Introduction to Thermal Interface Materials
Printed circuit boards (PCBs) are essential components in modern electronic devices, providing a platform for electrical components to be mounted and interconnected. As electronic devices continue to become more compact and powerful, managing heat dissipation has become a critical challenge for PCB designers. Overheating can lead to component failure, reduced performance, and even complete system breakdown.
To address this issue, thermal interface materials (TIMs) are used to facilitate heat transfer between heat-generating components and heat sinks or other cooling solutions. The two most common types of TIMs used in PCB thermal management are thermal pads and thermal paste. Each has its own unique properties, advantages, and disadvantages, making it crucial to understand when to use each material for optimal results.
What are Thermal Pads?
Thermal pads, also known as thermal gap fillers or thermal interface pads, are pre-cut, solid materials that are placed between a heat source and a heat sink to enhance heat transfer. They are typically made from silicone or other polymer materials filled with thermally conductive particles, such as ceramic, alumina, or boron nitride.
Thermal pads come in various thicknesses, ranging from 0.5mm to 5mm, and can be easily cut to fit the specific dimensions of the components being cooled. They offer a simple, clean, and easy-to-use solution for thermal management, as they do not require any preparation or curing time.
What is Thermal Paste?
Thermal paste, also referred to as thermal grease or thermal compound, is a viscous substance applied between a heat source and a heat sink to improve heat transfer. It is composed of a base material, typically silicone or hydrocarbon oil, mixed with thermally conductive fillers like silver, aluminum oxide, or zinc oxide.
Thermal paste works by filling the microscopic air gaps and irregularities between the surfaces of the heat source and heat sink, which would otherwise act as thermal insulators. By displacing the air and creating a thin, uniform layer of thermally conductive material, thermal paste significantly enhances heat transfer efficiency.
Factors to Consider When Choosing Between Thermal Pads and Paste
When deciding between thermal pads and paste for PCB thermal management, several factors must be considered to ensure optimal performance and reliability. These factors include:
- Thermal conductivity
- Ease of application
- Gap filling capability
- Electrical conductivity
- Durability and reliability
- Cost-effectiveness
Thermal Conductivity
Thermal conductivity is a measure of a material’s ability to conduct heat, expressed in watts per meter-kelvin (W/mK). Higher thermal conductivity values indicate better heat transfer performance. When comparing thermal pads and paste, it is essential to consider their respective thermal conductivities.
Thermal pads typically have thermal conductivities ranging from 1 W/mK to 10 W/mK, depending on the material composition and thickness. While this is sufficient for many applications, it may not be enough for high-performance or high-power components.
On the other hand, thermal pastes can have thermal conductivities ranging from 2 W/mK to over 70 W/mK for high-end, silver-based compounds. This makes thermal paste the preferred choice for applications that require the highest level of heat dissipation performance.
TIM Type | Typical Thermal Conductivity Range (W/mK) |
---|---|
Thermal Pads | 1 – 10 |
Thermal Paste | 2 – 70+ |
Ease of Application
The ease of application is another crucial factor when choosing between thermal pads and paste. Thermal pads offer a simple, clean, and user-friendly solution, as they can be easily cut to size and placed between the heat source and heat sink without any preparation or curing time. This makes them ideal for applications where ease of assembly and maintenance is a priority.
Thermal paste, however, requires a more involved application process. The paste must be applied in a thin, even layer, taking care to avoid air bubbles or excessive amounts that could hinder heat transfer. Additionally, some thermal pastes may require a curing period to achieve optimal performance. This can make the assembly process more time-consuming and complicated, especially for inexperienced users.
Gap Filling Capability
The ability to fill gaps between the heat source and heat sink is another important consideration when selecting a TIM. Thermal pads are available in various thicknesses, allowing them to accommodate larger gaps and surface irregularities. This makes them suitable for applications where the mating surfaces are not perfectly flat or where there is a significant height difference between components.
Thermal paste, on the other hand, is designed to fill microscopic air gaps and create a thin, uniform layer between surfaces. While it excels at filling small irregularities, it may not be suitable for applications with larger gaps or significant surface unevenness. In such cases, using a thicker thermal pad or a combination of thermal pad and paste may be necessary to ensure proper heat transfer.
Electrical Conductivity
Some thermal interface materials, particularly those containing metallic fillers like silver or aluminum, may exhibit electrical conductivity. This can be a concern in applications where electrical isolation between components is required to prevent short circuits or signal interference.
