Introduction to PCB Transmission Lines
Printed Circuit Boards (PCBs) are the backbone of modern electronics, providing a platform for interconnecting various components and enabling the flow of electrical signals. As the demand for high-speed and high-frequency applications continues to grow, the design of PCB transmission lines becomes increasingly critical. Transmission lines are specialized PCB tracks that are designed to carry high-speed signals while minimizing signal distortion, reflections, and crosstalk.
In this article, we will delve into the world of PCB transmission lines, exploring their fundamental concepts, design considerations, and best practices. Whether you are a seasoned PCB designer or a curious enthusiast, understanding the principles of transmission line design is essential for creating reliable and high-performance electronic systems.
Understanding the Basics of Transmission Lines
What is a Transmission Line?
A transmission line is a specialized electrical conductor designed to carry high-frequency signals with minimal loss and distortion. Unlike regular PCB tracks, which are treated as simple connections, transmission lines take into account the electromagnetic properties of the signal and the surrounding medium.
When an electrical signal propagates along a transmission line, it behaves as an electromagnetic wave, exhibiting characteristics such as impedance, velocity, and wavelength. The goal of transmission line design is to ensure that the signal maintains its integrity as it travels from the source to the destination.
Types of Transmission Lines
There are several types of transmission lines commonly used in PCB design, each with its own characteristics and applications. The most common types include:
-
Microstrip: A microstrip is a transmission line consisting of a conductive strip separated from a ground plane by a dielectric substrate. It is the most widely used transmission line in PCB design due to its simplicity and ease of fabrication.
-
Stripline: A stripline is a transmission line sandwiched between two ground planes, with a dielectric substrate on either side. Striplines offer better shielding and reduced crosstalk compared to microstrips but require more complex fabrication.
-
Coplanar Waveguide (CPW): A coplanar waveguide consists of a conductive strip with ground planes on either side, all on the same layer. CPWs provide low dispersion and are suitable for high-frequency applications.
-
Grounded Coplanar Waveguide (GCPW): A grounded coplanar waveguide is similar to a CPW but includes an additional ground plane on the opposite side of the substrate. GCPWs offer better shielding and reduced radiation compared to CPWs.
Key Parameters of Transmission Lines
To effectively design and analyze transmission lines, it is essential to understand the key parameters that characterize their behavior. These parameters include:
-
Characteristic Impedance (Z0): The characteristic impedance is the ratio of the voltage to the current in a transmission line. It determines the impedance that the transmission line presents to the source and load. Matching the characteristic impedance to the source and load impedances is crucial for minimizing reflections and ensuring efficient power transfer.
-
Propagation Velocity (vp): The propagation velocity is the speed at which the signal travels along the transmission line. It is determined by the dielectric constant of the substrate material and affects the wavelength of the signal at a given frequency.
-
Dielectric Constant (εr): The dielectric constant is a measure of the ability of the substrate material to store electrical energy. It influences the characteristic impedance and propagation velocity of the transmission line.
-
Conductor Thickness (t): The thickness of the conductive strip affects the resistance and current-carrying capacity of the transmission line. Thicker conductors have lower resistance and can handle higher currents.
-
Substrate Thickness (h): The thickness of the dielectric substrate influences the characteristic impedance and the coupling between adjacent transmission lines. Thicker substrates generally result in higher characteristic impedance and reduced coupling.
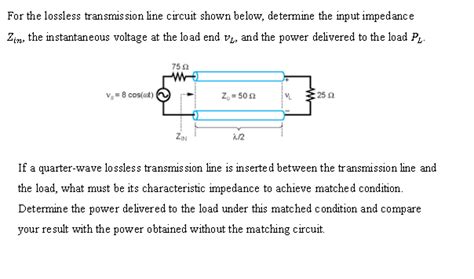
Designing PCB Transmission Lines
Impedance Matching
One of the primary goals of transmission line design is to ensure proper impedance matching between the source, the transmission line, and the load. When the impedances are matched, the signal can propagate without reflections, minimizing signal distortion and power loss.
To achieve impedance matching, the characteristic impedance of the transmission line (Z0) should be equal to the source impedance (ZS) and the load impedance (ZL). This can be expressed as:
Z0 = ZS = ZL
Common impedance values used in PCB design include 50 ohms for RF and high-speed digital applications, and 75 ohms for video and cable applications.
