Introduction to Multilayer PCB Fabrication
Multilayer PCB fabrication is a complex process that involves the creation of printed circuit boards with multiple layers of conductive and insulating materials. These boards are essential components in various electronic devices, ranging from smartphones and computers to medical equipment and aerospace systems. While advancements in technology have made multilayer PCB fabrication more efficient and precise, several challenges can arise during the manufacturing process. This article will discuss seven common problems encountered in multilayer PCB fabrication and provide insights into addressing these issues.
1. Alignment Issues
1.1 Layer Misalignment
One of the most critical aspects of multilayer PCB fabrication is ensuring proper alignment between the various layers. Misalignment can lead to several issues, such as:
- Improper connections between layers
- Reduced electrical performance
- Increased risk of short circuits
To mitigate layer misalignment, manufacturers must employ precise registration techniques and use high-quality equipment for layer alignment.
1.2 Drill Misalignment
In addition to layer misalignment, drill misalignment can also pose significant challenges in multilayer PCB fabrication. Misaligned drill holes can result in:
- Poor electrical connections
- Structural weaknesses in the board
- Difficulty in component assembly
Manufacturers can address drill misalignment by using advanced drilling machines with high precision and implementing strict quality control measures.
2. Copper Thickness Variation
2.1 Causes of Copper Thickness Variation
Copper thickness variation is another common issue in multilayer PCB fabrication. Several factors can contribute to this problem, including:
- Inadequate control of the electroplating process
- Uneven distribution of copper during the plating process
- Inconsistencies in the etching process
2.2 Impact of Copper Thickness Variation
Copper thickness variation can have a significant impact on the performance and reliability of the PCB. Some of the consequences include:
- Altered electrical characteristics
- Reduced current-carrying capacity
- Increased risk of signal integrity issues
To minimize copper thickness variation, manufacturers must implement strict process controls and regularly monitor the electroplating and etching processes.
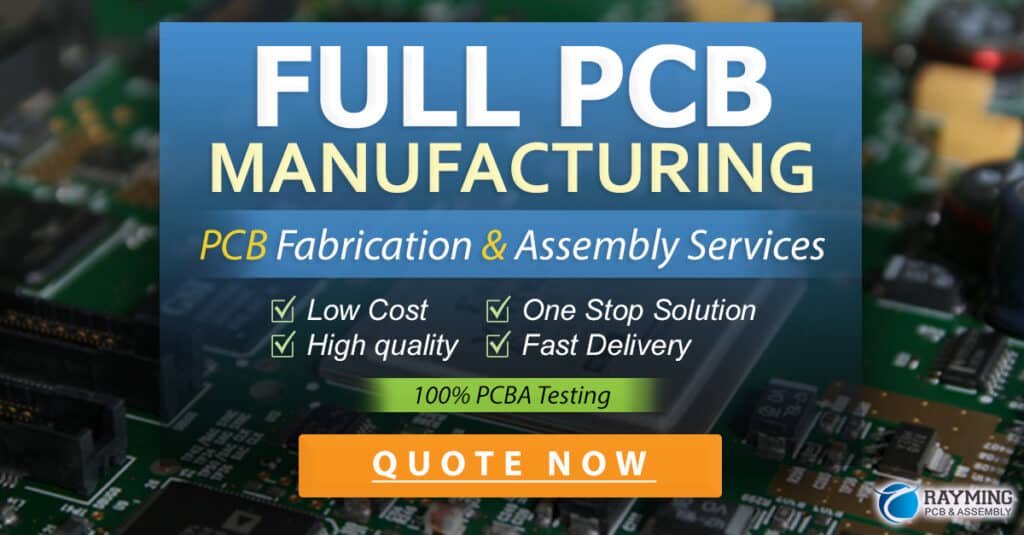
3. Delamination
3.1 Causes of Delamination
Delamination is a severe problem that occurs when the layers of a multilayer PCB separate from each other. This issue can be caused by several factors, such as:
- Improper bonding between layers
- Incompatible materials
- Excessive heat or stress during the manufacturing process
3.2 Consequences of Delamination
Delamination can have severe consequences for the functionality and longevity of the PCB, including:
- Complete failure of the board
- Compromised structural integrity
- Increased risk of short circuits and signal loss
To prevent delamination, manufacturers must carefully select compatible materials, optimize the bonding process, and control the temperature and pressure during lamination.
