Introduction to CAD: ECAD vs MCAD
Computer-Aided Design (CAD) is a broad term that encompasses various software tools used to design, analyze, and optimize products in different industries. CAD software allows engineers and designers to create precise 2D drawings and 3D models, simulate product performance, and generate manufacturing-ready data. Two main categories of CAD software are Electronic Computer-Aided Design (ECAD) and Mechanical Computer-Aided Design (MCAD). While both ECAD and MCAD are used for designing products, they serve different purposes and have distinct features tailored to their respective domains.
What is ECAD?
ECAD, or Electronic Computer-Aided Design, is a specialized branch of CAD software used for designing electronic systems, such as printed circuit boards (PCBs), integrated circuits (ICs), and electronic schematics. ECAD tools help electronics engineers design, simulate, and analyze electronic components and systems before manufacturing them. Some of the key features of ECAD software include:
- Schematic capture: Creating electronic schematics that represent the logical connections between components in a circuit.
- PCB layout: Designing the physical layout of electronic components on a printed circuit board, including component placement, routing, and layer stackup.
- Circuit simulation: Simulating the behavior of electronic circuits to verify their functionality and performance.
- Design rule checking (DRC): Verifying that the PCB layout adheres to manufacturing constraints and design rules to ensure manufacturability.
What is MCAD?
MCAD, or Mechanical Computer-Aided Design, is a branch of CAD software used for designing mechanical parts, assemblies, and systems. MCAD tools help mechanical engineers and designers create 3D models, perform structural analysis, and generate manufacturing-ready data for various mechanical components and products. Some of the key features of MCAD software include:
- 3D modeling: Creating precise 3D models of mechanical parts and assemblies using solid modeling, surface modeling, or parametric modeling techniques.
- Assembly design: Defining the relationships between parts in an assembly, including constraints, mates, and motion studies.
- Finite Element Analysis (FEA): Performing structural analysis on 3D models to evaluate stress, strain, and deformation under various loading conditions.
- Computer-Aided Manufacturing (CAM): Generating toolpaths and machine instructions for manufacturing processes like milling, turning, and 3D printing.
Key Differences Between ECAD and MCAD
While both ECAD and MCAD are used for designing products, they have several key differences that set them apart. Here are some of the main distinctions between ECAD and MCAD:
Design Domain
The primary difference between ECAD and MCAD lies in their design domains. ECAD is used for designing electronic systems, while MCAD is used for designing mechanical parts and assemblies. This difference in design domain leads to different tools, workflows, and considerations in the design process.
Design Domain | ECAD | MCAD |
---|---|---|
Focus | Electronic systems | Mechanical parts and assemblies |
Examples | PCBs, ICs, electronic schematics | Gears, housings, mechanical systems |
Design Elements
ECAD and MCAD deal with different design elements due to their respective domains. ECAD focuses on electronic components, such as resistors, capacitors, and integrated circuits, as well as their interconnections and routing on a PCB. MCAD, on the other hand, deals with geometric shapes, materials, and mechanical features like holes, slots, and fillets.
Design Elements | ECAD | MCAD |
---|---|---|
Components | Resistors, capacitors, ICs | Bolts, nuts, gears |
Connections | Electrical traces, vias | Mechanical interfaces, fits |
Features | Pads, holes, silkscreen | Holes, slots, fillets |
Design Workflow
The design workflows in ECAD and MCAD differ due to the nature of their design domains. In ECAD, the design workflow typically starts with creating a schematic that represents the logical connections between electronic components. The schematic is then used to create a PCB layout, where the physical placement and routing of components are defined. In MCAD, the design workflow usually begins with creating 3D models of individual parts, which are then assembled into a complete product. The 3D models are used for various analyses, such as stress and motion studies, to optimize the design.
Design Workflow | ECAD | MCAD |
---|---|---|
Initial Stage | Schematic capture | 3D modeling |
Intermediate Stage | PCB layout | Assembly design |
Analysis | Circuit simulation, DRC | FEA, motion studies |
Data Exchange Formats
ECAD and MCAD use different data exchange formats to share design data with other software tools and manufacturing processes. In ECAD, common data exchange formats include Gerber files for PCB manufacturing, ODB++ for PCB design data exchange, and STEP for 3D models of electronic components. In MCAD, popular data exchange formats include STEP, IGES, and Parasolid for 3D model exchange, as well as DXF and DWG for 2D drawings.
