What Are Build-ups in Construction?
Build-ups, in the context of construction, refer to the process of assembling various components and materials to create a complete structure or building element. These build-ups can be either standard or predefined, depending on the specific project requirements and the construction methods employed.
Standard Build-ups
Standard build-ups are the most common type of build-up in construction projects. They involve the use of conventional materials and techniques to create the desired structure or building element. Standard build-ups typically follow established industry practices and building codes, ensuring that the final product meets the necessary safety and performance standards.
Some examples of standard build-ups include:
Build-up Type | Description |
---|---|
Concrete Slab | A horizontal concrete surface, often used for floors or foundations |
Brick Wall | A vertical structure made of bricks and mortar, used for interior or exterior walls |
Timber Framing | A framework of wooden beams and posts, used to support the structure of a building |
Advantages of Standard Build-ups
- Familiarity: Contractors and construction workers are usually well-versed in standard build-up methods, which can lead to faster and more efficient project completion.
- Availability of materials: Standard build-ups often use readily available materials, making it easier to source the necessary components for the project.
- Cost-effectiveness: Due to their widespread use and the availability of materials, standard build-ups can be more cost-effective compared to custom or specialized build-ups.
Predefined Build-ups
Predefined build-ups are construction assemblies that have been designed and specified in advance, often by the architect or engineer. These build-ups are tailored to meet the specific requirements of a project, such as enhanced energy efficiency, improved acoustic performance, or unique aesthetic qualities.
Some examples of predefined build-ups include:
Build-up Type | Description |
---|---|
Green Roof | A roof covered with vegetation, designed to improve insulation and stormwater management |
Curtain Wall | A non-structural exterior wall, often made of glass and metal, used for improved daylighting and aesthetic appeal |
Acoustic Floor | A specialized floor assembly designed to reduce sound transmission between levels of a building |
Advantages of Predefined Build-ups
- Customization: Predefined build-ups allow for greater customization to meet the specific needs and requirements of a project.
- Enhanced performance: By designing build-ups with specific performance goals in mind, such as energy efficiency or acoustic control, predefined build-ups can offer superior performance compared to standard assemblies.
- Consistency: Predefined build-ups ensure that the specified materials and techniques are used consistently throughout the project, leading to a more uniform and cohesive final product.
Factors to Consider When Choosing Build-ups
When selecting between standard and predefined build-ups for a construction project, several factors should be considered:
-
Project requirements: The specific needs and goals of the project should be the primary driver in choosing the appropriate build-up type. Factors such as energy efficiency, acoustic performance, and aesthetic preferences should be taken into account.
-
Budget: The cost of materials and labor can vary significantly between standard and predefined build-ups. It is essential to consider the project budget when making a decision, as predefined build-ups may have higher upfront costs but could offer long-term savings through improved performance.
-
Timeline: The availability of materials and the familiarity of the construction team with the chosen build-up method can impact the project timeline. Standard build-ups may allow for faster completion, while predefined build-ups might require more time for sourcing materials and ensuring proper installation.
-
Building codes and regulations: All build-ups must comply with local building codes and regulations. It is crucial to ensure that the chosen build-up meets these requirements to avoid potential legal issues or project delays.
Implementing Build-ups in Construction Projects
Once the appropriate build-up type has been selected, the next step is to ensure its proper implementation within the construction project. This process involves several key aspects:
-
Detailed documentation: Comprehensive plans, specifications, and drawings should be prepared to clearly communicate the build-up requirements to the construction team. This documentation should include material lists, installation instructions, and any necessary performance criteria.
-
Coordination among stakeholders: Effective communication and coordination among the various project stakeholders, including the architect, engineer, contractor, and subcontractors, is essential for the successful implementation of build-ups. Regular meetings and updates can help ensure that everyone is working towards the same goals and adhering to the specified build-up methods.
-
Quality control: Strict quality control measures should be in place to verify that the build-ups are being constructed according to the plans and specifications. This may involve regular inspections, testing, and documentation to ensure compliance and catch any potential issues early in the process.
-
Proper installation techniques: The construction team must be well-versed in the proper installation techniques for the chosen build-up method. This may require specialized training or the involvement of experienced professionals to guarantee the build-ups are constructed correctly and perform as intended.
