Understand the Different Types of Solder
Before diving into the specifics of Choosing Solder, it’s essential to have a basic understanding of the different types available:
Lead-based Solder
Lead-based solder, typically consisting of a 60/40 tin-lead ratio (60% tin, 40% lead), was once the most common type used in electronics. However, due to environmental and health concerns, many countries have restricted or banned its use in recent years.
Lead-free Solder
As an alternative to lead-based solder, lead-free options have gained popularity. These solders are made from various alloys, such as tin-silver-copper (SAC), tin-copper (SnCu), or tin-bismuth (SnBi).
Rosin-core Solder
Rosin-core solder contains a flux core that helps to clean the metal surfaces during the soldering process, promoting better adhesion and preventing oxidation.
Acid-core Solder
Acid-core solder is primarily used for plumbing and should not be used for electrical connections, as the acid can corrode components and create short circuits.
Consider the Melting Point
One of the most important factors to consider when choosing solder is its melting point. The melting point is the temperature at which the solder transitions from a solid to a liquid state. It’s crucial to select a solder with a melting point that is appropriate for your project and the components you are working with.
Solder Type | Melting Point Range |
---|---|
Lead-based (60/40) | 183°C – 190°C |
Lead-free (SAC305) | 217°C – 220°C |
Lead-free (SnCu) | 227°C – 229°C |
Lead-free (SnBi) | 138°C – 140°C |
When choosing a solder based on its melting point, consider the following:
- The temperature tolerance of the components you are soldering
- The heat sensitivity of the circuit board material
- The available soldering tools and their temperature range
Evaluate the Wetting Ability
Wetting refers to the ability of the molten solder to spread evenly across the metal surfaces being joined. Good wetting ensures a strong, reliable connection between components. When selecting solder, consider its wetting ability on the specific metals you are working with, such as copper, gold, or silver.
Some factors that influence wetting ability include:
- The alloy composition of the solder
- The presence of flux or other additives
- The cleanliness of the metal surfaces
- The temperature and duration of the soldering process
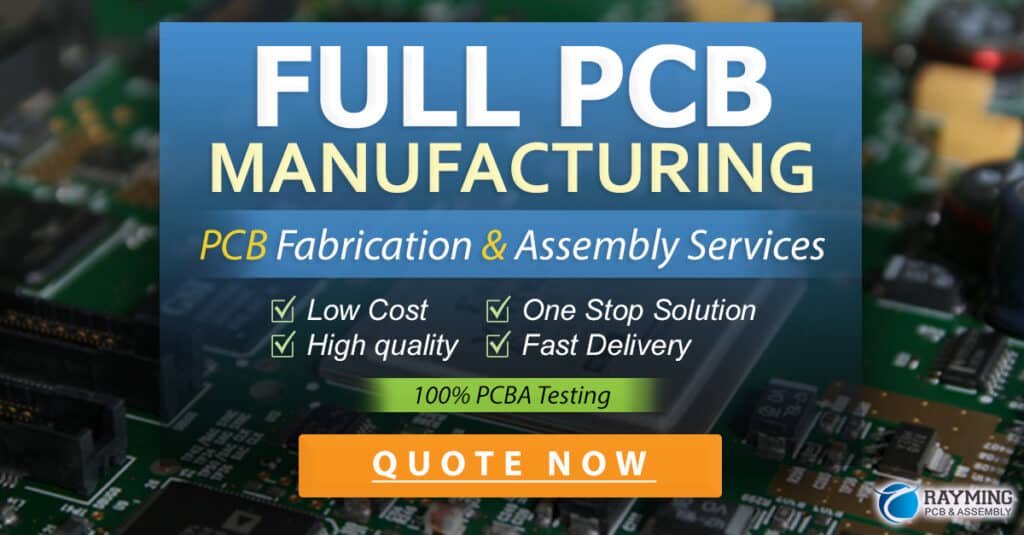
Assess the Mechanical Strength
The mechanical strength of a solder joint determines its ability to withstand physical stress and vibration. When choosing solder for your circuit board, consider the expected operating conditions and any potential mechanical stresses the board may encounter.
Factors that impact the mechanical strength of a solder joint include:
- The alloy composition of the solder
- The geometry and size of the solder joint
- The cooling rate during solidification
- The presence of any contaminants or voids in the joint
Determine the Electrical Conductivity
Electrical conductivity is a measure of how easily electricity flows through a material. In the context of soldering, it’s essential to choose a solder with good electrical conductivity to ensure efficient and reliable signal transmission.