Data Exchange Formats | ECAD | MCAD |
---|---|---|
Manufacturing Data | Gerber, ODB++ | STEP, IGES |
3D Model Exchange | STEP | STEP, Parasolid |
2D Drawing Exchange | – | DXF, DWG |
Integration and Collaboration
Despite their differences, ECAD and MCAD often need to work together in the product development process, especially for products that have both electronic and mechanical components. Many CAD software vendors offer tools and workflows that enable the integration and collaboration between ECAD and MCAD. Some examples include:
- ECAD-MCAD co-design: Allows electronic and mechanical designers to work concurrently on the same product, sharing design data and ensuring compatibility between electronic and mechanical components.
- 3D component libraries: Provide accurate 3D models of electronic components that can be used in MCAD for mechanical enclosure design and interference checks.
- Design data synchronization: Ensures that changes made in one domain (ECAD or MCAD) are automatically propagated to the other domain, maintaining design consistency and reducing errors.
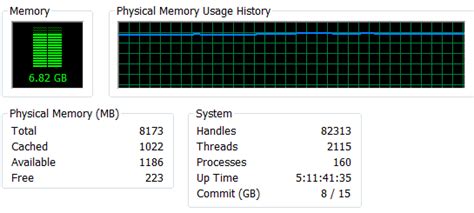
ECAD Software
There are several popular ECAD software packages used in the electronics industry for designing and simulating electronic systems. Some of the most widely used ECAD software include:
Altium Designer
Altium Designer is a comprehensive ECAD software that offers schematic capture, PCB layout, and 3D modeling capabilities. It is known for its user-friendly interface, extensive component libraries, and powerful design rule checking features. Altium Designer also provides tools for ECAD-MCAD co-design, allowing seamless collaboration between electronic and mechanical designers.
Cadence OrCAD
Cadence OrCAD is another popular ECAD software suite that includes tools for schematic capture, PCB layout, and circuit simulation. OrCAD offers a modular approach, allowing users to choose the tools they need based on their design requirements. It also provides integration with Cadence’s PCB manufacturing tools, enabling a seamless transition from design to production.
Mentor Graphics PADS
Mentor Graphics PADS is an ECAD software package that focuses on PCB design and layout. It offers a streamlined design workflow, with tools for schematic capture, constraint management, and design rule checking. PADS also provides integration with Mentor’s thermal analysis and signal integrity tools, allowing designers to optimize their PCB designs for performance and reliability.
KiCad
KiCad is a free and open-source ECAD software suite that includes tools for schematic capture, PCB layout, and 3D modeling. Despite being open-source, KiCad offers a robust set of features and has gained popularity among hobbyists, students, and small businesses. It supports a wide range of file formats and provides a scripting interface for automation and customization.
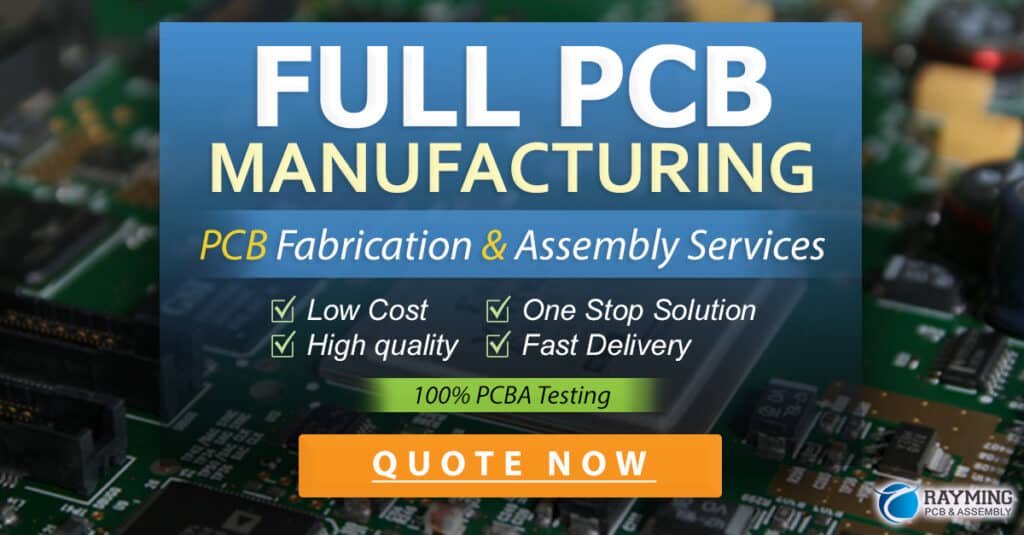
MCAD Software
There are numerous MCAD software packages available for designing and analyzing mechanical parts and assemblies. Some of the most popular MCAD software include:
SolidWorks
SolidWorks is a widely used MCAD software that offers a comprehensive set of tools for 3D modeling, assembly design, and engineering analysis. It is known for its intuitive user interface, extensive part libraries, and powerful simulation capabilities. SolidWorks also provides integration with ECAD software, enabling ECAD-MCAD co-design and collaboration.
