Introduction to 6 Layer PCB Design
Six-layer printed circuit boards (PCBs) have become increasingly popular in modern electronics due to their ability to accommodate complex designs and high-density components. Designing a 6 layer PCB requires careful consideration of various factors to ensure optimal performance, reliability, and manufacturability. In this article, we will discuss the essential guidelines for designing 6 layer PCBs, covering aspects such as layer stackup, signal integrity, power distribution, and more.
Understanding the 6 Layer PCB stackup
What is a 6 Layer PCB Stackup?
A 6 layer PCB stackup refers to the arrangement of conductive layers and insulating materials that make up the printed circuit board. The stackup determines the board’s electrical properties, mechanical strength, and thermal characteristics. A typical 6 layer PCB stackup consists of the following layers:
- Top Layer (Signal)
- Ground Layer
- Signal Layer
- Power Layer
- Signal Layer
- Bottom Layer (Signal)
Choosing the Right Layer Stackup
When designing a 6 layer PCB, it is crucial to choose the appropriate layer stackup based on the specific requirements of your project. Consider the following factors when selecting your stackup:
- Signal integrity
- Power distribution
- Electromagnetic compatibility (EMC)
- Manufacturing constraints
- Cost
Here are some common 6 layer PCB stackup configurations:
Layer | Configuration 1 | Configuration 2 | Configuration 3 |
---|---|---|---|
1 | Signal | Signal | Signal |
2 | Ground | Ground | Signal |
3 | Signal | Power | Ground |
4 | Power | Signal | Power |
5 | Signal | Ground | Signal |
6 | Signal | Signal | Signal |
Choose the stackup that best suits your design requirements and consult with your PCB manufacturer to ensure compatibility with their fabrication processes.
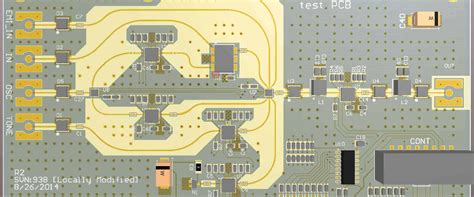
Signal Integrity in 6 Layer PCB Design
Controlling Impedance
Maintaining controlled impedance is essential for ensuring signal integrity in high-speed designs. The following guidelines can help you achieve controlled impedance in your 6 layer PCB:
- Use appropriate trace widths and spacing based on the target impedance and layer stackup
- Maintain consistent trace geometry throughout the signal path
- Use ground planes adjacent to signal layers to provide a reference for impedance control
- Consider using differential pairs for high-speed signals
Managing Crosstalk
Crosstalk occurs when signals from one trace interfere with signals on adjacent traces. To minimize crosstalk in your 6 layer PCB design, follow these guidelines:
- Increase spacing between adjacent traces
- Use guard traces or ground fills between sensitive signals
- Route critical signals on different layers with ground planes in between
- Use appropriate termination techniques, such as series termination or differential termination
Minimizing EMI
Electromagnetic interference (EMI) can disrupt the performance of your 6 layer PCB and cause compliance issues. To minimize EMI, consider the following guidelines:
- Use proper grounding techniques, such as a solid ground plane and multiple vias for ground connections
- Implement power planes to provide low-impedance power distribution
- Decouple power supplies using appropriate capacitors
- Use shielding techniques, such as ground fills or shielding cans, for sensitive components
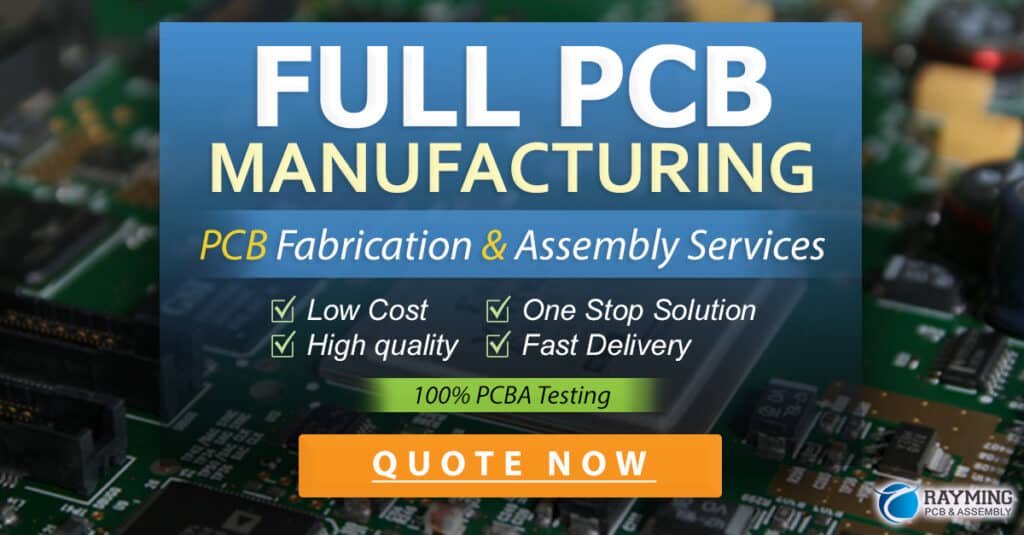
Power Distribution in 6 Layer PCB Design
Planning Power Distribution
Proper power distribution is critical for the stable operation of your 6 layer PCB. Consider the following guidelines when planning your power distribution network:
- Use dedicated power planes to provide low-impedance power distribution
- Place power planes close to the ground planes to minimize inductance
- Use appropriate via sizes and spacing to ensure reliable power connections
- Implement proper decoupling techniques to minimize power supply noise
Decoupling and Bypass Capacitors
Decoupling and bypass capacitors play a crucial role in maintaining a clean and stable power supply. Follow these guidelines for effective decoupling:
- Place decoupling capacitors close to the power pins of ICs
- Use a combination of bulk, ceramic, and small-value capacitors to cover different frequency ranges
- Minimize the loop area between the capacitor and the power/ground planes
- Use appropriate capacitor values based on the frequency and current requirements of your design
Power Plane Partitioning
In some cases, it may be necessary to partition your power plane to accommodate different voltage levels or to isolate sensitive circuits. When partitioning your power plane, consider the following:
