Introduction
When designing an electronic system that requires communication between a microcontroller and memory chips, engineers often face the decision of choosing between two popular protocols: Serial Peripheral Interface (SPI) and Inter-Integrated Circuit (I2C). Both protocols have their advantages and disadvantages, and the choice ultimately depends on the specific requirements of the project.
In this article, we will explore the key differences between SPI and I2C, their benefits and drawbacks, and provide guidance on how to select the best protocol for your memory chips based on factors such as speed, simplicity, cost, and scalability.
What is SPI?
Serial Peripheral Interface (SPI) is a synchronous serial communication protocol that enables full-duplex communication between a master device (usually a microcontroller) and one or more slave devices (such as memory chips, sensors, or displays). SPI was developed by Motorola in the late 1980s and has since become a widely used standard in the industry.
How SPI Works
SPI communication involves four signal lines:
- SCLK (Serial Clock): Generated by the master device to synchronize data transfer.
- MOSI (Master Out, Slave In): Data line for transmitting data from the master to the slave.
- MISO (Master In, Slave Out): Data line for transmitting data from the slave to the master.
- SS/CS (Slave Select/Chip Select): Used by the master to select the slave device for communication.
The master initiates communication by setting the SS/CS line low for the desired slave device. It then generates a clock signal on the SCLK line and simultaneously transmits data on the MOSI line. The slave device reads the data on the MOSI line on each clock cycle. If the slave needs to send data back to the master, it does so using the MISO line, which the master reads on each clock cycle.
Advantages of SPI
- High-speed communication: SPI can achieve data transfer rates up to several Mbps, making it suitable for applications that require fast data transfer, such as high-resolution displays or real-time sensor data.
- Full-duplex communication: SPI allows simultaneous data transmission and reception, enabling efficient communication between devices.
- Simple hardware implementation: SPI requires only four signal lines and minimal additional circuitry, making it easy to implement in hardware.
- Flexible data format: SPI does not have a fixed data format, allowing users to define their own protocol and data structure.
Disadvantages of SPI
- Limited scalability: As the number of slave devices increases, the number of SS/CS lines required also increases, leading to higher pin count and more complex PCB Routing.
- No acknowledgment mechanism: SPI does not have a built-in acknowledgment mechanism, making it difficult to detect and handle communication errors.
- No multi-master support: SPI is designed for a single master device and does not support multi-master communication natively.
- Lack of standardization: While SPI is widely used, there is no official standard, leading to variations in implementation across different manufacturers.
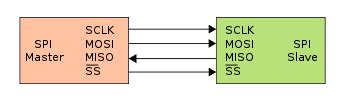
What is I2C?
Inter-Integrated Circuit (I2C) is a synchronous serial communication protocol developed by Philips Semiconductor (now NXP Semiconductors) in the early 1980s. I2C is designed to provide a simple, efficient, and standardized way to connect multiple devices using only two signal lines.
How I2C Works
I2C communication involves two signal lines:
- SCL (Serial Clock): Generated by the master device to synchronize data transfer.
- SDA (Serial Data): Bidirectional data line used for transmitting and receiving data between the master and slave devices.
In an I2C network, each device has a unique 7-bit or 10-bit address. The master initiates communication by sending a START condition followed by the slave device’s address and a read/write bit. If the addressed slave device is present, it responds with an acknowledgment (ACK) bit. The master then proceeds to transmit or receive data, with each byte followed by an ACK bit from the receiver. The communication ends with a STOP condition sent by the master.
Advantages of I2C
- Simple wiring: I2C requires only two signal lines (SCL and SDA), making it easier to route on a PCB and reducing the number of required pins on the devices.
- Standardized protocol: I2C has a well-defined specification and is widely adopted, ensuring compatibility among devices from different manufacturers.
- Multi-master support: I2C natively supports multiple master devices on the same bus, enabling more complex system architectures.
- Acknowledgment mechanism: I2C includes an acknowledgment bit after each byte transfer, allowing for error detection and handling.
- Scalability: I2C can support up to 127 devices on the same bus (with 7-bit addressing) or up to 1023 devices (with 10-bit addressing), making it suitable for systems with many connected devices.
Disadvantages of I2C
- Lower data transfer rates: I2C is typically slower than SPI, with standard mode supporting up to 100 kbps and fast mode supporting up to 400 kbps. High-speed mode (3.4 Mbps) and ultra-fast mode (5 Mbps) are available but less commonly used.
