Motor Controller Essentials
Motor controllers are essential components in various applications, from industrial automation to robotics and electric vehicles. They play a crucial role in controlling the speed, torque, and direction of electric motors, ensuring precise and efficient operation. In this article, we will delve into the key aspects of motor controllers, providing you with a comprehensive understanding of their functionality and importance.
1. What is a Motor Controller?
A motor controller is an electronic device that regulates the performance of an electric motor by adjusting the electrical power supplied to it. It acts as an intermediary between the power source and the motor, allowing users to control the motor’s speed, torque, and direction. Motor controllers come in different types and sizes, depending on the specific application and the type of motor being controlled.
Types of Motor Controllers
Type | Description |
---|---|
DC Motor Controllers | Used to control DC motors by adjusting the voltage or current supplied to the motor. |
AC Motor Controllers | Used to control AC motors by varying the frequency and voltage of the power supplied to the motor. |
Stepper Motor Controllers | Used to control stepper motors, providing precise positioning and speed control. |
Servo Motor Controllers | Used to control servo motors, offering accurate position, speed, and torque control. |
2. How Does a Motor Controller Work?
Motor controllers work by manipulating the electrical power supplied to the motor based on user inputs or predefined parameters. They typically consist of power electronics components, such as transistors, MOSFETs, or IGBTs, which act as switches to regulate the flow of electricity to the motor.
The basic working principle of a motor controller involves the following steps:
-
Input Signal: The motor controller receives an input signal, either from a user interface or a control system, indicating the desired motor behavior (e.g., speed, direction, or torque).
-
Signal Processing: The controller processes the input signal and determines the appropriate power output required to achieve the desired motor performance.
-
Power Modulation: The power electronics components in the controller modulate the electrical power supplied to the motor by rapidly switching on and off. This process is known as pulse-width modulation (PWM) and allows for precise control over the motor’s speed and torque.
-
Feedback Control: Many motor controllers incorporate feedback mechanisms, such as encoders or sensors, to monitor the motor’s actual performance. This feedback is used to make real-time adjustments to the power output, ensuring accurate and stable motor operation.
3. Benefits of Using Motor Controllers
Implementing motor controllers offers several significant benefits, including:
-
Precise Speed and Torque Control: Motor controllers enable accurate and responsive control over the motor’s speed and torque, allowing for smooth and efficient operation in various applications.
-
Energy Efficiency: By optimizing the power supplied to the motor based on the specific requirements, motor controllers help reduce energy consumption and improve overall system efficiency.
-
Protection and Safety: Motor controllers often incorporate protection features, such as overcurrent, overvoltage, and thermal protection, to safeguard the motor and the control system from potential damage.
-
Flexibility and Programmability: Many modern motor controllers offer programmable functionality, allowing users to customize the controller’s behavior to suit specific application needs.
4. Selecting the Right Motor Controller
Choosing the appropriate motor controller for your application is crucial to ensure optimal performance and reliability. Consider the following factors when selecting a motor controller:
-
Motor Type: Ensure that the controller is compatible with the type of motor you are using (e.g., DC, AC, stepper, or servo).
-
Power Rating: Select a controller that can handle the power requirements of your motor, considering factors such as voltage, current, and peak power demands.
-
Control Features: Determine the specific control features you require, such as speed control, position control, or torque control, and choose a controller that offers those capabilities.
-
Communication Interfaces: Consider the communication interfaces needed for your application, such as analog inputs, digital inputs/outputs, or communication protocols like RS-485 or CAN.
-
Environmental Factors: Take into account the operating environment of your application, including temperature range, humidity, and vibration, and select a controller that can withstand those conditions.
5. Motor Controller Configurations
Motor controllers can be configured in different ways to suit specific application requirements. Some common configurations include:
-
Open-Loop Control: In an open-loop configuration, the controller sends control signals to the motor without receiving feedback about the motor’s actual performance. This configuration is simpler but may lack precision and responsiveness.
-
Closed-Loop Control: Closed-loop control involves the use of feedback sensors to monitor the motor’s performance and make real-time adjustments. This configuration offers better accuracy and stability but requires additional components and complexity.
-
Cascaded Control: Cascaded control involves multiple control loops working together to achieve precise motor control. For example, an outer loop may control the motor’s position, while an inner loop controls the motor’s speed or torque.
6. Motor Controller Programming and Tuning
To achieve optimal motor performance, motor controllers often require programming and tuning. This process involves setting various parameters, such as acceleration and deceleration rates, current limits, and feedback gains, to match the specific requirements of the application.
Many motor controllers come with software tools or configuration interfaces that allow users to program and tune the controller easily. These tools often provide a user-friendly interface for setting parameters, monitoring performance, and troubleshooting issues.
When programming and tuning a motor controller, consider the following tips:
-
Start with Conservative Settings: Begin with conservative parameter values and gradually adjust them to achieve the desired performance. This approach helps prevent unexpected behavior or damage to the motor or controller.
-
Understand the Application Requirements: Clearly define the specific requirements of your application, such as speed range, acceleration, and load characteristics, and tune the controller accordingly.
-
Monitor and Optimize: Use monitoring tools or feedback data to observe the motor’s performance during operation. Optimize the controller settings based on the observed behavior to achieve the best possible performance.
7. Motor Controller Safety and Protection
Ensuring the safety and protection of the motor and the control system is crucial in any application. Motor controllers often incorporate various safety and protection features to prevent damage and ensure reliable operation. Some common safety and protection features include:
-
Overcurrent Protection: Motor controllers can detect and limit excessive current drawn by the motor, preventing damage to the motor windings and the controller itself.
