In today’s fast-paced world, businesses and individuals alike are constantly seeking ways to streamline their operations and maximize efficiency. One area that has gained significant attention is the realm of box build assembly services. Whether you’re a manufacturer, retailer, or an entrepreneur, outsourcing your box assembly needs can provide numerous benefits, including cost savings, increased productivity, and access to specialized expertise.
What are Box Build Assembly Services?
Box build assembly services encompass a wide range of processes involved in the assembly and packaging of products. These services are typically offered by third-party companies that specialize in the efficient and accurate assembly of various components into a finished product, which is then packaged and prepared for distribution.
The box build assembly process typically involves the following steps:
- Component Sourcing: The assembly service provider procures the necessary components, materials, and packaging supplies required for the assembly process.
- Assembly: Skilled technicians follow detailed instructions and schematics to assemble the components into the desired product configuration.
- Quality Control: Stringent quality control measures are implemented to ensure that the assembled products meet the required specifications and standards.
- Packaging: The assembled products are carefully packaged, often using custom-designed packaging materials, to protect them during transit and storage.
- Labeling and Documentation: Appropriate labeling and documentation are applied to the packaged products, including barcodes, serial numbers, and any necessary regulatory or compliance information.
- Shipping and Distribution: The final step involves the coordination of shipping and distribution logistics, ensuring that the packaged products reach their intended destinations in a timely and efficient manner.
Benefits of Outsourcing Box Build Assembly Services
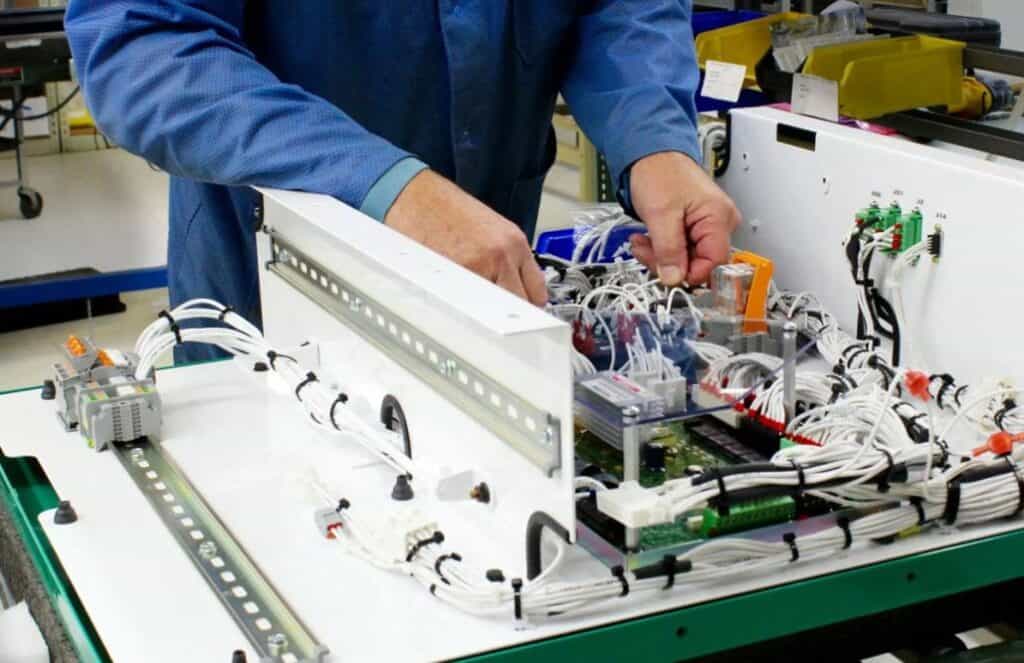
Outsourcing box build assembly services can offer numerous advantages to businesses of all sizes, including:
1. Cost Savings
By outsourcing the assembly process, businesses can significantly reduce overhead costs associated with maintaining an in-house assembly operation. These costs include:
- Labor expenses (salaries, benefits, and training)
- Equipment and facility maintenance
- Inventory management and storage
Outsourcing these tasks to a dedicated assembly service provider can result in substantial cost savings, allowing businesses to redirect their resources towards core activities and growth initiatives.
2. Access to Specialized Expertise
Box build assembly services providers employ teams of skilled technicians and engineers who possess extensive experience and expertise in assembly processes. These professionals stay up-to-date with the latest techniques, tools, and best practices, ensuring that the assembly is performed with precision and efficiency.
By leveraging this specialized expertise, businesses can ensure that their products are assembled correctly and consistently, minimizing the risk of defects or quality issues.
3. Scalability and Flexibility
Outsourcing box build assembly services allows businesses to easily scale their operations up or down based on demand fluctuations. Instead of maintaining a fixed in-house assembly capacity, which can be costly during periods of low demand, businesses can rely on the flexible resources of an assembly service provider.
This scalability enables businesses to respond quickly to market changes, seasonal variations, or unexpected spikes in demand, ensuring that they can meet customer expectations without compromising efficiency or quality.
