What is silk-screen“>PCB Silk-screen?
PCB silk-screen, also known as legend or nomenclature, is a layer of text and symbols printed on the surface of a printed circuit board (PCB). The purpose of the silk-screen is to provide information about the components, their placement, and the overall functionality of the PCB. This information is crucial for assembly, testing, and maintenance of the electronic device.
The silk-screen layer is typically printed using a fine mesh screen and a special ink that adheres to the PCB surface. The ink is usually white, but other colors such as black, yellow, or red can also be used depending on the PCB’s color and design requirements.
Benefits of PCB Silk-screen
- Improved readability: Silk-screen makes it easier to identify components and their orientation on the PCB, which is particularly helpful during assembly and debugging.
- Enhanced aesthetics: A well-designed silk-screen can make the PCB look more professional and visually appealing.
- Increased durability: The silk-screen ink is resistant to wear and tear, ensuring that the information remains legible throughout the PCB’s lifespan.
- Better documentation: The silk-screen can include important information such as the PCB version, company logo, and safety warnings, which can be useful for documentation and traceability purposes.
Designing PCB Silk-screen
Best Practices
When designing the silk-screen layer for a PCB, there are several best practices to follow:
- Keep it simple: Use clear and concise text, and avoid overcrowding the PCB with unnecessary information.
- Use appropriate font size: Ensure that the text is legible and easily readable. A minimum font size of 0.8mm is recommended for standard PCBs.
- Maintain clearance: Keep a minimum clearance of 0.2mm between the silk-screen and other PCB features such as pads, traces, and vias to avoid short circuits and manufacturing issues.
- Optimize component placement: Place components in a logical and organized manner, and use the silk-screen to provide clear labels and orientation indicators.
- Consider the manufacturing process: Ensure that the silk-screen design is compatible with the chosen manufacturing process and the capabilities of the PCB fabricator.
Silk-screen Design Software
There are several software tools available for designing PCB silk-screen, including:
- Altium Designer: A popular PCB Design Software that offers comprehensive silk-screen design features.
- Eagle: A widely used PCB design software that provides a user-friendly interface for silk-screen design.
- KiCad: An open-source PCB design software that includes silk-screen design capabilities.
- OrCAD: A powerful PCB design software suite that offers advanced silk-screen design tools.
Software | Silk-screen Design Features | Ease of Use | Price |
---|---|---|---|
Altium Designer | Comprehensive silk-screen design tools, 3D visualization | Moderate | High |
Eagle | User-friendly interface, extensive library support | Easy | Moderate |
KiCad | Open-source, growing community support | Moderate | Free |
OrCAD | Advanced silk-screen design features, simulation capabilities | Complex | High |
PCB Silk-screen Printing Process
Screen Printing
The most common method for printing silk-screen on PCBs is screen printing. This process involves the following steps:
- Screen preparation: A fine mesh screen is coated with a light-sensitive emulsion and exposed to UV light through a film positive of the silk-screen artwork. The exposed areas of the emulsion harden, while the unexposed areas remain soluble.
- Ink application: The screen is placed over the PCB, and the silk-screen ink is applied using a squeegee. The ink passes through the open areas of the screen and onto the PCB surface.
- Curing: The printed PCB is then sent through a curing process to dry and harden the ink, ensuring its durability and adhesion to the PCB surface.
Other Printing Methods
In addition to screen printing, there are other methods for applying silk-screen to PCBs, such as:
- Liquid Photo Imaging (LPI): This process uses a photosensitive polymer ink that is applied to the PCB surface and then exposed to UV light through a film negative of the silk-screen artwork. The exposed areas of the ink cure and adhere to the PCB, while the unexposed areas are washed away.
- Direct Ink Jet Printing: This method uses a specialized ink jet printer to directly print the silk-screen artwork onto the PCB surface. This process is faster and more flexible than screen printing but may not be suitable for high-volume production.
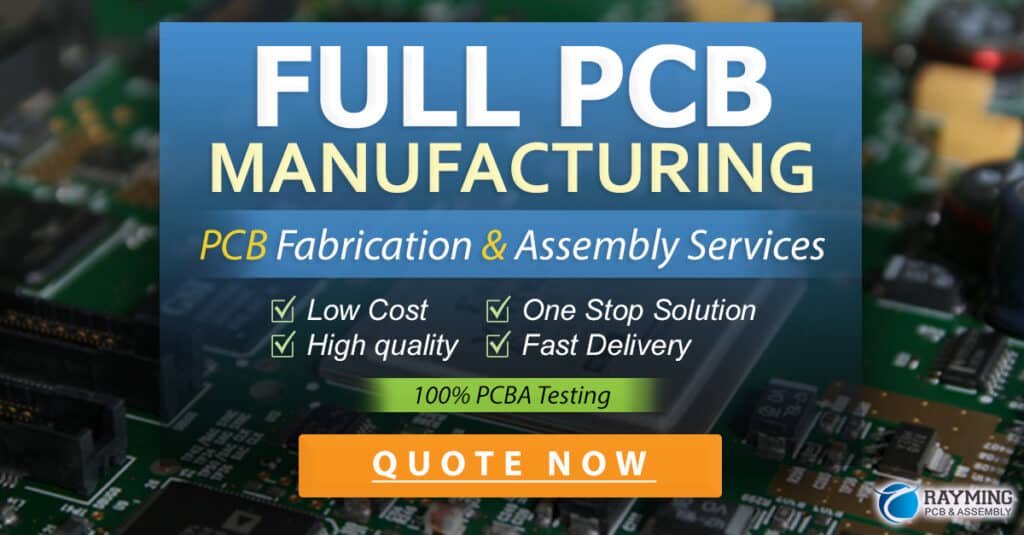
PCB Silk-screen Curing Process
After the silk-screen ink is applied to the PCB surface, it must undergo a curing process to ensure its durability and adhesion. The curing process involves exposing the printed PCB to heat, UV light, or a combination of both, depending on the type of ink used.
