Understanding PCB Copper Thickness Units
PCB copper thickness is typically measured in ounces per square foot (oz/ft²) or microns (µm). One ounce per square foot equals 1.37 mils or 34.79 microns in thickness.
Unit | Abbreviation | Conversion |
---|---|---|
Ounce | oz | 1 oz/ft² = 1.37 mils = 34.79 µm |
Mil | mil | 1 mil = 0.001 inch = 25.4 µm |
Micron | µm | 1 µm = 0.0393 mil |
The most common PCB copper thicknesses are:
- 0.5 oz/ft² (17.5 µm)
- 1 oz/ft² (35 µm)
- 2 oz/ft² (70 µm)
- 3 oz/ft² (105 µm)
- 4 oz/ft² (140 µm)
Factors Influencing PCB Copper Thickness Selection
When choosing the appropriate PCB copper thickness, consider the following factors:
Current Carrying Capacity
The primary factor in determining copper thickness is the current carrying capacity of the traces. Thicker copper can handle higher currents without excessive heating or voltage drop. To calculate the minimum copper thickness required for a given current, use the following formula:
I = kΔT^0.44 A^0.725 (w/h)
Where:
– I = maximum current in amps
– ΔT = temperature rise above ambient in °C
– A = cross-sectional area of the trace in mils²
– w = trace width in mils
– h = copper thickness in oz/ft²
– k = 0.048 for outer layers, 0.024 for inner layers
Voltage Drop
Voltage drop across a trace is another consideration when selecting copper thickness. Thicker copper results in lower resistance and less voltage drop. The voltage drop can be calculated using Ohm’s law:
V = IR
Where:
– V = voltage drop
– I = current
– R = trace resistance
The trace resistance depends on the copper thickness, trace length, and trace width. It can be calculated using the following formula:
R = ρL / (wh)
Where:
– R = resistance in ohms
– ρ = resistivity of copper (1.72 × 10⁻⁸ Ω·m at 20°C)
– L = trace length in meters
– w = trace width in meters
– h = copper thickness in meters
High-Frequency Performance
For high-frequency applications, such as RF and microwave circuits, the skin effect must be considered. The skin effect causes high-frequency currents to flow primarily on the surface of the conductor, effectively reducing the cross-sectional area and increasing resistance. To minimize the skin effect, use thicker copper or multiple copper layers.
The skin depth (δ) can be calculated using the following formula:
δ = √(ρ / (πfμ))
Where:
– δ = skin depth in meters
– ρ = resistivity of copper (1.72 × 10⁻⁸ Ω·m at 20°C)
– f = frequency in Hz
– μ = permeability of copper (1.256 × 10⁻⁶ H/m)
Mechanical Durability
Thicker copper layers provide better mechanical durability and resistance to damage during handling and assembly. For applications that require enhanced durability, such as aerospace or military systems, consider using 2 oz/ft² or thicker copper.
Manufacturing Cost
Thicker copper layers generally increase the manufacturing cost of a PCB due to the additional material and processing required. However, this cost increase may be offset by improved performance and reliability in demanding applications.
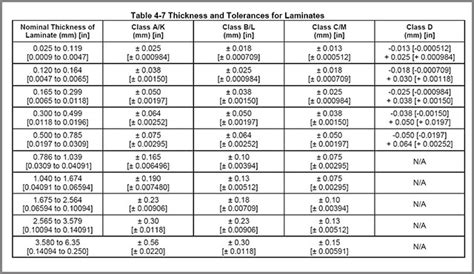
Copper Thickness Guidelines for Different Applications
Consumer Electronics
For most consumer electronics applications, 1 oz/ft² copper is sufficient. This thickness provides a good balance between current carrying capacity, manufacturing cost, and ease of etching fine traces.
Power Electronics
Power electronics applications, such as switching power supplies and motor drives, often require thicker copper to handle high currents. Use 2 oz/ft² or thicker copper for power traces and ground planes. For extremely high-current applications, consider using 4 oz/ft² or even 6 oz/ft² copper.
RF and Microwave
RF and microwave circuits typically use 0.5 oz/ft² to 1 oz/ft² copper for signal traces to minimize skin effect losses. Thicker copper, such as 2 oz/ft², may be used for power traces and ground planes to improve heat dissipation and mechanical stability.
Automotive and Industrial
Automotive and industrial applications often require robust PCBs that can withstand harsh environments and temperature extremes. Use 2 oz/ft² or thicker copper for improved mechanical durability and thermal performance. For high-current applications, consider 3 oz/ft² or 4 oz/ft² copper.
Aerospace and Military
Aerospace and military applications demand the highest levels of reliability and durability. Use 2 oz/ft² or thicker copper for enhanced mechanical strength and resistance to vibration and shock. For high-current applications, 4 oz/ft² or even 6 oz/ft² copper may be necessary.
