and design parameters, engineers and manufacturers can create PCBs that push the boundaries of performance and functionality while ensuring long-term reliability and cost-effectiveness.
As the electronics industry advances, innovations in PCB buildup technologies, materials, and processes will play a crucial role in enabling the next generation of devices and systems. From 5G communications to artificial intelligence and the Internet of Things, the success of these technologies will rely heavily on the ability to design and manufacture high-quality, high-performance PCBs with optimized buildup structures.
In conclusion, a thorough understanding of PCB buildup is a fundamental skill for anyone involved in electronics design and manufacturing. By mastering the principles and best practices of PCB buildup, designers and engineers can create boards that not only meet the demands of today’s applications but also lay the foundation for the innovations of tomorrow.
No responses yet