4. Focus on Core Competencies
By outsourcing the assembly process, businesses can redirect their focus and resources towards their core competencies, such as product design, marketing, and sales. This strategic shift allows companies to concentrate on their strengths, fostering innovation and enhancing their competitive advantage in their respective markets.
5. Reduced Lead Times
Box build assembly services providers often have streamlined processes and established supply chains, enabling them to efficiently manage inventory levels and assembly workflows. This can result in reduced lead times, ensuring that products are assembled and delivered to customers more quickly, enhancing customer satisfaction and reducing the risk of stockouts or backorders.
Types of Box Build Assembly Services
Box build assembly services can be tailored to meet the specific needs of different industries and product types. Some common types of box build assembly services include:
1. Electronics Assembly
This service involves the assembly of various electronic components, such as printed circuit boards (PCBs), cables, connectors, and enclosures. Electronic assembly services are commonly utilized in industries like consumer electronics, telecommunications, and industrial automation.
2. Medical Device Assembly
Medical device assembly requires strict adherence to regulatory guidelines and quality standards. Assembly service providers specializing in this area have expertise in handling sensitive components, maintaining sterile environments, and ensuring compliance with applicable regulations.
3. Automotive Assembly
The automotive industry relies heavily on box build assembly services for the production of various automotive components and sub-assemblies. These services encompass the assembly of electrical systems, mechanical parts, and interior components.
4. Aerospace Assembly
Aerospace assembly services cater to the stringent requirements of the aviation and aerospace industries. These services involve the assembly of complex components and sub-assemblies, often requiring specialized tools, techniques, and certifications.
5. Industrial Equipment Assembly
Box build assembly services are also utilized in the assembly of industrial equipment, machinery, and tools. These services encompass the assembly of components such as motors, pumps, valves, and control systems.
Choosing the Right Box Build Assembly Service Provider
When selecting a box build assembly service provider, it is crucial to consider several factors to ensure a successful partnership and high-quality outcomes. Here are some key considerations:
1. Experience and Expertise
Evaluate the service provider’s experience and expertise in your specific industry or product type. Look for providers that have a proven track record of delivering high-quality assembly services and have the necessary certifications or accreditations required in your industry.
2. Quality Control and Compliance
Assess the provider’s quality control processes and their ability to adhere to industry-specific regulations and standards. Inquire about their quality assurance procedures, documentation practices, and compliance with relevant certifications, such as ISO 9001 or industry-specific regulations.
3. Scalability and Flexibility
Consider the provider’s capacity to handle fluctuations in demand and their ability to scale operations up or down as needed. Evaluate their resource availability, production capabilities, and responsiveness to changing requirements.
4. Supply Chain Management
Investigate the provider’s supply chain management capabilities, including their ability to source components, manage inventory levels, and ensure timely delivery of assembled products. Efficient supply chain management can significantly impact lead times and overall project timelines.
5. Communication and Collaboration
Effective communication and collaboration between the service provider and your team are essential for successful box build assembly projects. Assess the provider’s communication channels, project management tools, and their willingness to work closely with your team throughout the assembly process.
6. Pricing and Cost Structure
While cost should not be the sole determining factor, it is important to evaluate the provider’s pricing structure and overall cost competitiveness. Consider factors such as labor rates, material costs, and any additional fees or charges that may be incurred during the assembly process.
7. Customer Service and Support
Evaluate the level of customer service and support offered by the service provider. Look for providers that offer responsive communication, proactive issue resolution, and dedicated account management to ensure a seamless and collaborative partnership.
By carefully evaluating these factors, businesses can increase their chances of finding a reliable and capable box build assembly service provider that aligns with their specific requirements and goals.
Case Studies: Successful Box Build Assembly Partnerships
To illustrate the benefits and successful implementation of box build assembly services, let’s explore a few case studies:
Case Study 1: Electronics Manufacturer
A leading electronics manufacturer was facing challenges in keeping up with the increasing demand for their popular home entertainment systems. Their in-house assembly operations were struggling to meet production targets, leading to delays and missed delivery deadlines.
Solution: The manufacturer partnered with a reputable box build assembly service provider specializing in electronics assembly. By outsourcing the assembly process, the manufacturer was able to:
- Increase production capacity without the need for additional capital investment in facilities and equipment.
- Leverage the expertise of skilled technicians and engineers dedicated to efficient assembly processes.
- Reduce lead times and improve on-time delivery rates, enhancing customer satisfaction.
- Focus internal resources on product design, marketing, and sales activities.
Result: Within the first year of partnering with the box build assembly service provider, the electronics manufacturer saw a 25% increase in production output, a 30% reduction in assembly-related costs, and a significant improvement in customer satisfaction ratings.
Case Study 2: Medical Device Company
A medical device company was facing stringent regulatory requirements and quality control challenges in the assembly of their specialized surgical instruments. Their in-house assembly operations were struggling to meet the necessary standards, leading to potential compliance issues and quality concerns.
