1. Component Selection and Placement
The first point to consider in Printed Circuit Assembly is the selection and placement of components. It is essential to choose the right components that meet the design specifications and are compatible with the PCB. The placement of components on the PCB is also crucial, as it affects the overall functionality and reliability of the electronic device.
Factors to Consider in Component Selection
Factor | Description |
---|---|
Functionality | The component must perform the intended function in the circuit. |
Reliability | The component must be reliable and have a long lifespan. |
Cost | The component must be cost-effective and within the budget. |
Availability | The component must be readily available for production. |
Component Placement Techniques
There are two primary techniques for placing components on a PCB:
- Through-hole technology (THT): Components are inserted into drilled holes on the PCB and soldered onto the other side.
- Surface-mount technology (SMT): Components are placed directly onto the surface of the PCB and soldered using a reflow oven.
SMT is the more modern and preferred technique, as it allows for smaller components and higher density placement on the PCB.
2. Solder Paste Application
The second point to consider in printed circuit assembly is the application of solder paste. Solder paste is a mixture of tiny solder particles and flux that is applied to the PCB pads before component placement. The solder paste holds the components in place during the reflow soldering process and forms a strong mechanical and electrical bond between the component and the PCB.
Solder Paste Application Methods
There are two primary methods for applying solder paste to a PCB:
- Stencil printing: A stainless steel stencil with apertures corresponding to the PCB pads is placed over the PCB, and solder paste is applied using a squeegee.
- Dispensing: Solder paste is dispensed onto the PCB pads using a pneumatic or a jetting dispenser.
Stencil printing is the more common method for high-volume production, while dispensing is used for low-volume or prototype production.
Factors Affecting Solder Paste Application
Factor | Description |
---|---|
Stencil design | The stencil aperture size and shape must match the PCB pad size and shape. |
Solder paste viscosity | The solder paste must have the right viscosity for the application method used. |
Stencil cleaning | The stencil must be regularly cleaned to prevent solder paste buildup and ensure consistent application. |
3. Reflow Soldering
The third point to consider in printed circuit assembly is reflow soldering. Reflow soldering is the process of heating the PCB and components to a specific temperature profile to melt the solder paste and form a strong bond between the components and the PCB. The reflow soldering process is critical to the overall quality and reliability of the electronic device.
Reflow Soldering Temperature Profile
The reflow soldering temperature profile consists of four stages:
- Preheat: The PCB and components are slowly heated to a temperature below the melting point of the solder paste to activate the flux and remove any moisture.
- Soak: The temperature is maintained for a specific time to ensure even heating of the PCB and components.
- Reflow: The temperature is quickly raised above the melting point of the solder paste to melt the solder and form a strong bond between the components and the PCB.
- Cooling: The PCB and components are slowly cooled to room temperature to allow the solder to solidify and form a strong mechanical and electrical bond.
Factors Affecting Reflow Soldering
Factor | Description |
---|---|
Temperature profile | The temperature profile must be optimized for the specific solder paste and components used. |
Oven calibration | The reflow oven must be regularly calibrated to ensure consistent and accurate temperature control. |
PCB design | The PCB design must allow for proper heat distribution and avoid thermal stress on the components. |
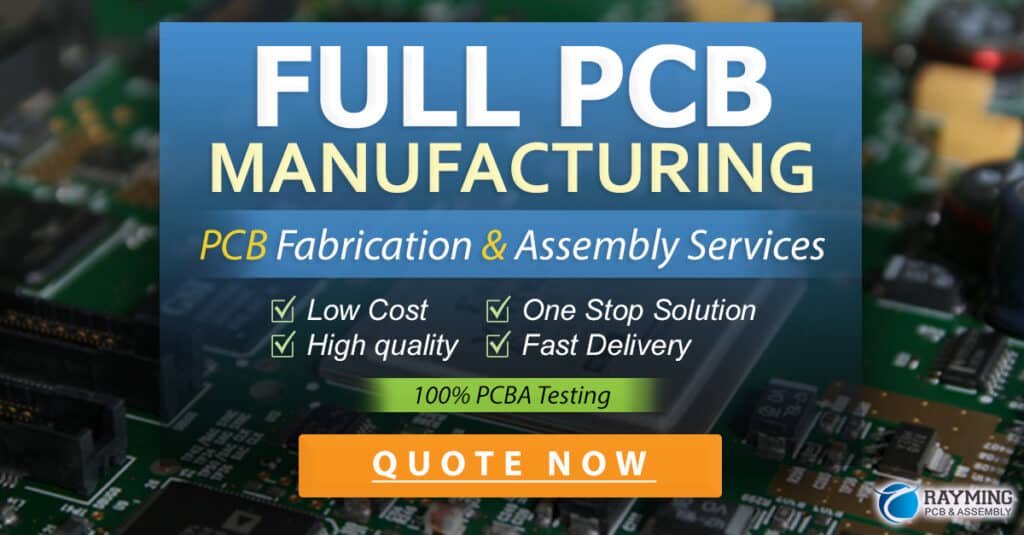
4. Inspection and Testing
The fourth point to consider in printed circuit assembly is inspection and testing. Inspection and testing are critical to ensuring the quality and reliability of the electronic device. It involves visual inspection, automated optical inspection (AOI), and functional testing to detect any defects or issues with the PCB and components.
