What are Signal Harnesses in Buses?
Signal harnesses, also known as wiring harnesses, are organized sets of wires, terminals, and connectors that transmit electrical power and signals between various components in buses. These harnesses play a crucial role in ensuring the proper functioning of a bus’s electrical system, including lighting, sensors, communication devices, and control modules.
Components of Signal Harnesses
Signal harnesses in buses typically consist of the following components:
- Wires: Insulated conductors that carry electrical current and signals.
- Terminals: Conductive elements that provide connection points for wires and components.
- Connectors: Devices that allow wires and terminals to be easily connected or disconnected.
- Protective coverings: Insulation, conduits, or sheaths that protect the wires from damage and environmental factors.
Advantages of Using Signal Harnesses
Using well-designed signal harnesses in buses offers several advantages:
- Organized wiring: Signal harnesses keep wires neat and tidy, reducing clutter and making maintenance easier.
- Simplified installation: Pre-assembled harnesses can be quickly installed, saving time and labor costs.
- Improved reliability: Properly designed harnesses minimize the risk of electrical faults and ensure consistent performance.
- Enhanced safety: By using appropriate materials and construction techniques, signal harnesses help prevent electrical fires and other hazards.
Types of Signal Harnesses Used in Buses
There are several types of signal harnesses used in buses, each serving specific functions:
Main Wiring Harness
The main wiring harness is the primary electrical distribution system in a bus. It connects the battery, alternator, starter motor, and other major electrical components. This harness typically runs along the chassis and branches out to various sections of the bus.
Engine Wiring Harness
The engine wiring harness connects the engine control module (ECM) to various sensors and actuators in the engine compartment. This harness is responsible for transmitting signals related to engine performance, emissions control, and diagnostics.
Lighting Harness
The lighting harness distributes power to the bus’s interior and exterior lighting systems, including headlights, taillights, turn signals, brake lights, and cabin lighting. This harness ensures that all lights function properly and comply with safety regulations.
HVAC Harness
The heating, ventilation, and air conditioning (HVAC) harness connects the HVAC control module to the blower motor, temperature sensors, and other components of the climate control system. This harness helps maintain a comfortable environment for passengers.
Door Control Harness
The door control harness links the door control module to the door sensors, actuators, and safety devices. This harness ensures that the doors open and close smoothly and safely, and that the bus does not move when the doors are open.
Comparison of Signal Harness Types
Harness Type | Main Function | Key Components Connected |
---|---|---|
Main Wiring | Primary electrical distribution | Battery, alternator, starter |
Engine | Engine control and monitoring | ECM, sensors, actuators |
Lighting | Interior and exterior illumination | Headlights, taillights, cabin lights |
HVAC | Climate control | Blower motor, temperature sensors |
Door Control | Door operation and safety | Door sensors, actuators, safety devices |
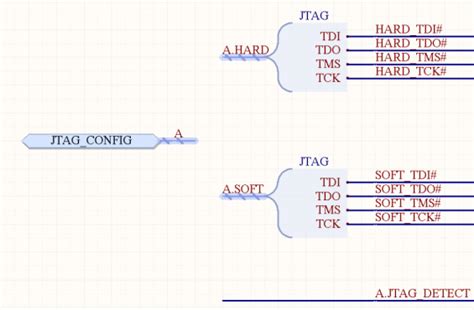
Signal Harness Design and Manufacturing
Designing and manufacturing high-quality signal harnesses for buses involves several key considerations and processes.
Design Considerations
When designing signal harnesses for buses, engineers must take into account factors such as:
- Electrical requirements: Ensuring that the harness can handle the required voltage, current, and signal integrity.
- Environmental conditions: Selecting materials and construction methods that can withstand vibration, temperature extremes, and exposure to chemicals.
- Space constraints: Designing the harness to fit within the available space in the bus while allowing for easy installation and maintenance.
- Safety and regulations: Complying with relevant industry standards and safety regulations.
Manufacturing Process
The manufacturing process for signal harnesses typically includes the following steps:
- Wire cutting and stripping: Cutting wires to the required lengths and removing insulation from the ends.
- Terminal crimping: Attaching terminals to the wire ends using specialized crimping tools.