-
Overvoltage Protection: Controllers can protect against voltage spikes or surges that may occur in the power supply, preventing damage to the electronic components.
-
Thermal Protection: Many controllers include temperature sensors to monitor the controller’s internal temperature and the motor’s temperature. If the temperature exceeds a safe threshold, the controller can take protective actions, such as reducing the power output or shutting down the system.
-
Short Circuit Protection: Motor controllers can detect and protect against short circuits in the motor or the wiring, preventing damage and potential fire hazards.
8. Motor Controller Maintenance and Troubleshooting
Regular maintenance and timely troubleshooting are essential to ensure the long-term reliability and performance of motor controllers. Some key maintenance and troubleshooting tips include:
-
Regular Inspection: Periodically inspect the motor controller for any signs of physical damage, loose connections, or excessive heat buildup. Address any issues promptly to prevent further damage.
-
Cleaning and Cooling: Ensure that the controller and its surrounding area are clean and free from dust, dirt, or debris. Maintain adequate cooling to prevent overheating and ensure optimal performance.
-
Parameter Backup: Regularly backup the controller’s configuration parameters to facilitate quick recovery in case of unexpected issues or controller replacement.
-
Diagnostic Tools: Utilize diagnostic tools or software provided by the controller manufacturer to monitor performance, identify faults, and troubleshoot issues effectively.
-
Spare Parts: Keep critical spare parts on hand, such as fuses, power electronics components, or communication modules, to minimize downtime in case of component failure.
Frequently Asked Questions (FAQ)
-
What is the difference between a motor controller and a motor drive?
A motor controller is a broader term that encompasses devices that control and regulate the performance of electric motors. A motor drive, on the other hand, specifically refers to a power electronic device that converts electrical power to drive an electric motor. In many cases, the terms “motor controller” and “motor drive” are used interchangeably. -
Can a motor controller be used with any type of motor?
No, motor controllers are designed to work with specific types of motors. It is essential to choose a controller that is compatible with the motor type being used, such as DC, AC, stepper, or servo motors. Using an incompatible controller can result in poor performance or even damage to the motor or controller. -
How do I determine the power rating required for my motor controller?
To determine the appropriate power rating for your motor controller, consider the power requirements of your motor, including the voltage, current, and peak power demands. The controller should be capable of handling the maximum power requirements of the motor with an adequate safety margin. Consult the motor’s datasheet or specifications to determine its power requirements. -
Can I use a motor controller in harsh environmental conditions?
Motor controllers are available in various designs and ratings to suit different environmental conditions. When selecting a controller for harsh environments, consider factors such as the operating temperature range, humidity, and vibration resistance. Look for controllers with appropriate enclosure ratings (e.g., IP ratings) and protective features suitable for your specific application. -
What should I do if my motor controller is not performing as expected?
If your motor controller is not performing as expected, first check for any obvious issues, such as loose connections, damaged wiring, or tripped protection devices. Consult the controller’s manual or troubleshooting guide for specific diagnostic procedures. Use diagnostic tools or software provided by the manufacturer to identify faults or abnormal behavior. If the issue persists, contact the manufacturer’s technical support or a qualified technician for assistance.
Conclusion
Motor controllers play a vital role in enabling precise and efficient control of electric motors in various applications. By understanding the essentials of motor controllers, including their working principles, benefits, selection criteria, configurations, programming, safety features, and maintenance requirements, you can effectively integrate them into your projects and optimize motor performance.
Remember to carefully consider your application requirements, choose compatible controllers, and follow best practices for programming, tuning, and maintenance to ensure reliable and efficient motor operation. With the right motor controller and proper implementation, you can unlock the full potential of your electric motors and achieve successful outcomes in your applications.
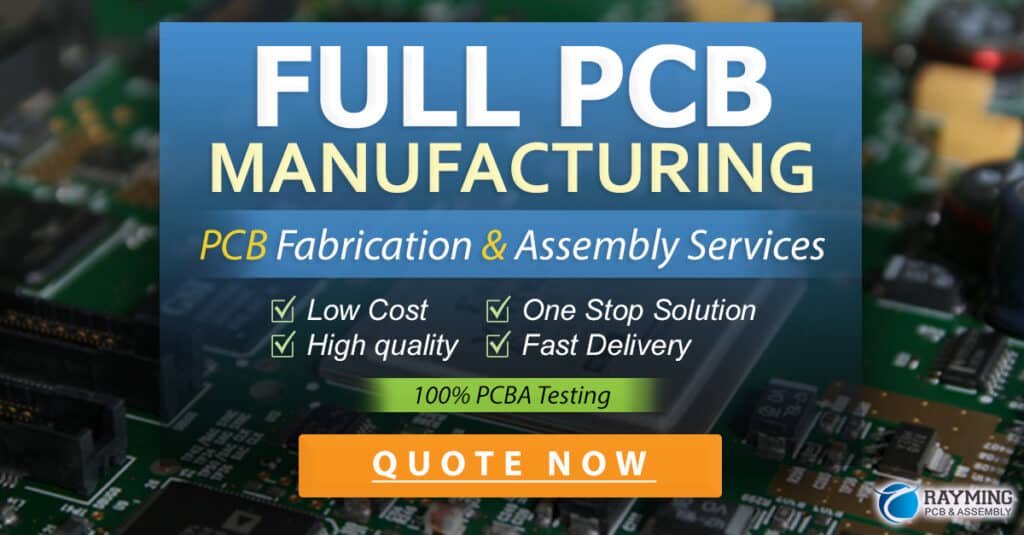
No responses yet