What is PCB Panelization?
PCB Panelization is the process of grouping multiple printed circuit board designs onto a single panel for more efficient production. By placing multiple PCB designs on one larger board, manufacturers can produce a higher quantity of PCBs in less time, reducing costs.
Panelization allows for:
– Faster assembly
– Lower production costs
– Easier handling of smaller PCBs
– More efficient testing
However, panelization introduces some additional design considerations that must be accounted for. Here are 7 key things designers should know about PCB panelization design guidelines:
1. Determine the Optimum Panel Utilization
The main goal of panelization is maximizing the number of PCBs that fit on a production panel while minimizing waste. Factors to consider when determining the ideal panel utilization include:
- Individual PCB dimensions
- Spacing between boards
- Placement of tooling holes, fiducials, and test coupons
- Fabrication tolerances
- Panelization method (e.g. V-scoring, tab routing)
Designers must carefully lay out the panels to achieve the highest possible utilization. Specialized panelization software can assist with this.
2. Include Breakaway Tabs or V-Grooves for Depaneling
The individual PCBs must be separated from the panel after assembly, a process called depaneling. The two most common depaneling methods are:
-
Tab Routing – Breakaway tabs with perforations are left in the spaces between boards. After assembly, the individual PCBs can be snapped out of the panel by hand or machine along these tabs.
-
V-Scoring – Thin V-shaped grooves are cut between the boards on the panel. After assembly, the PCBs can be cleanly snapped apart along these grooves.
The panelization design must include either perforated breakaway tabs or V-score locations between the individual boards. The size and number of tabs, or the depth of the V-grooves, depends on the board thickness and material.
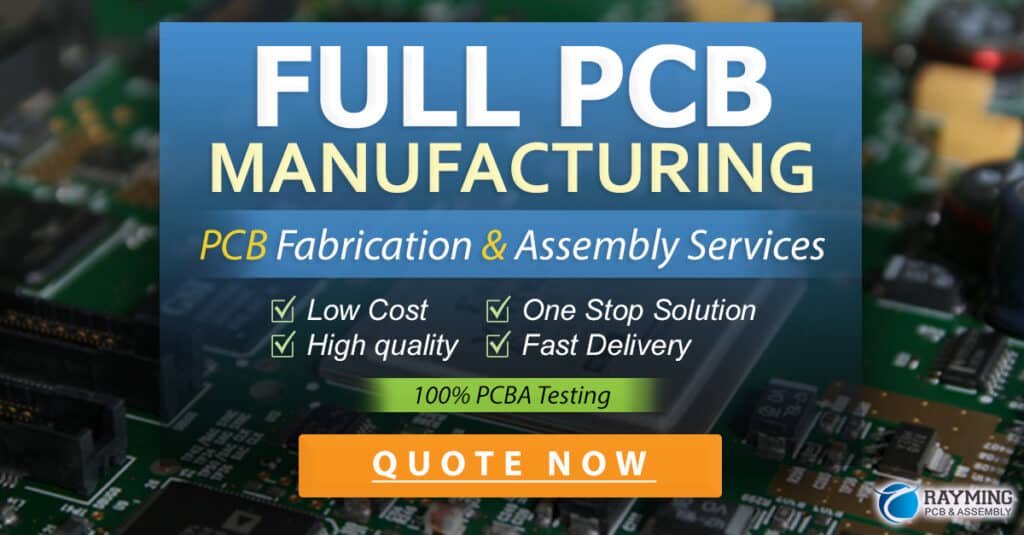
3. Provide Adequate Spacing Between Boards
Proper spacing between the individual PCBs on the production panel is critical for:
– Manufacturability
– Ease of assembly
– Reliable depaneling
– Preventing damage to components or traces
The minimum spacing between boards depends on the PCB thickness and depaneling method:
PCB Thickness | Tab Routed | V-Scored |
---|---|---|
<0.8mm | 1.5mm | 1.0mm |
0.8-1.6mm | 2.0mm | 1.5mm |
>1.6mm | 2.5mm | 2.0mm* |
*V-scoring is not recommended for boards over 1.6mm thick.
