Introduction to 94V 0 PCBs
In the world of Electronic Manufacturing, the quality and reliability of printed circuit boards (PCBs) are of utmost importance. Among the various standards and certifications for PCBs, the 94V 0 rating stands out as a mark of excellence. This article will delve into the intricacies of 94V 0 circuit boards, exploring their characteristics, benefits, and applications.
What is a 94V 0 Circuit Board?
A 94V 0 circuit board is a PCB that has been certified to meet the UL 94 flammability standard, specifically the V 0 rating. The Underwriters Laboratories (UL) 94 standard is a widely recognized safety standard that evaluates the flammability and fire resistance of plastic materials used in electronic devices.
The V 0 rating is the highest level of flame retardancy within the UL 94 standard. It indicates that the PCB material will self-extinguish within 10 seconds of being exposed to a flame, without dripping flaming particles that could ignite cotton placed below the sample.
Benefits of Using 94V 0 PCBs
Enhanced Safety
The primary benefit of using 94V 0 PCBs is the enhanced safety they provide. With their excellent flame retardancy, these circuit boards significantly reduce the risk of fire hazards in electronic devices. This is particularly crucial in applications where the consequences of a fire could be catastrophic, such as in aerospace, medical devices, and industrial control systems.
Compliance with Industry Standards
Many industries have strict regulations and standards regarding the fire safety of electronic components. By using 94V 0 PCBs, manufacturers can ensure compliance with these standards, facilitating the approval process and minimizing the risk of non-compliance issues.
Improved Reliability
In addition to their fire-resistant properties, 94V 0 PCBs also exhibit excellent electrical and mechanical characteristics. The high-quality materials used in these circuit boards contribute to their overall reliability, ensuring consistent performance and longevity.
Materials Used in 94V 0 PCBs
The choice of materials is crucial in achieving the 94V 0 rating for PCBs. The most commonly used materials for 94V 0 circuit boards are:
FR 4
FR 4 (Flame Retardant 4) is a glass-reinforced epoxy laminate that is widely used in the PCB industry. It offers excellent mechanical strength, electrical insulation, and thermal stability. FR 4 is available in various grades, with some specifically formulated to meet the 94V 0 standard.
Polyimide
Polyimide is a high-performance polymer known for its exceptional thermal and chemical resistance. It is often used in applications that require operation at high temperatures or exposure to harsh environments. Polyimide PCBs with 94V 0 rating provide both fire safety and robust performance.
Comparison of Materials
Material | Thermal Stability | Mechanical Strength | Electrical Insulation | Cost |
---|---|---|---|---|
FR 4 | Good | Excellent | Good | Low |
Polyimide | Excellent | Good | Excellent | High |
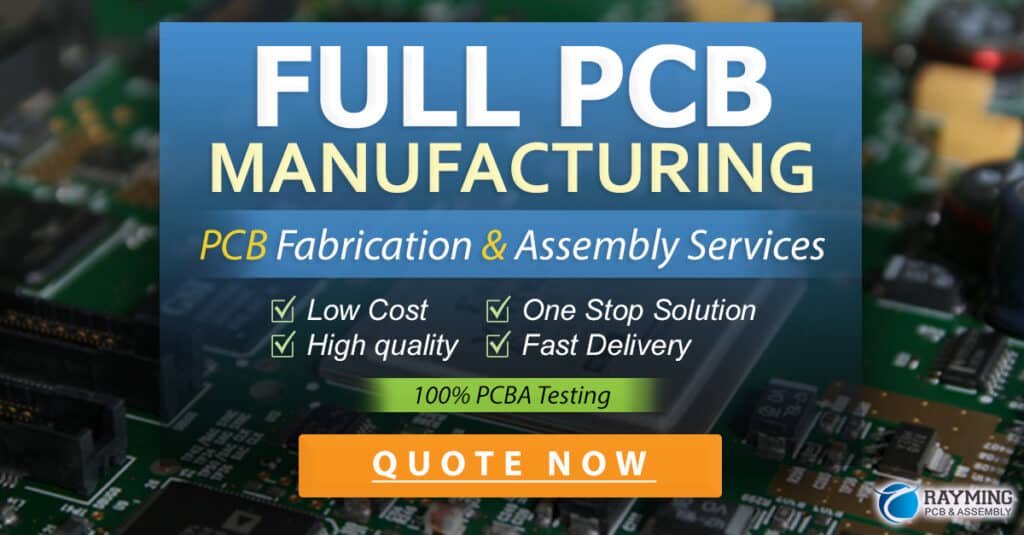
Manufacturing Process of 94V 0 PCBs
The manufacturing process of 94V 0 PCBs follows the general steps of PCB fabrication, with additional considerations to ensure the desired flame retardancy.
