Understanding the Impact of Supply Chain Disruptions on the Electronics Industry
The electronics industry relies heavily on a complex global supply chain to source the various components needed to manufacture products ranging from smartphones and laptops to automotive systems and industrial equipment. However, this interconnected network of suppliers, manufacturers, and distributors is vulnerable to disruptions caused by a variety of factors, including:
- Natural disasters
- Geopolitical tensions
- Trade disputes
- Pandemics
- Capacity constraints
- Logistics challenges
When these disruptions occur, they can lead to component shortages, price increases, and extended lead times, all of which can have a significant impact on the ability of electronics companies to meet customer demand and maintain profitability.
The Cost of Supply Chain Disruptions
According to a study by Accenture, supply chain disruptions can cause a company’s share price to drop by an average of 7% and can lead to a 62% decrease in profitability over a three-year period. The study also found that it can take up to two years for a company to fully recover from a significant supply chain disruption.
Impact of Supply Chain Disruptions | Average Decrease |
---|---|
Share Price | 7% |
Profitability (over 3 years) | 62% |
Source: Accenture
In addition to the financial impact, supply chain disruptions can also damage a company’s reputation and customer relationships. When customers are unable to obtain the products they need in a timely manner, they may turn to competitors or lose trust in the brand.
Strategies for Mitigating Supply Chain Risks
To minimize the impact of supply chain disruptions on their operations, electronics companies must proactively identify and mitigate potential risks. Some key strategies include:
1. Diversifying the Supplier Base
Relying on a single supplier for a critical component can leave a company vulnerable to disruptions if that supplier experiences issues. By diversifying their supplier base and sourcing components from multiple vendors in different geographic regions, companies can reduce their risk exposure and ensure a more stable supply of components.
2. Implementing Supply Chain Visibility Tools
Supply chain visibility tools, such as real-time tracking systems and analytics platforms, can help companies monitor their supply chain operations and identify potential issues before they escalate into major disruptions. By gaining a clear view of inventory levels, production schedules, and logistics performance, companies can make informed decisions and take proactive measures to mitigate risks.
3. Building Strategic Inventory Buffers
Maintaining a strategic inventory of critical components can help companies weather short-term supply chain disruptions and ensure continuity of production. However, it’s important to strike a balance between holding too much inventory, which can tie up working capital and increase storage costs, and holding too little, which can leave the company vulnerable to shortages.
4. Collaborating with Suppliers and Partners
Establishing close partnerships with key suppliers and logistics providers can help companies better anticipate and respond to supply chain disruptions. By sharing information, aligning production schedules, and jointly developing contingency plans, companies and their partners can work together to minimize the impact of disruptions and ensure a more resilient supply chain.
5. Investing in Supply Chain Risk Management
Developing a comprehensive supply chain risk management program can help companies systematically identify, assess, and mitigate potential risks. This may involve conducting regular risk assessments, developing business continuity plans, and investing in tools and technologies to support risk management efforts.
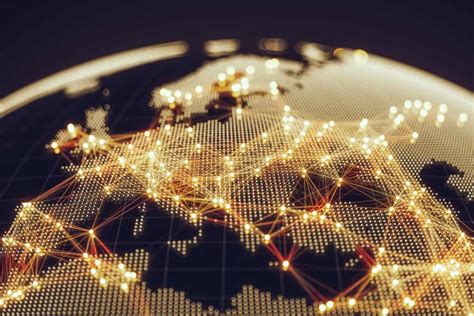
Case Studies: How Electronics Companies Have Overcome Supply Chain Disruptions
Apple’s Response to the COVID-19 Pandemic
The COVID-19 pandemic caused significant disruptions to Apple’s supply chain, as many of its key suppliers in China were forced to shut down or operate at reduced capacity. To mitigate the impact of these disruptions, Apple took several key actions:
- Diversified its supplier base by shifting some production to alternative suppliers in other countries, such as Vietnam and India.
- Worked closely with its existing suppliers to help them resume operations safely and efficiently.
- Adjusted its product launch schedules and inventory management strategies to account for potential delays and shortages.
As a result of these efforts, Apple was able to minimize the impact of the pandemic on its operations and continue to meet customer demand for its products.
Toyota’s Approach to Building Supply Chain Resilience
Toyota, a pioneer in lean manufacturing and just-in-time inventory management, has long recognized the importance of building a resilient supply chain. Some of the key strategies Toyota has employed include:
- Developing close partnerships with suppliers and involving them in the product development process to ensure alignment and collaboration.
- Implementing a multi-tier supplier management system to monitor and manage risks at all levels of the supply chain.
- Investing in advanced analytics and simulation tools to identify potential bottlenecks and optimize supply chain performance.
- Maintaining a strategic inventory of critical components to buffer against short-term disruptions.
By taking a proactive and comprehensive approach to supply chain risk management, Toyota has been able to maintain a high level of resilience and agility in the face of various disruptions over the years.