- Half-duplex communication: I2C uses a single data line for both transmitting and receiving data, resulting in half-duplex communication and potentially slower data transfer compared to SPI’s full-duplex capability.
- More complex hardware implementation: I2C requires pull-up resistors on the signal lines and more complex bus arbitration logic for multi-master support, making it slightly more challenging to implement than SPI.
- Limited cable length: I2C is designed for short-distance communication within a single device or PCB, and long cable lengths can cause signal degradation and communication issues.
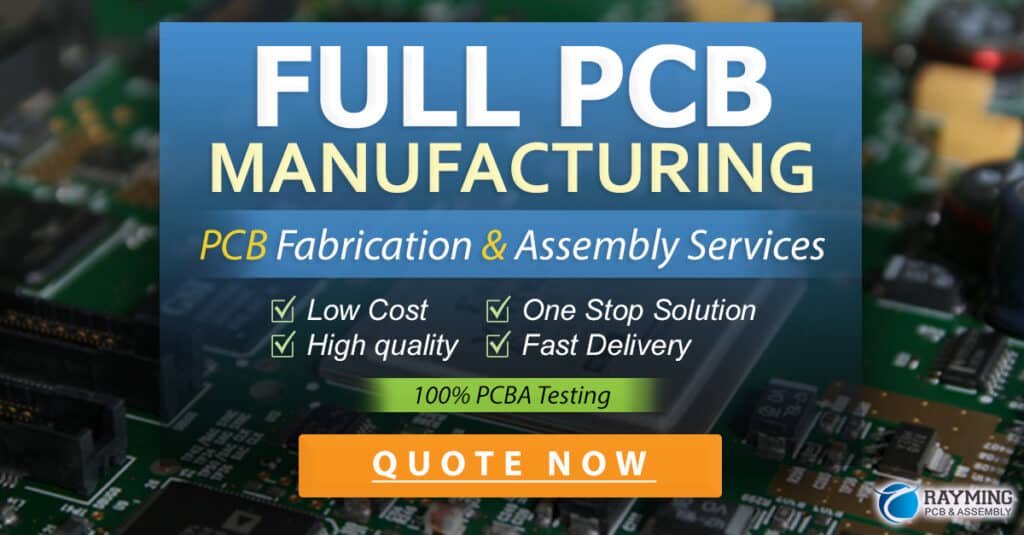
Comparing SPI and I2C
To help you choose the best protocol for your memory chips, let’s compare SPI and I2C based on several key factors:
Factor | SPI | I2C |
---|---|---|
Speed | High (up to several Mbps) | Low to medium (100 kbps to 5 Mbps) |
Wiring | 4 signal lines (SCLK, MOSI, MISO, SS/CS) | 2 signal lines (SCL, SDA) |
Standardization | No official standard, variations exist | Well-defined, widely adopted standard |
Multi-master | Not natively supported | Natively supported |
Scalability | Limited by number of SS/CS lines | Up to 127 devices (7-bit) or 1023 (10-bit) |
Data direction | Full-duplex | Half-duplex |
Error handling | No built-in acknowledgment | Acknowledgment bit after each byte |
Hardware | Simple, minimal additional circuitry | Requires pull-up resistors, more complex logic |
Cable length | Longer cables possible with proper termination | Short distances within a device or PCB |
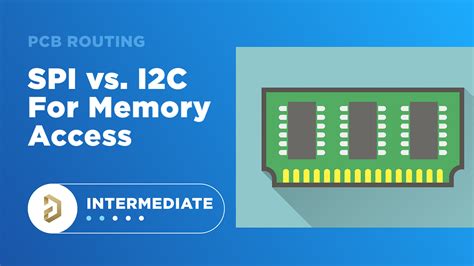
Choosing Between SPI and I2C for Your Memory Chips
When selecting the best protocol for your memory chips, consider the following factors:
-
Speed requirements: If your application demands high-speed data transfer, such as in high-resolution displays or real-time sensor data processing, SPI may be the better choice. However, if your speed requirements are more modest, I2C can be sufficient.
-
Number of devices: If your system has many memory chips or other devices that need to communicate with the microcontroller, I2C’s scalability and ability to support up to 127 or 1023 devices on a single bus can be a significant advantage. SPI’s scalability is limited by the number of available SS/CS lines.
-
PCB layout and wiring: I2C’s use of only two signal lines can simplify PCB layout and reduce the number of required pins on the microcontroller and memory chips. SPI’s four signal lines may be more challenging to route, especially in systems with many devices.