Additionally, components should be kept at least 0.3-0.5mm away from depaneling tabs or V-grooves to prevent damage.
4. Add Tooling Holes and Fiducials
Tooling holes and fiducials are used to ensure proper alignment and registration during the fabrication, assembly, and testing processes.
-
Tooling Holes – Used to align and secure the panel during drilling, routing, and assembly. Should be at least 1mm from the edge of the panel and 3mm in diameter.
-
Fiducials – Copper pads used as reference points for machine vision systems during pick-and-place assembly, AOI, and testing. Should be at least 1mm in diameter.
All panels should have at least 3 tooling holes and 2 fiducials. Larger panels may require additional holes and fiducials for stability and alignment.
5. Consider Using Panelization Sub-Rails
Sub-rails, also known as riser rails or snugger bars, are extra strips of material added to the edges or middles of production panels. They provide additional rigidity and support during assembly, which is especially helpful for thin boards (<1.2mm) or large panels (>200mm).
Sub-rails are typically 5mm wide and placed along the outer edges or center of the panel. Like the individual PCBs, sub-rails are removed after assembly by tab routing or V-scoring. While sub-rails can improve manufacturing yields, they also reduce panel utilization, so designers must weigh the trade-offs.
6. Include Test Coupons if Needed
Some PCB designs may require test coupons for in-process quality control. These are small PCBs included on the production panel that are used for:
- Destructive testing
- Microsectioning
- Solder float testing
- Ionic contamination testing
Test coupons are typically placed along the edge or corners of the panel. The number, size, and type of test coupons depends on the customer and application requirements. If test coupons are needed, they must be factored into the panelization design and panel utilization calculations.
7. Follow Fabrication DFM Guidelines
As with any PCB design, it’s important to adhere to the fabrication vendor’s design for manufacturing (DFM) guidelines when panelizing. This includes rules for:
- Minimum hole size and spacing
- Copper-to-edge and copper-to-copper clearances
- Solder mask and silkscreen tolerances
- Drill-to-copper clearances
- Controlled impedance requirements
Violating these DFM rules can lead to manufacturing issues and reduced yields. Always verify the design meets the fab vendor’s requirements before submitting for production.
FAQ
What is the main benefit of PCB panelization?
The main benefit of PCB panelization is increased manufacturing efficiency. By grouping multiple PCBs onto one panel, manufacturers can process a higher quantity of boards in less time, reducing production costs.
What are the two main methods for depaneling PCBs?
The two main depaneling methods are tab routing and V-scoring. With tab routing, perforated breakaway tabs are left between the PCBs which can be snapped apart after assembly. With V-scoring, thin V-shaped grooves are cut between the PCBs for separation.
How much space is needed between boards on a panel?
The spacing between individual PCBs on a panel depends on the board thickness and depaneling method. For tab routing, the minimum gap is 1.5-2.5mm depending on thickness. For V-scoring, the minimum is 1.0-2.0mm. More spacing may be needed for very thick boards.
What is the purpose of tooling holes and fiducials on a panel?
Tooling holes are used to align and secure the panel during fabrication and assembly. Fiducials are reference markers used by machine vision systems for accurate placement, inspection, and testing. All panels need several tooling holes and fiducials to ensure proper registration.
When should I use sub-rails on my PCB panels?
Sub-rails, or riser bars, are used to provide extra support and rigidity to panels during assembly. They are especially helpful for thin flex or rigid-flex designs under 1.2mm, as well as large panels over 200mm in size. Sub-rails improve manufacturing yields but reduce panel utilization.
Conclusion
PCB panelization is an important step in the design process that allows manufacturers to efficiently produce higher quantities of PCBs. However, it introduces additional design considerations beyond the individual board requirements.
Designers must carefully choose the placement, spacing, and depaneling methods for the PCBs on the production panel. Tooling holes, fiducials, sub-rails, and test coupons may also need to be included. Following the fab vendor’s DFM guidelines is critical.
By understanding these PCB panelization design guidelines, designers can help ensure their boards are efficiently and reliably manufactured. Advance planning and attention to detail during panelization streamlines production and reduces costs.
No responses yet