Introduction to Selective soldering
Selective soldering is a process used in printed circuit board (PCB) assembly where specific components are soldered onto the board without affecting the surrounding components. This technique is particularly useful when dealing with through-hole components or when certain parts of the PCB require special attention. Selective soldering offers several advantages over traditional wave soldering, including reduced thermal stress on components, improved process control, and the ability to handle a wider range of component types and sizes.
Advantages of Selective Soldering
- Reduced thermal stress on components
- Improved process control
- Ability to handle a wider range of component types and sizes
- Reduced risk of bridging or solder defects
- Increased flexibility in PCB Design
Selective Soldering Equipment
Selective soldering machines come in various configurations, each designed to meet specific manufacturing requirements. The most common types of selective soldering equipment include:
Laser Selective Soldering
Laser selective soldering uses a focused laser beam to heat and melt the solder, allowing for precise control over the soldering process. This method is particularly useful for small, delicate components or high-density PCBs.
Miniwave Selective Soldering
Miniwave selective soldering employs a small, localized wave of molten solder to selectively solder components. This technique is well-suited for larger components or those with high thermal mass.
Robotic Selective Soldering
Robotic selective soldering systems use a programmable robotic arm to position the soldering nozzle precisely over the desired components. This method offers high flexibility and can be easily adapted to different PCB layouts and component types.
Equipment Type | Advantages | Disadvantages |
---|---|---|
Laser Selective Soldering | High precision, suitable for small components | Higher equipment cost, slower process speed |
Miniwave Selective Soldering | Efficient for larger components, lower equipment cost | Less precise than laser soldering |
Robotic Selective Soldering | High flexibility, adaptable to different PCB layouts | Higher equipment cost, requires programming |
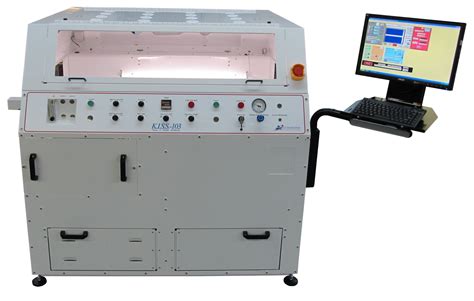
Selective Soldering Process
The selective soldering process involves several key steps to ensure a high-quality solder joint:
- PCB Preparation
- Ensure proper alignment and positioning of components
- Apply flux to the areas to be soldered
- Preheat
- Gradually heat the PCB and components to the desired temperature
- Helps activate the flux and prevent Thermal Shock
- Soldering
- Apply molten solder to the targeted areas using the selected soldering method
- Maintain consistent solder temperature and flow rate
- Cooling
- Allow the solder joints to cool and solidify
- Use forced air cooling if necessary to control the cooling rate
- Inspection
- Visually inspect the solder joints for defects such as bridging, Insufficient Solder, or poor wetting
- Use automated optical inspection (AOI) systems for high-volume production
Solder Alloys for Selective Soldering
The choice of solder alloy is critical for achieving reliable and high-quality solder joints. Some common solder alloys used in selective soldering include:
- SAC305 (Sn96.5Ag3.0Cu0.5): Lead-free alloy with good mechanical strength and reliability
- SN100C (Sn99.3Cu0.7 + Ni): Lead-free alloy with excellent wetting properties and reduced copper dissolution
- SnPb (63Sn37Pb): Traditional lead-based alloy with lower melting point and good wetting properties
Solder Alloy | Melting Point (°C) | Composition | Characteristics |
---|---|---|---|
SAC305 | 217-220 | Sn96.5Ag3.0Cu0.5 | Lead-free, good mechanical strength |
SN100C | 227 | Sn99.3Cu0.7 + Ni | Lead-free, excellent wetting, reduced copper dissolution |
SnPb (63Sn37Pb) | 183 | Sn63Pb37 | Lead-based, lower melting point, good wetting |
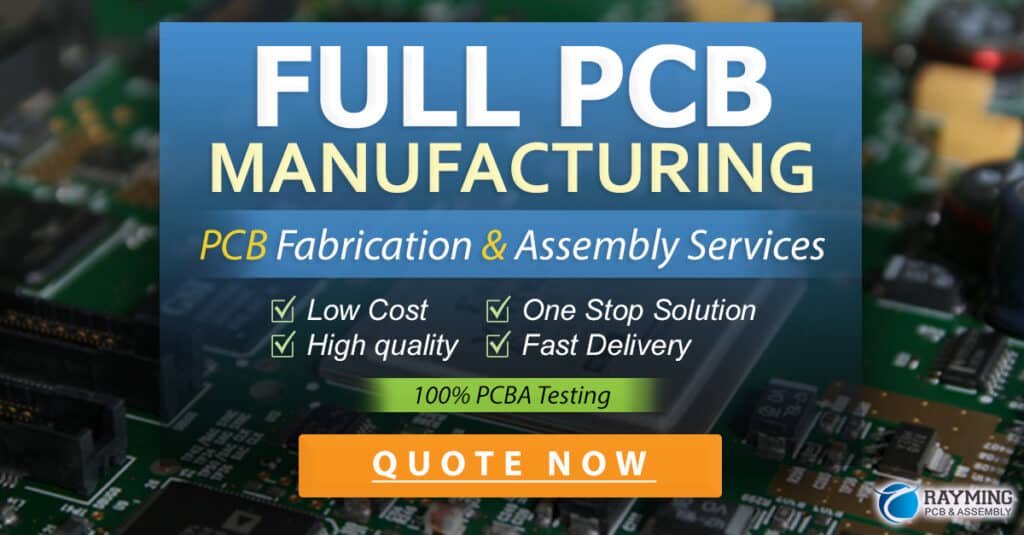
Process Control and Optimization
To ensure consistent and reliable selective soldering results, several process control and optimization techniques can be employed:
Temperature Control
Maintaining a stable and consistent solder temperature is crucial for achieving high-quality solder joints. This can be accomplished through the use of closed-loop temperature control systems, which continuously monitor and adjust the solder temperature based on feedback from sensors.
