Introduction to Aluminum PCB
Aluminum PCB, also known as metal core PCB (MCPCB), is a type of printed circuit board that uses aluminum as the base material instead of the traditional FR-4 substrate. This unique design offers several advantages over standard PCBs, making it an attractive choice for various applications that require efficient heat dissipation, high power density, and improved mechanical stability.
In this article, we will explore the benefits of using aluminum PCB substrate, its applications, and how to incorporate it into your next design. We will also discuss the manufacturing process, design considerations, and frequently asked questions about aluminum PCBs.
Benefits of Using Aluminum PCB Substrate
Excellent Thermal Management
One of the primary advantages of using aluminum PCB substrate is its superior thermal management capabilities. Aluminum has a high thermal conductivity, which allows it to efficiently transfer heat away from the components mounted on the PCB. This is particularly important for high-power applications, such as LED lighting, power electronics, and automotive systems, where excess heat can lead to component failure and reduced performance.
Compared to traditional FR-4 PCBs, aluminum PCBs can dissipate heat up to 10 times more effectively. This improved thermal management helps to maintain stable operating temperatures, prolong component lifespan, and enhance overall system reliability.
Increased Power Density
Aluminum PCBs enable higher power density designs due to their ability to handle greater currents and voltages. The excellent thermal dissipation properties of aluminum allow for more compact layouts, as components can be placed closer together without the risk of overheating. This is particularly beneficial for applications where space is limited, such as in automotive electronics, aerospace systems, and portable devices.
Improved Mechanical Stability
Another advantage of using aluminum PCB substrate is its enhanced mechanical stability. Aluminum provides a rigid and durable base for the PCB, reducing the risk of warping, twisting, or bending under mechanical stress. This is especially important for applications that are subject to vibration, shock, or extreme temperature variations, such as in industrial equipment, transportation systems, and outdoor installations.
Additionally, aluminum PCBs offer better thermal expansion matching with components, minimizing the risk of solder joint failure due to thermal cycling.
Cost-Effective Solution
While aluminum PCBs may have a higher initial cost compared to traditional FR-4 PCBs, they can provide a cost-effective solution in the long run. The improved thermal management and power handling capabilities of aluminum PCBs can help to reduce the need for additional cooling systems, such as heatsinks or fans. This can lead to lower overall system costs, reduced assembly time, and simplified designs.
Moreover, the enhanced reliability and longer lifespan of components on aluminum PCBs can result in lower maintenance and replacement costs over the product’s lifecycle.
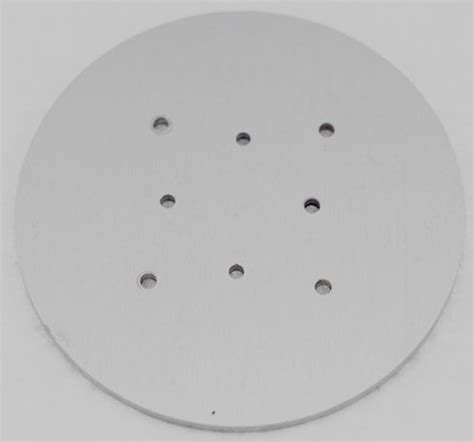
Applications of Aluminum PCB
Aluminum PCBs find applications in various industries and products where thermal management, power density, and mechanical stability are critical. Some common applications include:
-
LED Lighting: Aluminum PCBs are widely used in LED lighting applications, such as high-power LED bulbs, streetlights, and automotive lighting. The excellent thermal dissipation properties of aluminum help to maintain optimal LED performance and prolong the lifespan of the lighting system.
-
Power Electronics: In power electronic applications, such as switch-mode power supplies (SMPS), motor drives, and inverters, aluminum PCBs provide efficient heat dissipation and enable higher power density designs. This is crucial for managing the high currents and voltages involved in these applications.
-
Automotive Electronics: Aluminum PCBs are employed in various automotive electronic systems, such as engine control units (ECUs), power steering controllers, and battery management systems. The enhanced mechanical stability and thermal management capabilities of aluminum PCBs ensure reliable performance in the harsh automotive environment.
-
Aerospace and Defense: In aerospace and defense applications, aluminum PCBs offer a robust and lightweight solution for electronic systems that are subject to extreme temperature variations, vibration, and shock. They are used in avionics, radar systems, and satellite communication equipment.
-
Industrial Equipment: Aluminum PCBs are used in industrial equipment, such as motor controllers, power converters, and automation systems. The improved thermal management and mechanical stability provided by aluminum PCBs ensure reliable operation in demanding industrial environments.
