Introduction
Printed Circuit Board (PCB) assembly is a crucial process in the manufacturing of electronic devices. The cost of PCB Assembly can vary significantly depending on various factors such as the complexity of the design, the components used, and the manufacturing process. In this article, we will discuss eight key aspects that can help you estimate the cost of PCB assembly more accurately.
1. PCB Design Complexity
1.1. Board Size
The size of the PCB is one of the most significant factors that affect the assembly cost. Larger boards require more materials and take longer to assemble, resulting in higher costs. Additionally, larger boards may require special handling and packaging, which can further increase the cost.
Board Size | Relative Cost |
---|---|
Small | Low |
Medium | Medium |
Large | High |
1.2. Number of Layers
The number of layers in a PCB also has a significant impact on the assembly cost. More layers mean more complex manufacturing processes and higher material costs. The following table shows the relative cost of PCBs based on the number of layers:
Number of Layers | Relative Cost |
---|---|
1-2 | Low |
4 | Medium |
6-8 | High |
10+ | Very High |
1.3. Component Density
The component density of a PCB refers to the number of components per unit area. Higher component density means more components need to be placed and soldered, which increases the assembly time and cost. The following table shows the relative cost of PCBs based on component density:
Component Density | Relative Cost |
---|---|
Low | Low |
Medium | Medium |
High | High |
2. Component Selection
2.1. Component Type
The type of components used in a PCB can have a significant impact on the assembly cost. Some components, such as fine-pitch components or BGA (Ball Grid Array) packages, require specialized equipment and expertise to assemble, resulting in higher costs. On the other hand, using standard through-hole components can help reduce the assembly cost.
2.2. Component Availability
The availability of components can also affect the assembly cost. If a component is hard to find or has a long lead time, it can delay the assembly process and increase the overall cost. It is essential to consider component availability when designing a PCB and to choose readily available components whenever possible.
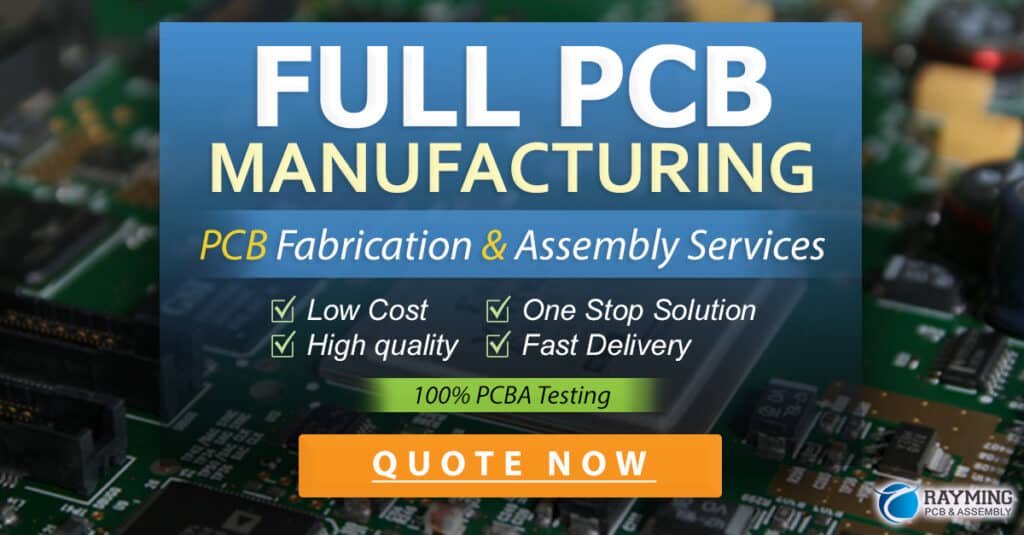
3. Manufacturing Process
3.1. Assembly Technology
The assembly technology used can significantly impact the cost of PCB assembly. Surface mount technology (SMT) is generally more cost-effective than through-hole technology (THT) for high-volume production. However, THT may be more suitable for low-volume or prototype builds.
3.2. Soldering Method
The soldering method used can also affect the assembly cost. Wave soldering is a cost-effective method for THT components, while reflow soldering is more suitable for SMT components. Hand soldering is generally more expensive and time-consuming but may be necessary for certain components or low-volume builds.
