Introduction
When it comes to designing high-performance printed circuit boards (PCBs), Rogers materials have become a popular choice among engineers and manufacturers. Rogers PCBs offer superior electrical properties, excellent thermal management, and reliable mechanical stability, making them ideal for demanding applications such as telecommunications, aerospace, and defense.
To maximize the performance of your Rogers PCB design, it is essential to consider various technical aspects and follow best practices. In this article, we will discuss eight technical tips that will help you design performance-driven Rogers PCBs.
Tip 1: Choose the Right Rogers Material
Understanding Rogers Material Properties
Rogers offers a wide range of materials, each with its unique properties and benefits. Some of the most commonly used Rogers materials include:
Material | Dielectric Constant | Dissipation Factor | Thermal Conductivity (W/m·K) |
---|---|---|---|
RO4003C | 3.38 | 0.0027 | 0.71 |
RO4350B | 3.48 | 0.0037 | 0.69 |
RO3003 | 3.00 | 0.0013 | 0.50 |
RT/duroid 5880 | 2.20 | 0.0009 | 0.20 |
When selecting a Rogers material for your PCB design, consider the following factors:
- Dielectric constant: A lower dielectric constant reduces signal propagation delay and improves signal integrity.
- Dissipation factor: A lower dissipation factor minimizes signal loss and enhances power efficiency.
- Thermal conductivity: Higher thermal conductivity enables better heat dissipation and prevents thermal-related issues.
Matching Material to Application Requirements
Choose the Rogers material that best suits your application’s requirements. For example:
- High-frequency applications (e.g., 5G, mmWave): RO4003C or RO4350B
- Low-loss applications (e.g., radar, satellite): RT/duroid 5880
- Cost-sensitive applications: RO3003
Tip 2: Optimize Signal Integrity
Impedance Matching
Proper impedance matching is crucial for maintaining signal integrity and minimizing reflections. When designing your Rogers PCB, ensure that the characteristic impedance of the transmission lines matches the impedance of the connected components and devices.
To achieve the desired characteristic impedance, use a PCB design tool with an integrated impedance calculator. This will help you determine the appropriate trace width, thickness, and spacing based on your chosen Rogers material and layer stackup.
Minimizing Crosstalk
Crosstalk occurs when signals from one trace interfere with signals on adjacent traces. To minimize crosstalk in your Rogers PCB design:
- Increase the spacing between traces, especially for high-speed signals
- Use guard traces or ground planes to isolate sensitive signals
- Avoid running parallel traces for long distances
- Utilize differential signaling for noise cancellation
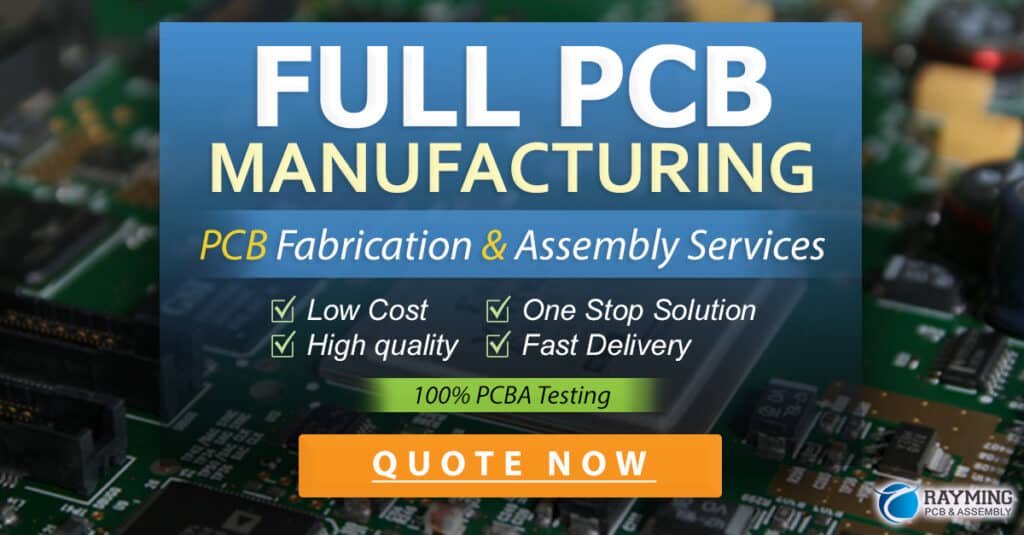
Tip 3: Manage Thermal Dissipation
Thermal Vias and Heat Spreaders
Rogers PCBs often handle high-power components that generate significant heat. To prevent thermal-related issues, such as component failure or performance degradation, incorporate thermal management techniques into your design.
