Understanding Reflow Oven Types and Configurations
Before diving into PCB Placement strategies, it is essential to understand the different types of reflow ovens available and their configurations. The two primary categories of reflow ovens are convection ovens and infrared (IR) ovens.
Convection Reflow Ovens
Convection reflow ovens utilize forced air circulation to evenly distribute heat throughout the oven chamber. They typically feature multiple heating zones, each with its own temperature control, allowing for precise temperature profiles tailored to specific solder paste and PCB requirements. Convection ovens are known for their excellent temperature uniformity and are widely used in high-volume production environments.
Infrared (IR) Reflow Ovens
Infrared reflow ovens employ infrared emitters to directly heat the PCB and components. They offer rapid heating and cooling rates, making them suitable for quick-turn prototyping and low-volume production. IR ovens can be further classified into near-infrared (NIR) and far-infrared (FIR) ovens based on the wavelength of the emitted radiation.
Oven Type | Heating Method | Temperature Uniformity | Typical Application |
---|---|---|---|
Convection | Forced air circulation | Excellent | High-volume production |
Infrared (IR) | Infrared emitters | Good | Quick-turn prototyping, low-volume production |
Factors Influencing PCB Placement
Several factors must be considered when determining the optimal placement of a PCB in the reflow oven. These factors include:
- Oven temperature profile
- PCB size and shape
- Component density and distribution
- Solder paste characteristics
- Conveyor system and speed
Let’s examine each of these factors in more detail.
Oven Temperature Profile
The temperature profile of the reflow oven plays a critical role in the success of the soldering process. It defines the time-temperature relationship that the PCB and components will experience during the reflow cycle. The temperature profile typically consists of four main stages: preheat, soak, reflow, and cooling.
When placing the PCB in the oven, it is essential to ensure that the board is exposed to the appropriate temperature profile for the specific solder paste and components used. This may require adjusting the conveyor speed or modifying the temperature settings of the oven zones.
PCB Size and Shape
The size and shape of the PCB can influence its placement in the reflow oven. Larger PCBs may require more careful positioning to ensure even heat distribution across the entire board. Irregularly shaped PCBs, such as those with cut-outs or complex geometries, may also demand special consideration to prevent hot spots or cold spots during the reflow process.
In general, it is recommended to place the PCB in the center of the oven conveyor to minimize the impact of any temperature variations along the edges of the oven chamber.
Component Density and Distribution
The density and distribution of components on the PCB can also affect its placement in the reflow oven. Boards with a high component density or uneven distribution may be more susceptible to thermal shadowing, where taller components block the heat flow to smaller components nearby.
To mitigate this issue, it may be necessary to position the PCB in a way that promotes uniform heat exposure to all components. This can be achieved by orienting the board so that taller components are not blocking the airflow to smaller components, or by using specialized fixtures to maintain proper board alignment.
Solder Paste Characteristics
The type and characteristics of the solder paste used on the PCB can also influence its placement in the reflow oven. Different solder pastes have varying melting temperatures, viscosities, and flux activation requirements, which can impact the optimal temperature profile and conveyor speed.
When placing the PCB in the oven, it is crucial to consider the specific requirements of the solder paste and adjust the oven settings accordingly. This may involve consulting the solder paste manufacturer’s recommendations or conducting trial runs to determine the best placement and settings for a given solder paste.
Conveyor System and Speed
The conveyor system and speed of the reflow oven can also affect PCB placement decisions. The conveyor system determines how the PCB moves through the oven and can impact the exposure time to each temperature zone.
In some cases, it may be necessary to adjust the conveyor speed to accommodate larger or more complex PCBs, ensuring that they receive adequate exposure to each stage of the temperature profile. Additionally, the type of conveyor system (e.g., belt, chain, or mesh) can influence the placement of the PCB, as different systems may have varying levels of support and stability.
Best Practices for PCB Placement
Based on the factors discussed above, here are some best practices to follow when placing your PCB in the reflow oven:
-
Center the PCB on the conveyor: Place the PCB in the center of the conveyor to ensure even heat distribution and minimize the impact of temperature variations along the edges of the oven chamber.
-
Orient the PCB for optimal airflow: Position the PCB so that taller components do not block the airflow to smaller components. This promotes uniform heat exposure and helps prevent thermal shadowing.
-
Use specialized fixtures when necessary: For irregularly shaped or large PCBs, consider using specialized fixtures to maintain proper board alignment and support throughout the reflow process.
