Introduction to MPS Panels
Manufacturer Part Search (MPS) panels are critical components in various industries, including automotive, aerospace, and electronics manufacturing. These panels are designed to facilitate the search and identification of specific parts required for production, maintenance, or repair processes. By streamlining the part search process, MPS panels help improve efficiency, reduce downtime, and minimize the risk of errors.
What is an MPS Panel?
An MPS panel is a user interface that allows operators to search for and locate specific manufacturer parts quickly. These panels typically consist of a display screen, a keyboard or touchscreen for user input, and a database containing information about various parts, such as their unique identifiers, descriptions, and locations within the facility.
Benefits of Using MPS Panels
The use of MPS panels offers several benefits to manufacturers and other industries that rely on efficient part search and identification processes. Some of the key advantages include:
-
Improved Efficiency: MPS panels allow operators to search for and locate parts quickly, reducing the time spent on manual searches and improving overall productivity.
-
Reduced Downtime: By facilitating faster part identification and retrieval, MPS panels help minimize equipment downtime caused by delays in locating necessary components.
-
Enhanced Accuracy: MPS panels reduce the risk of human error by providing accurate and up-to-date information about parts, ensuring that the correct components are used in production or repair processes.
-
Inventory Management: MPS panels can be integrated with inventory management systems, allowing for real-time tracking of part availability and stock levels.
Common Issues with MPS Panels
Despite their numerous benefits, MPS panels can experience various issues that may hinder their performance or cause disruptions in the part search process. Some of the most common problems encountered with MPS panels include:
1. Software Malfunctions
MPS panels rely on software to function correctly. However, like any software-based system, they can be susceptible to glitches, bugs, or compatibility issues. These software malfunctions can cause the panel to freeze, display incorrect information, or fail to respond to user input.
Troubleshooting Software Issues
To resolve software-related issues with MPS panels, consider the following steps:
-
Restart the System: Often, a simple restart can resolve minor software glitches. Power off the MPS panel, wait a few seconds, and then power it back on.
-
Check for Updates: Ensure that the MPS panel software is up-to-date. Manufacturers often release updates to address known bugs and improve performance.
-
Contact Technical Support: If the issue persists, contact the manufacturer’s technical support team for assistance. They can provide guidance on troubleshooting specific software problems.
2. Hardware Failures
MPS panels consist of various hardware components, such as displays, keyboards, and internal circuitry. Like any electronic device, these components can fail due to wear and tear, physical damage, or manufacturing defects.
Identifying Hardware Failures
Some common signs of hardware failure in MPS panels include:
-
Unresponsive or Malfunctioning Input Devices: If the keyboard or touchscreen fails to respond or produces erratic results, it may indicate a hardware issue.
-
Display Problems: A blank, flickering, or distorted display can suggest a problem with the screen or its connection to the panel’s internal components.
-
Unusual Noises or Smells: Strange noises, such as clicking or buzzing, or unusual smells, like burning odors, can indicate a serious hardware problem that requires immediate attention.
Addressing Hardware Failures
In cases of hardware failure, it is generally recommended to seek professional assistance from the manufacturer or a qualified technician. Attempting to repair hardware issues without proper expertise can lead to further damage or void the panel’s warranty.
3. Connectivity Issues
MPS panels often rely on network connectivity to access part databases and communicate with other systems within the facility. Connectivity issues can disrupt the panel’s functionality and hinder the part search process.
Common Connectivity Problems
Some common connectivity issues encountered with MPS panels include:
-
Network Outages: A failure in the facility’s network infrastructure can prevent the MPS panel from accessing the necessary databases or communicating with other systems.
-
Incorrect Network Settings: Misconfigured network settings, such as incorrect IP addresses or subnet masks, can prevent the MPS panel from establishing a connection.
-
Faulty Cabling: Damaged or loosely connected network cables can cause intermittent or complete loss of connectivity.
Resolving Connectivity Issues
To resolve connectivity issues with MPS panels, consider the following steps:
-
Check Network Status: Verify that the facility’s network is functioning correctly. Contact the IT department if there are any known outages or issues.
-
Review Network Settings: Ensure that the MPS panel’s network settings are correctly configured. Consult the manufacturer’s documentation or technical support for guidance on proper settings.
-
Inspect Cabling: Check the network cables for any signs of damage or loose connections. Replace or securely reconnect cables as needed.
4. Database Errors
MPS panels rely on accurate and up-to-date part databases to function effectively. Database errors, such as corrupted files or outdated information, can lead to incorrect search results or failure to locate parts.