4. Solder Mask Issues
4.1 Solder Mask Adhesion Problems
Solder mask is a protective layer applied to the surface of the PCB to prevent solder bridges and short circuits. However, solder mask adhesion problems can arise due to:
- Contamination on the PCB surface
- Incompatible solder mask materials
- Improper curing of the solder mask
4.2 Solder Mask Alignment Errors
Solder mask alignment errors can also occur during the fabrication process, leading to:
- Exposed copper areas
- Solder bridging between pads
- Difficulty in component assembly
To address solder mask issues, manufacturers must ensure proper surface preparation, select compatible solder mask materials, and implement precise alignment techniques.
5. Etching Problems
5.1 Over-etching
Over-etching is a common issue in multilayer PCB fabrication, where the etching process removes more copper than intended. This can lead to:
- Reduced trace widths
- Increased resistance
- Potential open circuits
5.2 Under-etching
Under-etching, on the other hand, occurs when insufficient copper is removed during the etching process. This can result in:
- Short circuits between traces
- Reduced spacing between features
- Decreased manufacturing yield
To minimize etching problems, manufacturers must optimize the etching process parameters, such as etchant concentration, temperature, and exposure time, and regularly monitor the process for consistency.
6. Via Formation Challenges
6.1 Via Drilling Accuracy
Via formation is a critical step in multilayer PCB fabrication, as it enables electrical connections between layers. One of the main challenges in via formation is maintaining drilling accuracy, which can be affected by:
- Drill bit wear
- Vibrations during drilling
- Inadequate drill parameter settings
6.2 Via Plating Uniformity
Another issue related to via formation is ensuring uniform plating inside the vias. Non-uniform plating can lead to:
- Increased resistance
- Weak connections between layers
- Potential reliability issues
To overcome via formation challenges, manufacturers must use high-quality drill bits, optimize drilling parameters, and implement advanced plating techniques, such as pulse plating or reverse pulse plating.
7. Material Selection and Compatibility
7.1 Substrate Material Selection
Selecting the appropriate substrate material is crucial for the performance and reliability of the multilayer PCB. Common substrate materials include:
- FR-4
- High-Tg FR-4
- Polyimide
- Ceramic
Each material has its own set of properties, such as dielectric constant, thermal stability, and mechanical strength, which must be carefully considered based on the application requirements.
7.2 Copper Foil Selection
The choice of copper foil also plays a significant role in multilayer PCB fabrication. Factors to consider when selecting copper foil include:
- Thickness
- Surface roughness
- Tensile strength
- Elongation
Compatibility between the substrate material and copper foil is essential to ensure proper bonding and prevent delamination issues.
Frequently Asked Questions (FAQ)
-
What is the typical turnaround time for multilayer PCB fabrication?
The turnaround time for multilayer PCB fabrication varies depending on the complexity of the design, the number of layers, and the manufacturer’s capacity. Generally, lead times can range from a few days to several weeks. -
How can I ensure the reliability of my multilayer PCB design?
To ensure the reliability of your multilayer PCB design, consider the following: - Adhere to recommended design guidelines and rules
- Select appropriate materials based on the application requirements
- Perform thorough design reviews and simulations
-
Work closely with your PCB manufacturer to address any potential issues
-
What are the advantages of using multilayer PCBs over single-layer PCBs?
Multilayer PCBs offer several advantages over single-layer PCBs, including: - Increased circuit density and functionality
- Improved signal integrity and reduced electromagnetic interference
- Better thermal management and mechanical stability
-
Reduced overall size and weight of the electronic device
-
How can I minimize the cost of multilayer PCB fabrication?
To minimize the cost of multilayer PCB fabrication, consider the following strategies: - Optimize your design for manufacturability
- Use standard materials and processes whenever possible
- Minimize the number of layers and drill holes
-
Order in larger quantities to take advantage of volume discounts
-
What are the common testing methods for multilayer PCBs?
Common testing methods for multilayer PCBs include: - Electrical continuity and isolation testing
- Microsectioning and cross-sectioning
- Thermal stress testing
- Impedance and capacitance testing
- X-ray inspection and automated optical inspection (AOI)
Conclusion
Multilayer PCB fabrication is a complex process that requires careful planning, design, and execution to ensure the production of high-quality and reliable boards. By understanding the common problems that can arise during the fabrication process, such as alignment issues, copper thickness variation, delamination, solder mask issues, etching problems, via formation challenges, and material compatibility, manufacturers can take proactive steps to mitigate these issues and improve the overall quality of their products. Implementing strict process controls, using advanced manufacturing techniques, and collaborating closely with clients to address design and material selection considerations can help minimize the occurrence of these problems and ensure the successful production of multilayer PCBs for a wide range of applications.
No responses yet