- Connector assembly: Inserting wires and terminals into connectors and securing them in place.
- Harness assembly: Arranging wires and connectors according to the design specification and applying protective coverings.
- Testing and inspection: Verifying the electrical continuity, insulation resistance, and overall quality of the harness.
Quality Control
To ensure the reliability and performance of signal harnesses, manufacturers implement strict quality control measures, such as:
- Material selection: Using high-quality wires, terminals, and connectors that meet the required specifications.
- Process control: Monitoring and controlling the manufacturing process to maintain consistency and minimize defects.
- Testing and inspection: Conducting thorough electrical and mechanical tests to verify the harness’s functionality and durability.
- Traceability: Maintaining records of materials, processes, and test results for each harness to enable traceability and facilitate problem-solving.
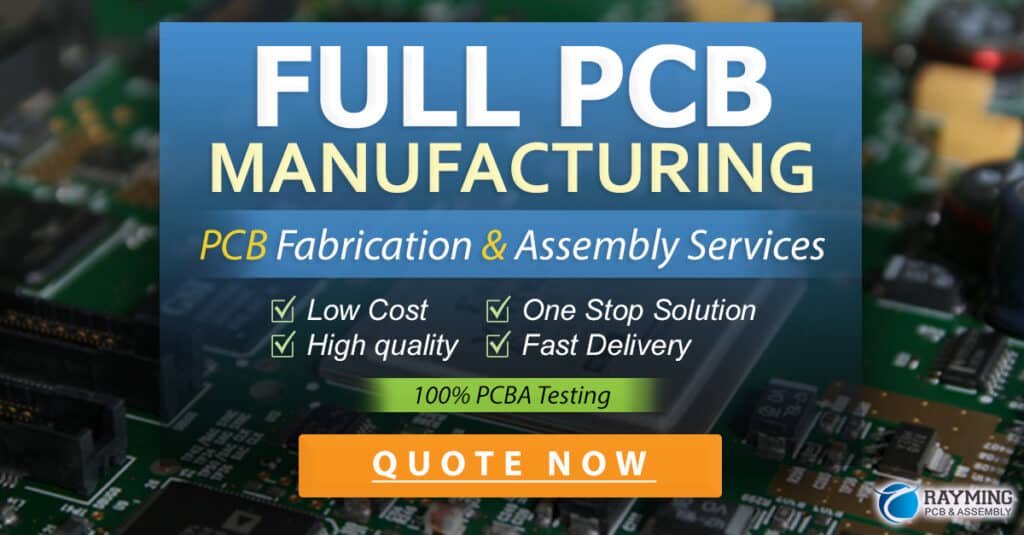
Installation and Maintenance of Signal Harnesses
Proper installation and maintenance of signal harnesses are essential for ensuring the reliable and safe operation of buses.
Installation Procedures
Installing signal harnesses in buses involves the following steps:
- Preparation: Reviewing the installation instructions and gathering the necessary tools and equipment.
- Routing: Carefully laying out the harness along the designated path, securing it with cable ties or clamps, and ensuring proper clearance from moving parts and heat sources.
- Connection: Plugging in connectors to their corresponding components and verifying that all connections are secure and properly seated.
- Testing: Checking the functionality of the connected components and systems to ensure that the harness is installed correctly.
Maintenance and Troubleshooting
Regular maintenance and troubleshooting of signal harnesses help prevent electrical problems and extend the lifespan of the bus’s electrical system. Key maintenance tasks include:
- Visual inspection: Regularly checking the harness for signs of damage, wear, or corrosion.
- Cleaning: Removing dirt, debris, or contaminants that may accumulate on the harness and its components.
- Tightening connections: Periodically checking and tightening any loose connections to prevent electrical faults.
- Diagnostic testing: Using specialized tools and software to diagnose and troubleshoot electrical issues related to the signal harness.
Best Practices for Installation and Maintenance
To optimize the performance and longevity of signal harnesses, follow these best practices:
- Use the correct tools and techniques: Employ the appropriate crimping, stripping, and assembly tools to ensure secure and reliable connections.
- Avoid excessive bending or stretching: Route the harness in a way that minimizes stress on the wires and connectors.
