What is PCB-Driven Design?
PCB-driven design is an approach to electronics product development that places the PCB at the center of the design process. In this methodology, the PCB is not merely a substrate for mounting components but an integral part of the product’s overall functionality and performance. By considering the PCB’s layout, materials, and manufacturing process from the outset, designers can optimize the product’s size, weight, power consumption, and reliability.
The Benefits of PCB-Driven Design
- Improved product performance
- Reduced development time and costs
- Enhanced manufacturability
- Increased reliability and durability
- Smaller form factors and lighter weight
The Role of PCB Designers in Product Development
PCB designers are responsible for translating a product’s schematic diagram into a physical layout that can be manufactured. This process involves a deep understanding of electronics theory, materials science, and manufacturing techniques. In PCB-driven design, the designer’s role is elevated from a mere executor to a key decision-maker in the product development process.
Key Skills for PCB Designers
- Proficiency in PCB design software (e.g., Altium Designer, OrCAD, Eagle)
- Knowledge of electronics theory and component behavior
- Understanding of PCB manufacturing processes and limitations
- Familiarity with industry standards and regulations (e.g., IPC, UL, RoHS)
- Strong problem-solving and communication skills
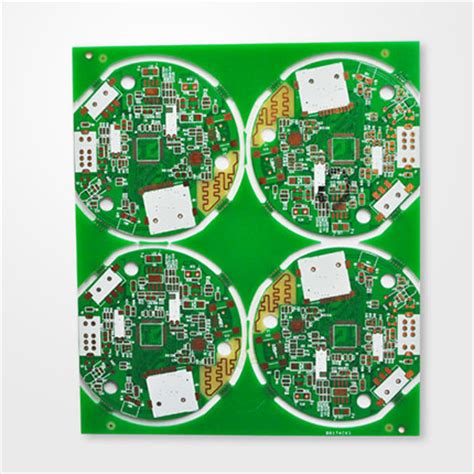
Trends in PCB-Driven Design
As technology advances and consumer demands evolve, PCB designers must stay abreast of the latest trends and techniques in their field. Some of the most significant trends in PCB-driven design include:
1. High-Density Interconnect (HDI) PCBs
HDI PCBs feature smaller traces, vias, and component sizes, allowing for more compact and complex designs. This technology is particularly valuable in applications such as smartphones, wearables, and medical devices, where space is at a premium.
2. Flexible and Rigid-Flex PCBs
Flexible PCBs and rigid-flex combinations offer designers the ability to create products with unique form factors and improved durability. These PCBs are ideal for applications that require bending, folding, or twisting, such as automotive electronics, aerospace systems, and consumer electronics.
3. 3D PCB Design
As product complexity increases, traditional 2D PCB design tools may no longer suffice. 3D PCB design software allows designers to visualize and optimize the layout of components, connectors, and mechanical features in three dimensions, leading to more efficient use of space and improved overall performance.
4. Thermal Management
With the increasing power density of modern electronics, thermal management has become a critical concern for PCB designers. Advanced techniques such as copper pours, thermal vias, and embedded heat sinks can help dissipate heat more effectively, ensuring reliable operation and extended product life.
5. Simulation and Analysis
Sophisticated simulation and analysis tools allow PCB designers to predict and optimize the performance of their designs before committing to manufacturing. These tools can help identify potential issues related to signal integrity, power distribution, electromagnetic compatibility (EMC), and thermal management, reducing the risk of costly redesigns and delays.
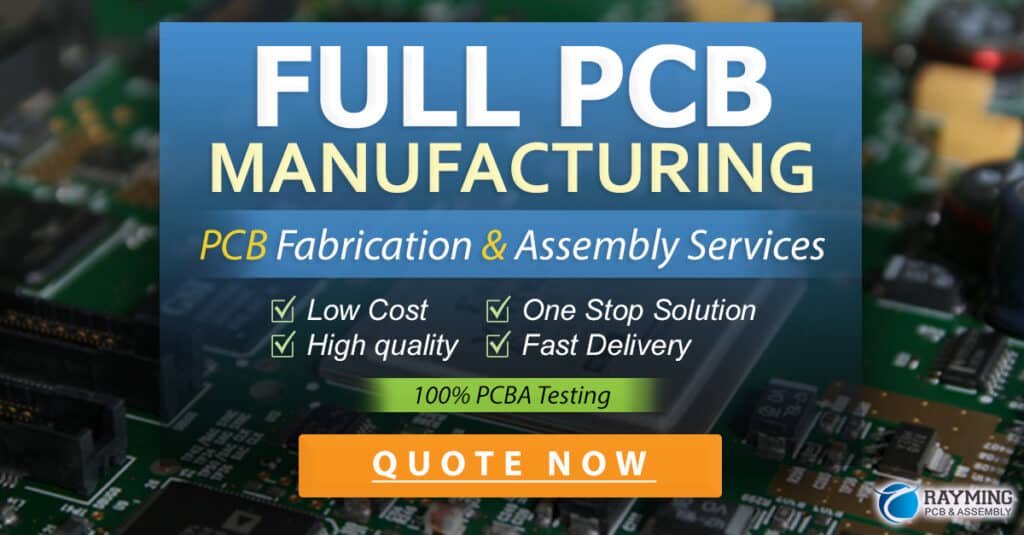
Case Studies in PCB-Driven Design
To illustrate the impact of PCB-driven design on the electronics industry, let’s examine a few real-world examples:
1. Apple’s AirPods Pro
Apple’s AirPods Pro wireless earbuds are a testament to the power of PCB-driven design. By utilizing a compact, high-density PCB with advanced components such as motion sensors and noise-canceling microphones, Apple was able to create a product that delivers exceptional audio quality and features in a tiny, lightweight package.
