What is Allocation slowdown?
Allocation slowdown refers to the reduced availability of essential components and materials required for electronics manufacturing. When suppliers cannot meet the demand for these components, manufacturers face delays in receiving the necessary parts, which slows down their production processes.
Causes of Allocation Slowdown
Several factors contribute to the allocation slowdown in the electronics industry:
-
Global Chip Shortage: The worldwide shortage of semiconductor chips has been a major contributor to the allocation slowdown. The COVID-19 pandemic disrupted supply chains and increased demand for electronic devices, leading to a scarcity of chips.
-
Increased Demand: The surge in demand for electronic devices, particularly during the pandemic, has put pressure on suppliers to meet the growing needs of manufacturers.
-
Supply Chain Disruptions: Disruptions in the global supply chain, such as transportation delays, port congestion, and raw material shortages, have further exacerbated the allocation slowdown.
-
Geopolitical Factors: Trade tensions and geopolitical issues can also impact the availability of components and materials, as countries may impose restrictions or tariffs on certain products.
Impact of Allocation Slowdown on Electronics Manufacturers
The allocation slowdown has far-reaching consequences for electronics manufacturers:
Production Delays
With limited access to essential components, manufacturers face production delays. They may have to halt or slow down their assembly lines until the required parts become available, leading to reduced output and missed deadlines.
Increased Costs
The scarcity of components often leads to price increases, as suppliers prioritize customers willing to pay a premium. Manufacturers may have to absorb these higher costs or pass them on to consumers, affecting their profitability and competitiveness.
Customer Dissatisfaction
Delayed product deliveries can result in customer dissatisfaction and loss of business. Customers may turn to competitors who can deliver products more quickly, damaging the manufacturer’s reputation and long-term relationships.
Inventory Management Challenges
The unpredictable nature of the allocation slowdown makes inventory management more challenging. Manufacturers may struggle to maintain optimal inventory levels, risking stockouts or overstocking, which can tie up capital and increase storage costs.
Strategies to Mitigate the Impact of Allocation Slowdown
Electronics manufacturers can employ several strategies to minimize the impact of the allocation slowdown:
Diversifying Supplier Base
By diversifying their supplier base, manufacturers can reduce their reliance on a single source and minimize the risk of supply disruptions. Establishing relationships with multiple suppliers across different regions can provide alternatives when one supplier faces allocation issues.
Long-term Contracts and Partnerships
Entering into long-term contracts and strategic partnerships with suppliers can help secure a steady supply of components. By committing to larger volumes and longer-term agreements, manufacturers can incentivize suppliers to prioritize their orders and allocate resources accordingly.
Designing for Flexibility
Designing products with flexibility in mind can help manufacturers adapt to Component Shortages. By using interchangeable or alternative components, manufacturers can modify their designs to work with available parts, reducing the impact of allocation slowdowns.
Improving Demand Forecasting
Accurate demand forecasting is crucial for effective inventory management and production planning. By leveraging data analytics and collaborating closely with customers, manufacturers can better predict demand and adjust their production schedules accordingly.
Investing in Automation and Technology
Investing in automation and advanced manufacturing technologies can help manufacturers optimize their production processes and improve efficiency. Automated systems can help streamline operations, reduce waste, and minimize the impact of Component Shortages.
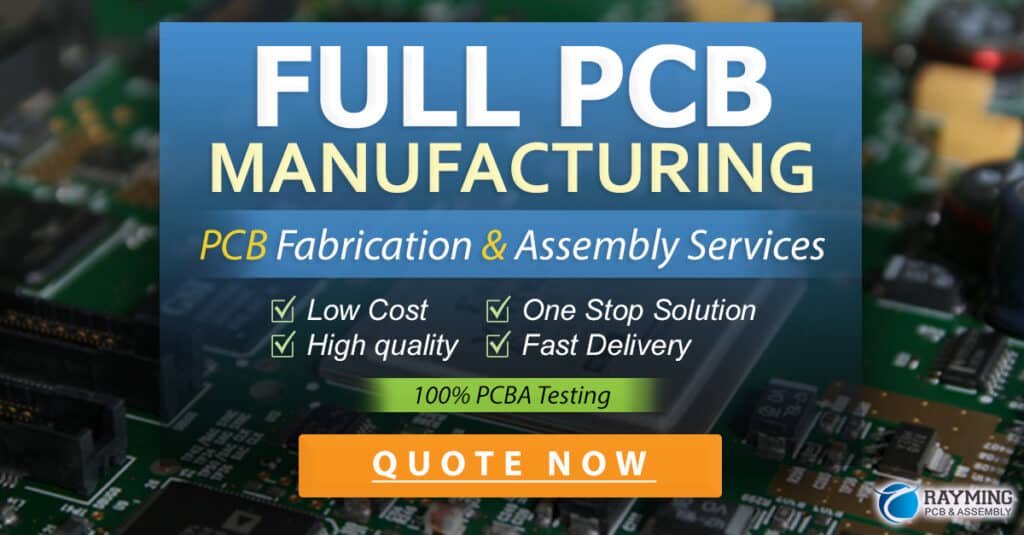
Case Studies
To illustrate the impact of the allocation slowdown and the strategies employed by electronics manufacturers, let’s look at two case studies:
Case Study 1: Smartphone Manufacturer
A leading smartphone manufacturer faced significant production delays due to the global chip shortage. With limited access to essential components, the company struggled to meet its production targets and delivery deadlines.