- Protect against environmental factors: Use protective coverings, seals, and grommets to prevent damage from moisture, dust, and other contaminants.
- Document and label: Clearly label each harness and maintain accurate documentation of its installation and maintenance history.
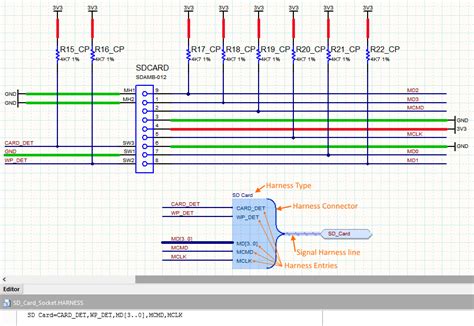
Future Trends and Developments in Bus Signal Harnesses
As technology advances and the demand for more efficient and sustainable transportation grows, signal harnesses in buses are likely to evolve in several ways:
Increased Use of Lightweight Materials
To improve fuel efficiency and reduce emissions, bus manufacturers are increasingly using lightweight materials for signal harnesses, such as:
- Aluminum wires: Replacing traditional copper wires with aluminum can significantly reduce the overall weight of the harness.
- Composite connectors: Using connectors made from lightweight, high-strength composite materials can further reduce weight while maintaining performance.
Integration of Wireless Technology
Wireless technology is expected to play a larger role in bus signal harnesses in the future, offering benefits such as:
- Reduced wiring complexity: Wireless communication between components can simplify the harness design and reduce the number of physical connections required.
- Enhanced flexibility: Wireless technology allows for easier reconfiguration and expansion of the electrical system as needed.
- Improved diagnostics: Wireless sensors and monitoring systems can provide real-time data on the health and performance of the harness and connected components.
Adoption of Smart Harness Technology
Smart harness technology, which incorporates embedded sensors and intelligent control modules, is expected to become more prevalent in buses. This technology offers advantages such as:
- Real-time monitoring: Smart harnesses can continuously monitor the condition of wires, connectors, and components, alerting maintenance personnel to potential issues before they cause failures.
- Predictive maintenance: By analyzing data from smart harnesses, bus operators can predict when maintenance or replacements will be necessary, reducing downtime and costs.
- Enhanced safety: Smart harnesses can detect and respond to electrical faults or anomalies in real-time, helping to prevent accidents and ensure passenger safety.
FAQ
1. What is the purpose of a signal harness in a bus?
A signal harness is a pre-assembled set of wires, terminals, and connectors that transmits electrical power and signals between various components in a bus. It ensures the proper functioning of the bus’s electrical system, including lighting, sensors, communication devices, and control modules.
2. What are the main components of a signal harness?
The main components of a signal harness include:
– Wires: Insulated conductors that carry electrical current and signals.
– Terminals: Conductive elements that provide connection points for wires and components.
– Connectors: Devices that allow wires and terminals to be easily connected or disconnected.
– Protective coverings: Insulation, conduits, or sheaths that protect the wires from damage and environmental factors.
3. What are the different types of signal harnesses used in buses?
The different types of signal harnesses used in buses include:
– Main wiring harness: The primary electrical distribution system in a bus.
– Engine wiring harness: Connects the engine control module to various sensors and actuators.
– Lighting harness: Distributes power to the bus’s interior and exterior lighting systems.
– HVAC harness: Connects the HVAC control module to the climate control system components.
– Door control harness: Links the door control module to the door sensors, actuators, and safety devices.
4. How are signal harnesses manufactured?
The manufacturing process for signal harnesses typically includes the following steps:
1. Wire cutting and stripping
2. Terminal crimping
3. Connector assembly
4. Harness assembly
5. Testing and inspection
Quality control measures, such as material selection, process control, and testing, are implemented to ensure the reliability and performance of the harnesses.
5. What are some future trends and developments in bus signal harnesses?
Some future trends and developments in bus signal harnesses include:
– Increased use of lightweight materials, such as aluminum wires and composite connectors.
– Integration of wireless technology for reduced wiring complexity and enhanced flexibility.
– Adoption of smart harness technology with embedded sensors and intelligent control modules for real-time monitoring, predictive maintenance, and enhanced safety.
No responses yet