Introduction to PCB Hole Tolerances
Printed Circuit Boards (PCBs) are essential components in modern electronics, serving as the foundation for mounting and connecting various Electronic Components. One critical aspect of PCB Design and manufacturing is the accuracy of drilled holes, which are used for component leads, vias, and mounting purposes. Understanding and properly specifying hole size tolerances is crucial for ensuring the functionality, reliability, and manufacturability of PCBs.
In this article, we will delve into the world of PCB hole tolerances, exploring the factors that influence them, industry standards, and best practices for designers and manufacturers. By the end of this article, you will have a comprehensive understanding of how to effectively manage hole size tolerances in your PCB projects.
The Importance of PCB Hole Tolerances
Functionality and Reliability
Accurate hole sizes are critical for the proper functioning and reliability of PCBs. If holes are too small, component leads may not fit properly, leading to assembly issues and potential damage to the components or the PCB itself. On the other hand, if holes are too large, components may not be securely held in place, resulting in poor electrical connections and reduced mechanical stability.
Manufacturing Feasibility
PCB hole tolerances also play a significant role in the manufacturability of the board. Overly tight tolerances can increase production costs and lead times, as they require more precise drilling equipment and stricter quality control measures. Conversely, excessively loose tolerances may result in a higher rate of manufacturing defects and reduced yield.
Cost Considerations
Striking the right balance between hole size accuracy and manufacturing feasibility is essential for optimizing costs. Specifying unnecessarily tight tolerances can drive up production expenses, while overly loose tolerances may lead to increased rework and scrap rates. By understanding the factors that influence hole size tolerances and following industry best practices, designers and manufacturers can achieve the desired level of accuracy while minimizing costs.
Factors Influencing PCB Hole Tolerances
Several factors contribute to the variation in PCB hole sizes, including:
Drilling Method
The drilling method employed during PCB manufacturing has a significant impact on hole size tolerances. The two primary drilling methods are mechanical drilling and laser drilling.
Mechanical Drilling
Mechanical drilling, also known as conventional drilling, uses high-speed drill bits to create holes in the PCB Substrate. This method is widely used for larger hole sizes and is generally more economical than laser drilling. However, mechanical drilling is subject to tool wear, which can affect hole size consistency over time.
Laser Drilling
Laser drilling utilizes focused laser beams to create holes in the PCB substrate. This method offers higher precision and is well-suited for smaller hole sizes and high-density designs. Laser drilling eliminates the issue of tool wear, resulting in more consistent hole sizes throughout the production run. However, laser drilling equipment is more expensive than mechanical drilling machines, which can impact overall production costs.
PCB Material
The choice of PCB substrate material can also influence hole size tolerances. Different materials have varying degrees of hardness, thermal stability, and moisture absorption, which can affect the drilling process and the resulting hole sizes.
FR-4
FR-4 is the most commonly used PCB substrate material, offering a good balance of mechanical and electrical properties. It is a composite material made of woven fiberglass fabric impregnated with an epoxy resin. FR-4 is relatively easy to drill and provides a stable base for hole size consistency.
High-Frequency Materials
High-frequency PCB materials, such as Rogers RO4000 series or Isola IS680, are designed for applications that require low dielectric loss and stable performance at high frequencies. These materials often have different drilling characteristics compared to FR-4, which can affect hole size tolerances. Manufacturers may need to adjust their drilling parameters and tolerances when working with high-frequency materials.
Flexible Substrates
Flexible PCBs, made from materials like polyimide or polyester, present unique challenges for hole size tolerances. The flexible nature of the substrate can lead to stretching or deformation during the drilling process, affecting hole size consistency. Special handling and drilling techniques may be required to maintain hole size accuracy in flexible PCBs.
Hole Aspect Ratio
The aspect ratio of a hole refers to the ratio of its depth to its diameter. Higher aspect ratios, meaning deeper holes relative to their diameter, can be more challenging to drill accurately. As the aspect ratio increases, drill bits are more prone to wandering or breaking, leading to variations in hole size.
