1. Choose the Right ESC for Your Drone Build
The first critical step is selecting ESCs that are compatible with your drone frame, motors, battery, and flight controller. Key factors to consider include:
Specification | Description |
---|---|
Constant Current Rating | Maximum continuous current the ESC can handle (e.g. 30A). Must exceed the max current draw of your motor. |
Burst Current Rating | Maximum current the ESC can handle in short bursts (e.g. 40A for 10 seconds). Important for punchy acceleration. |
Supported Battery Cell Count | ESC must match your battery’s cell count (e.g. 3-4S LiPo). |
BEC (Battery Eliminator Circuit) | Some ESCs have a built-in BEC to power the flight controller and receiver. The BEC’s voltage and current rating must be sufficient. |
Programmability | More advanced ESCs allow customization of settings like timing, throttle curve, and more. |
Choose an ESC with some headroom in terms of current rating. For example, if your motor has a max continuous current draw of 20A, opt for a 30A ESC instead of a 20A one. This ensures cooler running and longer ESC lifespan.
2. Perform ESC Calibration
ESC calibration matches the ESC’s throttle range to the flight controller’s output range. It’s essential for ensuring proper response across the throttle’s full span. To calibrate:
- Remove propellers for safety
- Power on transmitter and set throttle stick to max
- Connect battery to power on ESCs and flight controller
- Wait for ESCs to emit a musical tone indicating they’ve registered the max throttle signal
- Move throttle down to zero
- ESCs will emit another tone confirming the zero throttle position
- Calibration complete, ESCs will now arm
Some ESCs use different calibration procedures, so consult your ESC’s manual for specific instructions. Recalibrate if you change transmitters, receivers, or ESCs.
3. Optimize ESC Timing
ESC timing advance affects the efficiency and performance of your motors. Higher timing can increase top-end power but also generate more heat. Lower timing is more efficient and better for throttle response.
Here are common timing ranges for different motor types:
Motor Type | Timing Range |
---|---|
Low KV Motors | 5-15 degrees |
Medium KV Motors | 15-25 degrees |
High KV Motors | 22-30 degrees |
As a general rule, start with lower timing and only increase it if you need more power. Monitor motor temps and back down timing if they get too hot. You can set timing via your ESC’s programming card or configurator.
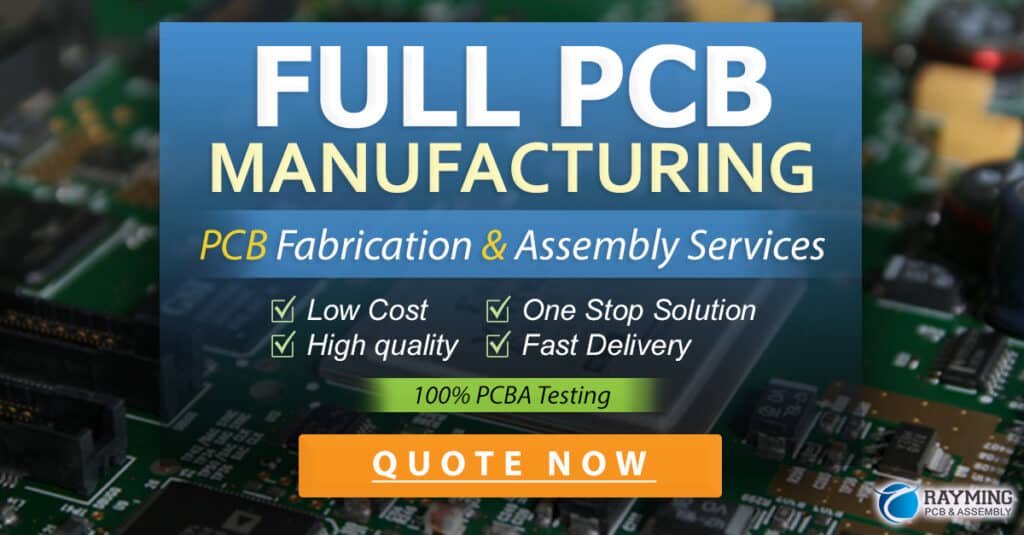
4. Dial In Motor Rotation Direction
For your drone to respond correctly to control inputs, you need to set the rotation direction of each motor. The standard configuration is:
Motor | Rotation |
---|---|
Front Left (1) | Counter-Clockwise |
Front Right (2) | Clockwise |
Rear Right (3) | Counter-Clockwise |
Rear Left (4) | Clockwise |
If a motor is spinning the wrong way, simply swap any two of the three motor wires connected to the ESC. Do not change wiring at the ESC itself.
