Understanding PCB Conformal Coating
Before diving into the factors that determine the ideal thickness of PCB conformal coating, let’s briefly understand what conformal coating is and its purpose.
What is PCB Conformal Coating?
PCB conformal coating is a thin, protective layer applied to the surface of a printed circuit board. This coating conforms to the contours of the board, providing a barrier against environmental hazards. The coating material can be acrylic, silicone, urethane, or other specialty polymers, each with its own unique properties.
Purpose of Conformal Coating
The primary purpose of conformal coating is to protect the PCB from various environmental factors that can cause damage or malfunction. These factors include:
- Moisture and humidity
- Dust and debris
- Chemical contamination
- Extreme temperatures
- Mechanical stress
By applying a conformal coating, the PCB’s lifespan is extended, and its reliability is enhanced.
Factors Influencing PCB Conformal Coating Ideal Thickness
Now, let’s explore the seven important factors that determine the ideal thickness of PCB conformal coating.
1. Environmental Conditions
The environmental conditions in which the PCB will operate play a significant role in determining the ideal coating thickness. PCBs exposed to harsh environments, such as high humidity, corrosive chemicals, or extreme temperatures, require a thicker coating for adequate protection. On the other hand, PCBs operating in mild environments may only need a thin layer of coating.
Environment | Recommended Thickness |
---|---|
Mild | 25-50 microns |
Moderate | 50-75 microns |
Harsh | 75-100 microns |
Extreme | 100+ microns |
2. Type of Conformal Coating Material
The type of conformal coating material used also influences the ideal thickness. Different coating materials have varying properties, such as dielectric strength, moisture resistance, and thermal stability. Some common conformal coating materials and their recommended thicknesses are:
Material | Recommended Thickness |
---|---|
Acrylic | 25-75 microns |
Silicone | 50-200 microns |
Urethane | 25-130 microns |
Parylene | 5-50 microns |
It’s essential to choose a coating material that is compatible with the PCB’s components and meets the specific requirements of the application.
3. PCB Components and Geometry
The components and geometry of the PCB also play a role in determining the ideal coating thickness. PCBs with tall components or intricate geometries may require a thicker coating to ensure complete coverage and protection. However, applying too thick a coating can lead to issues such as component interference or reduced heat dissipation.
To determine the ideal thickness, consider the following:
- Height of the tallest component
- Spacing between components
- Presence of fine-pitch components
- Existence of under-component areas
A general rule of thumb is to apply a coating thickness that is 25-50% of the height of the tallest component.
4. Application Method
The method used to apply the conformal coating can also influence the ideal thickness. Common application methods include:
- Spray coating
- Brush coating
- Dip coating
- Selective coating
Each method has its own advantages and limitations in terms of coating thickness control and uniformity. For example, spray coating allows for precise thickness control but may result in thinner coatings compared to dip coating.
Application Method | Typical Thickness Range |
---|---|
Spray Coating | 25-100 microns |
Brush Coating | 50-100 microns |
Dip Coating | 50-150 microns |
Selective Coating | 25-100 microns |
It’s important to choose an application method that ensures consistent and appropriate coating thickness across the entire PCB.
5. Curing Process
The curing process of the conformal coating also plays a role in determining the ideal thickness. Different coating materials require specific curing conditions, such as temperature and duration, to achieve optimal properties.
For example, acrylic coatings typically require a lower curing temperature compared to urethane coatings. Insufficient curing can result in a coating that is too soft or prone to damage, while excessive curing can lead to embrittlement and cracking.
Follow the manufacturer’s recommended curing guidelines to ensure the coating achieves its desired thickness and properties.
6. Regulatory Requirements
Depending on the industry and application, there may be specific regulatory requirements that dictate the minimum or maximum conformal coating thickness. For example, in the aerospace industry, the IPC-CC-830B standard provides guidelines for conformal coating thickness based on the environmental classification.
Class | Environment | Recommended Thickness |
---|---|---|
1 | Mild | 25-50 microns |
2 | Moderate | 50-75 microns |
3 | Harsh | 75-100 microns |
It’s crucial to be aware of and comply with any relevant regulatory requirements to ensure the PCB meets the necessary standards.