-
Telecommunications: In telecommunications equipment, such as base stations and routers, aluminum PCBs help to manage the heat generated by high-speed processors and RF components. This ensures stable performance and prevents premature component failure.
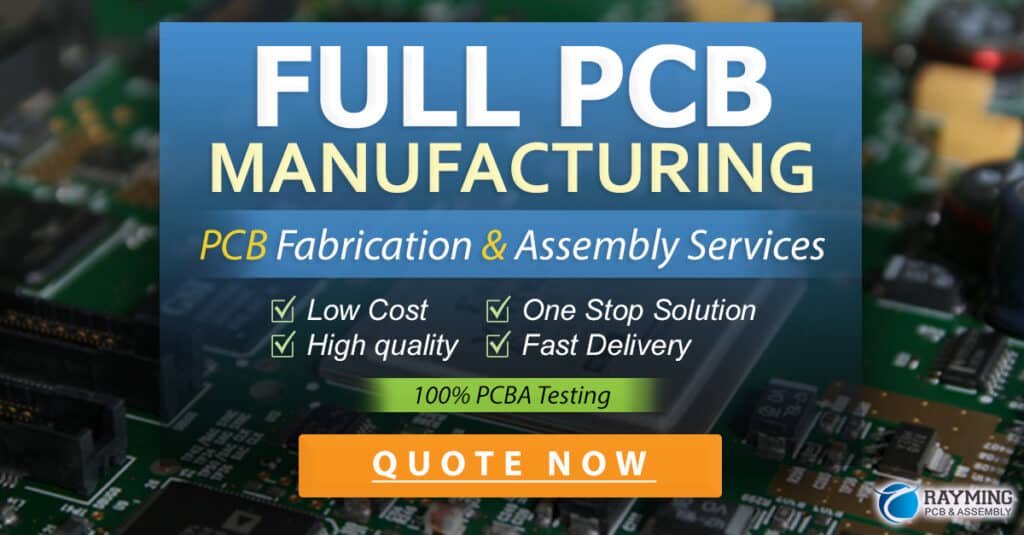
Manufacturing Process of Aluminum PCB
The manufacturing process of aluminum PCB involves several steps that differ from the production of traditional FR-4 PCBs. Understanding these steps is essential for designing and sourcing aluminum PCBs effectively.
-
Substrate Preparation: The aluminum substrate is cleaned and treated to ensure proper adhesion of the dielectric layer. This may involve a combination of chemical etching, brushing, and anodizing processes to create a rough surface that promotes adhesion.
-
Dielectric Layer Application: A thin layer of dielectric material, typically a polymer or epoxy, is applied to the aluminum substrate. This layer acts as an electrical insulator between the aluminum base and the copper traces. The dielectric material is chosen based on its thermal conductivity, electrical insulation properties, and compatibility with the aluminum substrate.
-
Copper Foil Lamination: A copper foil is laminated onto the dielectric layer using heat and pressure. The copper foil thickness is selected based on the desired current carrying capacity and thermal performance of the PCB.
-
Circuit Patterning: The copper foil is patterned using photolithography and etching processes to create the desired circuit layout. This involves applying a photoresist layer, exposing it to UV light through a photomask, and developing the resist to reveal the copper traces.
-
Drilling and Plating: Holes are drilled through the aluminum PCB for component mounting and interconnection. The holes are then plated with copper to create electrical connections between layers and to provide a surface for soldering components.
-
Solder Mask and Silkscreen Application: A solder mask layer is applied to the PCB to protect the copper traces from oxidation and to prevent solder bridges during component assembly. A silkscreen layer is then added to provide component placement and identification markings.
-
Surface Finishing: The exposed copper areas, such as pads and plated through-holes, are coated with a surface finish to protect them from oxidation and to enhance solderability. Common surface finishes for aluminum PCBs include HASL (Hot Air Solder Leveling), ENIG (Electroless Nickel Immersion Gold), and OSP (Organic Solderability Preservative).