Material Selection and Preparation
The first step is to select the appropriate 94V 0 rated material, such as FR 4 or polyimide. The material is then cut to the required size and thickness, and any necessary pre-treatment processes are carried out.
Circuit Design and Patterning
The desired circuit pattern is designed using specialized software and transferred onto the PCB material through a process called photolithography. This involves applying a light-sensitive resist, exposing it to UV light through a mask, and developing the pattern.
Etching and Plating
After the circuit pattern is developed, the unwanted copper is removed through an etching process, leaving only the desired conductive traces. The traces are then plated with a protective layer, typically tin or gold, to prevent oxidation and improve solderability.
Lamination and Drilling
For multi-layer PCBs, the individual layers are laminated together under high pressure and temperature. Holes are then drilled through the board to allow for electrical connections between layers.
Surface Finishing and Solder Mask Application
The PCB undergoes a surface finishing process to protect the exposed copper and enhance the ability to solder components. A solder mask is applied to the board, covering the areas that should not be soldered and leaving the pads exposed.
Testing and Quality Control
Throughout the manufacturing process, various tests and inspections are performed to ensure the quality and reliability of the 94V 0 PCBs. These may include visual inspections, electrical tests, and flammability tests to verify compliance with the UL 94 V 0 standard.
Applications of 94V 0 PCBs
94V 0 PCBs find applications in a wide range of industries and products where fire safety is a critical concern. Some examples include:
Aerospace and Defense
In the aerospace and defense sectors, 94V 0 PCBs are used in avionics, satellites, and military equipment. The high reliability and fire resistance of these circuit boards are essential for the safe operation of these systems in demanding environments.
Medical Devices
Medical devices, such as patient monitors, diagnostic equipment, and implantable devices, require PCBs that meet stringent safety standards. 94V 0 PCBs are commonly used in these applications to ensure patient safety and minimize the risk of fire hazards.
Industrial Control Systems
Industrial control systems, including programmable logic controllers (PLCs), sensors, and automation equipment, often operate in harsh environments with potential fire risks. 94V 0 PCBs provide the necessary fire protection and reliability for these critical systems.
Consumer Electronics
Although not all consumer electronics require 94V 0 PCBs, some high-end products, such as premium smartphones, laptops, and gaming devices, may use these circuit boards to enhance product safety and quality.
Frequently Asked Questions (FAQ)
1. What is the difference between 94V 0 and other UL 94 ratings?
The UL 94 standard defines several flammability ratings, including V 0, V 1, and V 2. The main differences lie in the flame extinguishing time and the allowance of flaming drips. 94V 0 is the most stringent rating, requiring self-extinguishment within 10 seconds and no flaming drips. V 1 and V 2 allow longer extinguishing times and some flaming drips.
2. Can 94V 0 PCBs be used in high-temperature applications?
Yes, 94V 0 PCBs can be designed for high-temperature applications. The choice of base material, such as polyimide, and the proper selection of components and manufacturing processes enable 94V 0 PCBs to operate reliably in high-temperature environments.
3. Are 94V 0 PCBs more expensive than standard PCBs?
In general, 94V 0 PCBs may be slightly more expensive than standard PCBs due to the higher-grade materials and additional testing required. However, the cost difference is often justified by the enhanced safety and compliance with industry standards.
4. How can I ensure that my PCB design meets the 94V 0 standard?
To ensure compliance with the 94V 0 standard, it is essential to work with a reputable PCB manufacturer that has experience in producing 94V 0 boards. Provide clear specifications and requirements, and discuss the design with the manufacturer to identify any potential issues or improvements.
5. Are there any limitations or challenges in using 94V 0 PCBs?
One challenge in using 94V 0 PCBs is the limited availability of certain components that meet the same flammability rating. Designers may need to carefully select components or work with suppliers to find suitable alternatives. Additionally, the higher-grade materials used in 94V 0 PCBs may require adjusted manufacturing processes and settings.
Conclusion
94V 0 circuit boards represent the pinnacle of fire safety and reliability in the PCB industry. By understanding the characteristics, benefits, and applications of these high-quality PCBs, designers and manufacturers can make informed decisions when developing products that require exceptional fire resistance and performance.
As the demand for safer and more reliable electronic devices continues to grow, the use of 94V 0 PCBs is likely to expand across various industries. By staying informed about the latest developments and best practices in PCB manufacturing, companies can leverage the advantages of 94V 0 circuit boards to create products that meet the highest standards of safety and quality.
No responses yet