Designers should be aware of the aspect ratio limitations of their chosen manufacturing process and design holes accordingly. In general, aspect ratios of 8:1 or less are considered manageable for most PCB manufacturing processes. For higher aspect ratios, specialized drilling techniques or multiple drilling passes may be necessary to maintain hole size accuracy.
Plating and Finishing
The plating and finishing processes applied to PCBs can also impact hole size tolerances. Copper plating, used to create conductive layers on the hole walls, can slightly reduce the finished hole diameter. The thickness of the copper plating should be taken into account when specifying hole sizes.
Additionally, surface finishes like Hot Air Solder Leveling (HASL), Immersion Silver, or Electroless Nickel Immersion Gold (ENIG) can affect hole sizes, particularly for smaller diameter holes. The thickness of the surface finish should be considered when determining the final hole size tolerances.
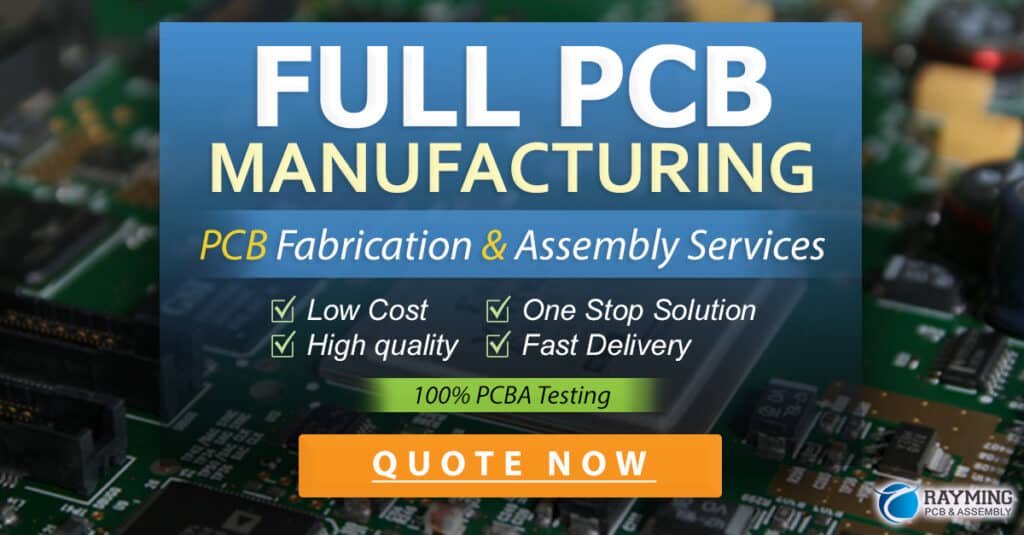
Industry Standards for PCB Hole Tolerances
Several industry standards provide guidelines for PCB hole size tolerances, helping designers and manufacturers ensure consistency and reliability.
IPC Standards
The Association Connecting Electronics Industries (IPC) is a global trade association that develops standards for the electronics industry. IPC-6012, “Qualification and Performance Specification for Rigid Printed Boards,” is a widely recognized standard that includes guidelines for hole size tolerances.
According to IPC-6012, the finished hole size tolerance for plated through holes should be:
Nominal Hole Size (mm) | Tolerance (mm) |
---|---|
0.2 – 0.4 | ±0.05 |
0.4 – 0.8 | ±0.08 |
0.8 – 1.5 | ±0.10 |
1.5 – 2.5 | ±0.13 |
2.5 – 4.0 | ±0.15 |
> 4.0 | ±0.20 |
For non-plated through holes, the finished hole size tolerance is typically specified as +0.05 mm / -0.00 mm, regardless of the nominal hole size.
Manufacturer Specific Standards
In addition to industry-wide standards, individual PCB manufacturers may have their own internal standards and capabilities for hole size tolerances. These standards are often based on the specific equipment and processes used by the manufacturer.
When working with a PCB manufacturer, it is essential to communicate your hole size requirements clearly and to understand their specific capabilities and limitations. Engaging with the manufacturer early in the design process can help ensure that your design is compatible with their manufacturing processes and can be produced reliably and cost-effectively.
