1. Solder Bridges
Solder bridges are one of the most common PCB Assembly Failures. They occur when excess solder connects two or more adjacent pins or pads, creating an unintended short circuit.
Causes of Solder Bridges
- Excessive solder paste application
- Improper solder paste stencil design
- Incorrect reflow oven temperature profile
- Poor component placement accuracy
Prevention Methods
- Optimize solder paste stencil design and aperture sizes
- Ensure proper solder paste application using automated dispensing systems
- Implement strict process controls for reflow oven temperature profiles
- Use automated optical inspection (AOI) systems to detect solder bridges
2. Cold Solder Joints
Cold solder joints occur when the solder fails to melt and flow properly, resulting in a weak and unreliable connection between the component and the PCB.
Causes of Cold Solder Joints
- Insufficient heat during the soldering process
- Contaminated or oxidized component leads or PCB pads
- Improper solder paste composition
- Incorrect reflow oven temperature profile
Prevention Methods
- Ensure proper reflow oven temperature profiles and conveyor speed
- Use high-quality solder paste with the appropriate composition
- Implement strict process controls for component storage and handling
- Perform regular maintenance on reflow ovens to ensure consistent heating
3. Tombstoning
Tombstoning, also known as “Manhattan effect” or “Stonehenge effect,” occurs when a surface-mount component stands up on one end due to uneven heating or surface tension during the reflow soldering process.
Causes of Tombstoning
- Uneven heating of the component during reflow soldering
- Imbalanced solder paste volume on component pads
- Incorrect component placement
- Improper pad design or sizing
Prevention Methods
- Ensure even heating during the reflow soldering process
- Optimize solder paste stencil design and aperture sizes for balanced paste volume
- Implement strict process controls for component placement accuracy
- Use automated optical inspection (AOI) systems to detect tombstoning
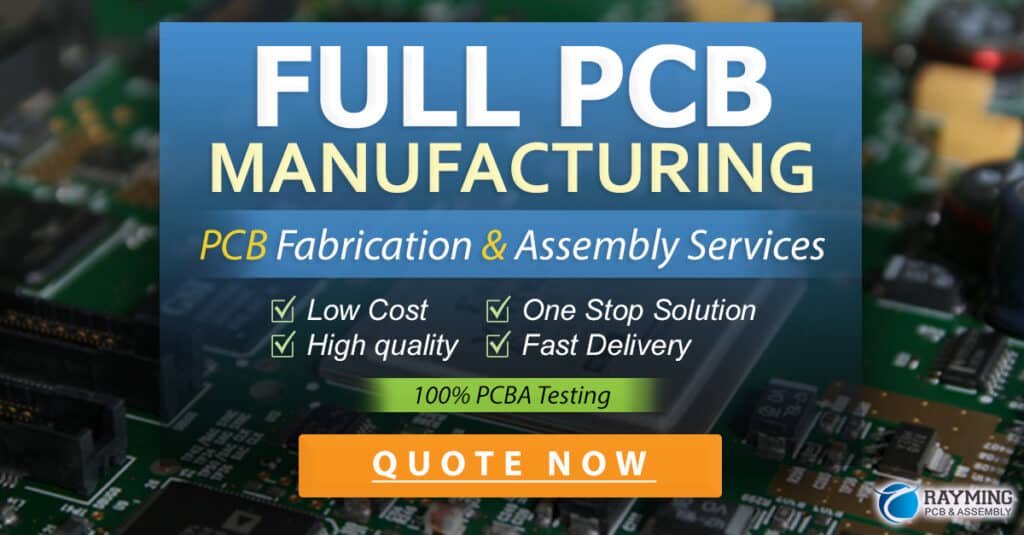
4. Lifted Pads
Lifted pads occur when the copper pad on the PCB separates from the laminate material during the assembly process, causing a break in the electrical connection.
Causes of Lifted Pads
- Excessive heat during soldering
- Poor PCB laminate material quality
- Incorrect PCB design, such as insufficient pad size or improper drill hole size
- Mechanical stress during component placement or handling
Prevention Methods
- Use high-quality PCB laminate materials
- Optimize PCB design, including pad sizes and drill hole diameters
- Ensure proper reflow oven temperature profiles and conveyor speed
- Implement gentle handling procedures during component placement and PCB handling
5. Solder Mask Defects
Solder mask defects can lead to short circuits, solder bridging, or poor adhesion of components to the PCB.
Causes of Solder Mask Defects
- Incorrect solder mask application or curing process
- Contamination of the solder mask material
- Improper solder mask design or aperture sizing
- Mechanical damage during handling or processing
Prevention Methods
- Ensure proper solder mask application and curing processes
- Use high-quality solder mask materials and store them properly
- Optimize solder mask design and aperture sizes
- Implement gentle handling procedures during PCB processing
6. Component Misalignment
Component misalignment occurs when a component is not placed accurately on the PCB, leading to poor connections or mechanical instability.
