What is an 8 Layer PCB?
An 8 layer PCB is a printed circuit board that consists of eight conductive copper layers laminated together with insulating material. These layers are interconnected through tiny holes called vias, allowing for complex routing and enhanced functionality within a compact space. The increased number of layers enables designers to create more intricate circuits and accommodate a higher component density compared to simpler 2 or 4 layer boards.
Advantages of 8 Layer PCBs
-
Enhanced Functionality: With eight layers at their disposal, designers can incorporate more complex circuitry and features into the PCB, enabling advanced applications and improved performance.
-
Increased Component Density: The additional layers allow for a higher component density, making it possible to fit more components onto a smaller board size. This is particularly beneficial for devices that require miniaturization, such as smartphones, wearables, and IoT devices.
-
Improved Signal Integrity: The use of dedicated power and ground planes in 8 layer PCBs helps to reduce electromagnetic interference (EMI) and improve signal integrity. This is crucial for high-speed and sensitive applications where signal quality is paramount.
-
Better Heat Dissipation: The increased number of layers provides more surface area for heat dissipation, allowing the PCB to manage thermal challenges more effectively. This is important for devices that generate significant heat, such as high-power electronics.
Manufacturing Process of 8 Layer PCBs
The manufacturing process of 8 layer PCBs is more complex and time-consuming compared to simpler boards. Here’s a step-by-step overview of the process:
-
Design and Layout: The PCB design is created using specialized software, taking into account the specific requirements and constraints of the 8 layer structure. The layout is carefully optimized to ensure proper signal routing, component placement, and manufacturability.
-
Layer Preparation: The individual layers of the PCB are prepared by printing the circuit patterns onto copper-clad laminates using a photolithographic process. Each layer undergoes etching to remove unwanted copper, leaving behind the desired conductive traces.
-
Lamination: The prepared layers are stacked together with insulating material between them. The stack is then subjected to high pressure and temperature in a lamination press, bonding the layers together to form a solid board.
-
Drilling: Holes are drilled through the laminated board to create vias and component mounting points. The drilling process is precisely controlled to ensure accurate hole placement and size.
-
Plating: The drilled holes are plated with copper to establish electrical connectivity between the layers. This is typically done using an electroplating process.
-
Solder Mask Application: A solder mask is applied to the outer layers of the PCB to protect the copper traces from oxidation and prevent solder bridging during the assembly process. The solder mask also provides insulation and improves the board’s appearance.
-
Surface Finish: A surface finish, such as HASL (Hot Air Solder Leveling), ENIG (Electroless Nickel Immersion Gold), or OSP (Organic Solderability Preservative), is applied to the exposed copper areas to enhance solderability and protect against corrosion.
-
Electrical Testing: The manufactured PCB undergoes thorough electrical testing to ensure that all connections are properly established and the board functions as intended. This step helps to identify any manufacturing defects or design issues.
-
Quality Control: Throughout the manufacturing process, strict quality control measures are implemented to ensure the consistency and reliability of the final product. Visual inspections, automated optical inspections (AOI), and x-ray inspections are commonly used to detect any anomalies or defects.
Challenges in 8 Layer PCB Manufacturing
While 8 layer PCBs offer numerous benefits, their manufacturing process also presents several challenges:
-
Design Complexity: Designing an 8 layer PCB requires expertise and careful consideration of signal integrity, impedance control, and power distribution. The increased complexity of the layout demands specialized knowledge and tools to ensure optimal performance.
-
Manufacturing Precision: With eight layers and numerous interconnections, the manufacturing tolerances for 8 layer PCBs are tighter compared to simpler boards. Maintaining precise alignment and registration between the layers is crucial to avoid manufacturing defects and ensure reliable functionality.
-
Cost: The manufacturing cost of 8 layer PCBs is higher than that of simpler boards due to the increased complexity, material requirements, and processing time. However, the cost can be justified for applications that demand the enhanced functionality and performance offered by 8 layer PCBs.
-
Longer Lead Times: The manufacturing process for 8 layer PCBs is more time-consuming compared to simpler boards. The additional layers and processing steps result in longer lead times, which need to be factored into production schedules.
Choosing the Right PCB Manufacturer
Selecting the right PCB manufacturer is crucial to ensure the quality, reliability, and timely delivery of your 8 layer PCBs. Here are some key factors to consider when choosing a PCB manufacturer:
-
Experience and Expertise: Look for a manufacturer with extensive experience in producing 8 layer PCBs. They should have a proven track record of successfully delivering complex, high-quality boards. Inquire about their technical capabilities, certifications, and quality control processes.
-
State-of-the-Art Facilities: A reputable PCB manufacturer should have state-of-the-art manufacturing facilities equipped with advanced equipment and technology. This ensures precise and consistent manufacturing processes, reducing the risk of defects and improving overall quality.
-
Quality Standards: Ensure that the manufacturer adheres to strict quality standards, such as ISO 9001, IPC Class 2 or 3, and UL certifications. These standards provide assurance that the manufacturer follows industry best practices and delivers products that meet the required specifications.