Calculating Characteristic Impedance
To design a transmission line with a specific characteristic impedance, you need to consider the geometric and material properties of the PCB. The characteristic impedance depends on the width of the conductive strip (w), the thickness of the substrate (h), the dielectric constant of the substrate (εr), and the thickness of the conductor (t).
For a microstrip transmission line, the characteristic impedance can be approximated using the following formula:
Z0 = (87 / √(εr + 1.41)) * ln(5.98 * h / (0.8 * w + t))
For a stripline transmission line, the characteristic impedance can be approximated using:
Z0 = (60 / √εr) * ln(4 * h / (0.67 * π * (0.8 * w + t)))
These formulas provide a starting point for designing transmission lines, but more accurate calculations can be performed using specialized PCB design software or electromagnetic simulation tools.
Routing Considerations
When routing transmission lines on a PCB, there are several considerations to keep in mind to ensure signal integrity and minimize interference:
-
Avoid sharp bends: Sharp bends in transmission lines can cause reflections and signal distortion. Use gentle curves or 45-degree angles instead of 90-degree bends.
-
Maintain consistent spacing: Maintain consistent spacing between transmission lines and adjacent traces to minimize crosstalk and coupling. The spacing should be based on the desired characteristic impedance and the PCB stackup.
-
Avoid discontinuities: Minimize discontinuities in the transmission line, such as vias, connectors, and layer transitions. Each discontinuity introduces impedance mismatches and can cause reflections.
-
Use ground planes: Incorporate ground planes adjacent to the transmission lines to provide a stable reference and reduce electromagnetic interference (EMI).
-
Match trace lengths: When routing differential pairs or parallel transmission lines, match the trace lengths to maintain signal synchronization and minimize skew.
-
Consider the substrate material: Choose a substrate material with a suitable dielectric constant and low loss tangent to minimize signal attenuation and dispersion.
Termination Techniques
Proper termination of transmission lines is essential to minimize reflections and ensure signal integrity. There are several termination techniques commonly used in PCB design:
-
Series Termination: A series resistor is placed near the source to match the impedance of the transmission line. This technique is suitable for point-to-point connections and reduces reflections at the load.
-
Parallel Termination: A resistor is placed at the end of the transmission line, in parallel with the load. The value of the resistor is chosen to match the characteristic impedance of the transmission line. Parallel termination absorbs reflections and is commonly used in high-speed digital systems.
-
Thévenin Termination: A combination of series and parallel resistors is used to provide a matched impedance at the load. Thévenin termination offers better signal integrity compared to series or parallel termination alone.
-
AC Termination: Capacitors and resistors are used to provide frequency-dependent termination. AC termination is useful for broadband applications where the impedance varies with frequency.
The choice of termination technique depends on the specific application, signal characteristics, and design constraints.
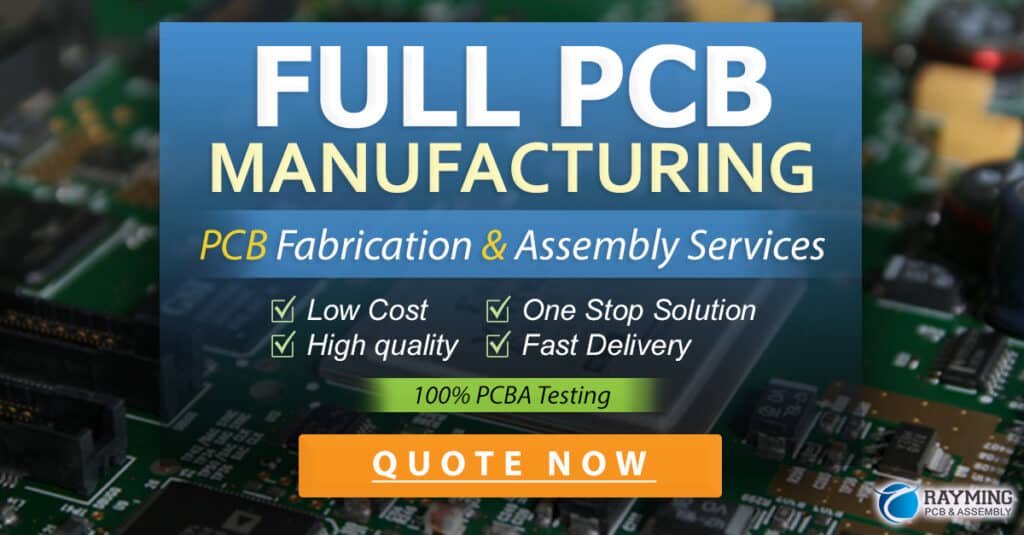
Analyzing Transmission Lines
Time-Domain Analysis
Time-domain analysis is used to examine the behavior of transmission lines in response to transient signals, such as pulses or steps. It helps in understanding signal propagation, reflections, and distortions over time.