Use thermal vias to transfer heat from the component to the ground plane or a dedicated heatsink. Thermal vias are plated through-holes that provide a low-resistance path for heat dissipation. Place thermal vias near high-power components and distribute them evenly to maximize heat transfer.
Consider using heat spreaders, such as copper coins or metal-core PCBs, to further enhance thermal dissipation. These spreaders help distribute heat more efficiently across the PCB surface.
Thermal Simulation and Analysis
Conduct thermal simulations and analyses to identify potential hotspots and optimize your PCB layout for better heat dissipation. Use PCB design tools with integrated thermal simulation capabilities to predict temperature distributions and identify areas that require additional cooling.
Based on the simulation results, make necessary adjustments to your design, such as repositioning components, adding more thermal vias, or incorporating heatsinks or fans.
Tip 4: Optimize Power Distribution Network (PDN)
Power Plane Placement
A well-designed power distribution network (PDN) is essential for maintaining stable power supply and minimizing noise. When designing your Rogers PCB, follow these guidelines for power plane placement:
- Place power planes on separate layers, away from sensitive signal layers
- Use a solid power plane instead of a gridded or hatched plane to reduce impedance and improve current-carrying capacity
- Minimize the distance between power planes and their respective ground planes to reduce inductance and improve decoupling
Decoupling Capacitors
Decoupling capacitors play a crucial role in stabilizing the power supply and filtering high-frequency noise. To optimize your PDN with decoupling capacitors:
- Place decoupling capacitors as close as possible to the power pins of the components they are decoupling
- Use a combination of capacitor values (e.g., 0.1 µF, 0.01 µF, and 1 nF) to target different frequency ranges
- Minimize the loop area between the capacitor and the power/ground planes to reduce parasitic inductance
Tip 5: Implement Electromagnetic Interference (EMI) Mitigation Techniques
Shielding and Grounding
Electromagnetic interference (EMI) can degrade the performance of your Rogers PCB and cause compliance issues. To mitigate EMI, implement shielding and grounding techniques:
- Use shielding enclosures or cans to contain EMI-sensitive components
- Incorporate grounding vias and gaskets to provide a low-impedance path for EMI currents
- Maintain a continuous ground plane throughout the PCB to minimize ground bounce and provide a stable reference
Filtering and Suppression
Apply filtering and suppression techniques to reduce EMI at the source and prevent its propagation:
- Use ferrite beads or common-mode chokes to suppress high-frequency noise on power lines and signal traces
- Incorporate EMI filters, such as LC or Pi filters, to attenuate conducted EMI
- Apply transient voltage suppression (TVS) diodes or varistors to protect against voltage spikes and surges
Tip 6: Follow High-Speed Design Guidelines
Length Matching and Delay Tuning
When designing high-speed circuits on your Rogers PCB, ensure that the signal paths are properly length-matched and delay-tuned. This helps maintain signal integrity and prevents timing issues.
