What is Rigid-Flex Synchronization?
Rigid-flex synchronization is the process of ensuring that the rigid and flexible sections of a rigid-flex printed circuit board (PCB) are properly aligned and synchronized during the manufacturing process. This is crucial for ensuring the proper functioning and reliability of the final product.
Rigid-flex PCBs are a type of circuit board that combines both rigid and flexible sections, allowing for greater design flexibility and improved performance in certain applications. However, the combination of rigid and flexible sections also presents unique challenges during the manufacturing process, particularly when it comes to ensuring proper synchronization between the two sections.
The Importance of Rigid-Flex Synchronization
Proper synchronization of the rigid and flexible sections is essential for several reasons:
-
Reliability: If the rigid and flexible sections are not properly aligned, it can lead to stress on the connections between the two sections, which can cause failures over time.
-
Functionality: Misalignment of the rigid and flexible sections can also affect the functionality of the final product, particularly if the misalignment is severe enough to cause shorts or opens in the circuit.
-
Manufacturing efficiency: Proper synchronization is also important for ensuring efficient manufacturing processes, as misaligned sections may require additional rework or may even result in scrapped boards.
Techniques for Achieving Rigid-Flex Synchronization
There are several techniques that can be used to achieve proper synchronization of rigid and flexible sections in a rigid-flex PCB:
1. Proper Design
The first step in achieving proper synchronization is to ensure that the PCB is designed correctly from the outset. This includes:
- Ensuring that the rigid and flexible sections are properly dimensioned and positioned relative to each other
- Using appropriate materials for each section (e.g., using flexible materials for the flexible section)
- Incorporating features such as registration holes or fiducials to aid in alignment during manufacturing
2. Careful Material Selection
The materials used for the rigid and flexible sections must be carefully selected to ensure compatibility and to minimize any differences in thermal expansion or contraction that could lead to misalignment.
Some common materials used for rigid-flex PCBs include:
- Polyimide: A flexible polymer material commonly used for the flexible section of the PCB.
- FR-4: A rigid, glass-reinforced epoxy laminate commonly used for the rigid sections of the PCB.
The choice of materials will depend on the specific requirements of the application, such as the required flexibility, temperature range, and environmental conditions.
3. Precise Manufacturing Processes
Achieving proper synchronization also requires precise manufacturing processes, particularly when it comes to aligning and laminating the rigid and flexible sections.
Some key considerations for the manufacturing process include:
- Registration: Ensuring that the rigid and flexible sections are properly aligned and registered with each other during lamination.
- Pressure and temperature: Carefully controlling the pressure and temperature during lamination to ensure proper bonding of the sections without causing misalignment.
- Inspection: Implementing appropriate inspection processes to catch any misalignment issues early in the manufacturing process.
4. Use of Specialized Equipment
Specialized equipment may also be used to aid in achieving proper synchronization of rigid and flexible sections. Some examples include:
- Cameras and vision systems: These can be used to verify proper alignment of the sections during manufacturing.
- Laser drills: Laser drilling can be used to create precise registration holes or other features to aid in alignment.
- Specialized lamination presses: Presses with precise temperature and pressure control can help ensure proper lamination of the sections.
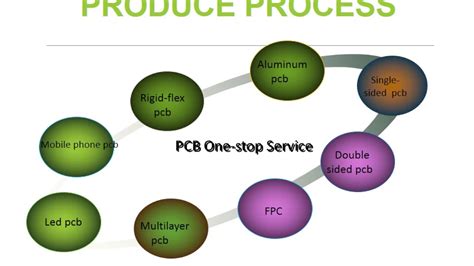
Common Challenges in Rigid-Flex Synchronization
Despite the various techniques available for achieving proper synchronization, there are still several common challenges that can arise:
1. Material Mismatch
Differences in the thermal expansion or contraction of the materials used for the rigid and flexible sections can lead to misalignment issues, particularly during lamination or during temperature cycling in the final application.
To mitigate this, it’s important to carefully select materials with similar thermal properties and to control the temperature and pressure during lamination.
2. Dimensional Variability
Variations in the dimensions of the rigid and flexible sections can also lead to misalignment issues. This can be caused by factors such as material shrinkage or stretching during processing or by variations in the original material dimensions.
Careful process control and inspection can help identify and correct for dimensional variability.
3. Handling and Alignment
Proper handling and alignment of the rigid and flexible sections during manufacturing can also be challenging, particularly for smaller or more complex designs.
The use of specialized fixtures or alignment tools can help ensure proper positioning of the sections during lamination and other processes.
