Introduction to 94v0 PCBs
94v0 PCBs, also known as 94v0 printed circuit boards, are a type of PCB material that meets the UL94V-0 flammability rating standard. This rating indicates that the PCB has excellent flame retardant properties and self-extinguishing capabilities, making it suitable for applications where fire safety is a critical concern.
The “94” in 94v0 refers to the UL 94 flammability standard, while the “v0” denotes the highest level of flame retardance within this standard. PCBs that achieve the 94v0 rating have undergone rigorous testing to ensure they can withstand exposure to open flames without igniting or spreading fire.
Key Features of 94v0 PCBs
- Flame Retardance: 94v0 PCBs are designed to resist ignition and self-extinguish within seconds of removing the flame source.
- Low Smoke and Toxicity: When exposed to fire, 94v0 PCBs produce minimal smoke and toxic fumes, reducing the risk of harm to people and equipment.
- High Temperature Resistance: These PCBs can withstand elevated temperatures without deteriorating or losing their flame-retardant properties.
- Durability: 94v0 PCBs are known for their robustness and ability to withstand harsh environmental conditions.
- Versatility: They can be used in a wide range of applications across various industries.
94v0 PCB Materials and Manufacturing Process
Common 94v0 PCB Materials
Several materials can be used to manufacture 94v0 PCBs, each with unique properties and advantages. Some of the most common materials include:
- FR-4: A glass-reinforced epoxy laminate that offers excellent mechanical and electrical properties, making it a popular choice for 94v0 PCBs.
- Polyimide: A high-performance polymer known for its exceptional thermal stability and resistance to chemicals, making it suitable for demanding applications.
- CEM-1: A composite material consisting of woven glass fabric and epoxy resin, offering good electrical properties and cost-effectiveness.
- PTFE (Teflon): A fluoropolymer with outstanding dielectric properties, low dissipation factor, and high temperature resistance.
Material | Dielectric Constant | Dissipation Factor | Thermal Conductivity (W/mK) | Tg (°C) |
---|---|---|---|---|
FR-4 | 4.5 – 4.7 | 0.02 – 0.03 | 0.3 – 0.4 | 130-140 |
Polyimide | 3.4 – 3.5 | 0.002 – 0.003 | 0.2 – 0.3 | 260-270 |
CEM-1 | 4.5 – 4.7 | 0.02 – 0.03 | 0.3 – 0.4 | 130-140 |
PTFE | 2.0 – 2.1 | 0.0002 – 0.0009 | 0.2 – 0.3 | 327 |
94v0 PCB Manufacturing Process
The manufacturing process for 94v0 PCBs is similar to that of standard PCBs, with a few additional steps to ensure the desired flame retardance is achieved. The general steps involved are:
- Design: The PCB layout is designed using CAD software, taking into account the specific requirements of the 94v0 standard.
- Material Selection: The appropriate 94v0-rated material is chosen based on the application’s requirements.
- Lamination: The selected material is laminated together with copper foil to create the PCB substrate.
- Drilling: Holes are drilled into the substrate to accommodate components and vias.
- Plating: The drilled holes are plated with copper to establish electrical connections between layers.
- Etching: Unwanted copper is removed from the substrate using a chemical etching process, leaving behind the desired circuit pattern.
- Solder Mask Application: A protective solder mask is applied to the PCB to prevent short circuits and improve durability.
- Silkscreen Printing: Text and symbols are printed onto the PCB using silkscreen printing for easy identification and assembly.
- Surface Finishing: A surface finish, such as HASL, ENIG, or OSP, is applied to the exposed copper to prevent oxidation and enhance solderability.
- Testing and Inspection: The finished 94v0 PCB undergoes rigorous testing and inspection to ensure it meets the required standards and specifications.