4. Order Quantity
The order quantity is another crucial factor in determining the PCB Assembly Cost. Generally, larger order quantities result in lower per-unit costs due to economies of scale. The following table shows the relative cost of PCBs based on order quantity:
Order Quantity | Relative Cost |
---|---|
1-10 | Very High |
11-100 | High |
101-500 | Medium |
501-1000 | Low |
1000+ | Very Low |
5. Quality Requirements
5.1. Testing and Inspection
The level of testing and inspection required can also impact the assembly cost. Basic visual inspection is generally included in the assembly cost, but more advanced testing, such as in-circuit testing (ICT) or functional testing, may incur additional charges. It is essential to determine the necessary level of testing based on the application and reliability requirements of the PCB.
5.2. Certifications and Standards
Certain applications may require the PCB assembly to meet specific certifications or standards, such as ISO, UL, or RoHS. Meeting these requirements may involve additional costs for materials, processes, and documentation. It is important to consider these requirements early in the design phase to avoid unexpected costs later.
6. Lead Time
The lead time for PCB assembly can also affect the overall cost. Shorter lead times may require expedited services or rush fees, which can increase the cost. On the other hand, longer lead times may allow for more cost-effective production methods or materials. It is essential to balance the required lead time with the cost considerations when planning PCB assembly.
7. Logistics and Shipping
7.1. Location
The location of the PCB assembly facility can impact the cost due to differences in labor rates, materials costs, and shipping expenses. Offshore manufacturing, such as in China or other low-cost countries, may offer lower assembly costs but may also involve longer lead times and higher shipping costs. Local manufacturing may provide faster turnaround times and easier communication but may have higher labor costs.
7.2. Shipping Method
The shipping method chosen can also affect the overall cost of PCB assembly. Faster shipping methods, such as air freight, are generally more expensive than slower options like sea freight. The choice of shipping method should be based on the required lead time and the size and weight of the PCB order.
8. Value-Added Services
Some PCB assembly providers offer value-added services that can impact the overall cost. These services may include:
- PCB design assistance
- Component sourcing and procurement
- Box build and final assembly
- Conformal coating and potting
- Custom packaging and labeling
While these services can add to the overall cost, they can also provide significant value by simplifying the supply chain and reducing the need for additional vendors or in-house resources.
FAQ
1. How can I reduce the cost of PCB assembly?
There are several ways to reduce the cost of PCB assembly, including:
- Optimizing the PCB design for manufacturability
- Choosing standard components and packages
- Increasing the order quantity to take advantage of economies of scale
- Selecting a cost-effective manufacturing process and soldering method
- Balancing lead time requirements with cost considerations
2. What is the difference between SMT and THT assembly?
Surface mount technology (SMT) involves placing components directly onto the surface of the PCB, while through-hole technology (THT) involves inserting component leads through holes in the PCB and soldering them on the opposite side. SMT is generally more cost-effective for high-volume production, while THT may be more suitable for low-volume or prototype builds.
3. How does the number of layers affect the PCB assembly cost?
The number of layers in a PCB has a significant impact on the assembly cost. More layers mean more complex manufacturing processes and higher material costs. PCBs with more layers are generally more expensive than those with fewer layers.
4. What is the impact of component availability on PCB assembly cost?
Component availability can affect the PCB assembly cost by impacting the lead time and the overall production schedule. If a component is hard to find or has a long lead time, it can delay the assembly process and increase the overall cost. Choosing readily available components can help minimize this risk.
5. How can I determine the necessary level of testing and inspection for my PCB assembly?
The necessary level of testing and inspection for PCB assembly depends on the application and reliability requirements of the PCB. Basic visual inspection is generally included in the assembly cost, but more advanced testing, such as in-circuit testing (ICT) or functional testing, may be required for critical applications. It is essential to consider the testing requirements early in the design phase and to communicate them clearly with the PCB assembly provider.
Conclusion
Estimating the cost of PCB assembly requires considering multiple aspects, including the PCB design complexity, component selection, manufacturing process, order quantity, quality requirements, lead time, logistics, and value-added services. By understanding these factors and making informed decisions based on the specific requirements of the project, it is possible to optimize the cost of PCB assembly while ensuring the necessary quality and reliability.
Effective communication with the PCB assembly provider is also crucial in managing costs and expectations. Providing clear and complete documentation, such as the bill of materials (BOM), Gerber files, and assembly instructions, can help streamline the process and avoid potential issues or delays.
Ultimately, the key to successful PCB assembly cost estimation is finding the right balance between cost, quality, and lead time based on the unique needs of each project. By carefully considering the aspects discussed in this article, designers and project managers can make informed decisions and achieve the best possible outcome for their PCB assembly projects.
No responses yet