5. Enable Active Braking
Most ESCs have an active braking feature that engages motor windings to slow the motor faster when throttle is reduced. This provides snappier throttle response and can reduce prop wash oscillations in flight.
The trade-off is active braking increases motor and ESC temperatures. If you enable active braking, start with a low setting (e.g. 25%) and monitor temps before increasing it further.
6. Sync PWM Frequency
The PWM (Pulse Width Modulated) frequency is how quickly the ESC sends power pulses to the motors. A higher PWM frequency provides smoother operation and faster acceleration.
The optimal PWM frequency depends on your motor’s switching frequency and other factors. Here are typical ranges:
Motor Type | Recommended PWM |
---|---|
Low KV | 8-16 kHz |
Medium KV | 16-24 kHz |
High KV | 24-32 kHz |
If your ESC and motors support it, enable damped light mode. This boosts PWM frequency even higher when throttle is at zero for quieter operation and faster motor deceleration.
7. Soft-Mount Your ESCs
Soft-mounting your ESCs with vibration-absorbing foam or grommets can reduce the mechanical strain and fatigue on the components. Excess vibrations can lead to premature ESC failure and cause electronic noise that interferes with your drone’s sensors and RF links.
Methods for soft-mounting ESCs include:
- Foam tape or pads between ESC and frame
- Rubber bobbins or O-rings on ESC mounting holes
- 3D printed TPU mounts
- Silicon or hot glue to decouple ESC from frame
Secure the ESC’s wires so vibrations don’t transfer to the board. You can use zip-ties or cable clips to fasten wires to the frame.
Frequently Asked Questions
What happens if I use an underrated ESC?
An ESC without sufficient current capacity for your motor will overheat and likely fail, potentially damaging your other electronics in the process. Always choose an ESC with a current rating notably higher than your motor’s max draw.
Why do I need to calibrate my ESCs?
ESC calibration ensures the full throttle range of your transmitter matches the ESC’s throttle range. If they are mismatched, you may experience dead zones at low throttle or inability to arm at zero throttle. Recalibrate ESCs whenever you change your radio system components.
Is higher timing advance always better?
No, higher ESC timing is not always ideal. While it can provide more power at top end, it reduces efficiency and generates more heat in the motors and ESCs. Only use higher timing if absolutely necessary for your application and monitor temperatures closely. High timing with an over-propped motor can easily burn out an ESC.
Can I use different ESC models and brands on the same drone?
Ideally, you should use the same make and model of ESC on all arms of your drone. This ensures consistent performance across the motors. If you must mix ESCs, at least ensure they have near-identical specs in terms of current rating, battery voltage, programming options, and supported PWM frequency. Never mix ESCs that require different firmware.
My motors get extremely hot with active braking. What should I do?
Active braking intentionally runs current through the motor windings to decelerate the motor faster. This generates heat. If your motors are getting too hot, first try lowering the active braking strength in your ESC programming. If temps are still high, you may need to disable active braking completely. Also check that your motors are not over-propped for their KV rating.
By implementing these 7 tips for optimizing your drone’s electronic speed controls, you can enhance flight performance, efficiency, and reliability. Always choose ESC hardware that matches your build’s specifications and fine-tune settings like timing and active braking to find the sweet spot for your setup. Happy flying!
No responses yet