The electrical conductivity of a solder is primarily determined by its alloy composition. Some common solder alloys and their relative electrical conductivity are:
Solder Alloy | Electrical Conductivity |
---|---|
Lead-based (60/40) | High |
Lead-free (SAC305) | Moderate |
Lead-free (SnCu) | Moderate |
Lead-free (SnBi) | Low |
When selecting solder based on electrical conductivity, consider the following:
- The current-carrying requirements of your circuit
- The desired signal integrity and transmission speed
- Any potential trade-offs with other properties, such as mechanical strength or thermal performance
Check the Compatibility with Surface Finishes
Circuit boards often have various surface finishes on the component pads and contacts, such as HASL (Hot Air Solder Leveling), ENIG (Electroless Nickel Immersion Gold), or OSP (Organic Solderability Preservative). When choosing solder, ensure that it is compatible with the surface finishes on your board.
Compatibility issues can lead to poor wetting, weak joints, or even soldering failures. Some key considerations when evaluating compatibility include:
- The wetting ability of the solder on the specific surface finish
- The potential for intermetallic compound formation
- Any temperature sensitivity or thermal limitations of the surface finish
Evaluate the Thermal Performance
Thermal performance refers to how well the solder joint conducts heat and maintains its integrity under varying temperature conditions. This is particularly important for applications where the circuit board is exposed to high temperatures or thermal cycling.
Factors that influence the thermal performance of a solder include:
- The alloy composition and its thermal conductivity
- The coefficient of thermal expansion (CTE) of the solder and the joined materials
- The size and geometry of the solder joint
- The presence of any thermal stresses or gradients
When selecting solder based on thermal performance, consider the following:
- The expected operating temperature range of your circuit board
- Any potential thermal cycling or shock conditions
- The thermal management requirements of your components and system
Consider the Environmental Impact
With the increasing focus on environmental sustainability, it’s essential to consider the ecological impact of the solder you choose. Lead-based solders, while once popular, have been largely phased out due to their toxicity and potential for environmental contamination.
When selecting solder, consider the following environmental factors:
- The presence of any hazardous substances, such as lead or cadmium
- The recyclability and disposal requirements of the solder
- Any regulatory compliance requirements, such as RoHS (Restriction of Hazardous Substances) or REACH (Registration, Evaluation, Authorization, and Restriction of Chemicals)
Opting for lead-free solders, such as SAC or SnCu alloys, can help reduce the environmental impact of your electronics manufacturing process.
Assess the Cost and Availability
Finally, when choosing solder for your circuit board, consider the cost and availability of the specific alloy or formulation. While some specialized solders may offer superior performance in certain aspects, they may also come with a higher price tag or limited availability.
When evaluating cost and availability, consider the following:
- The volume and frequency of your soldering needs
- Any potential supply chain constraints or lead times
- The trade-offs between performance and cost for your specific application
It’s essential to strike a balance between performance, reliability, and cost-effectiveness when selecting solder for your circuit board project.
FAQ
1. What is the most common lead-free solder alloy?
The most common lead-free solder alloy is SAC305, which consists of 96.5% tin (Sn), 3% silver (Ag), and 0.5% copper (Cu).
2. Can I use lead-based solder for RoHS-compliant products?
No, lead-based solders are not permitted for use in RoHS-compliant products. You must use lead-free alternatives to ensure compliance with the regulation.
3. What is the difference between rosin-core and acid-core solder?
Rosin-core solder contains a flux core that helps to clean and prepare the metal surfaces for soldering, making it suitable for electrical connections. Acid-core solder, on the other hand, contains an acidic flux that is primarily used for plumbing and should not be used for electrical soldering.
4. How does the melting point of solder affect the soldering process?
The melting point of solder determines the temperature at which it transitions from a solid to a liquid state. It’s crucial to choose a solder with a melting point that is appropriate for the components and materials you are working with to avoid damage and ensure proper joint formation.
5. Can I mix different types of solder when working on a circuit board?
It’s generally not recommended to mix different types of solder when working on a circuit board, as the different alloy compositions and properties can lead to incompatibility issues, poor joint quality, and reduced reliability. It’s best to stick with a single solder type that is well-suited for your specific application.
In conclusion, choosing the best solder for your circuit board project involves considering a range of factors, including the type of solder, melting point, wetting ability, mechanical strength, electrical conductivity, compatibility with surface finishes, thermal performance, environmental impact, cost, and availability. By carefully evaluating these factors and selecting a solder that balances performance, reliability, and cost-effectiveness, you can ensure the success and longevity of your electronic assemblies.
No responses yet