To mitigate the impact, the manufacturer took the following steps:
– Diversified its supplier base by partnering with multiple chip manufacturers across different regions.
– Entered into long-term contracts with key suppliers to secure a steady supply of components.
– Redesigned certain models to use alternative or more readily available components.
– Invested in advanced demand forecasting tools to better predict customer demand and optimize inventory levels.
As a result of these strategies, the smartphone manufacturer was able to minimize production delays, maintain customer satisfaction, and remain competitive in the market.
Case Study 2: Automotive Electronics Supplier
An automotive electronics supplier experienced allocation slowdowns for various components, including sensors, microcontrollers, and displays. The company’s production lines were affected, leading to delayed deliveries to its automotive customers.
To address the issue, the supplier implemented the following measures:
– Collaborated closely with its automotive customers to understand their demand forecasts and production schedules.
– Established strategic partnerships with key suppliers to secure long-term supply agreements and priority allocation.
– Invested in automation and lean manufacturing practices to optimize production processes and reduce waste.
– Explored alternative sourcing options, including local suppliers and second-tier manufacturers.
Through these efforts, the automotive electronics supplier was able to improve its resilience to allocation slowdowns, meet customer demands more effectively, and strengthen its position in the market.
Frequently Asked Questions (FAQ)
-
Q: How long is the allocation slowdown expected to last in the electronics industry?
A: The duration of the allocation slowdown depends on various factors, such as the resolution of the global chip shortage, supply chain disruptions, and geopolitical tensions. Experts predict that the situation may improve gradually over the next few years as suppliers ramp up production and new manufacturing facilities come online. -
Q: Can electronics manufacturers completely avoid the impact of allocation slowdowns?
A: While it may not be possible to completely avoid the impact of allocation slowdowns, manufacturers can take proactive measures to minimize their exposure. Diversifying supplier bases, establishing long-term partnerships, designing for flexibility, and improving demand forecasting can help manufacturers navigate these challenges more effectively. -
Q: How can electronics manufacturers ensure the quality of components sourced from alternative suppliers?
A: When sourcing components from alternative suppliers, manufacturers should conduct thorough due diligence to ensure the quality and reliability of the parts. This may involve supplier audits, quality inspections, and testing procedures. Establishing clear quality standards and communication channels with suppliers can help maintain product quality. -
Q: What role can government policies play in addressing the allocation slowdown?
A: Governments can play a crucial role in mitigating the impact of allocation slowdowns by implementing supportive policies and initiatives. This may include incentivizing local production of essential components, providing financial support for research and development, and fostering international cooperation to address supply chain challenges. -
Q: How can electronics manufacturers communicate effectively with customers about allocation slowdowns and production delays?
A: Transparent and proactive communication is key when dealing with allocation slowdowns and production delays. Manufacturers should keep customers informed about the status of their orders, provide realistic timelines, and offer regular updates. Collaborating closely with customers to understand their priorities and exploring alternative solutions can help maintain trust and long-term relationships.
Conclusion
The allocation slowdown poses significant challenges for electronics manufacturers, impacting production, costs, and customer satisfaction. However, by adopting proactive strategies such as diversifying supplier bases, establishing long-term partnerships, designing for flexibility, and improving demand forecasting, manufacturers can mitigate the impact of these slowdowns.
As the electronics industry navigates this challenging landscape, collaboration, innovation, and resilience will be key to overcoming the allocation slowdown and ensuring the continued growth and success of the sector.
No responses yet