- Use appropriate spacing between power plane sections to prevent coupling
- Implement proper decoupling at the boundaries of each power plane section
- Consider using ferrite beads or inductors to isolate noisy sections of the power plane
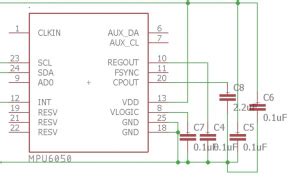
Thermal Management in 6 Layer PCB Design
Identifying Heat Sources
Effective thermal management starts with identifying the primary heat sources on your 6 layer PCB. These may include:
- Power-intensive components, such as processors, FPGAs, or power regulators
- High-speed components, such as transceivers or memory devices
- Components with high pin counts or large packages
Designing for Thermal Management
Once you have identified the heat sources on your 6 layer PCB, consider the following guidelines for effective thermal management:
- Provide adequate copper coverage for power planes and ground planes to distribute heat evenly
- Use thermal vias to transfer heat from components to the inner layers or the opposite side of the board
- Implement proper air flow and ventilation in your enclosure design
- Consider using thermal interface materials, such as thermal pads or thermal adhesives, for critical components
Thermal Simulation and Analysis
To ensure optimal thermal performance, it is recommended to perform thermal simulation and analysis during the design phase. This can help you:
- Identify potential hot spots and thermal bottlenecks
- Optimize component placement and copper distribution for better heat dissipation
- Evaluate the effectiveness of your thermal management strategies
- Make informed decisions about heatsink requirements or other cooling solutions
Manufacturing Considerations for 6 Layer PCBs
Design for Manufacturability (DFM)
To ensure a smooth and cost-effective manufacturing process, it is essential to incorporate Design for Manufacturability (DFM) principles into your 6 layer PCB design. Consider the following guidelines:
- Adhere to the minimum trace width and spacing requirements specified by your PCB manufacturer
- Use appropriate via sizes and pad dimensions based on your manufacturer’s capabilities
- Avoid sharp corners and acute angles in your trace routing to improve manufacturability
- Provide clear and accurate documentation, including layer stackup, drill files, and gerber files
Panelization and Routing
Panelization is the process of arranging multiple PCB designs on a single panel for efficient manufacturing. When panelizing your 6 layer PCBs, consider the following:
- Use appropriate spacing between individual boards to allow for routing and separation
- Implement fiducial markers and tooling holes for accurate alignment during assembly
- Consider the panel size and aspect ratio to optimize material usage and minimize waste
- Consult with your PCB manufacturer for specific panelization requirements and guidelines
Testing and Validation of 6 Layer PCBs
Electrical Testing
Electrical testing is crucial for verifying the functionality and performance of your 6 layer PCB. Common electrical tests include:
- Continuity testing to ensure proper connections between components and layers
- Insulation resistance testing to detect potential short circuits or leakage paths
- High-potential (HiPot) testing to verify the dielectric strength of the insulating materials
- Impedance Testing to validate the controlled impedance of critical signal paths
Functional Testing
Functional testing involves verifying the overall operation of your 6 layer PCB in its intended application. This may include:
- Power-on testing to ensure proper power sequencing and distribution
- Signal integrity testing to validate the quality and timing of high-speed signals
- Electromagnetic compatibility (EMC) testing to ensure compliance with relevant standards and regulations
- Environmental testing to assess the performance of your PCB under various temperature, humidity, and vibration conditions
Failure Analysis and Debugging
In the event of a failure during testing or operation, it is essential to have a well-defined failure analysis and debugging process. This may involve:
- Visual inspection of the PCB for obvious defects or anomalies
- Boundary scan testing to isolate faults at the component level
- X-ray inspection to detect internal defects or voids in solder joints
- Thermal imaging to identify hot spots or areas of excessive heat generation
By implementing a comprehensive testing and validation plan, you can ensure the reliability and performance of your 6 layer PCB design.