One commonly used technique for time-domain analysis is the Time-Domain Reflectometry (TDR). TDR involves sending a fast-rising pulse into the transmission line and measuring the reflected signal. By analyzing the reflected waveform, you can determine the impedance profile along the transmission line and identify discontinuities or mismatches.
To perform TDR analysis, you can use specialized test equipment or simulate the transmission line using circuit simulation software, such as SPICE or ADS.
Frequency-Domain Analysis
Frequency-domain analysis examines the behavior of transmission lines in response to sinusoidal signals of varying frequencies. It helps in understanding the frequency-dependent characteristics of the transmission line, such as attenuation, phase shift, and impedance.
Scattering parameters (S-parameters) are commonly used for frequency-domain analysis of transmission lines. S-parameters describe the relationship between the incident and reflected waves at the ports of a network. They provide information about the transmission and reflection characteristics of the transmission line as a function of frequency.
To measure S-parameters, you can use a Vector Network Analyzer (VNA) or perform electromagnetic simulations using tools like HFSS or CST Studio Suite.
Eye Diagram Analysis
Eye diagram analysis is a technique used to assess the quality of high-speed digital signals transmitted over a transmission line. An eye diagram is a graphical representation of the superimposed waveforms of a digital signal, resembling an eye-like shape.
By analyzing the eye diagram, you can evaluate various signal quality metrics, such as:
- Eye Height: The vertical opening of the eye, indicating the signal amplitude and noise margin.
- Eye Width: The horizontal opening of the eye, indicating the timing margin and jitter tolerance.
- Rise and Fall Times: The slopes of the signal transitions, indicating the speed and sharpness of the edges.
- Jitter: The deviation of the signal transitions from their ideal positions, caused by noise or timing variations.
Eye diagram analysis helps in identifying signal integrity issues, such as intersymbol interference (ISI), crosstalk, and noise. It is commonly performed using high-speed oscilloscopes or specialized signal integrity analysis software.
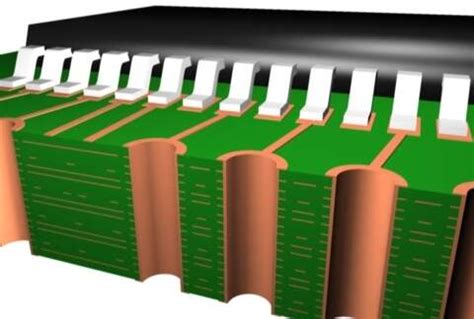
Best Practices for PCB Transmission Line Design
To ensure optimal performance and signal integrity in PCB transmission line design, consider the following best practices:
-
Plan the stackup: Carefully plan the PCB stackup, considering the number of layers, dielectric materials, and thicknesses. Ensure that the stackup provides the desired characteristic impedance and minimizes crosstalk.
-
Use controlled impedance: Specify controlled impedance requirements for critical transmission lines. Work with the PCB manufacturer to ensure that the impedance is within the specified tolerance.
-
Minimize discontinuities: Avoid or minimize discontinuities in the transmission lines, such as vias, stubs, and layer transitions. When unavoidable, use appropriate compensation techniques, such as via stitching or impedance matching.
-
Provide adequate grounding: Incorporate solid ground planes adjacent to the transmission lines to provide a low-impedance return path and reduce EMI. Use multiple vias to connect ground planes across layers.
-
Simulate and optimize: Perform pre-layout simulations to optimize the transmission line design. Use electromagnetic simulation tools to analyze the behavior of the transmission lines and identify potential issues.
-
Validate with measurements: After fabrication, validate the transmission line performance using appropriate measurement techniques, such as TDR, VNA, or eye diagram analysis. Compare the measured results with the simulated or calculated values to ensure compliance.
-
Document and communicate: Clearly document the transmission line requirements, design decisions, and simulation results. Communicate the information to the PCB manufacturer and assembly team to ensure that the design intent is properly implemented.