-
Adjust oven settings based on solder paste requirements: Consult the solder paste manufacturer’s recommendations and adjust the oven temperature profile and conveyor speed accordingly to ensure optimal reflow results.
-
Conduct trial runs: Before committing to a specific PCB placement strategy, conduct trial runs with sample boards to validate the effectiveness of the chosen approach and make any necessary adjustments.
By following these best practices and considering the various factors that influence PCB placement, you can optimize your reflow soldering process and achieve high-quality, reliable results.
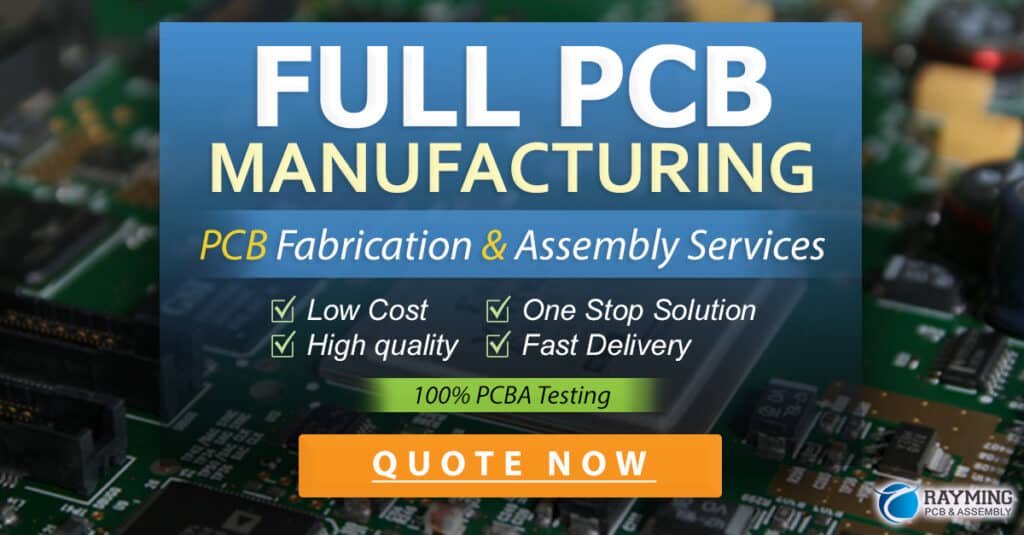
Frequently Asked Questions (FAQ)
-
Q: Can I place multiple PCBs side by side in the reflow oven?
A: Yes, you can place multiple PCBs side by side in the reflow oven, as long as there is sufficient space between the boards to allow for proper heat circulation. Ensure that the PCBs do not touch each other or the oven walls to prevent any heat-related issues. -
Q: How do I determine the optimal conveyor speed for my PCB?
A: The optimal conveyor speed depends on factors such as the PCB size, component density, and solder paste characteristics. Consult the solder paste manufacturer’s recommendations and conduct trial runs with sample boards to determine the best conveyor speed for your specific PCB. -
Q: Can I use the same PCB placement strategy for both convection and IR reflow ovens?
A: While the general principles of PCB placement apply to both convection and IR reflow ovens, there may be some differences in the specific strategies employed. IR ovens, for example, may require more careful consideration of component shadowing due to the direct heating nature of the infrared emitters. -
Q: What should I do if my PCB has components on both sides?
A: For double-sided PCBs, it is generally recommended to place the side with the most components or the side with the taller components facing up in the reflow oven. This allows for better heat exposure and helps prevent component shadowing on the bottom side of the board. -
Q: How can I prevent my PCBs from warping during the reflow process?
A: To minimize the risk of PCB warping, ensure that the board is properly supported in the oven and that the temperature profile is optimized for the specific PCB Thickness and material. Using specialized fixtures or carriers can also help maintain the flatness of the board throughout the reflow process.
Conclusion
Proper placement of PCBs in the reflow oven is essential for achieving optimal soldering results and ensuring the reliability of the finished product. By understanding the factors that influence PCB placement, such as oven temperature profile, PCB size and shape, component density and distribution, solder paste characteristics, and conveyor system and speed, you can make informed decisions and implement best practices for your specific PCB Assembly process.
Remember to center the PCB on the conveyor, orient it for optimal airflow, use specialized fixtures when necessary, adjust oven settings based on solder paste requirements, and conduct trial runs to validate your chosen placement strategy. By following these guidelines, you can optimize your reflow soldering process and produce high-quality PCBs with consistent and reliable performance.
No responses yet