Visual Inspection
Visual inspection is the first step in the inspection process and involves a manual examination of the PCB and components for any visible defects or issues, such as:
- Solder bridges or shorts
- Insufficient or excessive solder
- Misaligned or missing components
- Damaged or bent components
Automated Optical Inspection (AOI)
AOI is an automated inspection process that uses cameras and image processing software to detect any defects or issues with the PCB and components. AOI can detect defects that are difficult or impossible to detect with visual inspection, such as:
- Solder paste defects
- Component polarity or orientation issues
- Solder joint defects
Functional Testing
Functional testing involves testing the electronic device to ensure it functions as intended and meets the required specifications. Functional testing can include:
- In-circuit testing (ICT)
- Boundary scan testing
- Functional test fixtures
5. Rework and Repair
The fifth point to consider in printed circuit assembly is rework and repair. Despite the best efforts in inspection and testing, defects or issues may still occur in the electronic device. Rework and repair involve the process of identifying and fixing any defects or issues to ensure the device meets the required specifications and functions as intended.
Rework Techniques
Rework techniques involve the process of removing and replacing defective components or fixing any issues with the PCB. Some common rework techniques include:
- Soldering iron rework
- Hot air rework
- Desoldering and resoldering
Factors Affecting Rework and Repair
Factor | Description |
---|---|
Operator skill | The operator must have the necessary skills and training to perform the rework and repair process. |
Equipment and tools | The right equipment and tools must be used for the specific rework and repair process. |
Documentation | Proper documentation must be maintained for tracking and traceability of the rework and repair process. |
6. Documentation and Traceability
The sixth and final point to consider in printed circuit assembly is documentation and traceability. Documentation and traceability are critical to ensuring the quality and reliability of the electronic device and maintaining a record of the entire assembly process.
Documentation
Documentation involves maintaining a record of the entire assembly process, including:
- Bill of Materials (BOM)
- Assembly drawings and schematics
- Work instructions and procedures
- Inspection and testing reports
- Rework and repair records
Traceability
Traceability involves the ability to track the entire assembly process from the raw materials to the final product. Traceability is critical for identifying and resolving any issues or defects that may occur during the assembly process or in the field. Some common traceability methods include:
- Serial numbers
- Lot numbers
- Date codes
- Barcodes or RFID tags
Frequently Asked Questions (FAQ)
-
What is the difference between through-hole technology (THT) and surface-mount technology (SMT)?
THT involves inserting components into drilled holes on the PCB and soldering them onto the other side, while SMT involves placing components directly onto the surface of the PCB and soldering them using a reflow oven. SMT is the more modern and preferred technique, as it allows for smaller components and higher density placement on the PCB. -
What are the factors affecting solder paste application?
The factors affecting solder paste application include stencil design, solder paste viscosity, and stencil cleaning. The stencil aperture size and shape must match the PCB pad size and shape, the solder paste must have the right viscosity for the application method used, and the stencil must be regularly cleaned to prevent solder paste buildup and ensure consistent application. -
What are the stages of the reflow soldering temperature profile?
The reflow soldering temperature profile consists of four stages: preheat, soak, reflow, and cooling. The PCB and components are slowly heated to a temperature below the melting point of the solder paste, maintained at that temperature for a specific time, quickly raised above the melting point of the solder paste to melt the solder and form a strong bond, and then slowly cooled to room temperature to allow the solder to solidify. -
What are the different types of inspection and testing in printed circuit assembly?
The different types of inspection and testing in printed circuit assembly include visual inspection, automated optical inspection (AOI), and functional testing. Visual inspection involves a manual examination of the PCB and components for any visible defects or issues, AOI uses cameras and image processing software to detect any defects or issues, and functional testing involves testing the electronic device to ensure it functions as intended and meets the required specifications. -
What is the importance of documentation and traceability in printed circuit assembly?
Documentation and traceability are critical to ensuring the quality and reliability of the electronic device and maintaining a record of the entire assembly process. Documentation involves maintaining a record of the entire assembly process, including the bill of materials, assembly drawings and schematics, work instructions and procedures, inspection and testing reports, and rework and repair records. Traceability involves the ability to track the entire assembly process from the raw materials to the final product, which is critical for identifying and resolving any issues or defects that may occur during the assembly process or in the field.
In conclusion, printed circuit assembly is a complex process that requires precision, accuracy, and attention to detail. By paying attention to these six essential points – component selection and placement, solder paste application, reflow soldering, inspection and testing, rework and repair, and documentation and traceability – manufacturers can ensure the quality, reliability, and functionality of their electronic devices. As technology continues to advance and electronic devices become more complex, it is crucial for manufacturers to stay up-to-date with the latest techniques and best practices in printed circuit assembly to remain competitive in the market.
No responses yet