2. Tesla’s Model 3
The Tesla Model 3 electric vehicle relies heavily on PCB-driven design to achieve its impressive performance and efficiency. The car’s main control board, known as the “Superbottle,” integrates multiple systems such as battery management, power distribution, and thermal control into a single, highly optimized PCB assembly. This approach not only saves space and weight but also improves the vehicle’s reliability and reduces manufacturing costs.
3. Medtronic’s Micra Transcatheter Pacing System
Medtronic’s Micra Transcatheter Pacing System is a miniaturized, leadless pacemaker that can be implanted directly into the heart via a minimally invasive procedure. This groundbreaking device relies on a highly integrated, flexible PCB that incorporates the pacemaker’s battery, electronics, and sensors into a package the size of a large vitamin. By leveraging advanced PCB design techniques, Medtronic was able to create a product that improves patient outcomes and quality of life.
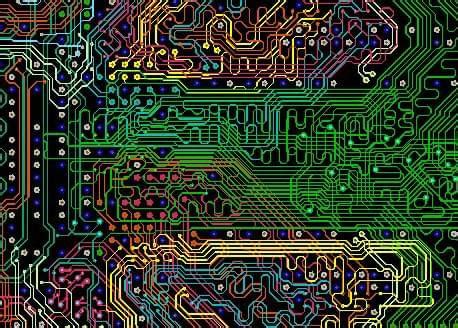
The Future of PCB-Driven Design
As the electronics industry continues to evolve, PCB-driven design will play an increasingly important role in shaping the products of tomorrow. Some of the key areas where PCB designers will make a significant impact include:
1. Internet of Things (IoT) Devices
The proliferation of connected devices in the IoT ecosystem will require PCB designers to create ever-smaller, more power-efficient, and more reliable products. Techniques such as system-on-chip (SoC) integration, energy harvesting, and wireless charging will become increasingly important in this domain.
2. 5G and Beyond
The rollout of 5G networks and the development of future wireless technologies will present new challenges and opportunities for PCB designers. High-frequency materials, advanced packaging techniques, and sophisticated signal integrity analysis will be essential for creating products that can operate reliably in these demanding environments.
3. Sustainable Electronics
As concerns about electronic waste and environmental impact grow, PCB designers will be called upon to create products that are more sustainable and recyclable. This may involve the use of biodegradable materials, modular designs that facilitate repair and upgrade, and strategies for minimizing the use of hazardous substances.
Conclusion
PCB-driven design is transforming the way electronics products are developed, manufactured, and used. By placing the PCB at the center of the design process, today’s designers are creating products that are smaller, faster, more efficient, and more reliable than ever before. As technology continues to advance and new challenges emerge, PCB designers will remain at the forefront of innovation, driving the electronics industry forward into an exciting and unpredictable future.
Frequently Asked Questions (FAQ)
-
What is the difference between PCB-driven design and traditional electronics design?
In traditional electronics design, the PCB is often treated as an afterthought, with the focus being on the schematic and component selection. In PCB-driven design, the PCB is considered an integral part of the product from the outset, with the layout, materials, and manufacturing process being optimized for performance, reliability, and manufacturability. -
What skills do I need to become a successful PCB designer?
To become a successful PCB designer, you should have a strong foundation in electronics theory, proficiency in PCB design software, knowledge of manufacturing processes and limitations, familiarity with industry standards and regulations, and excellent problem-solving and communication skills. -
How can I stay up-to-date with the latest trends and techniques in PCB design?
To stay current with the latest developments in PCB design, you can attend industry conferences and workshops, participate in online forums and communities, read technical publications and blogs, and pursue continuing education opportunities through professional organizations such as the IPC (Association Connecting Electronics Industries). -
What are some of the most significant challenges facing PCB designers today?
Some of the key challenges facing PCB designers include managing increasing product complexity, meeting demands for smaller form factors and higher performance, ensuring signal and power integrity, addressing thermal management concerns, and complying with evolving industry standards and regulations. -
How can I optimize my PCB designs for manufacturing?
To optimize your PCB designs for manufacturing, you should collaborate closely with your fabrication and assembly partners, adhere to industry standards and best practices, use design for manufacturing (DFM) techniques such as panelization and component placement optimization, and leverage simulation and analysis tools to identify and address potential issues early in the design process.
Trend | Description | Benefits |
---|---|---|
High-Density Interconnect (HDI) PCBs | Smaller traces, vias, and component sizes for compact designs | Enables smaller, more complex products |
Flexible and Rigid-Flex PCBs | PCBs that can bend, fold, or twist for unique form factors | Improves durability and allows for innovative designs |
3D PCB Design | Visualizing and optimizing layouts in three dimensions | More efficient use of space and improved performance |
Thermal Management | Techniques for dissipating heat more effectively | Ensures reliable operation and extends product life |
Simulation and Analysis | Predicting and optimizing performance before manufacturing | Reduces risk of costly redesigns and delays |
No responses yet