Flux Application
Proper flux application is essential for promoting good wetting and preventing oxidation during the soldering process. Automated flux dispensing systems can help ensure consistent and controlled flux application, reducing the risk of defects caused by insufficient or excessive flux.
Nozzle Selection
Choosing the appropriate soldering nozzle is important for achieving the desired solder joint geometry and minimizing the risk of defects. Factors to consider when selecting a nozzle include the size and shape of the component leads, the spacing between components, and the required solder volume.
Process Monitoring and Data Collection
Implementing process monitoring and data collection systems can help identify trends, detect potential issues, and optimize the selective soldering process over time. This can include monitoring key parameters such as solder temperature, flux application rate, and cycle times, as well as collecting data on defect rates and process yields.
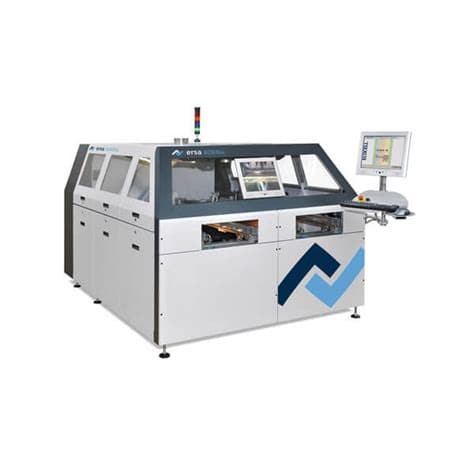
Defect Prevention and Troubleshooting
Despite careful process control and optimization, defects can still occur during selective soldering. Some common defects and their causes include:
- Bridging: Caused by excessive solder, incorrect nozzle selection, or poor component spacing
- Insufficient solder: Caused by low solder temperature, inadequate flux application, or contaminated surfaces
- Poor wetting: Caused by oxidized surfaces, insufficient flux, or incorrect solder alloy selection
To prevent and troubleshoot these defects, consider the following strategies:
- Regularly maintain and calibrate soldering equipment
- Ensure proper PCB and component cleaning prior to soldering
- Optimize flux application and solder temperature settings
- Select appropriate nozzles and solder alloys for the specific application
- Implement process monitoring and data collection to identify trends and potential issues
Selective Soldering and Industry Standards
Selective soldering processes must comply with various industry standards to ensure the quality and reliability of the final product. Some key standards related to selective soldering include:
- IPC-A-610: Acceptability of Electronic Assemblies
- IPC-J-STD-001: Requirements for Soldered Electrical and Electronic Assemblies
- IPC-7711/7721: Rework, Modification, and Repair of Electronic Assemblies
Adhering to these standards helps ensure that selective soldering processes meet the required quality and reliability criteria for the intended application.
Frequently Asked Questions (FAQ)
-
What is selective soldering, and how does it differ from wave soldering?
Selective soldering is a process where specific components are soldered onto a PCB without affecting the surrounding components. Unlike wave soldering, which exposes the entire PCB to a wave of molten solder, selective soldering targets only the desired areas, reducing thermal stress on components and allowing for greater flexibility in PCB design. -
What are the main advantages of selective soldering?
The main advantages of selective soldering include reduced thermal stress on components, improved process control, the ability to handle a wider range of component types and sizes, reduced risk of bridging or solder defects, and increased flexibility in PCB design. -
What types of selective soldering equipment are available?
The most common types of selective soldering equipment include laser selective soldering, miniwave selective soldering, and robotic selective soldering. Each type has its own advantages and disadvantages, and the choice depends on factors such as the specific manufacturing requirements, component types, and PCB layout. -
How can I optimize my selective soldering process to prevent defects?
To optimize your selective soldering process and prevent defects, consider implementing the following strategies: - Regularly maintain and calibrate soldering equipment
- Ensure proper PCB and component cleaning prior to soldering
- Optimize flux application and solder temperature settings
- Select appropriate nozzles and solder alloys for the specific application
-
Implement process monitoring and data collection to identify trends and potential issues
-
What industry standards should I be aware of when implementing selective soldering in my manufacturing process?
Some key industry standards related to selective soldering include IPC-A-610 (Acceptability of Electronic Assemblies), IPC-J-STD-001 (Requirements for Soldered Electrical and Electronic Assemblies), and IPC-7711/7721 (Rework, Modification, and Repair of Electronic Assemblies). Adhering to these standards helps ensure that your selective soldering processes meet the required quality and reliability criteria for your intended application.
No responses yet