Identifying Database Errors
Some signs of database errors in MPS panels include:
-
Incorrect Search Results: If the MPS panel consistently returns incorrect or irrelevant search results, it may indicate a problem with the part database.
-
Missing or Outdated Information: If the panel fails to display critical information about parts, such as their location or availability, it may suggest that the database is not being properly maintained.
Resolving Database Errors
To address database errors in MPS panels, consider the following steps:
-
Perform Database Updates: Ensure that the part database is regularly updated with the latest information. Work with the appropriate departments to establish a process for maintaining and updating the database.
-
Verify Data Integrity: Periodically check the database for corrupted or inconsistent data. Use database management tools to identify and resolve any issues.
-
Consult Technical Support: If database errors persist, contact the manufacturer’s technical support team for assistance. They can provide guidance on troubleshooting specific database issues and recommend solutions.
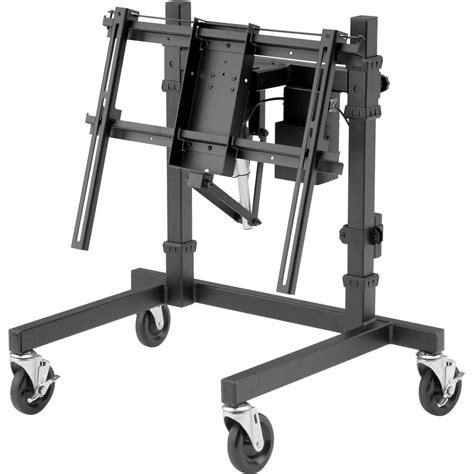
Preventive Maintenance for MPS Panels
To minimize the occurrence of issues and ensure the optimal performance of MPS panels, it is essential to implement a preventive maintenance program. Regular maintenance can help identify and address potential problems before they lead to significant disruptions in the part search process.
Maintenance Checklist
A comprehensive preventive maintenance checklist for MPS panels should include the following items:
-
Software Updates: Regularly check for and install any available software updates provided by the manufacturer. These updates often include bug fixes, performance improvements, and new features.
-
Hardware Inspection: Perform visual inspections of the MPS panel’s hardware components, including the display, keyboard, and any external connections. Look for signs of wear, damage, or loose connections, and address them promptly.
-
Cleaning: Clean the MPS panel’s display and keyboard regularly to prevent the buildup of dust, dirt, and debris. Use manufacturer-recommended cleaning products and methods to avoid damaging the components.
-
Network Maintenance: Work with the IT department to ensure that the facility’s network infrastructure is properly maintained. This includes regular network health checks, firmware updates for network devices, and the replacement of any faulty network components.
-
Database Maintenance: Collaborate with the appropriate departments to establish a regular database maintenance schedule. This may include data backups, integrity checks, and the removal of outdated or irrelevant information.
Training and User Education
In addition to preventive maintenance, it is crucial to provide adequate training and education to the users of MPS panels. Well-informed users are more likely to use the panels correctly, reducing the risk of user-related issues and improving overall efficiency.
Some key topics to cover in user training and education include:
-
Basic Operation: Provide users with a clear understanding of how to operate the MPS panel, including navigating the user interface, performing searches, and interpreting search results.
-
Troubleshooting Common Issues: Educate users on how to identify and resolve common issues, such as software glitches or connectivity problems. Provide them with a checklist of basic troubleshooting steps they can follow before escalating the issue to technical support.
-
Best Practices: Encourage users to follow best practices when using MPS panels, such as performing regular searches to ensure the accuracy of part information, reporting any discrepancies or errors promptly, and handling the panels with care to prevent physical damage.