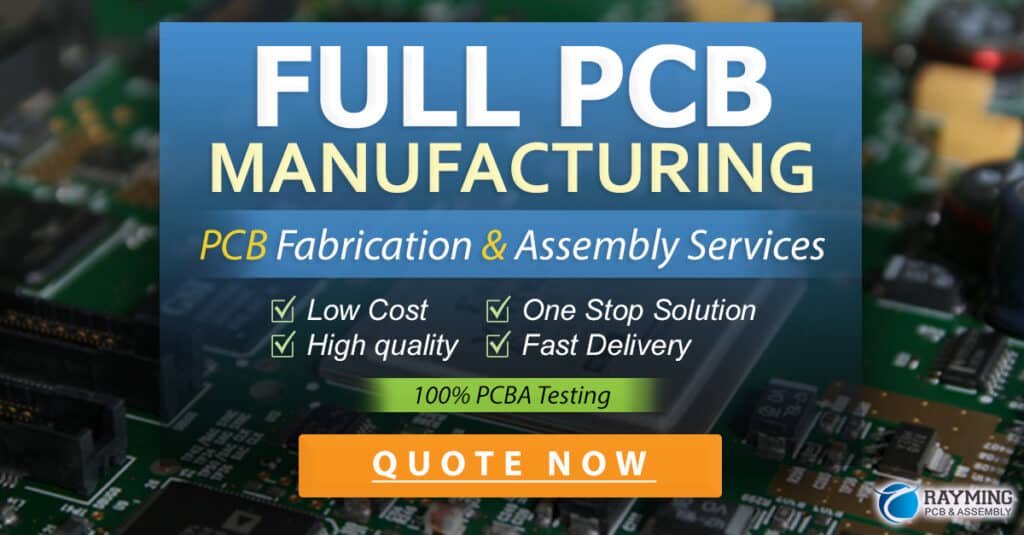
Best Practices for Rigid-Flex Synchronization
To ensure the best possible results for rigid-flex synchronization, several best practices should be followed:
-
Early collaboration: Involve all stakeholders (designers, manufacturers, etc.) early in the design process to ensure that synchronization considerations are addressed from the outset.
-
Detailed documentation: Provide detailed documentation and specifications to the manufacturer to ensure that all requirements for synchronization are clearly understood.
-
Robust design: Incorporate features such as registration holes, fiducials, or other alignment aids into the PCB design to facilitate proper synchronization during manufacturing.
-
Material selection: Carefully select materials for the rigid and flexible sections to ensure compatibility and minimize differences in thermal expansion or contraction.
-
Process control: Implement strict process controls during manufacturing, particularly for critical steps such as lamination, to ensure consistent and repeatable results.
-
Inspection and testing: Implement appropriate inspection and testing processes to catch any synchronization issues early in the manufacturing process and to ensure the final product meets all requirements.
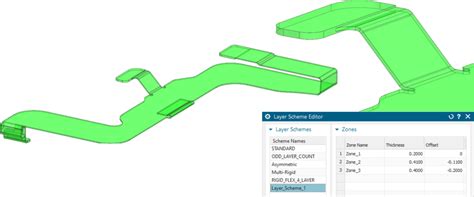
FAQs
-
Q: What is the difference between rigid and flexible PCBs?
A: Rigid PCBs are made from a solid, inflexible material such as FR-4, while flexible PCBs are made from flexible materials such as polyimide. Rigid-flex PCBs combine both rigid and flexible sections into a single board. -
Q: Why is proper synchronization of rigid and flexible sections important?
A: Proper synchronization is essential for ensuring the reliability, functionality, and manufacturing efficiency of the final product. Misalignment of the sections can lead to stress on connections, affect circuit functionality, and require additional rework during manufacturing. -
Q: What are some common techniques for achieving proper synchronization?
A: Common techniques include proper PCB design, careful material selection, precise manufacturing processes, and the use of specialized equipment such as cameras, laser drills, and specialized lamination presses. -
Q: What are some common challenges in achieving proper synchronization?
A: Common challenges include material mismatches, dimensional variability, and difficulties in handling and aligning the sections during manufacturing. -
Q: What are some best practices for ensuring proper synchronization?
A: Best practices include early collaboration among stakeholders, detailed documentation, robust PCB design, careful material selection, strict process controls during manufacturing, and appropriate inspection and testing processes.
Conclusion
Achieving proper synchronization of rigid and flexible sections is a critical consideration in the design and manufacture of rigid-flex PCBs. By understanding the importance of synchronization, the techniques available for achieving it, and the common challenges and best practices, designers and manufacturers can ensure the successful production of reliable and high-performing rigid-flex PCBs.
As the demand for more complex and versatile electronic devices continues to grow, the use of rigid-flex PCBs is likely to increase. By staying up-to-date with the latest techniques and best practices for rigid-flex synchronization, designers and manufacturers can position themselves to meet this demand and deliver innovative and reliable products to their customers.
No responses yet