Most thermal pads are electrically insulating, making them suitable for use in applications where electrical conductivity is not desired. However, it is essential to verify the specific properties of the thermal pad being used, as some may contain conductive fillers.
Thermal pastes, especially those with high metal content, can be electrically conductive. In applications where electrical isolation is crucial, it is important to select a non-conductive thermal paste or use an electrically insulating thermal pad in conjunction with the paste.
Durability and Reliability
The long-term durability and reliability of the TIM are critical factors in ensuring the longevity and performance of the electronic device. Thermal pads are generally more durable and stable over time, as they are solid materials that do not degrade or pump out under normal operating conditions. They also have a lower risk of drying out or hardening, which can lead to reduced thermal performance.
Thermal pastes, while initially providing excellent thermal conductivity, may be more susceptible to degradation over time. Factors such as high temperatures, thermal cycling, and exposure to environmental contaminants can cause the paste to dry out, harden, or pump out from between the mating surfaces. This can result in reduced heat transfer efficiency and potentially lead to component failure.
Cost-Effectiveness
Cost is always a consideration when selecting components for electronic devices. Thermal pads are often more cost-effective than thermal pastes, especially for applications with larger surface areas or higher volume production. They also offer a longer shelf life and do not require specialized dispensing equipment, further reducing overall costs.
Thermal pastes, particularly high-performance, silver-based compounds, can be more expensive than thermal pads. However, their superior thermal conductivity may justify the added cost in applications where maximum heat dissipation is critical. Additionally, the precise dispensing and application of thermal paste can add to the overall manufacturing costs.
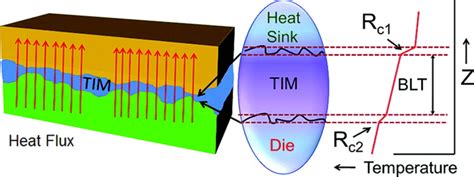
When to Use Thermal Pads
Thermal pads are the preferred choice in the following scenarios:
-
Applications with larger gaps or surface irregularities: Thermal pads can effectively fill gaps between the heat source and heat sink, making them suitable for applications where the mating surfaces are not perfectly flat or where there is a significant height difference between components.
-
Electrical isolation is required: Most thermal pads are electrically insulating, making them ideal for applications where electrical conductivity between components is not desired.
-
Ease of assembly and maintenance is a priority: Thermal pads offer a simple, clean, and user-friendly solution, as they can be easily cut to size and placed between the heat source and heat sink without any preparation or curing time.
-
Cost-sensitive applications: Thermal pads are often more cost-effective than thermal pastes, especially for applications with larger surface areas or higher volume production.
-
Long-term durability is essential: Thermal pads are generally more durable and stable over time, as they are solid materials that do not degrade or pump out under normal operating conditions.
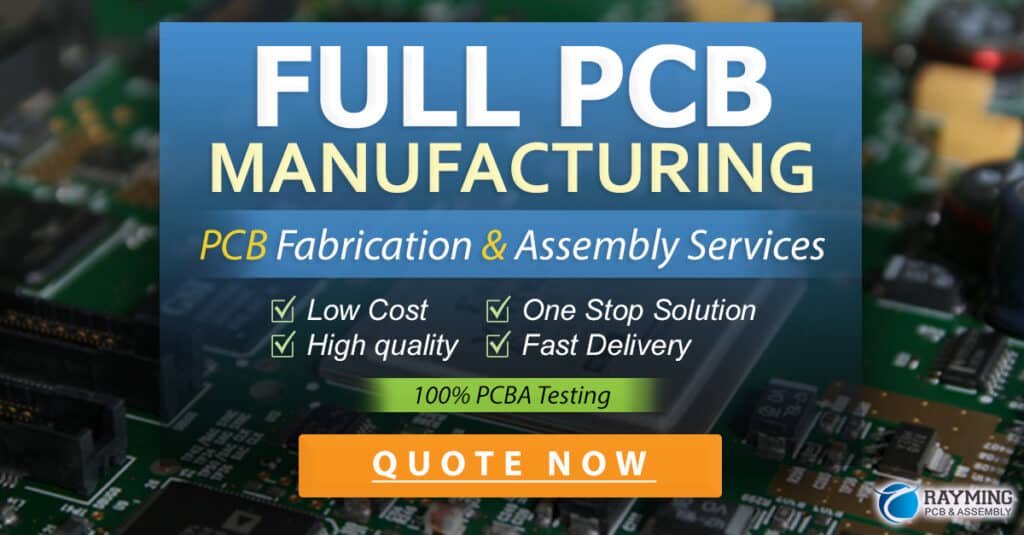
When to Use Thermal Paste
Thermal paste is the preferred choice in the following scenarios:
-
High-performance applications: Thermal pastes, especially high-end, silver-based compounds, offer superior thermal conductivity compared to thermal pads, making them the preferred choice for applications that require the highest level of heat dissipation performance.