Applications of 94v0 PCBs
Consumer Electronics
94v0 PCBs are widely used in consumer electronics due to their flame-retardant properties, which help prevent the spread of fire in the event of a device malfunction or overheating. Some common applications include:
- Smartphones and tablets
- Laptops and desktop computers
- Televisions and displays
- Gaming consoles
- Home appliances
Automotive Electronics
The automotive industry relies on 94v0 PCBs for various electronic systems, as they must withstand harsh environmental conditions and ensure passenger safety. Applications include:
- Engine control units (ECUs)
- Infotainment systems
- Advanced driver-assistance systems (ADAS)
- Lighting control modules
- Power management systems
Medical Devices
Medical devices require high levels of reliability and safety, making 94v0 PCBs an essential component. They are used in:
- Patient monitoring systems
- Diagnostic imaging equipment
- Implantable devices
- Surgical instruments
- Laboratory equipment
Aerospace and Defense
94v0 PCBs are crucial in aerospace and defense applications, where reliability and durability are paramount. Examples include:
- Avionics systems
- Radar and communication equipment
- Satellite components
- Military vehicles and weaponry
- Unmanned aerial vehicles (UAVs)
Industrial Automation and Control
Industrial environments often involve high temperatures, vibrations, and exposure to chemicals, making 94v0 PCBs a suitable choice for automation and control systems. Applications include:
- Programmable logic controllers (PLCs)
- Human-machine interfaces (HMIs)
- Sensors and transducers
- Motor drives and control systems
- Power distribution and management
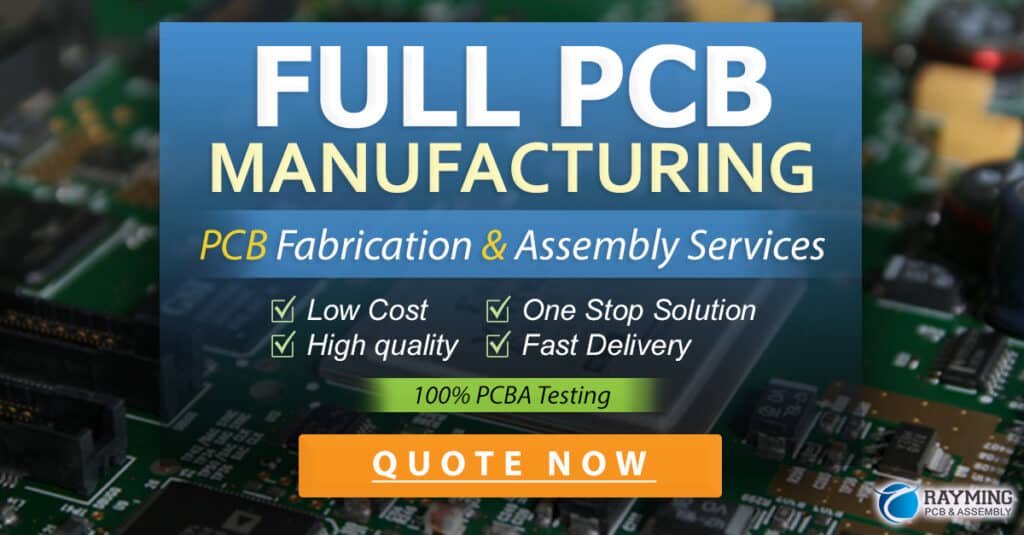
94v0 PCB Design Considerations
Thermal Management
Proper thermal management is essential when designing 94v0 PCBs to ensure optimal performance and longevity. Some key considerations include:
- Component placement: Position heat-generating components away from sensitive areas and provide adequate spacing for heat dissipation.
- Thermal vias: Use thermal vias to transfer heat from components to other layers or heatsinks.
- Heatsinks and cooling solutions: Incorporate heatsinks, fans, or other cooling solutions when necessary to manage heat effectively.
- PCB Material Selection: Choose materials with appropriate thermal conductivity and Tg values based on the application’s requirements.
Signal Integrity
Maintaining signal integrity is crucial for ensuring reliable operation and preventing issues like crosstalk, EMI, and signal distortion. Consider the following:
- Trace routing: Route traces carefully to minimize crosstalk and maintain consistent impedance.
- Ground planes: Use solid ground planes to provide a low-impedance return path for signals and reduce EMI.
- Decoupling capacitors: Place decoupling capacitors close to ICs to suppress high-frequency noise and stabilize power supply.
- Shielding: Implement shielding techniques, such as copper pours or metal enclosures, to minimize EMI and external interference.
Manufacturing Considerations
When designing 94v0 PCBs, it’s essential to keep manufacturing considerations in mind to ensure a smooth and cost-effective production process. Some key factors include:
- Minimum feature sizes: Adhere to the manufacturer’s minimum feature sizes for traces, spacing, and drilled holes to avoid production issues.
- Panelization: Design the PCB layout to allow for efficient panelization, minimizing waste and optimizing production yield.
- DFM guidelines: Follow design for manufacturability (DFM) guidelines provided by the PCB manufacturer to avoid potential issues during production.
