What is a 94v0 PCB?
A 94v0 PCB is a type of printed circuit board that is manufactured using materials that meet the UL94V-0 flammability standard. This standard, set by Underwriters Laboratories (UL), is a widely recognized safety standard for electronic components and materials. The “94” in the name refers to the UL 94 standard, while the “v0” indicates the highest level of flame retardancy within the standard.
The UL94V-0 standard requires that the material used in the PCB must self-extinguish within 10 seconds after being exposed to a flame, and the material should not drip flaming particles that could ignite cotton placed below the sample. This ensures that even if the PCB is exposed to a fire or high temperatures, it will not contribute to the spread of the fire, minimizing the risk of damage to the device and its surroundings.
Composition of 94v0 PCBs
94v0 PCBs are typically made from a flame-retardant substrate material, such as FR-4 (Flame Retardant 4). FR-4 is a composite material composed of woven fiberglass cloth with an epoxy resin binder. The flame-retardant properties of the substrate are achieved by adding brominated or halogen-free flame retardants to the epoxy resin.
In addition to the substrate, 94v0 PCBs also feature copper traces and pads that are used to connect electronic components. The copper layer is laminated onto the substrate using heat and pressure, creating a strong bond between the two materials. The thickness of the copper layer can vary depending on the specific requirements of the device and the current-carrying capacity needed.
Characteristics of 94v0 PCBs
Flame Retardancy
The most notable characteristic of 94v0 PCBs is their excellent flame-retardant properties. As mentioned earlier, these PCBs are designed to self-extinguish within 10 seconds of being exposed to a flame, preventing the spread of fire. This is achieved through the use of flame-retardant materials in the PCB substrate and the addition of flame retardants to the epoxy resin.
Thermal Stability
94v0 PCBs offer excellent thermal stability, which is essential for electronic devices that generate significant amounts of heat. The glass transition temperature (Tg) of FR-4, the most common substrate material used in 94v0 PCBs, is around 130°C to 140°C. This means that the PCB can withstand temperatures up to this range without experiencing significant changes in its mechanical properties.
Mechanical Strength
Another important characteristic of 94v0 PCBs is their mechanical strength. The use of woven fiberglass cloth in the substrate provides excellent tensile strength and dimensional stability to the PCB. This is particularly important for devices that are subject to vibrations, shocks, or other mechanical stresses during operation.
Electrical Insulation
94v0 PCBs provide good electrical insulation between the copper traces and pads. The substrate material, such as FR-4, has a high dielectric strength, which prevents current leakage and short circuits between adjacent traces. This is crucial for maintaining the integrity of the electronic signals and preventing damage to the components.
Moisture Resistance
94v0 PCBs also exhibit good moisture resistance, which is essential for devices that may be exposed to humid environments. The epoxy resin used in the substrate is inherently moisture-resistant, and the PCB can be further protected by applying conformal coatings or potting compounds to the surface.
Applications of 94v0 PCBs
94v0 PCBs find applications in a wide range of electronic devices, particularly those that require high levels of safety and reliability. Some common applications include:
Consumer Electronics
94v0 PCBs are widely used in consumer electronics, such as smartphones, tablets, laptops, and televisions. These devices often have compact designs and generate significant amounts of heat, making the use of flame-retardant PCBs essential for ensuring user safety and device longevity.
Automotive Electronics
The automotive industry heavily relies on 94v0 PCBs for various electronic systems, such as engine control units, infotainment systems, and advanced driver assistance systems (ADAS). These PCBs must withstand harsh environmental conditions, including high temperatures, vibrations, and exposure to moisture and chemicals.
Medical Devices
Medical devices, such as patient monitors, diagnostic equipment, and implantable devices, require PCBs that meet stringent safety and reliability standards. 94v0 PCBs are commonly used in these applications due to their flame-retardant properties and ability to withstand sterilization processes.
Industrial Equipment
Industrial equipment, such as power supplies, motor controllers, and automation systems, often operate in demanding environments with high temperatures and exposure to dust and moisture. 94v0 PCBs are well-suited for these applications, as they offer excellent thermal stability and moisture resistance.
Aerospace and Defense
The aerospace and defense industries require PCBs that can withstand extreme environmental conditions and meet strict safety requirements. 94v0 PCBs are commonly used in these applications, as they offer excellent flame retardancy, mechanical strength, and resistance to vibrations and shocks.
