Introduction to 6 Layer PCB Manufacturing
In today’s world of advanced electronics, printed circuit boards (PCBs) play a crucial role in connecting and supporting various components within a device. As technology continues to evolve, the demand for more complex and compact PCBs has led to the development of multi-layer boards, such as 6 layer PCBs. These boards offer increased functionality and space efficiency compared to their simpler counterparts. In this article, we will delve into the intricacies of 6 layer PCB manufacturing and explore the process of how these sophisticated circuit boards are made.
What is a 6 Layer PCB?
A 6 layer PCB is a printed circuit board that consists of six conductive layers laminated together with insulating material. These layers are divided into:
- Top layer
- Ground layer
- Signal layer 1
- Signal layer 2
- Power layer
- Bottom layer
Each layer serves a specific purpose in the overall functionality of the PCB. The top and bottom layers are typically used for component placement and routing, while the inner layers are dedicated to power distribution, ground planes, and signal routing.
Advantages of 6 Layer PCBs
6 layer PCBs offer several advantages over their simpler counterparts:
-
Increased Functionality: With six layers, designers have more space to route signals and place components, enabling more complex designs and functionality.
-
Improved Signal Integrity: The dedicated ground and power layers help reduce electromagnetic interference (EMI) and maintain signal integrity.
-
Better Heat Dissipation: The additional layers allow for better heat distribution, preventing hot spots and enhancing the overall reliability of the PCB.
-
Compact Design: By utilizing the available space more efficiently, 6 layer PCBs enable designers to create more compact devices.
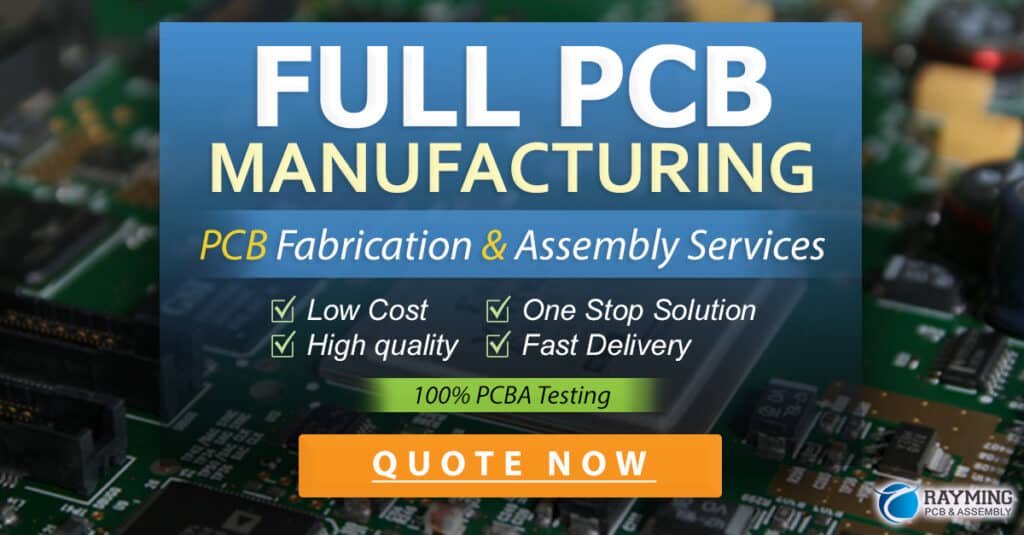
The 6 Layer PCB Manufacturing Process
The manufacturing process for 6 layer PCBs is more complex than that of single or double-sided boards. It involves several key steps:
Step 1: Design and Preparation
The first step in 6 layer PCB manufacturing is the design phase. Engineers use specialized software to create a detailed layout of the board, including component placement, routing, and layer stackup. Once the design is finalized, the necessary files are generated for manufacturing, such as Gerber files and drill files.
Step 2: Inner Layer Printing
The inner layers of the 6 layer PCB are printed using a process called photolithography. A photosensitive resist is applied to the copper-clad laminate, and the desired circuit pattern is exposed using UV light through a photomask. The exposed areas are then developed, leaving behind the circuit pattern.
Step 3: Etching and Inspection
After the inner layers are printed, they undergo an etching process to remove the unwanted copper, leaving only the desired circuit pattern. The etched layers are then inspected for any defects or inconsistencies.
Step 4: Lamination
The etched inner layers are then laminated together with insulating material, such as prepreg (pre-impregnated fiberglass), using heat and pressure. This process creates a solid, multi-layer board.
Step 5: Drilling
Once the board is laminated, holes are drilled through the layers to allow for component mounting and inter-layer connections. The drilling process is controlled by CNC machines that use the drill files generated during the design phase.
Step 6: Plating
After drilling, the holes are plated with a conductive material, typically copper, to ensure electrical connectivity between layers. This process is called through-hole plating.