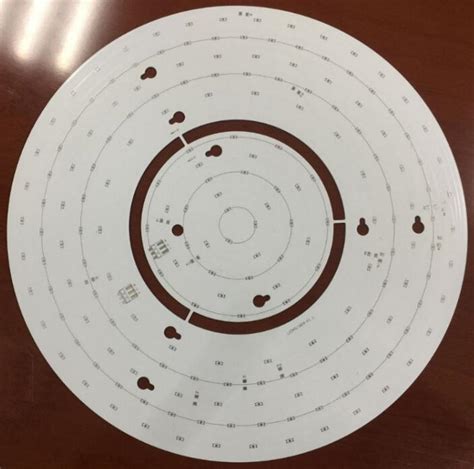
Design Considerations for Aluminum PCB
When designing an aluminum PCB, there are several key factors to consider to ensure optimal performance and manufacturability:
-
Thermal Management: Consider the thermal requirements of your application and design the aluminum PCB accordingly. This may involve selecting the appropriate aluminum substrate thickness, dielectric material, and copper foil thickness to achieve the desired thermal performance. Additionally, incorporate thermal vias and copper pours to enhance heat dissipation.
-
Dielectric Layer Selection: Choose a dielectric material that offers the right balance of thermal conductivity, electrical insulation, and adhesion properties for your application. Common dielectric materials for aluminum PCBs include polyimide, epoxy, and ceramic-filled polymers.
-
Copper Foil Thickness: Select the appropriate copper foil thickness based on the current carrying requirements and thermal performance needs of your design. Thicker copper foils provide better current handling and thermal dissipation but may increase the overall cost and weight of the PCB.
-
Mechanical Considerations: Take into account the mechanical stresses that the aluminum PCB will be subjected to in your application. Design the PCB with appropriate mounting holes, support structures, and strain relief features to ensure mechanical stability and reliability.
-
Manufacturing Constraints: Work closely with your PCB manufacturer to understand their capabilities and constraints for aluminum PCB fabrication. This may include minimum feature sizes, layer count limitations, and available surface finishes. Designing within these constraints will help to ensure a smooth and cost-effective manufacturing process.
-
Assembly Process: Consider the assembly process for your aluminum PCB, including component placement, soldering, and inspection. Ensure that your design is compatible with the chosen assembly methods and that the components can withstand the thermal and mechanical stresses associated with the assembly process.
Frequently Asked Questions (FAQ)
-
Q: What is the difference between aluminum PCB and traditional FR-4 PCB?
A: Aluminum PCB uses an aluminum substrate as the base material, while traditional FR-4 PCB uses a glass-reinforced epoxy laminate. Aluminum PCBs offer superior thermal management, higher power density, and better mechanical stability compared to FR-4 PCBs. -
Q: Can aluminum PCBs be used for multilayer designs?
A: Yes, aluminum PCBs can be fabricated with multiple layers, allowing for more complex circuit designs. However, the number of layers may be limited compared to traditional FR-4 PCBs due to the manufacturing constraints associated with aluminum substrates. -
Q: Are aluminum PCBs more expensive than FR-4 PCBs?
A: Initially, aluminum PCBs may have a higher cost compared to FR-4 PCBs due to the specialized manufacturing process and materials involved. However, the improved thermal management and power handling capabilities of aluminum PCBs can lead to cost savings in the long run by reducing the need for additional cooling systems and enhancing overall system reliability. -
Q: What are the common surface finishes for aluminum PCBs?
A: Common surface finishes for aluminum PCBs include HASL (Hot Air Solder Leveling), ENIG (Electroless Nickel Immersion Gold), and OSP (Organic Solderability Preservative). The choice of surface finish depends on the specific application requirements, such as solderability, durability, and environmental resistance. -
Q: Can aluminum PCBs be used in high-frequency applications?
A: Aluminum PCBs can be used in high-frequency applications, but special considerations must be taken during the design process. The dielectric material and thickness, as well as the copper foil thickness and surface roughness, can impact the high-frequency performance of the PCB. It is essential to work closely with your PCB manufacturer and to perform thorough simulations and testing to ensure that the aluminum PCB meets your high-frequency requirements.
Conclusion
Aluminum PCB substrate offers numerous advantages over traditional FR-4 PCBs, including superior thermal management, increased power density, and improved mechanical stability. These benefits make aluminum PCBs an attractive choice for a wide range of applications, from LED lighting and power electronics to automotive systems and aerospace equipment.
When designing an aluminum PCB, it is crucial to consider factors such as thermal management, dielectric layer selection, copper foil thickness, mechanical requirements, and manufacturing constraints. By carefully addressing these aspects and working closely with your PCB manufacturer, you can unlock the full potential of aluminum PCBs in your next design.
As technology continues to advance and the demand for high-performance, reliable electronic systems grows, aluminum PCBs will undoubtedly play an increasingly important role in shaping the future of PCB design and manufacturing.
No responses yet