Autodesk Inventor
Autodesk Inventor is another popular MCAD software that offers a complete set of tools for mechanical design, simulation, and visualization. It provides a parametric modeling environment, allowing designers to create complex parts and assemblies with ease. Inventor also offers advanced simulation tools, such as dynamic motion analysis and stress analysis, to optimize designs for performance and durability.
Siemens NX
Siemens NX is a high-end MCAD software that offers a comprehensive set of tools for product design, engineering, and manufacturing. It provides advanced modeling capabilities, such as synchronous technology and subdivision modeling, as well as integrated CAM tools for manufacturing. NX also offers seamless integration with other Siemens software, such as Teamcenter for product lifecycle management (PLM) and Simcenter for simulation and testing.
PTC Creo
PTC Creo is a scalable MCAD software suite that offers a range of tools for 3D modeling, simulation, and manufacturing. It provides a flexible modeling environment, with tools for parametric modeling, direct editing, and freestyle design. Creo also offers advanced simulation capabilities, such as topology optimization and computational fluid dynamics (CFD), to help designers create optimized and high-performance products.
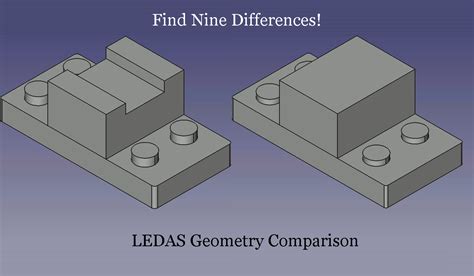
Frequently Asked Questions (FAQ)
-
Q: Can ECAD software be used for designing mechanical parts?
A: While ECAD software is primarily used for designing electronic systems, some ECAD tools offer limited 3D modeling capabilities for creating simple mechanical enclosures or visualizing electronic components in 3D. However, for complex mechanical design tasks, MCAD software is more suitable. -
Q: Is it possible to import ECAD designs into MCAD software?
A: Yes, many MCAD software packages offer tools for importing ECAD designs, such as PCB layouts, into the mechanical design environment. This allows mechanical designers to create enclosures and housings that accurately fit the electronic components and ensure proper clearances and mounting points. -
Q: What are the benefits of ECAD-MCAD co-design?
A: ECAD-MCAD co-design enables electronic and mechanical designers to work concurrently on the same product, sharing design data and ensuring compatibility between electronic and mechanical components. This approach helps reduce design errors, accelerate the product development process, and ultimately leads to better-integrated and optimized products. -
Q: Are there any open-source MCAD software alternatives?
A: Yes, there are several open-source MCAD software packages available, such as FreeCAD, OpenSCAD, and LibreCAD. While these tools may not offer the same level of features and functionality as commercial MCAD software, they can be suitable for simple mechanical design tasks or for users on a tight budget. -
Q: How do I choose the right ECAD or MCAD software for my project?
A: When choosing ECAD or MCAD software, consider factors such as the complexity of your design tasks, the size of your team, your budget, and the compatibility with other software tools and manufacturing processes. It’s also a good idea to evaluate the learning curve, user support, and community resources available for each software package. Many CAD software vendors offer free trials or educational licenses, which can help you assess the suitability of a particular tool for your project.
Conclusion
ECAD and MCAD are two essential branches of CAD software that play crucial roles in the product development process. While ECAD focuses on designing electronic systems, MCAD is used for designing mechanical parts and assemblies. Understanding the differences between ECAD and MCAD, as well as their respective software tools and design workflows, is crucial for engineers and designers working on projects that involve both electronic and mechanical components.
As the demand for smart, connected, and high-performance products continues to grow, the need for seamless integration and collaboration between ECAD and MCAD becomes increasingly important. By leveraging the strengths of both domains and utilizing the latest CAD technologies, engineers and designers can create innovative, reliable, and manufacturable products that meet the evolving needs of the market.
No responses yet