Introduction to PCB design
PCB (Printed Circuit Board) design is the process of creating a layout for electronic components on a printed circuit board. It involves the placement of components, routing of traces, and adherence to various design rules to ensure the proper functioning and manufacturability of the board. PCB design is a critical aspect of electronics engineering, as it determines the performance, reliability, and cost of the final product.
In this article, we will cover the essential steps and considerations involved in PCB design, including component selection, schematic capture, layout design, design rules, and manufacturing considerations.
Understanding the PCB Design Process
Step 1: Define Project Requirements
Before starting the PCB design process, it is crucial to define the project requirements. This includes understanding the functionality of the circuit, the operating environment, and any specific constraints or standards that need to be met. Consider factors such as:
- Circuit functionality and purpose
- Power requirements and voltage levels
- Signal integrity and noise considerations
- Mechanical constraints (size, shape, and mounting)
- Environmental factors (temperature, humidity, and vibration)
- Regulatory standards and certifications
Step 2: Create a Schematic
The next step is to create a schematic diagram of the circuit. A schematic represents the electrical connections and components in a symbolic manner. It serves as a blueprint for the PCB layout and helps in understanding the circuit’s functionality. When creating a schematic, consider the following:
- Use a schematic capture tool (e.g., Eagle, KiCad, or Altium Designer)
- Place components and create electrical connections
- Assign unique reference designators to each component
- Define net names for signal traces
- Specify component values and tolerances
- Add power and ground symbols
- Include any necessary notes or annotations
Step 3: Component Selection and Placement
After creating the schematic, the next step is to select and place components on the PCB layout. Component selection involves choosing the appropriate components based on their electrical specifications, package type, and availability. When placing components, consider the following:
- Group related components together for better organization
- Place components to minimize trace lengths and reduce signal interference
- Consider the mechanical constraints and mounting requirements
- Ensure proper clearance between components for manufacturability
- Orient components for optimal signal flow and ease of assembly
- Use component footprints that match the selected package types
Step 4: Routing and Trace Design
Routing involves creating the conductive traces that connect the components on the PCB. Trace design is critical for maintaining signal integrity and minimizing noise. When routing traces, consider the following:
- Use appropriate trace widths based on the current carrying capacity and signal requirements
- Maintain proper spacing between traces to avoid crosstalk and signal interference
- Use ground planes and power planes to provide a low-impedance return path for signals
- Avoid sharp corners and use smooth bends to minimize signal reflections
- Consider the use of vias for connecting traces on different layers
- Adhere to the manufacturer’s design rules and guidelines
Step 5: Design Rule Check (DRC)
After completing the component placement and routing, it is essential to perform a Design Rule Check (DRC). DRC verifies that the PCB layout meets the specified design rules and constraints. It checks for issues such as:
- Minimum trace width and spacing
- Clearance between components and traces
- Drill hole sizes and spacing
- Solder mask and silkscreen requirements
- Copper pour and thermal relief considerations
Running DRC helps identify and resolve any design rule violations before proceeding to manufacturing.
Step 6: Generate Manufacturing Files
Once the PCB layout is finalized and has passed the DRC, the next step is to generate the necessary manufacturing files. These files are used by the PCB manufacturer to fabricate the board. The common manufacturing files include:
- Gerber files: These are the standard format files that contain information about the copper layers, solder mask, silkscreen, and drill holes.
- Drill files: These files specify the locations and sizes of the drill holes on the PCB.
- Bill of Materials (BOM): The BOM lists all the components used in the design, along with their quantities, part numbers, and specifications.
- Assembly drawings: These drawings provide instructions for the placement and orientation of components on the PCB.
Ensure that the manufacturing files are generated according to the manufacturer’s requirements and specifications.