Solution: The company outsourced their box build assembly process to a service provider specializing in medical device assembly. This provider had extensive experience in adhering to regulatory guidelines and maintaining strict quality control measures.
- The service provider implemented stringent quality assurance procedures, including rigorous testing and documentation processes.
- Clean room environments and specialized equipment were utilized to ensure the highest levels of precision and sterility.
- Continuous training and certification programs were in place to maintain the expertise of the assembly technicians.
Result: By partnering with the specialized box build assembly service provider, the medical device company was able to:
- Achieve full compliance with regulatory requirements and industry standards.
- Significantly reduce the occurrence of quality issues and product defects.
- Increase customer confidence in the reliability and safety of their products.
- Focus internal resources on research and development, enhancing their competitive edge in the market.
Case Study 3: Industrial Machinery Manufacturer
An industrial machinery manufacturer was experiencing challenges in managing the assembly of their complex equipment due to fluctuating demand and limited in-house capacity. This led to production bottlenecks, delayed deliveries, and increased costs.
Solution: The manufacturer partnered with a box build assembly service provider that offered scalable and flexible assembly solutions. This provider had the capability to rapidly adjust their assembly workforce and resources based on the manufacturer’s changing needs.
- During periods of high demand, the service provider could quickly allocate additional technicians and production lines to meet the increased assembly requirements.
- During slower periods, the service provider could scale down their operations, reducing the manufacturer’s overhead costs.
- The service provider also implemented lean manufacturing principles and streamlined assembly processes, further improving efficiency and reducing waste.
Result: By outsourcing their box build assembly needs, the industrial machinery manufacturer was able to:
- Respond quickly to fluctuations in demand, ensuring timely delivery of products to their customers.
- Reduce inventory carrying costs and minimize production bottlenecks.
- Leverage the expertise and efficiency of a dedicated assembly workforce.
- Focus internal resources on product development, sales, and customer support activities.
These case studies demonstrate the versatility and effectiveness of box build assembly services across various industries and highlight the potential benefits of partnering with the right service provider.
Frequently Asked Questions (FAQs)
1. What is the typical lead time for box build assembly services?
The lead time for box build assembly services can vary depending on several factors, such as the complexity of the product, the availability of components, and the service provider’s capacity. Generally, service providers strive to offer competitive lead times, often ranging from a few days to several weeks. However, it is essential to discuss your specific requirements with the service provider to obtain an accurate estimate.
2. How are quality control measures implemented in box build assembly services?
Quality control is a critical aspect of box build assembly services. Service providers typically employ a combination of processes and techniques to ensure quality standards are met. These may include:
- Incoming material inspections
- In-process quality checks
- Final product testing and verification
- Statistical process control (SPC)
- Adherence to industry-specific regulations and standards (e.g., ISO 9001, FDA, etc.)
- Comprehensive documentation and traceability
Additionally, many service providers have dedicated quality assurance teams and implement continuous improvement programs to maintain high levels of quality.
3. Can box build assembly services handle complex or custom products?
Yes, reputable box build assembly service providers have the capability and expertise to handle complex and custom products. They often employ skilled technicians and engineers who are trained to work with intricate designs, specialized components, and unique assembly requirements. Service providers may also offer design for assembly (DFA) services, where they collaborate with clients to optimize product designs for efficient assembly processes.
4. How is intellectual property protected when outsourcing box build assembly services?
Protecting intellectual property (IP) is a valid concern when outsourcing assembly services. Reputable service providers typically have robust measures in place to safeguard their clients’ IP. These measures may include:
- Non-disclosure agreements (NDAs) and confidentiality clauses
- Secure facilities and access controls
- Employee training and awareness programs
- Data protection and cybersecurity protocols
- Segregation of client projects and information
It is essential to discuss IP protection measures with the service provider and ensure that appropriate safeguards are in place before engaging their services.
5. Can box build assembly services accommodate fluctuations in demand?
One of the key advantages of outsourcing box build assembly services is the ability to scale operations up or down based on demand fluctuations. Service providers typically have flexible workforce models and production capacities that allow them to adjust their resources accordingly. This flexibility enables clients to respond quickly to changes in market demand, seasonal variations, or unexpected spikes in orders without incurring significant overhead costs.
Conclusion
Box build assembly services offer a valuable solution for businesses seeking to streamline their operations, reduce costs, and access specialized expertise. By outsourcing the assembly process, companies can focus on their core competencies, achieve greater operational efficiency, and respond more effectively to market demands.
With the right box build assembly service provider, businesses can leverage the benefits of scalability, cost savings, and access to skilled technicians and advanced assembly processes. By carefully evaluating potential partners and selecting a provider that aligns with their specific needs, companies can gain a competitive edge and enhance their overall productivity and customer satisfaction.
As the demand for efficient and cost-effective assembly solutions continues to grow, box build assembly services will play an increasingly important role in supporting various industries and enabling businesses to adapt to evolving market conditions.
No responses yet