-
Customer Support: Good customer support is essential throughout the manufacturing process. Look for a manufacturer that offers responsive communication, technical assistance, and support in case of any issues or concerns. They should be willing to collaborate and provide guidance to optimize your PCB design for manufacturability.
-
Pricing and Lead Times: While cost is an important consideration, it should not be the sole deciding factor. Strike a balance between competitive pricing and the manufacturer’s ability to deliver high-quality PCBs within the required timeframe. Be cautious of extremely low prices, as they may compromise quality or lead to delays.
-
Scalability: If your project requires large-scale production or has the potential for future growth, consider a manufacturer that can accommodate your scaling needs. They should have the capacity and flexibility to handle increased production volumes without compromising quality or lead times.
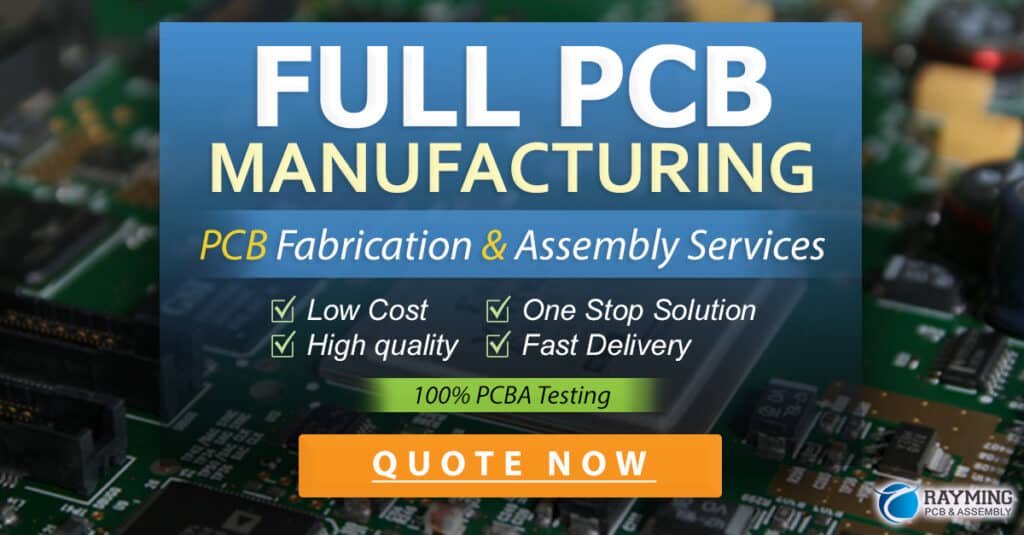
Frequently Asked Questions (FAQ)
-
Q: What are the typical applications for 8 layer PCBs?
A: 8 layer PCBs are commonly used in complex electronic devices that require high functionality and compact form factors. Some typical applications include smartphones, tablets, automotive electronics, medical devices, aerospace systems, and high-performance computing. -
Q: How long does it take to manufacture an 8 layer PCB?
A: The lead time for manufacturing an 8 layer PCB can vary depending on the complexity of the design, the manufacturer’s capacity, and the specific requirements. Typically, the lead time ranges from 2 to 4 weeks, but it can be longer for more complex designs or higher volumes. -
Q: Can 8 layer PCBs be manufactured with different materials?
A: Yes, 8 layer PCBs can be manufactured using different base materials, such as FR-4, high-Tg FR-4, or polyimide. The choice of material depends on the specific requirements of the application, including temperature tolerance, dielectric properties, and cost considerations. -
Q: How can I ensure the quality of my 8 layer PCBs?
A: To ensure the quality of your 8 layer PCBs, partner with a reputable manufacturer that follows strict quality standards and has a proven track record. Provide comprehensive design files and specifications, and communicate openly with the manufacturer throughout the process. Conduct thorough testing and inspections upon receiving the manufactured boards to verify their functionality and quality. -
Q: Are 8 layer PCBs more expensive than simpler boards?
A: Yes, 8 layer PCBs are generally more expensive than simpler 2 or 4 layer boards due to the increased complexity of the manufacturing process, material requirements, and processing time. However, the higher cost is often justified by the enhanced functionality, performance, and miniaturization benefits that 8 layer PCBs offer.
Conclusion
8 layer PCBs are a powerful solution for complex electronic devices that demand high functionality, compact form factors, and reliable performance. The manufacturing process of 8 layer PCBs is intricate and requires expertise, precision, and adherence to strict quality standards. When choosing a PCB manufacturer, consider factors such as experience, state-of-the-art facilities, quality standards, customer support, pricing, lead times, and scalability.
By partnering with a reputable 8 layer PCB manufacturer and following best practices in design and communication, you can ensure the successful production of high-quality boards that meet your specific requirements. As technology continues to advance, 8 layer PCBs will remain a crucial component in enabling the development of innovative and sophisticated electronic devices.
No responses yet