PCB Design Considerations
Signal Integrity
Signal integrity refers to the quality and reliability of the electrical signals transmitted through the PCB. It is essential to maintain signal integrity to ensure the proper functioning of the circuit. Consider the following factors to improve signal integrity:
- Use appropriate trace widths and spacing to minimize crosstalk and signal reflections
- Implement proper termination techniques to match the impedance of the traces
- Use ground planes and power planes to provide a low-impedance return path for signals
- Avoid long parallel traces to reduce electromagnetic interference (EMI)
- Consider the use of differential signaling for high-speed signals
Power Distribution
Proper power distribution is crucial for the stable operation of the circuit. Consider the following factors when designing the power distribution network:
- Use appropriate trace widths to handle the required current
- Implement power and ground planes to provide a low-impedance power distribution
- Use decoupling capacitors near power-hungry components to reduce noise and voltage fluctuations
- Consider the use of voltage regulators for stable power supply
- Minimize the loop area between power and ground traces to reduce inductance
Thermal Management
Thermal management is essential to ensure that the components on the PCB operate within their specified temperature range. Overheating can lead to component failure and reliability issues. Consider the following thermal management techniques:
- Provide adequate copper pour and thermal relief for heat-generating components
- Use thermal vias to transfer heat from components to the opposite side of the board
- Consider the use of heatsinks or thermal pads for high-power components
- Ensure proper airflow and ventilation in the enclosure
- Perform thermal simulations to identify hot spots and optimize the thermal design
Electromagnetic Compatibility (EMC)
Electromagnetic Compatibility (EMC) refers to the ability of the PCB to operate without causing or being affected by electromagnetic interference (EMI). Consider the following EMC techniques:
- Implement proper grounding and shielding techniques to reduce EMI
- Use filters and suppressors to attenuate unwanted frequencies
- Minimize the loop area of high-frequency signals
- Separate analog and digital circuits to reduce crosstalk
- Adhere to relevant EMC standards and regulations
Manufacturability and Assembly
Designing a PCB with manufacturability and assembly in mind helps reduce costs and improve production efficiency. Consider the following factors:
- Adhere to the manufacturer’s design rules and guidelines
- Use standard component sizes and packages for easy sourcing and assembly
- Provide adequate clearance and spacing for component placement and soldering
- Use appropriate solder mask and silkscreen for component identification and protection
- Consider the use of surface mount technology (SMT) for higher component density and automated assembly
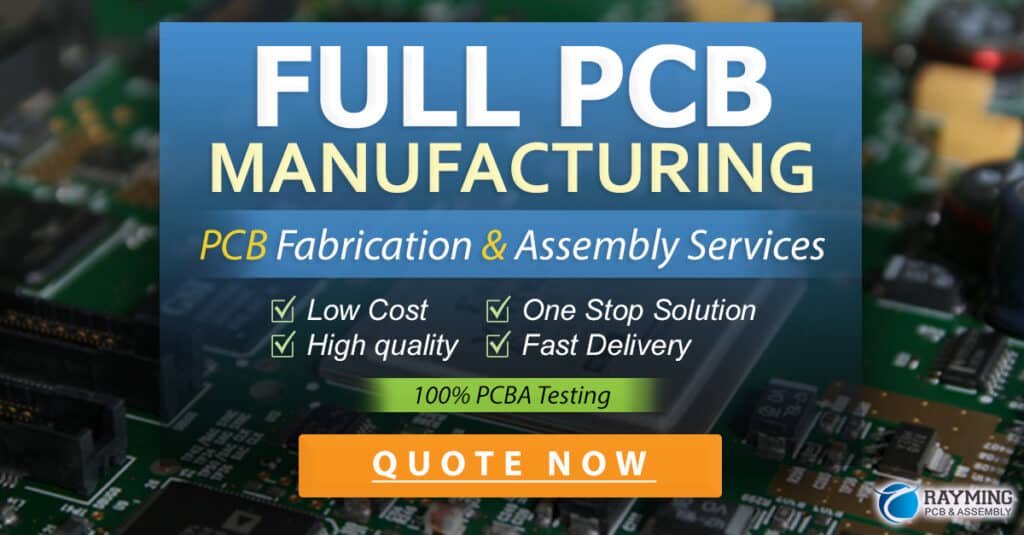
Frequently Asked Questions (FAQ)
-
What software is commonly used for PCB design?
Some popular PCB design software include Altium Designer, Eagle, KiCad, and OrCAD. -
What are the different layers in a PCB?
A typical PCB consists of multiple layers, including copper layers (signal, power, and ground), substrate (insulating material), solder mask, and silkscreen. -
What is the purpose of a ground plane in PCB design?
A ground plane provides a low-impedance return path for signals, reduces EMI, and helps maintain signal integrity. -
What are vias in PCB design?
Vias are small holes drilled through the PCB that allow electrical connections between different layers of the board. -
What is the difference between through-hole and surface mount components?
Through-hole components have leads that are inserted into holes drilled in the PCB, while surface mount components are mounted directly on the surface of the board.
Conclusion
PCB design is a crucial aspect of electronics engineering that requires careful planning, attention to detail, and adherence to design rules and guidelines. By following the steps outlined in this article and considering factors such as signal integrity, power distribution, thermal management, EMC, and manufacturability, you can create reliable and efficient PCB designs.
Remember to use appropriate tools, such as schematic capture software and PCB layout tools, to streamline the design process. Collaborate with manufacturers and assembly partners to ensure that your design meets their requirements and can be successfully fabricated and assembled.
Continuous learning and staying updated with the latest industry trends and techniques will help you improve your PCB design skills and create innovative electronic products.
Component Type | Advantages | Disadvantages |
---|---|---|
Through-hole | – Strong mechanical connection – Easier to solder manually – Suitable for high-power components |
– Larger footprint – Requires drilling holes – Limited component density |
Surface Mount (SMT) | – Smaller footprint – Higher component density – Suitable for automated assembly |
– Requires precise placement – More challenging for manual soldering – Limited power handling capacity |
By understanding the characteristics and trade-offs of different component types, you can make informed decisions when selecting components for your PCB design.
Happy PCB designing!
No responses yet