- Match the lengths of differential pairs and parallel buses to minimize skew and ensure synchronous signal arrival
- Utilize serpentine routing or delay lines to fine-tune signal delays and compensate for path length differences
- Consider the impact of via stubs on signal propagation delay and minimize their length
Ground Stitching and Isolation
Implement ground stitching and isolation techniques to minimize crosstalk and improve signal integrity in high-speed designs:
- Use ground stitching vias to create a low-impedance connection between ground planes on different layers
- Isolate high-speed signals from other signals using ground guard traces or dedicated signal layers
- Avoid crossing high-speed signals with other signals on adjacent layers to reduce crosstalk
Tip 7: Optimize Via Design and Placement
Via Types and Sizes
Vias are essential for interconnecting different layers in your Rogers PCB. Choose the appropriate via types and sizes based on your design requirements:
- Use through-hole vias for low-frequency signals and power distribution
- Employ blind or buried vias for high-density designs and to minimize stub effects
- Select via sizes that provide a good balance between electrical performance and manufacturability
Via Placement and Spacing
Proper via placement and spacing are critical for maintaining signal integrity and manufacturability:
- Place vias as close as possible to the components they are connecting to minimize trace lengths and parasitic effects
- Ensure adequate spacing between vias to prevent manufacturing issues, such as drill wander or breakout
- Follow the recommended via-to-pad and via-to-via spacing guidelines provided by your PCB manufacturer
Tip 8: Collaborate with PCB Manufacturer
Design for Manufacturability (DFM)
To ensure the successful fabrication of your Rogers PCB, collaborate with your PCB manufacturer and follow their design for manufacturability (DFM) guidelines. DFM considerations include:
- Minimum trace width and spacing
- Minimum drill hole size and spacing
- Copper thickness and plating requirements
- Solder mask and silkscreen specifications
Prototype and Testing
Before mass production, fabricate prototype boards and conduct thorough testing to validate your design’s performance and reliability. Work closely with your PCB manufacturer to address any issues identified during prototyping and make necessary design revisions.
Engage with your manufacturer’s engineering support team to discuss any specific requirements or challenges related to your Rogers PCB design. Their expertise can help you optimize your design and avoid potential manufacturing pitfalls.
Frequently Asked Questions (FAQ)
-
Q: What are the benefits of using Rogers materials for PCB design?
A: Rogers materials offer superior electrical properties, such as low dielectric constant and low dissipation factor, which make them ideal for high-frequency and low-loss applications. They also provide excellent thermal management and mechanical stability, ensuring reliable performance in demanding environments. -
Q: How do I select the right Rogers material for my PCB design?
A: When selecting a Rogers material, consider your application’s requirements, such as frequency range, signal loss tolerance, and thermal management needs. Evaluate the material’s dielectric constant, dissipation factor, and thermal conductivity to ensure it matches your design goals. Consult with your PCB manufacturer for recommendations based on your specific requirements. -
Q: What are some key considerations for managing thermal dissipation in Rogers PCBs?
A: To manage thermal dissipation in Rogers PCBs, incorporate thermal vias near high-power components to transfer heat to the ground plane or a dedicated heatsink. Use heat spreaders, such as copper coins or metal-core PCBs, to distribute heat more efficiently. Conduct thermal simulations and analyses to identify hotspots and optimize your PCB layout for better heat dissipation. -
Q: How can I mitigate electromagnetic interference (EMI) in my Rogers PCB design?
A: To mitigate EMI, implement shielding and grounding techniques, such as using shielding enclosures, grounding vias, and maintaining a continuous ground plane. Apply filtering and suppression techniques, such as ferrite beads, EMI filters, and transient voltage suppression diodes, to reduce EMI at the source and prevent its propagation. -
Q: Why is it important to collaborate with my PCB manufacturer when designing Rogers PCBs?
A: Collaborating with your PCB manufacturer is crucial to ensure the successful fabrication of your Rogers PCB. They can provide valuable design for manufacturability (DFM) guidelines, helping you optimize your design for production. Engaging with their engineering support team can help you address specific requirements, overcome challenges, and avoid potential manufacturing issues.
Conclusion
Designing performance-driven Rogers PCBs requires careful consideration of various technical aspects, such as material selection, signal integrity, thermal management, power distribution, EMI mitigation, high-speed design, via optimization, and manufacturability.
By following the eight technical tips discussed in this article, you can optimize your Rogers PCB design to achieve superior performance, reliability, and manufacturability. Remember to choose the right Rogers material, optimize signal integrity, manage thermal dissipation, implement EMI mitigation techniques, follow high-speed design guidelines, optimize via design and placement, and collaborate closely with your PCB manufacturer.
As you embark on your Rogers PCB design journey, keep these tips in mind and consult with industry experts and your PCB manufacturer to ensure the success of your project. With the right approach and attention to detail, you can unlock the full potential of Rogers materials and create high-performance PCBs that meet the demands of your application.
No responses yet