-
Filling microscopic air gaps: Thermal paste excels at filling small irregularities and creating a thin, uniform layer between surfaces, ensuring optimal heat transfer.
-
Applications with limited space: Thermal paste can be applied in a very thin layer, making it suitable for applications with limited clearance between the heat source and heat sink.
-
Customizable thermal performance: The thermal conductivity of thermal paste can be tailored by adjusting the type and concentration of fillers used, allowing for customization based on specific application requirements.
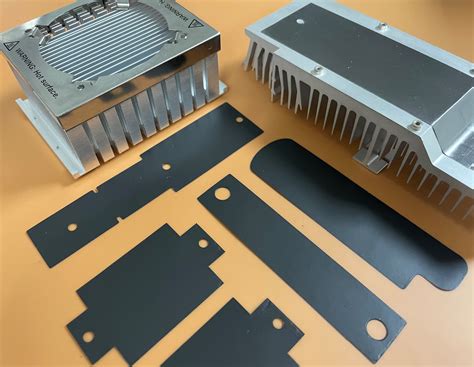
Frequently Asked Questions (FAQ)
-
Can I use both thermal pads and paste together?
Yes, in some cases, using a combination of thermal pad and paste can provide the benefits of both materials. For example, a thermal pad can be used to fill larger gaps and provide electrical isolation, while a thin layer of thermal paste can be applied between the pad and the mating surfaces to improve thermal conductivity. -
How often should I replace thermal pads or paste?
The replacement interval for thermal pads and paste depends on several factors, such as the operating temperature, environmental conditions, and the specific material used. As a general rule, thermal pads have a longer lifespan and may not require replacement unless they become physically damaged or contaminated. Thermal paste, on the other hand, may need to be replaced more frequently, especially if it begins to dry out, harden, or lose its thermal conductivity. It is recommended to consult the manufacturer’s guidelines and monitor the performance of the thermal solution regularly. -
Can I use thermal pads or paste on non-flat surfaces?
Thermal pads are better suited for non-flat surfaces, as they can conform to surface irregularities and fill gaps more effectively than thermal paste. However, for optimal performance, it is always best to ensure that the mating surfaces are as flat and smooth as possible, regardless of the TIM used. -
How do I choose the right thickness for a thermal pad?
The appropriate thickness of a thermal pad depends on the specific application and the gap size between the heat source and heat sink. It is essential to choose a thickness that allows the pad to make proper contact with both surfaces without being excessively compressed or leaving air gaps. Manufacturers often provide guidelines for selecting the appropriate thickness based on the application requirements. -
Can I reuse thermal pads or paste?
It is generally not recommended to reuse thermal pads or paste. Thermal pads may become deformed or contaminated over time, reducing their effectiveness. Thermal paste, once applied and exposed to heat and pressure, may lose its original consistency and thermal conductivity. For optimal performance and reliability, it is best to use fresh thermal pads or paste whenever reassembling or replacing components.
Conclusion
Selecting the appropriate thermal interface material is crucial for effective PCB thermal management. Thermal pads and thermal paste each have their own unique properties, advantages, and disadvantages, making it essential to consider factors such as thermal conductivity, ease of application, gap filling capability, electrical conductivity, durability, and cost when choosing between them.
Thermal pads are the preferred choice for applications with larger gaps, electrical isolation requirements, ease of assembly, cost-sensitivity, and long-term durability. Thermal paste, on the other hand, excels in high-performance applications, filling microscopic air gaps, limited space scenarios, and customizable thermal performance.
By understanding the specific requirements of your application and the properties of each TIM, you can make an informed decision to ensure optimal heat dissipation, performance, and reliability in your electronic devices.
No responses yet