Understanding the Differences Between Vibration and Electric Shock on PCBs
Printed Circuit Boards (PCBs) are essential components in modern electronic devices, from smartphones and laptops to industrial equipment and aerospace systems. These boards are subjected to various environmental factors that can impact their performance and longevity. Two of the most significant factors are vibration and electric shock. In this article, we will explore the differences between vibration and electric shock, their effects on PCBs, and how to protect your PCBs from these factors.
What is Vibration?
Vibration is a mechanical phenomenon that occurs when an object oscillates or moves back and forth around its equilibrium position. In the context of PCBs, vibration can be caused by various sources, such as:
- Motors and fans
- Transportation (e.g., vehicles, aircraft)
- Mechanical shocks (e.g., drops, impacts)
Vibration can cause several issues for PCBs, including:
- Component damage or failure
- Solder joint cracking or fatigue
- Connector and cable problems
- Intermittent electrical connections
Types of Vibration
There are two main types of vibration that can affect PCBs:
-
Sinusoidal Vibration: This type of vibration is characterized by a smooth, repetitive motion with a specific frequency and amplitude. Sinusoidal vibration is often encountered in rotating machinery, such as motors and fans.
-
Random Vibration: Random vibration is characterized by a complex, non-repetitive motion that contains a wide range of frequencies and amplitudes. Random vibration is typically encountered in transportation applications, such as vehicles and aircraft.
Measuring Vibration
Vibration is typically measured using accelerometers, which are sensors that convert mechanical motion into electrical signals. The output of an accelerometer is usually expressed in terms of acceleration (g) or velocity (m/s). The following table shows some common vibration measurement units:
Unit | Description |
---|---|
g | Acceleration due to gravity (1 g = 9.81 m/s²) |
m/s² | Acceleration in meters per second squared |
mm/s | Velocity in millimeters per second |
μm | Displacement in micrometers |
Vibration Testing Standards
Several international standards have been developed to guide the testing and qualification of electronic equipment under vibration conditions. Some of the most widely used standards include:
- IEC 60068-2-6: Environmental testing – Part 2-6: Tests – Test Fc: Vibration (sinusoidal)
- IEC 60068-2-64: Environmental testing – Part 2-64: Tests – Test Fh: Vibration, broadband random and guidance
- MIL-STD-810: Environmental Engineering Considerations and Laboratory Tests (U.S. Department of Defense)
These standards provide detailed requirements for vibration testing, including test levels, durations, and methods.
Understanding Electric Shock
What is Electric Shock?
Electric shock, in the context of PCBs, refers to the sudden discharge of static electricity or the exposure of the board to high-voltage transients. These events can cause damage to the PCB and its components, leading to malfunction or complete failure.
Causes of Electric Shock
There are several common causes of electric shock in PCBs:
-
Electrostatic Discharge (ESD): ESD occurs when a charged object comes into contact with the PCB, causing a rapid transfer of charge. This can happen during handling, assembly, or even in the final application.
-
Electrical Overstress (EOS): EOS occurs when the PCB is exposed to a voltage or current that exceeds its designed limits. This can be caused by power surges, lightning strikes, or faulty power supplies.
-
Electromagnetic Interference (EMI): EMI can induce high-voltage transients in the PCB’s traces or components, leading to damage or malfunction.
Effects of Electric Shock on PCBs
Electric shock can have several detrimental effects on PCBs, including:
- Component damage or failure
- Dielectric breakdown of insulating materials
- Thermal damage due to high currents
- Latent defects that may cause premature failure
Protecting PCBs from Electric Shock
There are several strategies for protecting PCBs from electric shock:
-
ESD Protection: Use ESD-safe handling procedures, grounding straps, and ESD-safe packaging materials to minimize the risk of ESD damage during assembly and handling.
-
Surge Protection: Incorporate surge protection devices (SPDs), such as transient voltage suppressors (TVS), varistors, or gas discharge tubes (GDTs), to clamp high-voltage transients and protect sensitive components.
-
EMI Shielding: Use EMI shielding techniques, such as grounded enclosures, shielded cables, and filtering, to reduce the coupling of electromagnetic interference into the PCB.
-
Design for Robustness: Design the PCB with adequate clearances, creepage distances, and insulation to withstand the expected levels of electrical stress in the application.