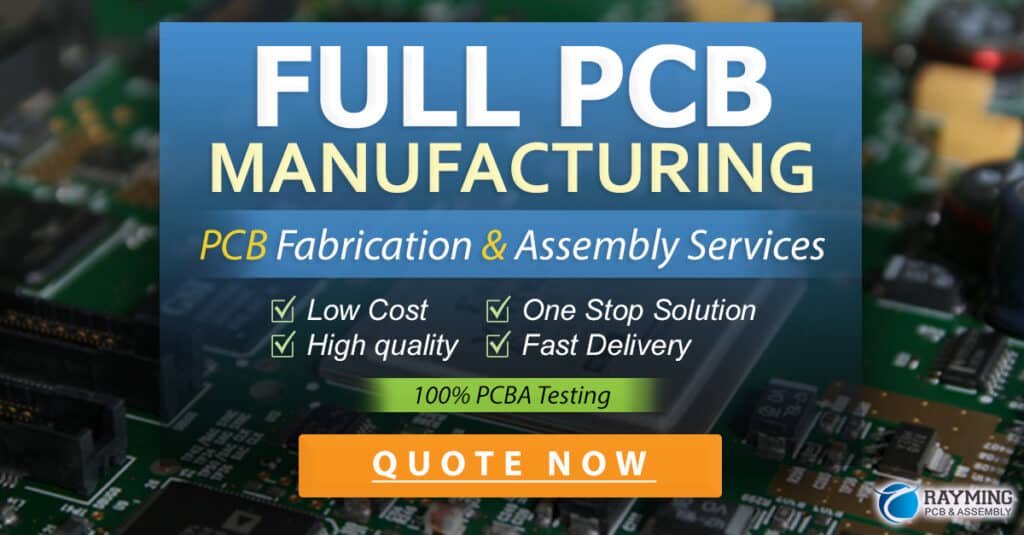
Maintenance and Longevity of Build-ups
Once the construction project is complete, the focus shifts to maintaining the build-ups to ensure their long-term performance and durability. Regular maintenance is essential for both standard and predefined build-ups, as it helps to identify and address any potential issues before they become significant problems.
Some key maintenance considerations include:
-
Regular inspections: Scheduled inspections should be conducted to assess the condition of the build-ups and identify any signs of wear, damage, or deterioration. These inspections can help catch issues early, allowing for prompt repairs and preventing more extensive damage.
-
Cleaning and upkeep: Depending on the type of build-up, regular cleaning and upkeep may be necessary to maintain its appearance and performance. For example, green roofs may require periodic weeding and irrigation, while curtain walls may need regular cleaning to maintain their transparency and aesthetic appeal.
-
Timely repairs: When issues are identified during inspections or through other means, it is crucial to address them promptly. Delaying repairs can lead to more extensive damage and higher costs in the long run. Working with qualified professionals to perform necessary repairs can help ensure the longevity and performance of the build-ups.
Frequently Asked Questions (FAQ)
-
What is the difference between standard and predefined build-ups?
Standard build-ups use conventional materials and techniques and follow established industry practices, while predefined build-ups are designed and specified in advance to meet specific project requirements, such as enhanced energy efficiency or unique aesthetic qualities. -
How do I choose between standard and predefined build-ups for my project?
Consider factors such as project requirements, budget, timeline, and building codes when choosing between standard and predefined build-ups. Evaluate the specific needs and goals of your project and consult with professionals to determine the most appropriate option. -
What are some examples of predefined build-ups?
Examples of predefined build-ups include green roofs, curtain walls, and acoustic floors. These build-ups are designed to offer specific performance benefits or aesthetic qualities tailored to the project’s needs. -
How can I ensure the proper implementation of build-ups in my construction project?
Ensure proper implementation by preparing detailed documentation, fostering coordination among stakeholders, implementing quality control measures, and ensuring the construction team is well-versed in the proper installation techniques for the chosen build-up method. -
What maintenance is required for build-ups?
Regular maintenance for build-ups includes scheduled inspections to identify potential issues, cleaning and upkeep to maintain appearance and performance, and timely repairs to address any identified problems. The specific maintenance requirements will depend on the type of build-up and its intended function.
Conclusion
Understanding the differences between standard and predefined build-ups is essential for successful construction projects. By carefully considering the project requirements, budget, timeline, and building codes, stakeholders can select the most appropriate build-up method to meet their needs. Proper implementation and maintenance of build-ups are crucial for ensuring long-term performance and durability.
As the construction industry continues to evolve, it is likely that new build-up methods and materials will emerge, offering even greater opportunities for customization and performance. By staying informed about these developments and working closely with experienced professionals, construction teams can ensure that their projects benefit from the most suitable and effective build-up solutions available.
No responses yet