-
Compatibility and standardization: If compatibility with a wide range of devices from different manufacturers is essential, I2C’s well-defined and widely adopted standard can be beneficial. SPI’s lack of an official standard may lead to variations in implementation that could cause compatibility issues.
-
Error handling and reliability: If your application requires robust error detection and handling, I2C’s acknowledgment mechanism can provide a level of reliability that SPI lacks. However, if your system is well-designed and less prone to communication errors, SPI’s lack of built-in error handling may not be a significant concern.
-
Cost and complexity: SPI’s simpler hardware implementation and fewer required components can lead to lower costs and reduced complexity compared to I2C. However, the cost difference may be minimal in most cases, and I2C’s benefits in terms of scalability and standardization may outweigh the slightly higher cost and complexity.
Real-World Applications
Let’s look at some real-world applications and the typical protocol choice for each:
-
High-resolution displays: SPI is often used for driving high-resolution displays, such as TFT LCDs, due to its high-speed data transfer capabilities and full-duplex communication. The display module acts as a slave device, while the microcontroller sends pixel data and control commands via SPI.
-
EEPROM and flash memory: Both SPI and I2C are commonly used for interfacing with EEPROM and flash memory chips. The choice depends on the specific memory chip and the system requirements. For example, SPI is often used with higher-capacity memory chips that require fast read and write speeds, while I2C is used with smaller EEPROM chips that prioritize simplicity and low pin count.
-
Sensor networks: I2C is a popular choice for connecting multiple sensors to a microcontroller in a sensor network. Its ability to support many devices on a single bus and its standardized protocol make it well-suited for this application. Examples include temperature sensors, humidity sensors, and motion sensors in smart home or industrial monitoring systems.
-
Automotive electronics: In automotive applications, both SPI and I2C are used depending on the specific requirements. SPI is often used for high-speed communication between electronic control units (ECUs) and sensors or actuators that require real-time data transfer, such as accelerometers or gyroscopes. I2C is used for slower-speed communication between ECUs and devices like temperature sensors or battery management systems.
FAQ
-
Can SPI and I2C be used simultaneously in the same system?
Yes, SPI and I2C can coexist in the same system, as they use different signal lines and protocols. A microcontroller with both SPI and I2C peripherals can communicate with devices using either protocol as needed. -
Is it possible to convert between SPI and I2C?
While SPI and I2C are distinct protocols, it is possible to use a bridge chip to convert between the two. These bridge chips act as a translator, allowing an SPI master to communicate with an I2C slave, or vice versa. However, using a bridge chip adds complexity and cost to the system, so it’s generally better to choose the appropriate protocol for each device. -
How does the cost of implementing SPI compare to I2C?
The cost difference between implementing SPI and I2C is usually minimal. SPI requires a few more signal lines and may need additional SS/CS pins for each slave device, which can slightly increase the cost of connectors and PCB routing. I2C requires pull-up resistors on the signal lines, which adds a small cost. However, these cost differences are often negligible compared to the overall system cost. -
Can I2C be used for long-distance communication?
I2C is designed for short-distance communication within a single device or PCB. Long cable lengths can cause signal degradation and communication issues due to the capacitance and resistance of the cable. For longer distances, other protocols like RS-485 or CAN bus are more suitable. Alternatively, you can use I2C extenders or repeaters to increase the effective distance of I2C communication. -
Are there any security concerns with using SPI or I2C for memory chips?
Both SPI and I2C are vulnerable to eavesdropping and tampering, as the data is transmitted over exposed signal lines. If security is a concern, you should consider using memory chips with built-in security features, such as encrypted data storage or secure key storage. Additionally, you can implement software-based encryption and authentication mechanisms to protect sensitive data transmitted over SPI or I2C.
Conclusion
Choosing between SPI and I2C for your memory chips depends on a variety of factors, including speed requirements, number of devices, PCB layout, compatibility, error handling, and cost. By understanding the strengths and weaknesses of each protocol and considering the specific needs of your application, you can make an informed decision that balances performance, reliability, and simplicity.
In general, SPI is a good choice when high-speed data transfer is a priority, and the number of devices is limited. I2C, on the other hand, is well-suited for applications with many devices, standardized communication, and simple wiring requirements.
Ultimately, the best protocol for your memory chips will depend on your unique project requirements. By carefully evaluating your needs and the characteristics of each protocol, you can select the option that will provide the optimal balance of performance, cost, and reliability for your application.
No responses yet