FAQs
1. What are the benefits of using a 6 layer PCB over a 4 layer PCB?
A 6 layer PCB offers several advantages over a 4 layer PCB, including:
- Increased routing density and flexibility
- Better signal integrity and reduced crosstalk
- Improved power distribution and thermal management
- Enhanced mechanical stability and durability
2. How do I choose the right layer stackup for my 6 layer PCB?
Choosing the right layer stackup depends on several factors, such as:
- The specific requirements of your design, including signal integrity, power distribution, and EMC
- The manufacturing capabilities and constraints of your PCB fabricator
- The cost and performance trade-offs associated with different stackup configurations
It is recommended to consult with your PCB manufacturer and discuss your design requirements to determine the optimal layer stackup for your project.
3. What are some common challenges in 6 layer PCB design, and how can I overcome them?
Some common challenges in 6 layer PCB design include:
- Maintaining signal integrity and controlling impedance in high-speed designs
- Managing crosstalk and EMI in dense layouts
- Ensuring proper power distribution and decoupling
- Achieving effective thermal management for power-intensive components
To overcome these challenges, follow the guidelines outlined in this article, including:
- Selecting the appropriate layer stackup and routing strategies
- Implementing proper grounding and shielding techniques
- Using appropriate decoupling and bypass capacitors
- Incorporating thermal management features, such as thermal vias and copper pours
4. How can I ensure the manufacturability of my 6 layer PCB design?
To ensure the manufacturability of your 6 layer PCB, consider the following:
- Adhere to the design rules and guidelines provided by your PCB manufacturer
- Use standard component sizes and footprints whenever possible
- Implement DFM principles, such as avoiding sharp corners and minimizing the use of vias
- Provide clear and accurate documentation, including gerber files and drill files
- Communicate with your PCB manufacturer throughout the design process to address any potential issues or concerns
5. What are some best practices for testing and validating my 6 layer PCB design?
Some best practices for testing and validating your 6 layer PCB design include:
- Developing a comprehensive test plan that covers electrical, functional, and environmental aspects
- Performing thorough visual inspections and using automated optical inspection (AOI) when possible
- Conducting electrical tests, such as continuity, insulation resistance, and HiPot testing
- Performing functional tests to verify the overall operation of the PCB in its intended application
- Implementing a robust failure analysis and debugging process to quickly identify and resolve any issues that may arise
By following these best practices and the guidelines outlined in this article, you can ensure the successful design, manufacturing, and operation of your 6 layer PCB.
Conclusion
Designing a 6 layer PCB requires careful consideration of various factors, including signal integrity, power distribution, thermal management, and manufacturability. By following the guidelines and best practices outlined in this article, you can optimize your 6 layer PCB design for performance, reliability, and cost-effectiveness.
Remember to:
- Select the appropriate layer stackup based on your design requirements
- Implement proper routing and grounding strategies to maintain signal integrity
- Use appropriate decoupling and thermal management techniques
- Incorporate DFM principles and collaborate with your PCB manufacturer
- Develop a comprehensive testing and validation plan to ensure the quality and reliability of your PCB
By adhering to these guidelines and continually refining your design process, you can successfully navigate the complexities of 6 layer PCB design and create high-performance electronic products.
No responses yet