- Testing and inspection: Include testability features, such as test points and fiducials, to facilitate testing and inspection during manufacturing.
Future Trends and Developments in 94v0 PCBs
As technology advances and new applications emerge, 94v0 PCBs continue to evolve to meet the changing demands of various industries. Some future trends and developments include:
- Advanced materials: Ongoing research and development of new materials with improved thermal, mechanical, and electrical properties for enhanced performance and reliability.
- Miniaturization: The trend towards smaller, more compact electronic devices drives the need for miniaturized 94v0 PCBs with higher component density and finer feature sizes.
- High-speed applications: Increasing demand for high-speed data transmission and processing requires 94v0 PCBs optimized for signal integrity and low-loss performance.
- Sustainable manufacturing: Growing environmental concerns drive the development of eco-friendly 94v0 PCB materials and manufacturing processes, minimizing the use of hazardous substances and promoting recyclability.
- Integration with emerging technologies: 94v0 PCBs will play a crucial role in enabling emerging technologies, such as 5G networks, Internet of Things (IoT) devices, artificial intelligence (AI), and renewable energy systems.
FAQ
What is the difference between 94v0 and 94v2 PCBs?
Both 94v0 and 94v2 PCBs meet the UL94 flammability standard, but they differ in their flame-retardant properties. 94v0 PCBs have the highest level of flame retardance, self-extinguishing within 10 seconds of removing the flame source. 94v2 PCBs, on the other hand, have a lower level of flame retardance, self-extinguishing within 30 seconds. 94v0 PCBs are more suitable for applications with stringent fire safety requirements.
Can 94v0 PCBs be used in high-temperature environments?
Yes, 94v0 PCBs are designed to withstand elevated temperatures without losing their flame-retardant properties. The specific temperature range depends on the PCB material used. For example, FR-4 94v0 PCBs can typically withstand temperatures up to 130-140°C, while polyimide 94v0 PCBs can operate at temperatures up to 260-270°C.
Are 94v0 PCBs more expensive than standard PCBs?
Generally, 94v0 PCBs are more expensive than standard PCBs due to the specialized materials and additional manufacturing steps required to achieve the desired flame-retardant properties. However, the cost difference can vary depending on factors such as PCB size, complexity, and production volume. The added cost is often justified by the enhanced safety and reliability provided by 94v0 PCBs in critical applications.
How can I ensure my 94v0 PCB design meets the required standards?
To ensure your 94v0 PCB design meets the required standards, follow these steps:
- Choose a reputable PCB manufacturer with experience in producing 94v0 PCBs.
- Clearly communicate your requirements and specifications to the manufacturer, including the desired UL94 rating and any application-specific needs.
- Follow the manufacturer’s design guidelines and DFM recommendations to avoid potential issues during production.
- Request a certificate of compliance from the manufacturer, confirming that the produced PCBs meet the 94v0 standard.
- Perform thorough testing and inspection of the finished PCBs to verify their performance and compliance with the required standards.
Can 94v0 PCBs be recycled?
Yes, 94v0 PCBs can be recycled, but the process is more complex compared to standard PCBs due to the presence of flame-retardant additives. Specialized recycling facilities are equipped to handle 94v0 PCBs, using advanced techniques to separate and recover the valuable materials while safely disposing of the flame-retardant substances. As sustainability becomes an increasingly important consideration, PCB manufacturers and recyclers are working on developing more eco-friendly 94v0 materials and recycling processes.
Conclusion
94v0 PCBs are essential components in a wide range of applications where fire safety, reliability, and durability are critical. With their excellent flame-retardant properties, low smoke and toxicity, and high-temperature resistance, these PCBs provide a robust solution for industries such as consumer electronics, automotive, medical devices, aerospace, and industrial automation.
When designing 94v0 PCBs, it is crucial to consider factors such as thermal management, signal integrity, and manufacturing considerations to ensure optimal performance and cost-effectiveness. As technology advances and new applications emerge, 94v0 PCBs will continue to evolve, incorporating advanced materials, miniaturization, and support for high-speed applications while prioritizing sustainability.
By understanding the key features, applications, and design considerations of 94v0 PCBs, engineers and manufacturers can make informed decisions when developing electronic systems that prioritize safety, reliability, and performance. As the demand for fire-resistant and high-performance PCBs grows, 94v0 PCBs will remain an indispensable component in shaping the future of electronics across various industries.
No responses yet