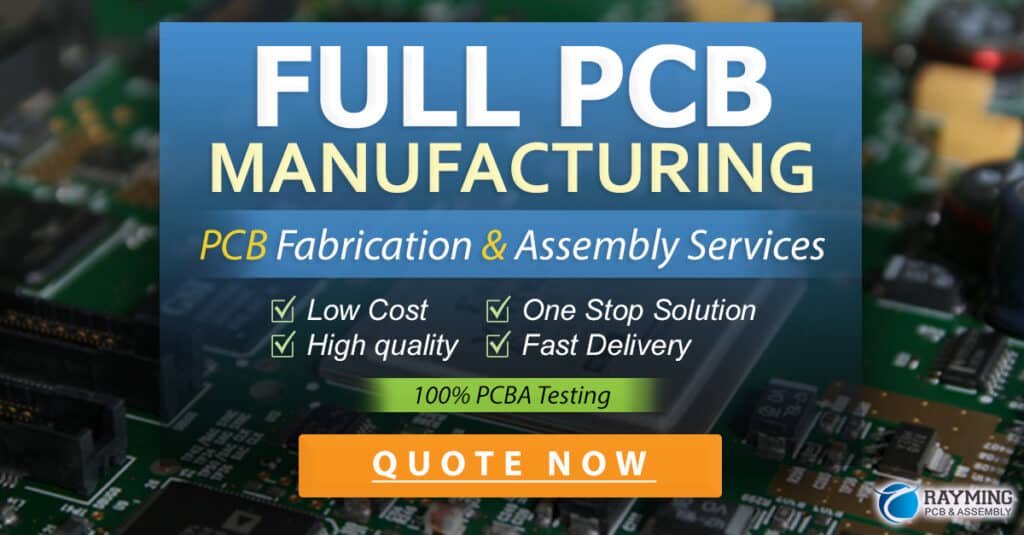
Mixed Copper Weights
In some cases, it may be advantageous to use different copper thicknesses on the same PCB. This technique, known as mixed copper weights, allows you to optimize the copper thickness for each part of the circuit based on its specific requirements.
For example, you might use 1 oz/ft² copper for signal traces and 2 oz/ft² or thicker copper for power traces and ground planes. This approach can help you achieve the desired electrical and thermal performance while minimizing manufacturing costs.
When using mixed copper weights, be sure to communicate your requirements clearly to your PCB manufacturer and follow their design guidelines to ensure manufacturability.
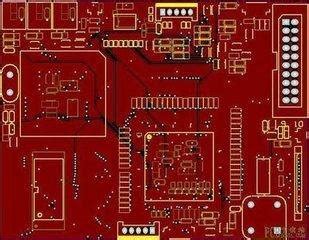
FAQ
What is the most common PCB copper thickness?
The most common PCB copper thickness is 1 oz/ft² (35 µm). This thickness provides a good balance between current carrying capacity, manufacturability, and cost for most applications.
Can I use different copper thicknesses on the same PCB?
Yes, you can use different copper thicknesses on the same PCB. This technique, known as mixed copper weights, allows you to optimize the copper thickness for each part of the circuit based on its specific requirements. However, be sure to consult with your PCB manufacturer to ensure manufacturability.
What copper thickness should I use for high-current applications?
For high-current applications, such as power electronics or automotive systems, use 2 oz/ft² or thicker copper. In extreme cases, 4 oz/ft² or even 6 oz/ft² copper may be necessary. Thicker copper helps to reduce voltage drop, improve heat dissipation, and enhance mechanical durability.
How does copper thickness affect the cost of a PCB?
Thicker copper layers generally increase the manufacturing cost of a PCB due to the additional material and processing required. However, this cost increase may be offset by improved performance and reliability in demanding applications. Consult with your PCB manufacturer to find the most cost-effective solution for your project.
What is the skin effect, and how does it relate to copper thickness?
The skin effect is a phenomenon that causes high-frequency currents to flow primarily on the surface of a conductor, effectively reducing the cross-sectional area and increasing resistance. To minimize the skin effect, use thicker copper or multiple copper layers. The skin depth, which determines the effective conducting thickness, decreases with increasing frequency.
Conclusion
Selecting the appropriate PCB copper thickness is crucial for achieving the desired electrical performance, mechanical durability, and manufacturing cost of your PCB. By considering factors such as current carrying capacity, voltage drop, high-frequency performance, and application requirements, you can make an informed decision on the optimal copper thickness for your project.
Remember to consult with your PCB manufacturer early in the design process to ensure that your chosen copper thickness is compatible with their manufacturing capabilities and design guidelines. With careful planning and attention to detail, you can create a high-quality, reliable PCB that meets the specific needs of your application.
No responses yet