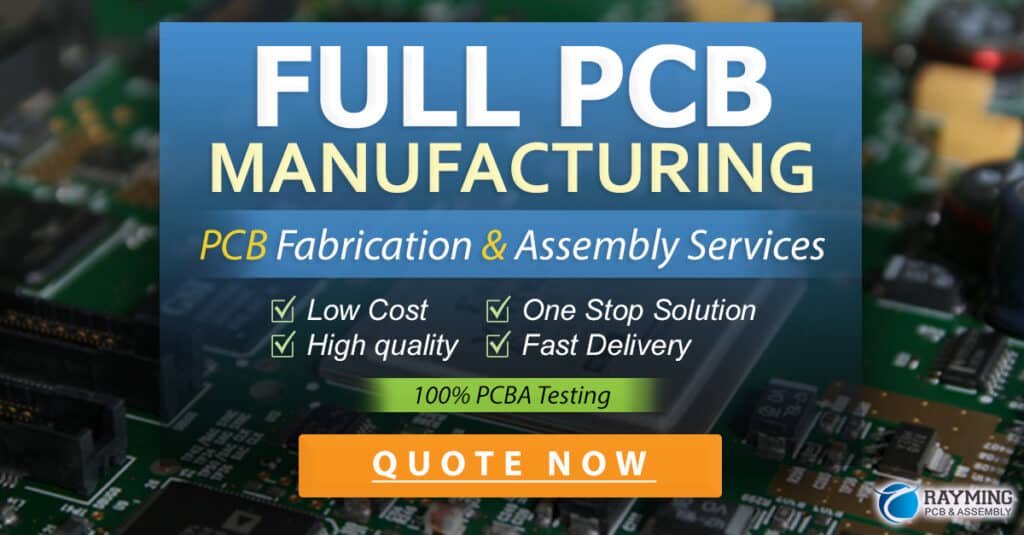
Emerging Technologies for Supply Chain Risk Management
In addition to the strategies outlined above, there are several emerging technologies that can help electronics companies better manage supply chain risks and improve overall resilience. Some of the most promising technologies include:
1. Blockchain
Blockchain technology can be used to create a secure, transparent, and tamper-proof record of supply chain transactions, enabling companies to track the movement of components from origin to destination and verify the authenticity of parts. This can help reduce the risk of counterfeit components entering the supply chain and improve overall visibility and traceability.
2. Artificial Intelligence and Machine Learning
AI and machine learning algorithms can be used to analyze vast amounts of supply chain data and identify patterns and anomalies that may indicate potential risks or disruptions. By leveraging these technologies, companies can gain real-time insights into supply chain performance and make more informed decisions to mitigate risks.
3. Internet of Things (IoT)
IoT sensors and devices can be used to monitor the condition and location of components throughout the supply chain, providing real-time data on factors such as temperature, humidity, and shock. This information can help companies identify potential quality issues and take proactive measures to prevent damage or degradation of components.
4. Digital Twins
Digital twins are virtual replicas of physical supply chain assets and processes that can be used to simulate and optimize supply chain operations. By creating digital twins of their supply chains, companies can test different scenarios and contingency plans, identify potential bottlenecks, and make data-driven decisions to improve resilience and efficiency.
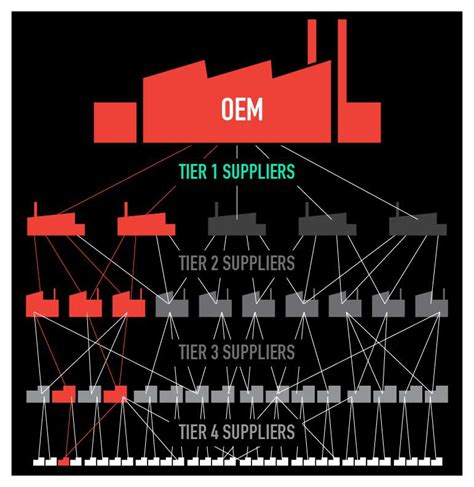
FAQ
1. What are the most common causes of supply chain disruptions in the electronics industry?
Some of the most common causes of supply chain disruptions in the electronics industry include natural disasters, geopolitical tensions, trade disputes, pandemics, capacity constraints, and logistics challenges.
2. How can electronics companies mitigate the impact of supply chain disruptions?
Electronics companies can mitigate the impact of supply chain disruptions by diversifying their supplier base, implementing supply chain visibility tools, building strategic inventory buffers, collaborating with suppliers and partners, and investing in supply chain risk management programs.
3. What are some emerging technologies that can help manage supply chain risks?
Some emerging technologies that can help manage supply chain risks include blockchain, artificial intelligence and machine learning, Internet of Things (IoT), and digital twins.
4. How long does it typically take for a company to recover from a significant supply chain disruption?
According to a study by Accenture, it can take up to two years for a company to fully recover from a significant supply chain disruption.
5. What are the potential consequences of supply chain disruptions for electronics companies?
The potential consequences of supply chain disruptions for electronics companies include decreased profitability, damage to reputation and customer relationships, and loss of market share to competitors. In severe cases, supply chain disruptions can even lead to bankruptcy or business failure.
Conclusion
Supply chain disruptions are a major challenge for the electronics industry, with the potential to cause significant financial losses, damage customer relationships, and even threaten the viability of businesses. To overcome these challenges, electronics companies must take a proactive and comprehensive approach to supply chain risk management, leveraging a combination of proven strategies and emerging technologies.
By diversifying their supplier base, implementing supply chain visibility tools, building strategic inventory buffers, collaborating with partners, and investing in risk management programs, companies can improve their resilience and agility in the face of disruptions. Additionally, by exploring the potential of technologies such as blockchain, AI, IoT, and digital twins, companies can gain new insights and capabilities to help them navigate an increasingly complex and uncertain supply chain landscape.
Ultimately, the key to overcoming supply chain disruptions in the electronics industry is to embrace a culture of continuous improvement and innovation, staying alert to emerging risks and opportunities, and adapting quickly to changing circumstances. By doing so, companies can not only survive but thrive in the face of even the most challenging supply chain disruptions.
No responses yet