Causes of Component Misalignment
- Incorrect component placement programming
- Mechanical issues with pick-and-place machines
- Poor quality or damaged component packaging
- Incorrect PCB design, such as improper pad sizing or spacing
Prevention Methods
- Ensure accurate component placement programming and machine calibration
- Perform regular maintenance on pick-and-place machines
- Use high-quality components and inspect them for damage before assembly
- Optimize PCB design for proper pad sizing and spacing
7. Insufficient Solder
Insufficient solder can lead to weak or unreliable connections between components and the PCB.
Causes of Insufficient Solder
- Incorrect solder paste stencil design or aperture sizing
- Poor solder paste quality or improper storage
- Insufficient solder paste application
- Incorrect reflow oven temperature profile
Prevention Methods
- Optimize solder paste stencil design and aperture sizes
- Use high-quality solder paste and store it properly
- Ensure proper solder paste application using automated dispensing systems
- Implement strict process controls for reflow oven temperature profiles
8. Flux Residue
Flux residue can cause corrosion, poor adhesion, or electrical leakage if not properly cleaned after the soldering process.
Causes of Flux Residue
- Insufficient cleaning after soldering
- Incorrect cleaning process or materials
- Use of inappropriate flux for the application
- Excessive flux application
Prevention Methods
- Ensure proper cleaning processes and materials are used after soldering
- Select appropriate flux for the specific application and process
- Optimize flux application to minimize excess
- Implement strict process controls for post-soldering cleaning
9. Electrostatic Discharge (ESD) Damage
ESD damage can cause immediate or latent failures in sensitive electronic components.
Causes of ESD Damage
- Improper handling of sensitive components
- Insufficient ESD protection in the manufacturing environment
- Lack of proper grounding for personnel and equipment
- Use of non-ESD-safe materials and tools
Prevention Methods
- Implement comprehensive ESD protection measures in the manufacturing environment
- Ensure proper grounding of personnel and equipment
- Use ESD-safe materials, tools, and packaging
- Provide regular ESD training for all personnel involved in PCB assembly
FAQ
-
What are the most common PCB assembly failures?
The most common PCB assembly failures include solder bridges, cold solder joints, tombstoning, lifted pads, and component misalignment. -
How can I prevent solder bridges in my PCB assembly process?
To prevent solder bridges, optimize your solder paste stencil design and aperture sizes, ensure proper solder paste application using automated dispensing systems, implement strict process controls for reflow oven temperature profiles, and use automated optical inspection (AOI) systems to detect solder bridges. -
What causes tombstoning in surface-mount components?
Tombstoning can be caused by uneven heating of the component during reflow soldering, imbalanced solder paste volume on component pads, incorrect component placement, or improper pad design or sizing. -
How can I minimize the risk of ESD damage in my PCB assembly process?
To minimize the risk of ESD damage, implement comprehensive ESD protection measures in the manufacturing environment, ensure proper grounding of personnel and equipment, use ESD-safe materials, tools, and packaging, and provide regular ESD training for all personnel involved in PCB assembly. -
What steps can I take to prevent insufficient solder in my PCB assembly?
To prevent insufficient solder, optimize your solder paste stencil design and aperture sizes, use high-quality solder paste and store it properly, ensure proper solder paste application using automated dispensing systems, and implement strict process controls for reflow oven temperature profiles.
PCB Assembly Failure | Causes | Prevention Methods |
---|---|---|
Solder Bridges | – Excessive solder paste application – Improper solder paste stencil design – Incorrect reflow oven temperature profile – Poor component placement accuracy |
– Optimize solder paste stencil design and aperture sizes – Ensure proper solder paste application using automated dispensing systems – Implement strict process controls for reflow oven temperature profiles – Use automated optical inspection (AOI) systems to detect solder bridges |
Cold Solder Joints | – Insufficient heat during the soldering process – Contaminated or oxidized component leads or PCB pads – Improper solder paste composition – Incorrect reflow oven temperature profile |
– Ensure proper reflow oven temperature profiles and conveyor speed – Use high-quality solder paste with the appropriate composition – Implement strict process controls for component storage and handling – Perform regular maintenance on reflow ovens to ensure consistent heating |
Tombstoning | – Uneven heating of the component during reflow soldering – Imbalanced solder paste volume on component pads – Incorrect component placement – Improper pad design or sizing |
– Ensure even heating during the reflow soldering process – Optimize solder paste stencil design and aperture sizes for balanced paste volume – Implement strict process controls for component placement accuracy – Use automated optical inspection (AOI) systems to detect tombstoning |
By understanding the common PCB assembly failures, their causes, and prevention methods, you can take proactive steps to minimize the risk of these issues in your manufacturing process. Implementing strict process controls, using high-quality materials, and investing in automated inspection systems can help you achieve more reliable and consistent PCB assembly results.
No responses yet