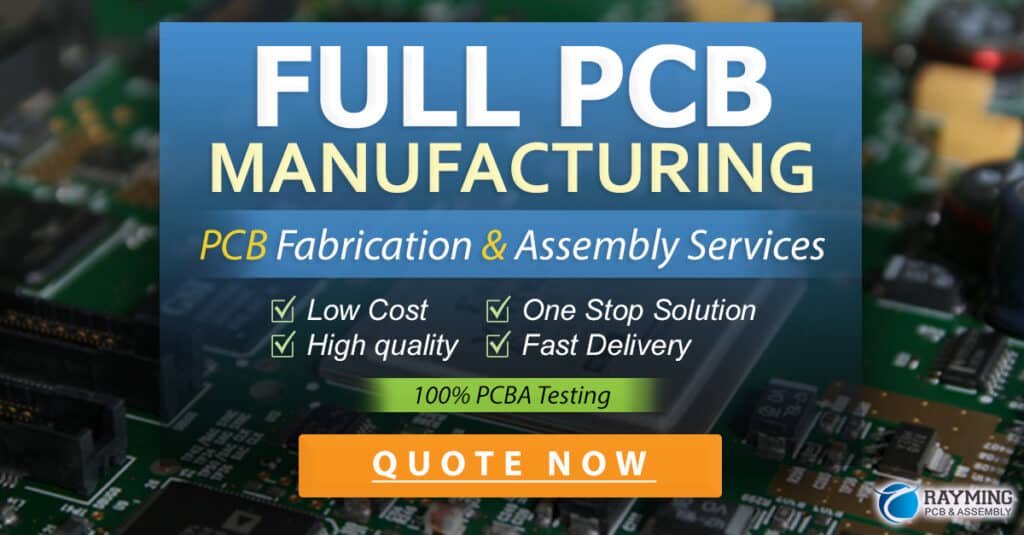
Frequently Asked Questions (FAQ)
-
What should I do if my MPS panel freezes or becomes unresponsive?
If your MPS panel freezes or becomes unresponsive, first try restarting the system by powering it off and then back on. If the issue persists, contact your manufacturer’s technical support team for further assistance. -
How often should I update the software on my MPS panel?
It is recommended to check for and install software updates for your MPS panel regularly, ideally as soon as they become available. These updates often include important bug fixes and performance improvements. -
Can I replace a damaged component of my MPS panel myself?
It is generally not recommended to attempt repairs on MPS panel hardware yourself, as this can lead to further damage or void the warranty. Instead, contact your manufacturer’s technical support or a qualified technician for assistance. -
What should I do if my MPS panel is not connecting to the network?
If your MPS panel is experiencing connectivity issues, first check that your facility’s network is functioning correctly. Then, verify that the panel’s network settings are properly configured and that all network cables are securely connected and free from damage. If the problem persists, consult your IT department or the manufacturer’s technical support. -
How can I ensure that the part database on my MPS panel is accurate and up-to-date?
To maintain an accurate and up-to-date part database, establish a regular database maintenance schedule in collaboration with the appropriate departments within your organization. This should include regular data backups, integrity checks, and the removal of outdated or irrelevant information. Additionally, encourage MPS panel users to report any discrepancies or errors they encounter while using the system.
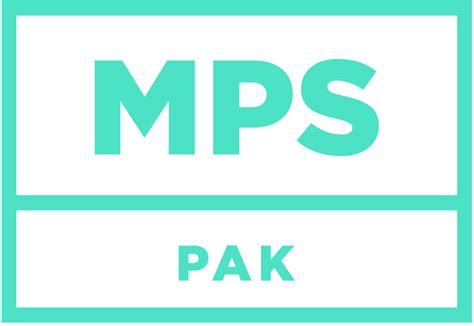
Conclusion
MPS panels are essential tools for streamlining part search and identification processes in various industries. However, like any technology, they can experience issues that impact their performance and reliability. By understanding common problems, such as software malfunctions, hardware failures, connectivity issues, and database errors, organizations can take proactive steps to minimize disruptions and ensure the smooth operation of their MPS panels.
Implementing a comprehensive preventive maintenance program, which includes regular software updates, hardware inspections, cleaning, network maintenance, and database management, can help prevent many common issues and extend the life of MPS panels. Additionally, providing thorough training and education to panel users can further reduce the risk of user-related errors and improve overall efficiency.
By addressing MPS panel issues promptly and effectively, organizations can maximize the benefits of these powerful tools, ultimately improving productivity, reducing downtime, and enhancing the accuracy of their part search and identification processes.
Component | Maintenance Task | Frequency |
---|---|---|
Software | Check for and install manufacturer-provided updates | Monthly |
Hardware – Display | Visually inspect for damage or wear; clean with recommended products | Weekly |
Hardware – Keyboard | Visually inspect for damage or wear; clean with recommended products | Weekly |
Network | Perform network health checks and firmware updates | Monthly |
Database | Perform data backups, integrity checks, and remove outdated data | Weekly |
Table 1: Preventive Maintenance Schedule for MPS Panels
By following this maintenance schedule and addressing any issues that arise promptly, organizations can ensure the optimal performance and longevity of their MPS panels, ultimately benefiting their overall part search and identification processes.
No responses yet