7. Cost Considerations
Finally, cost considerations must be taken into account when determining the ideal conformal coating thickness. Thicker coatings require more material and may incur higher costs. However, skimping on coating thickness to save costs can compromise the PCB’s protection and lead to premature failure.
It’s essential to strike a balance between adequate protection and cost-effectiveness. Consider the following factors:
- Material cost per unit volume
- Application process costs
- Rework and repair costs due to insufficient protection
By optimizing the coating thickness based on the specific requirements of the application, you can achieve reliable protection while minimizing unnecessary costs.
Frequently Asked Questions (FAQ)
-
Q: What is the typical thickness range for PCB conformal coatings?
A: The typical thickness range for PCB conformal coatings varies depending on the material and application method. Generally, it falls between 25 and 150 microns. -
Q: Can I apply multiple layers of conformal coating to increase thickness?
A: Yes, multiple layers of conformal coating can be applied to increase the overall thickness. However, it’s important to allow sufficient drying or curing time between layers and ensure compatibility between the layers. -
Q: How do I measure the thickness of the applied conformal coating?
A: Conformal coating thickness can be measured using various methods, such as microscopy, eddy current testing, or ultrasonic thickness gauges. Some coating materials may require specific measurement techniques. -
Q: What happens if the conformal coating is too thin?
A: If the conformal coating is too thin, it may not provide adequate protection against environmental factors. This can lead to moisture ingress, corrosion, or other issues that can affect the PCB’s performance and reliability. -
Q: Can a conformal coating be too thick?
A: Yes, a conformal coating that is too thick can cause problems. Excessive thickness can interfere with component functionality, hinder heat dissipation, or cause mechanical stress on the PCB. It’s important to find the optimal thickness that provides sufficient protection without compromising the board’s performance.
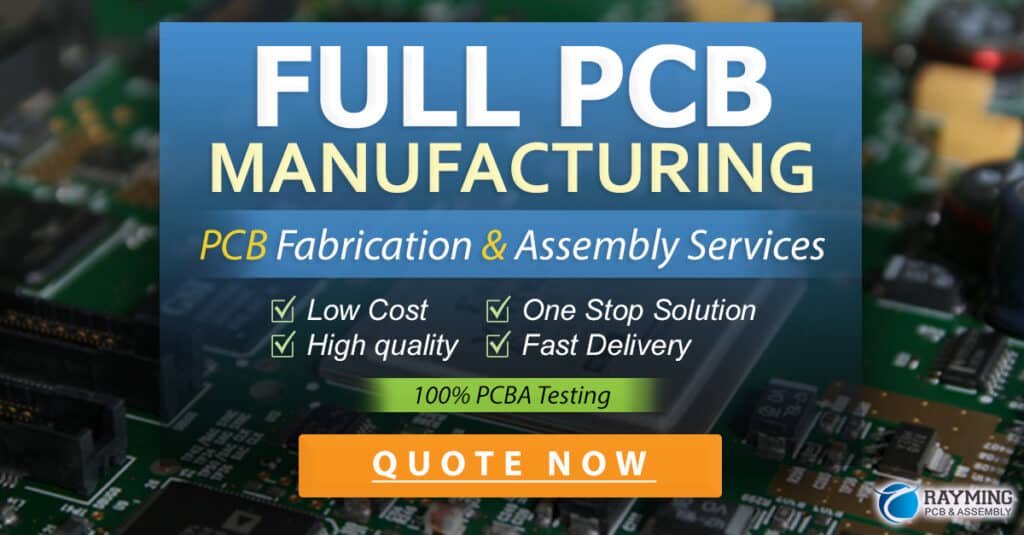
Conclusion
Determining the ideal thickness of PCB conformal coating is a critical aspect of ensuring reliable protection for printed circuit boards. By considering factors such as environmental conditions, coating material, PCB components and geometry, application method, curing process, regulatory requirements, and cost considerations, you can select an appropriate coating thickness that meets the specific needs of your application.
Remember, the ideal coating thickness is not a one-size-fits-all solution. It requires careful evaluation and optimization based on the unique requirements of each PCB. By striking the right balance between protection and functionality, you can enhance the longevity and reliability of your electronic devices.
No responses yet