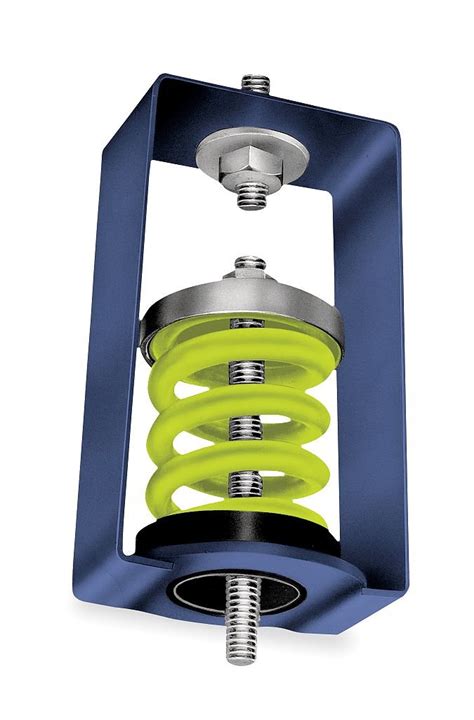
Comparing Vibration and Electric Shock
While both vibration and electric shock can cause damage to PCBs, they have distinct characteristics and require different mitigation strategies. The following table summarizes the key differences between vibration and electric shock:
Factor | Vibration | Electric Shock |
---|---|---|
Nature | Mechanical | Electrical |
Cause | Oscillatory motion | Sudden discharge or high-voltage transient |
Effects | Component damage, solder joint failure, intermittent connections | Component damage, dielectric breakdown, thermal damage, latent defects |
Mitigation | Vibration isolation, damping, robust mechanical design | ESD protection, surge protection, EMI shielding, robust electrical design |
Testing Standards | IEC 60068-2-6, IEC 60068-2-64, MIL-STD-810 | IEC 61000-4-2 (ESD), IEC 61000-4-5 (Surge), IEC 61000-4-4 (EFT) |
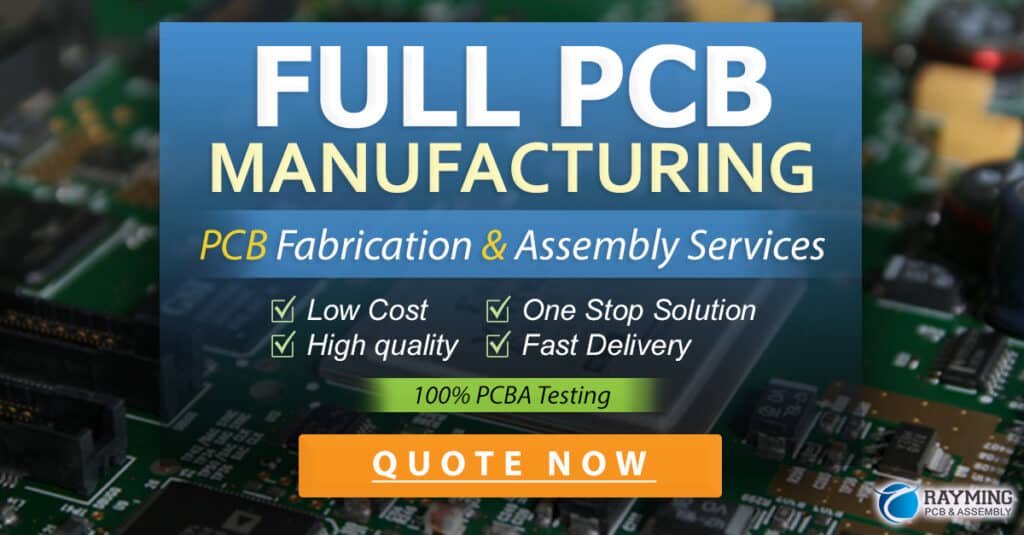
Protecting Your PCB from Vibration and Electric Shock
To ensure the reliability and longevity of your PCB, it is essential to implement a comprehensive protection strategy that addresses both vibration and electric shock. Here are some key steps to follow:
-
Understand the Environment: Identify the expected levels of vibration and electric shock in the intended application. This will help you select appropriate components and design techniques.
-
Design for Robustness: Incorporate vibration isolation, damping, and robust mechanical design to withstand the expected vibration levels. Use adequate clearances, creepage distances, and insulation to protect against electric shock.
-
Select Suitable Components: Choose components that are rated for the expected vibration and shock levels. Pay attention to component packaging, lead configurations, and mounting techniques.
-
Implement Protection Measures: Incorporate ESD protection, surge protection, and EMI shielding to mitigate the risk of electric shock damage.
-
Test and Qualify: Perform vibration and electric shock testing per the relevant standards to validate the PCB’s performance and reliability. Use accelerated life testing to identify potential weaknesses and improve the design.
By following these steps, you can significantly enhance the resilience of your PCB against vibration and electric shock, ensuring reliable operation in demanding environments.
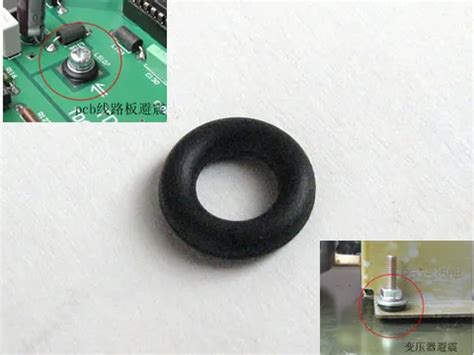
Frequently Asked Questions (FAQ)
- What is the difference between vibration and electric shock?
-
Vibration is a mechanical phenomenon caused by oscillatory motion, while electric shock is an electrical phenomenon caused by sudden discharges or high-voltage transients.
-
How can vibration damage a PCB?
-
Vibration can cause component damage, solder joint failure, and intermittent connections, leading to malfunction or complete failure of the PCB.
-
What are some common causes of electric shock in PCBs?
-
Common causes of electric shock in PCBs include electrostatic discharge (ESD), electrical overstress (EOS), and electromagnetic interference (EMI).
-
How can I protect my PCB from vibration?
-
To protect your PCB from vibration, use vibration isolation, damping, and robust mechanical design. Select components rated for the expected vibration levels and perform vibration testing to validate the design.
-
What are some strategies for protecting PCBs from electric shock?
- To protect PCBs from electric shock, implement ESD protection measures, incorporate surge protection devices, use EMI shielding techniques, and design for electrical robustness. Perform electric shock testing per the relevant standards to ensure the PCB’s reliability.
In conclusion, understanding the differences between vibration and electric shock, their effects on PCBs, and the appropriate protection strategies is crucial for designing reliable and long-lasting electronic devices. By following the guidelines outlined in this article and staying informed about the latest industry standards and best practices, you can ensure that your PCBs are well-equipped to withstand the challenges of vibration and electric shock in their intended applications.
No responses yet