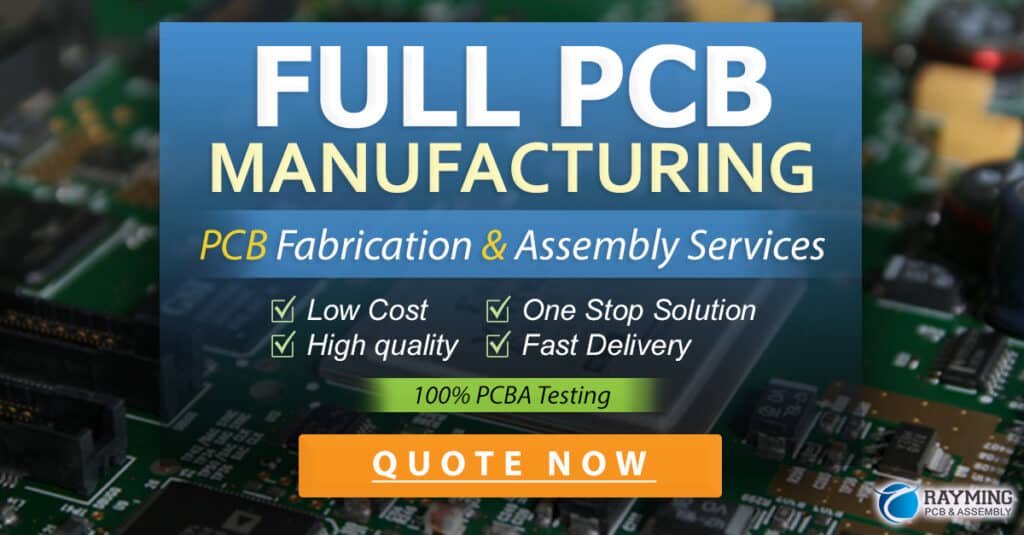
Benefits of Using 94v0 PCBs
Using 94v0 PCBs in electronic devices offers several benefits, including:
-
Enhanced safety: The excellent flame-retardant properties of 94v0 PCBs minimize the risk of fire, protecting users and the device itself.
-
Improved reliability: The thermal stability, mechanical strength, and moisture resistance of 94v0 PCBs contribute to the overall reliability of the device, reducing the risk of failures and extending its lifespan.
-
Compliance with safety standards: By using 94v0 PCBs, manufacturers can ensure that their devices comply with relevant safety standards, such as UL94V-0, which is often a requirement for certain applications and markets.
-
Cost-effectiveness: While 94v0 PCBs may have a slightly higher initial cost compared to non-flame-retardant PCBs, their use can help reduce the overall cost of ownership by minimizing the risk of device failures and potential liability issues.
FAQ
1. What is the difference between 94v0 and 94v2 PCBs?
The main difference between 94v0 and 94v2 PCBs lies in their flame-retardant properties. 94v0 PCBs have the highest level of flame retardancy, self-extinguishing within 10 seconds of being exposed to a flame, without dripping flaming particles. 94v2 PCBs, on the other hand, have a lower level of flame retardancy, allowing for some burning and dripping of flaming particles.
2. Can 94v0 PCBs be used in high-temperature applications?
Yes, 94v0 PCBs can be used in high-temperature applications, as they offer excellent thermal stability. The glass transition temperature (Tg) of FR-4, the most common substrate material used in 94v0 PCBs, is around 130°C to 140°C, allowing the PCB to withstand temperatures up to this range without experiencing significant changes in its mechanical properties.
3. Are 94v0 PCBs more expensive than non-flame-retardant PCBs?
94v0 PCBs may have a slightly higher initial cost compared to non-flame-retardant PCBs due to the use of specialized materials and additives. However, the enhanced safety and reliability offered by 94v0 PCBs can help reduce the overall cost of ownership by minimizing the risk of device failures and potential liability issues.
4. Can 94v0 PCBs be customized to meet specific design requirements?
Yes, 94v0 PCBs can be customized to meet specific design requirements. Manufacturers can work with PCB designers to create custom layouts, choose appropriate substrate materials, and specify the required copper thickness and trace widths to ensure optimal performance and reliability for the intended application.
5. How can I ensure that a PCB meets the 94v0 standard?
To ensure that a PCB meets the 94v0 standard, it is essential to work with a reputable PCB manufacturer that uses materials and processes that comply with the UL94V-0 standard. Manufacturers should provide documentation, such as material datasheets and test reports, to demonstrate compliance with the standard. Additionally, end-users can request third-party testing and certification to verify that the PCB meets the required flame-retardant properties.
Conclusion
94v0 PCBs are an essential component in ensuring the safety and reliability of electronic devices. Their excellent flame-retardant properties, thermal stability, mechanical strength, and electrical insulation make them well-suited for a wide range of applications, from consumer electronics to industrial equipment and aerospace systems.
By using 94v0 PCBs, manufacturers can minimize the risk of fire, improve device reliability, and ensure compliance with relevant safety standards. As electronic devices continue to become more complex and compact, the importance of using high-quality, flame-retardant PCBs will only continue to grow.
When designing and manufacturing electronic devices, it is crucial to work with experienced PCB manufacturers who can provide 94v0 PCBs that meet the specific requirements of the application. By doing so, manufacturers can create safer, more reliable products that meet the needs of their customers and contribute to the overall advancement of the electronics industry.
No responses yet