Best Practices for Managing PCB Hole Tolerances
To effectively manage PCB hole size tolerances and ensure the best possible outcomes for your PCB projects, consider the following best practices:
Collaborate with Your Manufacturer
Engage with your PCB manufacturer early in the design process to discuss your hole size requirements and understand their specific capabilities and limitations. They can provide valuable insights and guidance on how to optimize your design for manufacturability and reliability.
Consider the End-Use Environment
When specifying hole size tolerances, consider the end-use environment of your PCB. Applications that are subject to extreme temperatures, vibration, or other harsh conditions may require tighter tolerances to ensure reliable performance over the product’s lifetime.
Use Appropriate Drill Bit Sizes
Select drill bit sizes that are appropriate for your hole size requirements and the capabilities of your chosen manufacturing process. Using excessively small drill bits can lead to increased tool wear and breakage, while using oversized drill bits can result in larger than desired hole sizes.
Specify Tolerances Based on Criticality
Not all holes on a PCB are equally critical to the board’s functionality and reliability. Identify the most critical holes, such as those used for component leads or high-current vias, and specify tighter tolerances for these holes. Less critical holes, such as those used for mounting or low-current vias, can often be specified with looser tolerances, helping to balance cost and manufacturability.
Allow for Plating and Finishing Thicknesses
When specifying hole sizes, account for the thickness of copper plating and surface finishes that will be applied to the PCB. These layers will slightly reduce the finished hole diameter, so it is essential to factor them into your design and tolerances.
Communicate Clearly with Documentation
Provide clear and comprehensive documentation to your PCB manufacturer, including detailed hole size requirements and tolerances. Use industry-standard notations and symbols to ensure that your requirements are easily understood and accurately implemented.
Conduct Thorough Testing and Inspection
Perform thorough testing and inspection of your PCBs, both during the manufacturing process and upon receipt of the finished boards. This will help identify any issues with hole sizes early on and allow for corrective action to be taken if necessary.
Frequently Asked Questions (FAQ)
1. What is the difference between plated and non-plated through holes on a PCB?
Plated through holes (PTHs) are drilled holes that have been coated with a conductive material, typically copper, to create an electrical connection between the layers of the PCB. Non-plated through holes (NPTHs) are drilled holes that do not have a conductive coating and are used for purposes such as component mounting or alignment.
2. How do I determine the appropriate hole size tolerances for my PCB design?
The appropriate hole size tolerances for your PCB design will depend on several factors, including the components being used, the end-use environment, and the capabilities of your chosen manufacturing process. Consult industry standards such as IPC-6012 for guidance, and collaborate with your PCB manufacturer to determine the best tolerances for your specific project.
3. Can I specify different hole size tolerances for different parts of my PCB?
Yes, you can specify different hole size tolerances for different parts of your PCB based on the criticality of the holes and the requirements of the components being used. This can help balance cost and manufacturability while ensuring that the most critical holes meet the necessary tolerances for functionality and reliability.
4. How do I communicate my hole size requirements to my PCB manufacturer?
To communicate your hole size requirements to your PCB manufacturer, provide clear and comprehensive documentation that includes detailed hole size specifications and tolerances. Use industry-standard notations and symbols to ensure that your requirements are easily understood and accurately implemented.
5. What should I do if I receive PCBs with hole sizes that are out of tolerance?
If you receive PCBs with hole sizes that are out of tolerance, contact your PCB manufacturer immediately to discuss the issue and determine the best course of action. Depending on the severity of the issue and the specific requirements of your project, the manufacturer may need to rework or replace the affected boards.
Conclusion
PCB hole size tolerances play a critical role in ensuring the functionality, reliability, and manufacturability of printed circuit boards. By understanding the factors that influence hole size tolerances, adhering to industry standards, and following best practices for design and communication, you can effectively manage hole size requirements in your PCB projects.
Remember to collaborate closely with your PCB manufacturer, consider the end-use environment, and specify tolerances based on the criticality of the holes. By taking a proactive and informed approach to hole size tolerances, you can optimize your PCB designs for success and achieve the best possible outcomes for your projects.
No responses yet