Thermal Curing
Thermal curing is the most common method for curing silk-screen ink on PCBs. The printed PCB is passed through an oven or a conveyor belt equipped with heating elements. The heat evaporates the solvents in the ink and causes the resin to polymerize, forming a strong and durable layer on the PCB surface.
Typical curing temperatures range from 120°C to 150°C, and the curing time can vary from a few minutes to an hour, depending on the ink formulation and the PCB’s size and thickness.
UV Curing
UV curing is another method for curing silk-screen ink, particularly for inks that contain photosensitive polymers. The printed PCB is exposed to high-intensity UV light, which initiates a rapid polymerization reaction in the ink, causing it to harden and adhere to the PCB surface.
UV curing is generally faster than thermal curing and can be completed in a matter of seconds. However, it requires specialized UV curing equipment and may not be suitable for all types of silk-screen inks.
Advantages of Proper Curing
Proper curing of the silk-screen ink offers several advantages:
- Improved durability: A well-cured silk-screen layer is resistant to abrasion, chemicals, and environmental factors, ensuring that the information remains legible throughout the PCB’s lifespan.
- Better adhesion: Proper curing ensures that the ink adheres strongly to the PCB surface, preventing peeling, chipping, or flaking of the silk-screen layer.
- Enhanced appearance: A properly cured silk-screen has a smooth, even, and professional appearance, contributing to the overall quality and aesthetics of the PCB.
Troubleshooting PCB Silk-screen Issues
Despite following best practices and proper curing procedures, issues may still arise with the PCB silk-screen. Some common problems and their solutions include:
- Incomplete or uneven printing: This can be caused by a clogged or damaged screen, improper ink consistency, or incorrect squeegee pressure. To resolve this issue, clean or replace the screen, adjust the ink viscosity, and ensure proper squeegee technique.
- Poor adhesion: If the silk-screen ink is not adhering properly to the PCB surface, it may be due to inadequate curing, surface contamination, or incompatible ink formulation. Ensure that the curing process is carried out correctly, clean the PCB surface thoroughly before printing, and use an ink that is compatible with the PCB Material and the curing method.
- Smudging or bleeding: This can occur if the ink is too thin or if there is excessive squeegee pressure during printing. Adjust the ink viscosity and ensure proper squeegee technique to minimize smudging and bleeding.
- Misaligned or shifted silk-screen: This can happen if the screen is not properly aligned with the PCB during printing or if the PCB moves during the curing process. Use alignment marks and registration pins to ensure precise screen placement, and secure the PCB properly during curing to prevent shifting.
Frequently Asked Questions (FAQ)
-
Q: What is the minimum font size for PCB silk-screen?
A: The minimum recommended font size for standard PCBs is 0.8mm to ensure legibility and readability. -
Q: Can PCB silk-screen be printed in colors other than white?
A: Yes, PCB silk-screen can be printed in various colors, such as black, yellow, or red, depending on the PCB’s color and design requirements. -
Q: How do I ensure proper adhesion of the silk-screen ink to the PCB surface?
A: To ensure proper adhesion, make sure that the PCB surface is clean and free from contaminants, use an ink that is compatible with the PCB material and the curing method, and carry out the curing process correctly. -
Q: What is the difference between thermal curing and UV curing for PCB silk-screen?
A: Thermal curing uses heat to evaporate solvents and polymerize the ink, while UV curing uses high-intensity UV light to initiate a rapid polymerization reaction. UV curing is generally faster but requires specialized equipment and may not be suitable for all types of inks. -
Q: Can PCB silk-screen be removed or modified after curing?
A: Once the silk-screen ink is cured, it becomes a permanent part of the PCB and cannot be easily removed or modified. If changes are necessary, a new PCB may need to be fabricated with the updated silk-screen design.
In conclusion, PCB silk-screen is a crucial element in the design and manufacture of printed Circuit Boards, providing valuable information for assembly, testing, and maintenance. By following best practices in silk-screen design, printing, and curing, manufacturers can ensure the production of high-quality, reliable, and visually appealing PCBs. As technology advances, new materials and methods for PCB silk-screen may emerge, further enhancing the functionality and aesthetics of electronic devices.
No responses yet