Step 7: Outer Layer Printing and Etching
The outer layers of the 6 layer PCB are then printed and etched using the same photolithography process as the inner layers.
Step 8: Solder Mask Application
A solder mask is applied to the outer layers of the PCB to protect the copper traces from oxidation and prevent accidental short circuits during soldering. The solder mask also provides insulation and improves the board’s appearance.
Step 9: Surface Finish
A surface finish, such as HASL (Hot Air Solder Leveling), ENIG (Electroless Nickel Immersion Gold), or OSP (Organic Solderability Preservative), is applied to the exposed copper areas to protect them from oxidation and enhance solderability.
Step 10: Silk Screen Printing
The final step in the 6 layer PCB manufacturing process is silk screen printing. This involves printing text, logos, and component identifiers onto the board for easier assembly and identification.
Quality Control and Testing
Throughout the manufacturing process, strict quality control measures are implemented to ensure the 6 layer PCBs meet the required specifications. This includes:
- Visual inspection
- Automated optical inspection (AOI)
- Electrical testing
- Microsectioning
- Thermal stress testing
These tests help identify any defects or issues that may affect the performance or reliability of the PCB.
6 Layer PCB Stackup
The stackup of a 6 layer PCB refers to the arrangement of the layers and their respective thicknesses. A typical 6 layer PCB stackup might look like this:
Layer | Material | Thickness (mm) |
---|---|---|
Top Layer | Copper | 0.035 |
Prepreg | FR-4 (Fiberglass) | 0.2 |
Ground | Copper | 0.035 |
Core | FR-4 (Fiberglass) | 0.4 |
Signal 1 | Copper | 0.018 |
Core | FR-4 (Fiberglass) | 0.4 |
Signal 2 | Copper | 0.018 |
Core | FR-4 (Fiberglass) | 0.4 |
Power | Copper | 0.035 |
Prepreg | FR-4 (Fiberglass) | 0.2 |
Bottom Layer | Copper | 0.035 |
The specific stackup may vary depending on the design requirements and the manufacturer’s capabilities.
Applications of 6 Layer PCBs
6 layer PCBs find applications in a wide range of industries and products, including:
- Consumer electronics (smartphones, tablets, laptops)
- Automotive electronics (infotainment systems, driver assistance systems)
- Medical devices (diagnostic equipment, monitoring systems)
- Industrial automation and control systems
- Telecommunications equipment
- Aerospace and defense systems
As technology continues to advance, the demand for 6 layer PCBs is expected to grow, driven by the need for more complex and compact electronic devices.
Frequently Asked Questions (FAQ)
1. What is the typical turnaround time for 6 layer PCB manufacturing?
The turnaround time for 6 layer PCB manufacturing depends on various factors, such as the complexity of the design, the quantity ordered, and the manufacturer’s capacity. Typically, the lead time ranges from 7 to 14 days, but expedited services may be available for an additional cost.
2. How much does a 6 layer PCB cost compared to a 4 layer PCB?
The cost of a 6 layer PCB is generally higher than that of a 4 layer PCB due to the increased complexity of the manufacturing process and the additional materials required. The exact cost difference depends on factors such as the board size, quantity, and design complexity. On average, a 6 layer PCB can cost 20-50% more than a similar 4 layer PCB.
3. Can 6 layer PCBs be manufactured with different surface finishes?
Yes, 6 layer PCBs can be manufactured with various surface finishes, such as HASL, ENIG, OSP, and Immersion Silver. The choice of surface finish depends on the specific requirements of the application, such as solderability, durability, and cost.
4. Are there any special design considerations for 6 layer PCBs?
When designing a 6 layer PCB, it’s essential to consider factors such as signal integrity, power distribution, and thermal management. Designers should follow best practices for via placement, trace routing, and layer stackup to ensure optimal performance and manufacturability. It’s also important to work closely with the PCB manufacturer to ensure the design is compatible with their capabilities and design rules.
5. How can I ensure the quality of my 6 layer PCBs?
To ensure the quality of your 6 layer PCBs, choose a reputable manufacturer with experience in producing multi-layer boards. Provide clear and accurate design files, and communicate your requirements and expectations to the manufacturer. Request a detailed manufacturing specification and quality control plan, and consider ordering a prototype or small batch for testing and evaluation before proceeding with a full production run.
Conclusion
6 layer PCB manufacturing is a complex process that involves multiple steps and precise control to ensure the highest quality and performance. These sophisticated circuit boards offer increased functionality, improved signal integrity, better heat dissipation, and more compact designs compared to simpler PCBs. As technology continues to evolve, the demand for 6 layer PCBs is expected to grow across various industries, from consumer electronics to automotive and aerospace applications.
By understanding the manufacturing process, design considerations, and quality control measures involved in 6 layer PCB production, engineers and product designers can make informed decisions when developing their next-generation electronic devices. Working closely with experienced PCB manufacturers and following best practices in design and testing can help ensure the success of their projects and the reliability of their products.
No responses yet