Frequently Asked Questions (FAQ)
1. What is the difference between a microstrip and a stripline?
A microstrip is a transmission line consisting of a conductive strip separated from a ground plane by a dielectric substrate. It is exposed on one side and is suitable for simpler PCB designs. On the other hand, a stripline is a transmission line sandwiched between two ground planes, with a dielectric substrate on either side. Striplines offer better shielding and reduced crosstalk compared to microstrips but require more complex fabrication.
2. How do I choose the appropriate characteristic impedance for my PCB transmission line?
The choice of characteristic impedance depends on the specific application and the system requirements. Common impedance values include 50 ohms for RF and high-speed digital applications, and 75 ohms for video and cable applications. Consider factors such as the signal frequency, the desired signal integrity, and the compatibility with other components in the system when selecting the characteristic impedance.
3. What is the purpose of termination in transmission line design?
Termination is used to minimize reflections and ensure signal integrity in transmission lines. When a signal reaches the end of a transmission line, if the load impedance does not match the characteristic impedance of the line, a portion of the signal is reflected back towards the source. Termination techniques, such as series, parallel, or Thévenin termination, are employed to match the impedance and absorb the reflections, preventing signal distortion and ringing.
4. How can I minimize crosstalk between adjacent transmission lines?
To minimize crosstalk between adjacent transmission lines, consider the following techniques:
- Increase the spacing between the transmission lines. The greater the separation, the lower the crosstalk.
- Use ground planes between the transmission lines to provide shielding and reduce electromagnetic coupling.
- Route the transmission lines orthogonally to each other to minimize the coupling area.
- Use differential signaling, where the signal is transmitted as a pair of complementary signals, canceling out the electromagnetic fields and reducing crosstalk.
5. What is the role of a Vector Network Analyzer (VNA) in transmission line analysis?
A Vector Network Analyzer (VNA) is a powerful tool used for frequency-domain analysis of transmission lines. It measures the scattering parameters (S-parameters) of the transmission line, providing information about the transmission and reflection characteristics as a function of frequency. A VNA can help in determining the impedance profile, insertion loss, return loss, and phase response of the transmission line, aiding in the design and optimization process.
Conclusion
PCB transmission line design is a critical aspect of modern electronic systems, enabling the efficient and reliable transmission of high-speed signals. By understanding the fundamental concepts, design considerations, and analysis techniques, PCB designers can create robust and high-performance transmission lines.
This article has covered the basics of transmission lines, including their types, key parameters, and design principles. We have explored impedance matching, routing considerations, termination techniques, and analysis methods such as time-domain, frequency-domain, and eye diagram analysis.
To achieve optimal results, it is essential to follow best practices in PCB transmission line design, such as careful stackup planning, controlled impedance, minimizing discontinuities, providing adequate grounding, simulating and optimizing the design, and validating with measurements.
As the demand for high-speed and high-frequency applications continues to grow, the importance of effective transmission line design cannot be overstated. By applying the knowledge and techniques discussed in this article, PCB designers can tackle the challenges of signal integrity and create reliable and high-performance electronic systems.
Remember, the key to successful transmission line design lies in understanding the principles, using appropriate tools and techniques, and continuously refining and optimizing the design based on simulations and measurements. With practice and experience, you can master the art of PCB transmission line design and contribute to the advancement of cutting-edge electronic technologies.
Parameter | Description |
---|---|
Characteristic Impedance (Z0) | The ratio of the voltage to the current in a transmission line. It determines the impedance that the transmission line presents to the source and load. |
Propagation Velocity (vp) | The speed at which the signal travels along the transmission line. It is determined by the dielectric constant of the substrate material. |
Dielectric Constant (εr) | A measure of the ability of the substrate material to store electrical energy. It influences the characteristic impedance and propagation velocity. |
Conductor Thickness (t) | The thickness of the conductive strip, affecting the resistance and current-carrying capacity of the transmission line. |
Substrate Thickness (h) | The thickness of the dielectric substrate, influencing the characteristic impedance and coupling between adjacent transmission lines. |
Transmission Line Type | Description |
---|---|
Microstrip | A transmission line consisting of a conductive strip separated from a ground plane by a dielectric substrate. |
Stripline | A transmission line sandwiched between two ground planes, with a dielectric substrate on either side. |
Coplanar Waveguide (CPW) | A transmission line consisting of a conductive strip with ground planes on either side, all on the same layer. |
Grounded Coplanar Waveguide (GCPW) | Similar to a CPW but includes an additional ground plane on the opposite side of the substrate. |
No responses yet